Looks like some of you have already seen it but I uploaded a new video! https://youtu.be/nXk434kHBww And thank you guys for the encouragement with the videos, sometimes I wonder if producing them is worthwhile but I have fun making them :)
Yeah, so there was a little fire. It was the electrical tape wrapped around the wiring harness on the inside of the metal panel that I was welding to. What I should have done was sprayed the wires inside there with a little water or something first. I'll make sure to do that in the future. I'm really lucky that it was only the electrical tape that burned and that the fire didn't grow. And I was even more lucky that I even saw or noticed it because it was totally out of sight and it wasn't crackling or making any noise, and it was already so smokey in there that more smoke wouldn't be noticeable. I saw just a little flicker of light through one of the burn-through holes in my welding. If I didn't see that then it could have grown much bigger before I noticed.
And about the wooden floors. I've been using a welding blanket but I admit that I've relaxed a bit on using it. I have it covering the gas tank now but I'm going to cut it into smaller pieces that I can spread around the project as needed. I got the biggest one I could find at HF, 6' x 8', I thought I would just spread it out over the garage floor under the car but its still not big enough to do that. When welding in the PS rocker panel, a fairly large MIG berry fell and landed on the plywood floor and I sat there for about 20 seconds and watched it to see how the wood would fair. It charred a pit in it but that was it. But if that part of the floor had some oil or wd40 soaked into it or something... who knows. Yeah I gotta be more careful.
NOHOME said:
The pace is pretty impressive. 20 hours a week is lot of time to take away from other things in life!? The Molvo is 5.5 years in at 10 hours/week, and I find that requires a supportive spousal unit.
yeah my wife Logan (our 6 month anniversary is coming up) is starting to refer to the project as my other wife, lol. But I made sure to get her blessing before starting the project, and she at least pretends to be interested in my videos and sometimes she even enjoys watching them, haha. I told her I'll build her a car next, she wants a murdered out '67 Lincoln Continental, "like the one in Entourage." But I think she'll be happy with an old Cadillac haha.
Alright here's the pics!
I want to share this one first, but note that this is not be the actual ride height because the body was still sitting on jacks when the pic was snapped, and therefore the weight of it wasn't sitting on the suspension. I wanted to hang the fender to make sure the wheel was in the center of the wheel well before welding the body to the chassis.
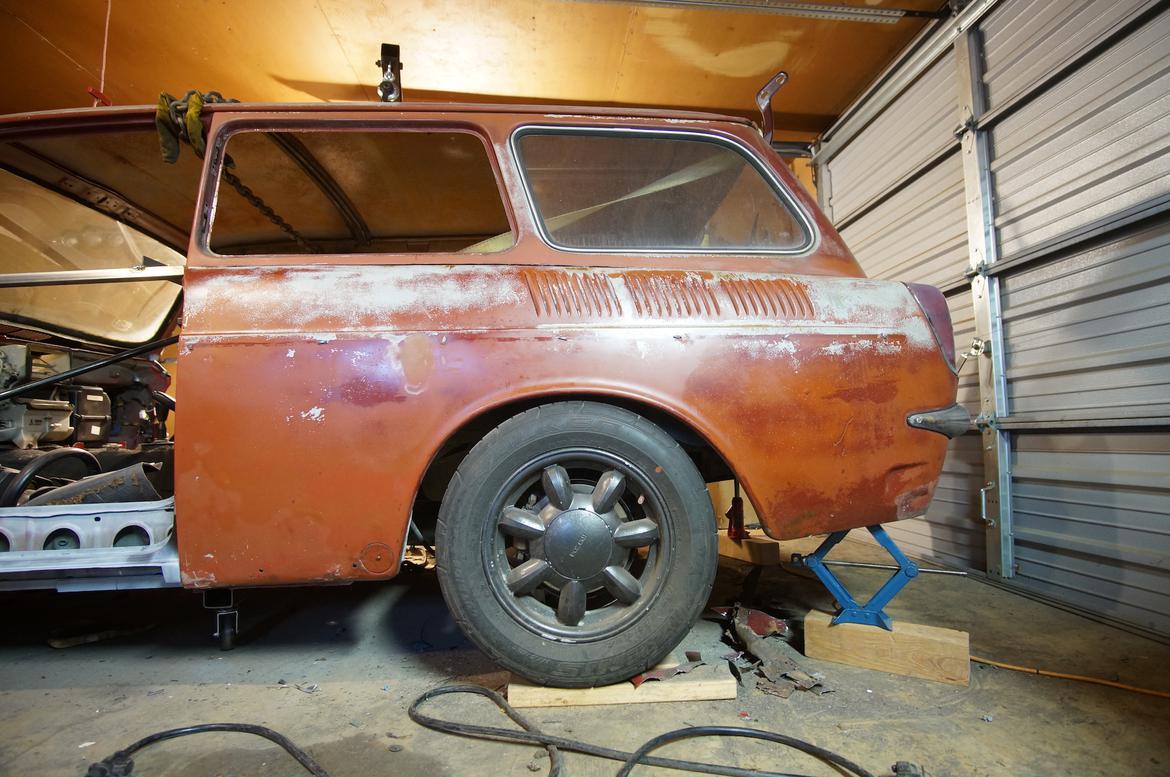
I should have took a pic of how far the tire was sticking out but I was in too much of a hurry I guess. But I measured how far the tires stuck out past the fenders and it was bout 3/4".
