So, after some thought, I am thinking about using 1/4" aluminum with a minimum width of 6" for the uprights in the upper photo version-1, one 12x48" piece each, and 8" in the lower photo version-2, one 16x48" piece each.
In version-1, I question whether the aluminum can be bent after cutting out the curved shape without winding up too twisted to use or even if 6061 T6 can be bent at a 60 deg angle. If I tried to bend the uprights, I would get the wing longer than needed and shorten to whatever width it wound out to be. Or, I could cut the individual pieces out and then weld them together in some sort of jig.
In version-2, it would be a lot easier to fab up and I think that the fully welded 1/2" steel rod perimeter sheet metal flare is strong enough, (at least strong enough to jack up the car). I don't know exactly how wide the flare spacing is and the rear view photo is greatly distorted and for discussion purposes only. Also, everything is scaled at the very rear of the car to the license plate that is exactly 12" wide.
And lastly, I have read that you can router aluminum with a simple wood router bit, how about routing an 1/8" radius in 6061-T6 aluminum?
Any thoughts?
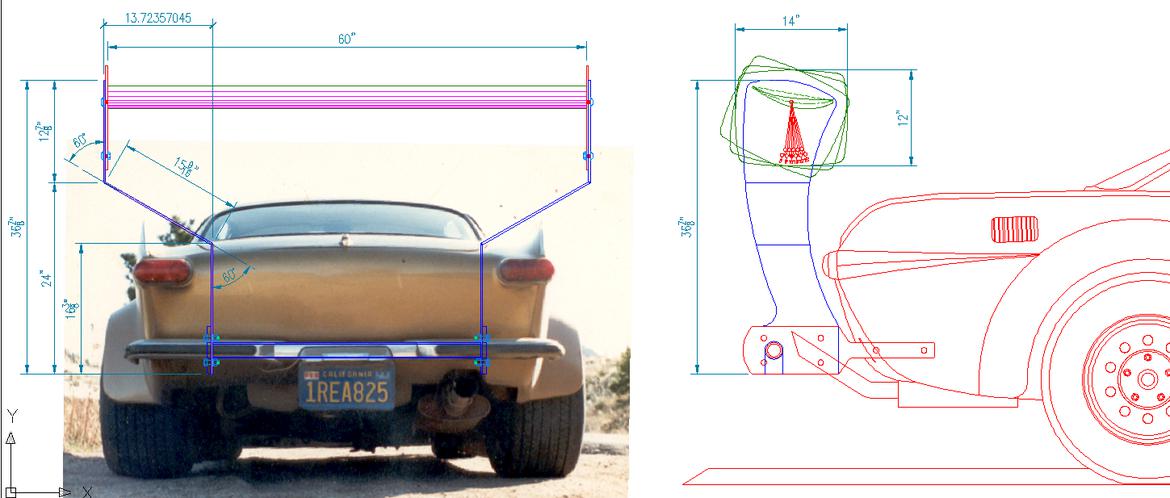
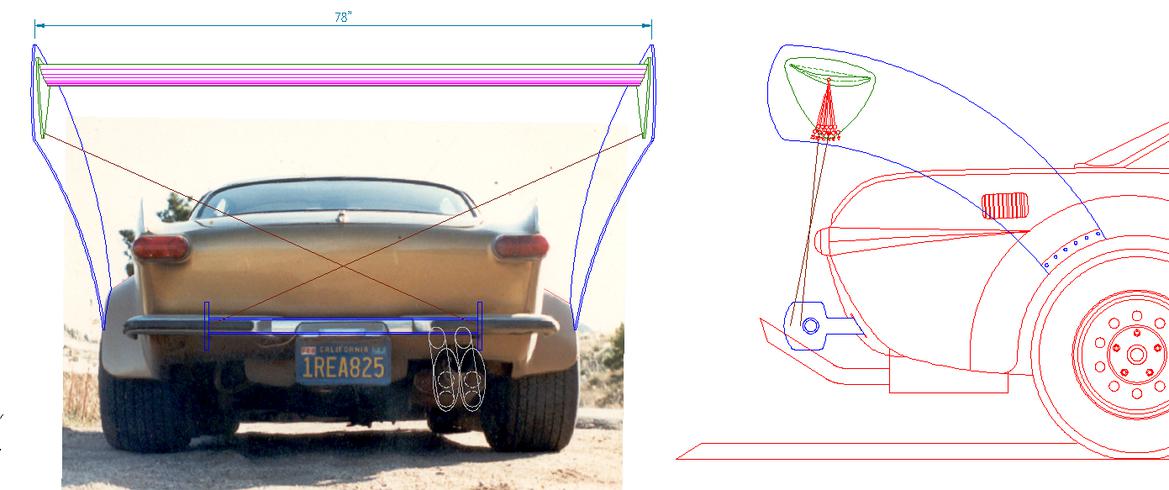
I finally with great difficulty leveled down to the floor and measured the width of the rear flares at the widest point which is the leading edge and came up with about 74" plus or minus, so 4" narrower than my guess. It didn't change the drawing much.
