I drew up some elliptical velocity stacks and had them printed while I shake down the bugs of my own 3d printer. Thought you guys might like to see them.
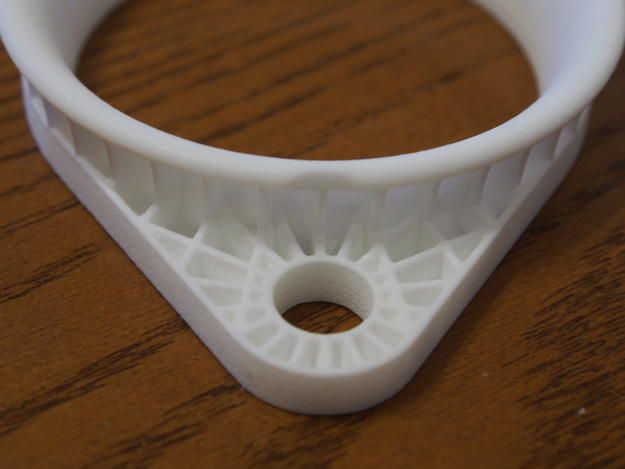
These are 13 mm long. With the adjustable spacers I made these would be similar to about 70mm stacks. Here's one on my blacktop next to some 50mm SQ Eng stacks, with my adjustable spacers and a Pipercross PX600 back plate I drew up.
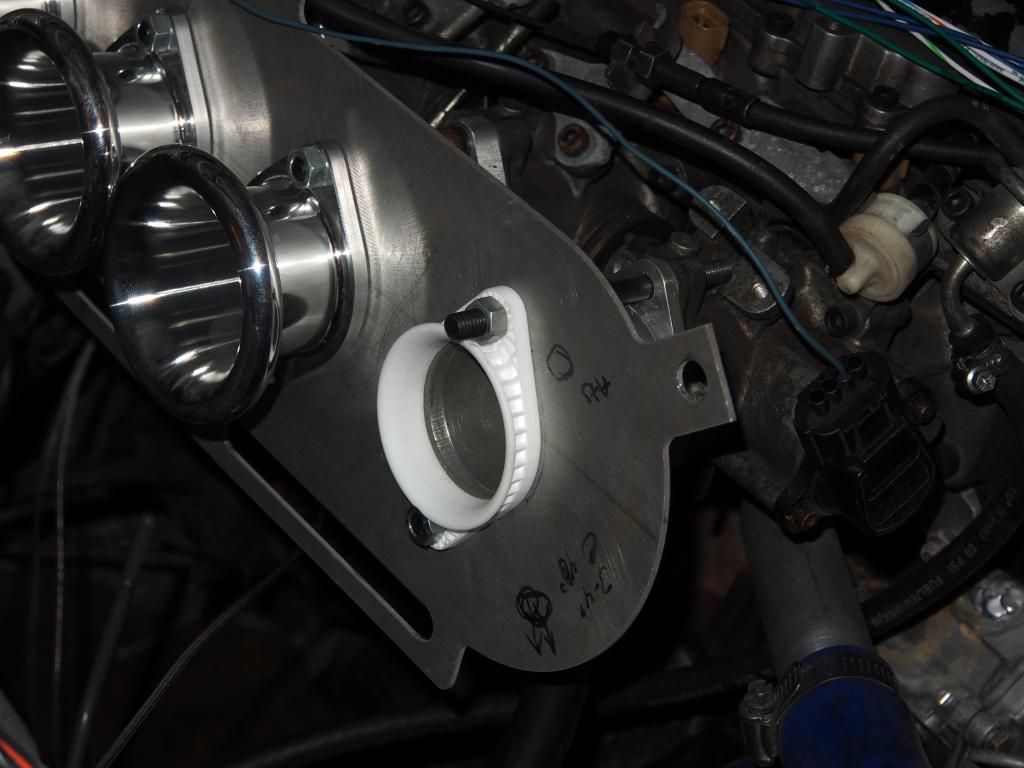
I need to trim up my hardware, and then they should be good to go! I've got 30 mm versions on the way, as well. I'm planning on running staggered lengths. This is an inexpensive way to test lengths, but these are nylon, so they should withstand the fun of an engine bay rather well.