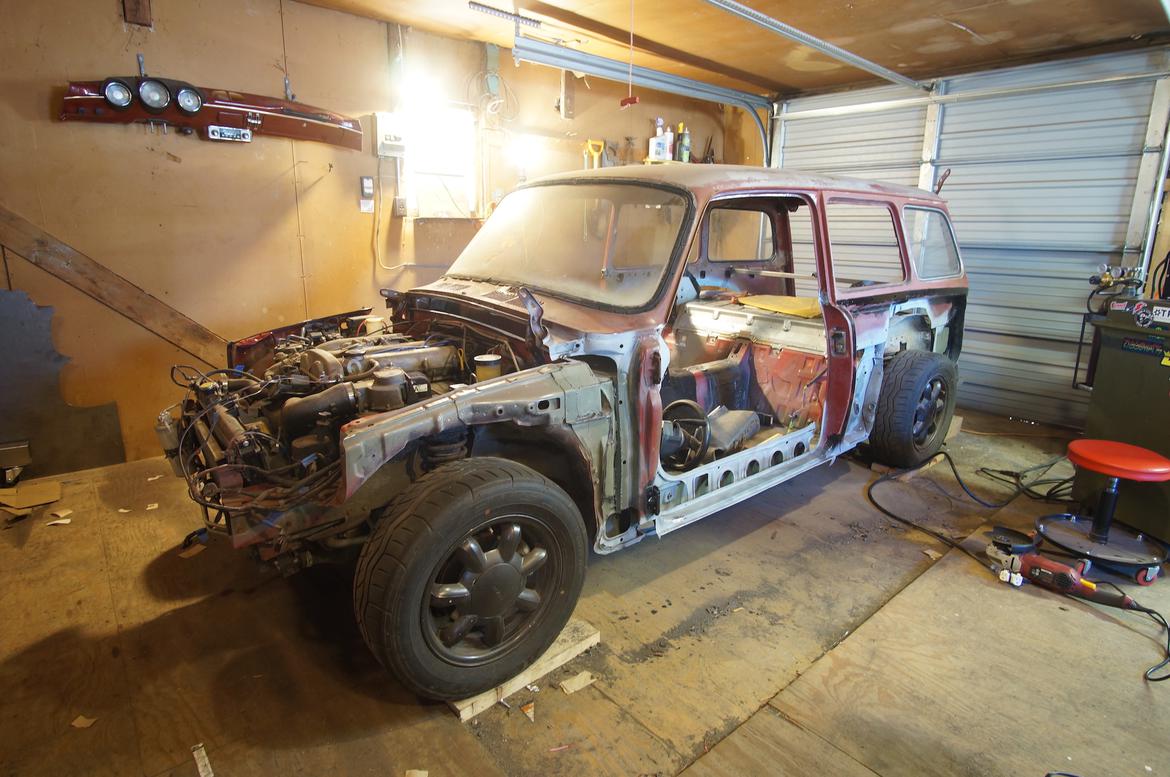
Notice anything different? No more braces and no more hoist holding it up.