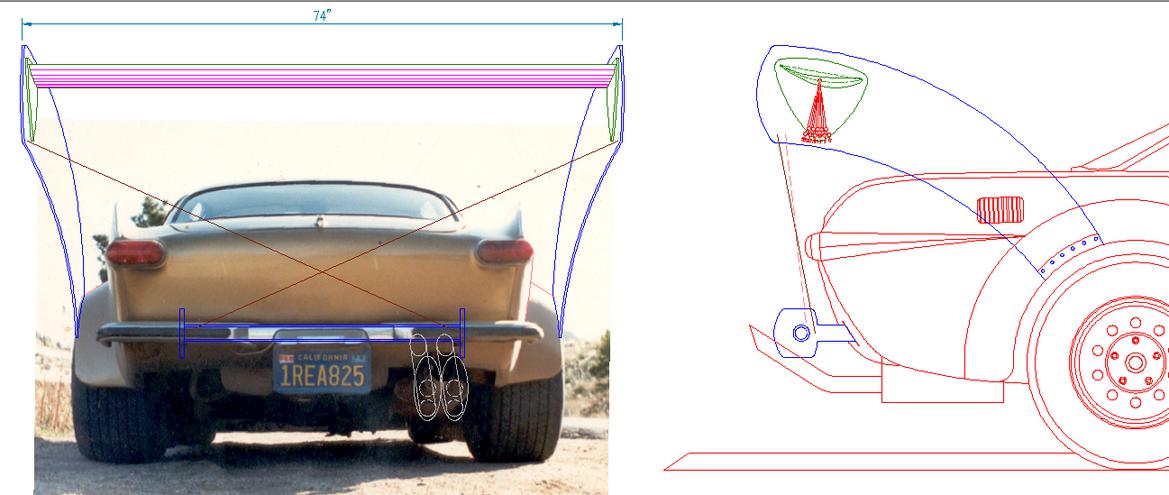
Too bad to mount the wing this way I have to build new flares first. The original ones I formed up the 1/2" rod and cut the sheet metal out with a semi-circle double the opening diameter and when rolled around the rod, it formed a 45 deg. angle and then welded together before I meticulously trimmed it to fit the body. It follows the plan view front and back tappers that are narrower than the door areas so that the back of the front flare sticks out more and so does the front of the back flare.
Next time I will fully form and weld the rod to the body first and then I will build a gizmo that bolts onto the wheel studs and with wood and nesting brass tubing from a model airplane hobby shop that I can rotate around the flare opening, trace the body attachment line by moving a marker in and out along the 45 deg. angle so I can trace out the flare shape onto the body and then run the flare past the body cut and then weld it. Let me sketch it up...
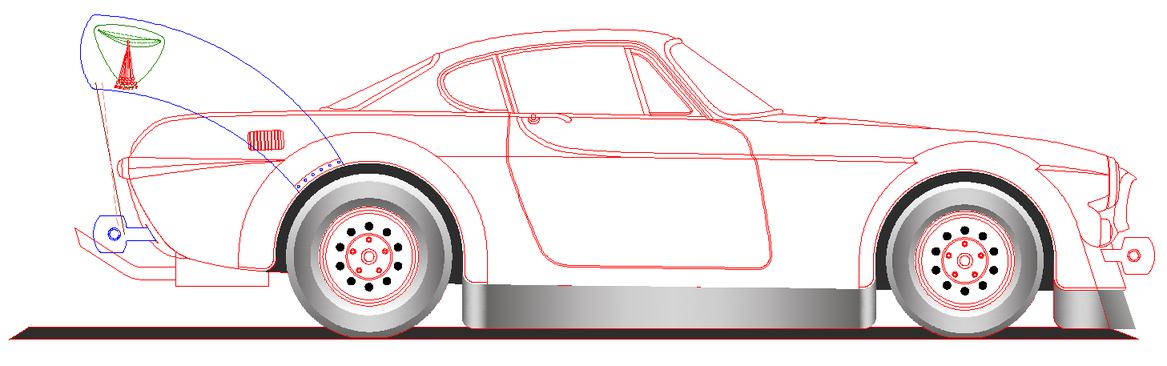