84FSP
Reader
12/23/14 7:21 p.m.
Nice work! Been boning up on my cad skills hoping to crankout a lower airbox/intake for El Rabbito via the 3d printer at my office.
84FSP wrote:
Nice work! Been boning up on my cad skills hoping to crankout a lower airbox/intake for El Rabbito via the 3d printer at my office.
It took me an iteration before it occurred to me to do these in this manner. My first iteration was shaped just like it would have been had I machined it. Then I realized that was entirely unnecessary and did this one, with 1 mm walls and 1 mm ribs.
I did the design parametrically so that I could do several lengths: https://www.shapeways.com/shops/OrionEngineeredMachineworks
Please don't consider this as me trying to pander or advertise, I'm just trying to demonstrate how parametric modeling and 3d printing has allowed me to make several different lengths of velocity stacks for my intended testing. I had them printed by ShapeWays, which also allowed me to set up a vendor spot for them. I don't care if anyone buys them or doesn't. I made them for myself. I'm actually considering releasing them under an open hardware license, if there's interest in that.
How durable would these be under the hood (temps, et al)?
I have an older Makerbot at work, and was thinking.....
bluej
SuperDork
12/23/14 8:41 p.m.
A comment in the sbf swap thread got me thinking about a complete 3d printed manifold system. Then you post this. Nice work! 
SkinnyG wrote:
How durable would these be under the hood (temps, et al)?
I have an older Makerbot at work, and was thinking.....
These are nylon and claim to be good to 80 C (176 F). https://www.shapeways.com/materials/strong-and-flexible-plastic
They also have what they used to call alumide and are now calling 'metallic plastic'. It's aluminum bonded with nylon. https://www.shapeways.com/materials/metallic-plastic
They have a bunch of other materials, most of which would not be suitable here: https://www.shapeways.com/materials?li=nav
You'd want to print in ABS if you were wanting to make anything which would be useful for more than quick testing. I don't think PLA would live under a hood.
bluej wrote:
A comment in the sbf swap thread got me thinking about a complete 3d printed manifold system. Then you post this. Nice work!
I'm also working on (back burner) a manifold for these ITBs, which will probably be printed out of alumide. It'd be provisioned for top feed fuel injectors, a vacuum block, MAP sensor, and IACV.
84FSP
Reader
12/24/14 7:15 a.m.
In reply to burdickjp:
The choice of Nylon was a good one but a Nylon 66 would be even better as it buys you another 15 degrees C and is still on the affordable side of thermoplastics. Feel free to hit me with any plastics questions as that's what I do 9-5!
84FSP wrote:
In reply to burdickjp:
The choice of Nylon was a good one but a Nylon 66 would be even better as it buys you another 15 degrees C and is still on the affordable side of thermoplastics. Feel free to hit me with any plastics questions as that's what I do 9-5!
I hope I wouldn't find myself requiring any higher temperature performance. I'd suspect something is wrong.
I'm basing this off of average IAT temps reported by people at track days. I haven't any good IAT logs.
...
The choice of Nylon was a good one but a Nylon 66 would be even better as it buys you another 15 degrees C and is still on the affordable side of thermoplastics. Feel free to hit me with any plastics questions as that's what I do 9-5!
OK, what's best material for timing chain guides?
It's kind of a related question, as 3D printed custom chain guides could be very useful.
84FSP
Reader
12/24/14 7:53 a.m.
In reply to erohslc:
Timing chain guides are actually a pretty complicated one. The temps are higher, they are constantly bathed in oil, and the wear becomes a critical factor when added to those variables. The best designs I see are are molded over a metal brack for reinforcement.
The most popular materials are nylon 66 and nylon 6T with a heavy heat stabilizer and a significant lube in the recipe. No idea how available those are for 3d printers. What type of machine are you working with?
84FSP
Reader
12/24/14 8:02 a.m.
In reply to burdickjp:
You are probably ok with the nylon 6 there. Folks tend to use a healthy safety factor for polymer designs. For any given resin check the data sheet for the glass transition temperature and the relative thermal index (rti). The rti is the temperature the material can withstand for a constant 100,000 hrs. You notice that the rti temp is probably only half of the glass transition temperature of the material.