This is a screenshot from the video:
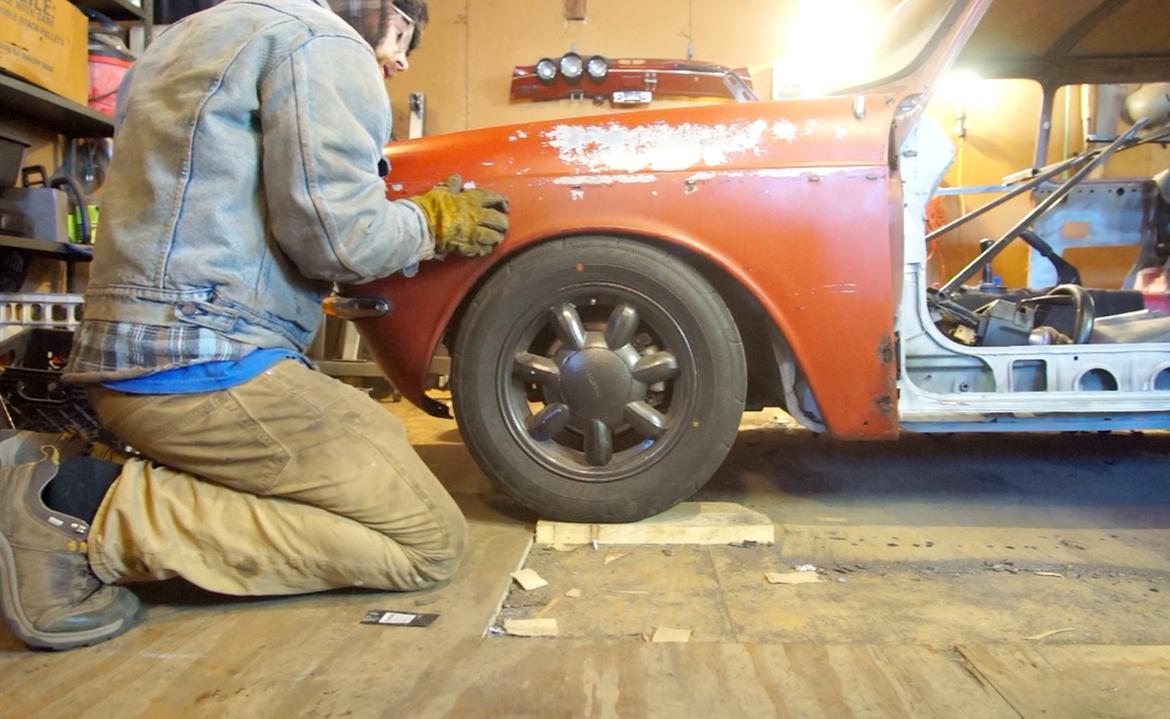
Umm, do you guys think the front wheel looks a little forward? Maybe it is but it doesn't look too bad. I'd rather it be too far forward than too far back! I knew that the wheelbase would be 3/4" too long, I guess this is the result of that. But I can definitely live with it.
And this is with the body on the weight of the suspension, so that's the actual ride height. I didn't have enough hands to measure it and hold the fender at the same time, but it looked like the tire was sticking out past the fender only about 1/4".
Then I put it up on jack stands:
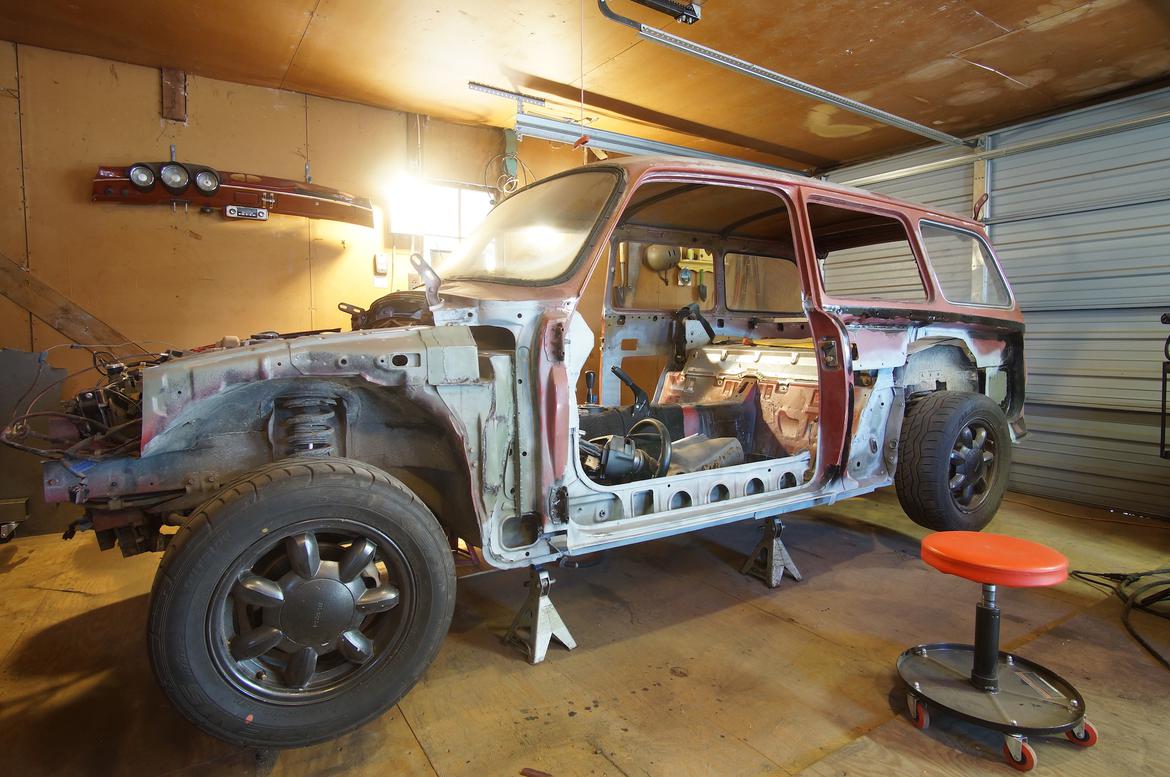
I'll get some shots of the new rocker panels and of the burn damage today so you guys can see that too.