For parts like you are manufacturing you should be fine using 70% of the glass transition temperature of the material as a rule of thumb.
Interesting, I'm planning to use a 3D printed ITB adapter to put blacktop ITBs on my 4AGE 16v. I could use off-the-shelf trumpets, but I was thinking about Yamaha R1/R6-style splitting variable trumpets and this could be a good way to make them!
GameboyRMH wrote:
Interesting, I'm planning to use a 3D printed ITB adapter to put blacktop ITBs on my 4AGE 16v. I could use off-the-shelf trumpets, but I was thinking about Yamaha R1/R6-style splitting variable trumpets and this could be a good way to make them!
I saw a FSAE car which used the Yamaha variable trumpets. I thought it was rather clever.
There are decent ITB manifolds on the market.
84FSP wrote: Feel free to hit me with any plastics questions as that's what I do 9-5!
What do you think of Shapeways alumide: https://www.shapeways.com/materials/metallic-plastic
I haven't been able to find much more information on it, but it seems rather novel, and this seems like a good application for it.
84FSP
Reader
12/25/14 5:52 p.m.
In reply to burdickjp:
I would avoid the aluminum filled material as it appears to do nothing for the mechanical integrity of the material other than make it conductive.
For any plastics application I have a stock set of questions that seem to work well for making sure we select the right material. The right questions with a good how to guide for plastics will get you there!
1) Where does it live?
- what is the environment for the finished part
- temperature - fluid contact - mechanicals - longevity - UV
2) What are the mechanical requirements?
- does it need to be strong - have high modulus - high impact
3) What is the production method intended?
- printer material - wire - powder - sinter - infrared
In the case of auto I generally segment into the different types of applications like underhood, interior, structural, and drivetrain as that really helps to focus in on some material details.
Plastics are great but do not have anywhere near the same level of understanding that is out there for metals. The better I get at this the fewer constants there really are which is sometimes frustrating. The answer is always debatable as there is no best plastic that solves all issues.
These guys do a really nice job of laying out an overview of materials based on their capabilities.
Tangram Periodic Table Of Thermoplastics
84FSP
Reader
12/25/14 5:56 p.m.
In reply to burdickjp:
Acetyl is a great material that has wonderful wear characteristics, decent mechanical properties, decent chemical resistance, and nice surface qualities. My company is the largest producer of it in the world so we're pretty partial to it.
Acetyl has a home in auto interiors and all things bushing, wear, or fuel related.
In this application the concern here is temperature which is an Achilles heel for Acetyl.
84FSP wrote:
In reply to burdickjp:
Acetyl is a great material that has wonderful wear characteristics, decent mechanical properties, decent chemical resistance, and nice surface qualities. My company is the largest producer of it in the world so we're pretty partial to it.
Acetyl has a home in auto interiors and all things bushing, wear, or fuel related.
In this application the concern here is temperature which is an Achilles heel for Acetyl.
I used acetal to make near-zero backlash lead screw nuts for my 3d printer.
It's my understanding there are two things regularly called acytal, one of which has a much lower melting temperature than the other. I originally intended on melt-forming my lead screw nut, but ordered the wrong material and couldn't make it work, so I cut a nut instead.
84FSP wrote:
In reply to burdickjp:
I would avoid the aluminum filled material as it appears to do nothing for the mechanical integrity of the material other than make it conductive.
They claim it is 'heatproof' to 169 C. Whatever that means, the number is higher than the nylon these are made of.
84FSP
Reader
12/25/14 7:37 p.m.
In reply to burdickjp:
Ok - so I left out fasteners as a great fit for Acetyl. In that applications the wear characteristics and good mechanicals make it a good choice.
84FSP
Reader
12/25/14 7:41 p.m.
In reply to burdickjp:
Fast fingers sir! Many fillers can drastically improve the temp range of polymers. Polypropylene us a nice fit for the temps and mechanicals. Polypropylene also is one of the lightest specific gravity materials to meet these requirements. Every production vechile on earth has approximately 50lbs of polypropylene for this reason!