simon_C
New Reader
6/22/16 4:43 p.m.
MulletTruck wrote:
and a lot of people put the head from a Ranger on too. Has a roller top end that can handle the RPMs a little better.
Volvo 16v heads will fit with modification as well. Apparently it's a significant upgrade to RPM handling and peak flow.
^^ I would like to try that with one of my 2 spare blocks, but that's a long ways down the road from even being a real thought. I didn't have work today so I spent a good bit of time messing around in the garage (which is super nice to be able to use). Today started with a running, driving car and ended with one that is far from it. I drained the coolant and took out the radiator and fan shroud. Then moved on and pulled the driveshaft, took the shifter off, removed exhaust bracketry, and then got dealing with the wires.
Luckily, the only harness on the driver's side deals exclusively with the lights. The main harness wraps from the passenger side all the way around the engine. I've separated out the lights from the passenger harness as well and have the rest of the harness "isolated" to get rid of. My main question, and I'm sure it's stupid, is this - which voltage regulator do I use? My gut tells me to go with the one from the new/Merkur harness but I'm just not sure. Thoughts?
GPz11
New Reader
6/24/16 9:06 a.m.
On a XR4Ti, the voltage regulator is built into the alternator.
Well, I've been away for a while and traveling some the last few weeks but I've managed to get a decent bit of time in the last few days. The engine is out, finally! I was working alone and without a leveler so it took some time and some readjusting but it was pretty uneventful all things considered. Luckily I have a buyer lined up so I should be getting it out of the way this week or next.

Today I started cutting a few patches for the firewall. The only sheet metal I have around in a decently similar gauge is chromoly, so I need to pick up some gas so I can MIG weld instead of flux core. I've read a few conflicting things online, but I trust the hive: can 4130 be welded to the mild steel of my firewall? It shouldn't need to be structural, I just want to have it be more flush. For the floor pans I'll probably have to pick up some 18 gauge since that will need to be structural. I need to find some way to bead roll the patches before I weld them in but I'm not there yet either. I finished up the afternoon today by starting to clean up the engine bay. I got the battery tray mostly removed as well as the "jut out" on the driver's side. I still need to either keep drilling out the spot welds (pain in the ass) or just grind the remaining bits down to appear flush with the metal around them. Last week I went back up to Greenville and ended up spending a whole day hanging out with a buddy of mine up there. In the morning we just shot the breeze, but from about noon on we worked on straightening out a spare fender I had bought on craigslist to replace/ be a spare for my damaged passenger side. I don't have many pictures of before or after, but here you can see some of the wrinkles on the inner fender lip.

There was more damage below the lower body line that he got straightened out as well. Now I need to look for some hammer/dollies. PS, if anyone in the southeast finds a finger brake (not a harbor freight, something decent) for a couple hundred bucks, I'm on the lookout for one. I get to be working on it for the next few days which will be very nice. On August 4th I head out on a 16 day-ish trip and when I get back I'll have to start school so I'm trying to squeeze in as much as possible while I can!
What engine is that that you just pulled? Not a mazda fma, is it?
It's a 1.8l Mazda from 1975, not sure of the engine code beyond that! What should I be looking for to identify?
Umm....
I think it's cast into the block.
Best friend has a 80 b2000 with a bad engine. His is fma.
If the deal goes pear shaped, let me know. I'll see if he can use it.
I pulled the passenger fender today in hopes that i'll be able to start welding in patch panels where water has been leaking through tomorrow. Overall, behind the fender was in pretty good shape with just a few areas that appear to need cutting/welding.

Looking everything over makes me think that whatever hit the bottom here is what caused the damage to the fender and door on this side,as well as potentially my hood alignment troubles. I'll check by pulling the driver's fender tomorrow and seeing if it's different/ less wrinkly but I'm pretty confident something happened on this side.

classicJackets wrote:
It's a 1.8l Mazda from 1975, not sure of the engine code beyond that! What should I be looking for to identify?
I know this isn't the path you are going to take- but would a Miata 1.8 powertrain fit, you think?
People are shoehorning V8s in without much issue. I'm sure a Miata 1.8 would fit. If I manage to mangle enough 2.3's I consider that a good fallback option. I'm sure it would be lighter, too.
It dawned on me last night watching Wheeler Dealer- where they were rebuilding a Chevy Luv. Would be a good swap for a decent power improvement.
I'd personally also look into a 2.3l from a modern Ranger, too. But that's a different thing.
I watched a few minutes of that episode but turned it off to fall asleep before anything exciting happened. Yesterday was a big day around here. I uncovered a few more holes with a wire wheel and began patching. I started with the bullet hole in the passenger floor/wheel well: Cut it out, patched, ground down (some) and covered it in spray-bedliner. I love the texture/look of that and it seems much more durable than the rubber undercoating I've tried in other places. Here's the 2nd patch I started; this one is going for making the car watertight again. You can see the outside of this rust hole in one of the pictures above, and you can see here that I cut it out as almost an "L" shape.

The first patches I tried to make looked like this, and folded/bent over:

After a few failed attempts at that I changed tack. Since what goes behind the fender will never be seen, I figured I'd set the patch in with an overhang to the backside, and then just fill the vertical rectangle by tacking it on the backside. I got the first patch mostly done last night, but it needs some cleaning up and probably a few more tacks then I'll tackle the other patch. I'm hoping to get the car watertight before this coming Thursday, but we'll see.


Do you know of any Couriers, or Mazda's of that era for sale cheap? I'm looking for one to have as a project fro my son and I, and hopefully use some of the REPU specific stuff I have kicking around. Still interested in the fender flares? I totally spazzed on getting you a shipping quote on those, but just tripped over them in the corner of the garage last night, and it reminded me.
I just found your build thread. As many have stated at the start of your adventure, I had a 1980 Courier and drove it for many years before passing it on to my son. He was living in Minneapolis and discovered a homeless person had been sleeping in it at night (it had a topper).The idler arm wore out as yours did and I decided to sell it. Being in MN, rust is what finally took it off of the road. However, it continued on as a wood hauler/baja truck on a farm.
I still have a brake m/cylinder rebuilt kit. Want it?
If you get a chance, would you mind measuring the distance from firewall to the radiator support under the hood? I've been eyeing trucks like this myself and thinking that one of my spare BMW M42 4-cyl engines might fit nicely in that engine bay. Also 1.8L, but about twice the stock Courier horsepower :)
Wow, I'm sorry guys, I blanked on checking this! Nothing much has changed on my end, just been selling spare 2.3 parts and researching things like rear end swaps. I'm still thinking narrowed 8.8" Explorer; something like 3.73's with Trak-Loc sounds about right..
Mazda, cheap ones pop up down here on Craigslist from time to time, and the Facebook group (Ford Courier Nation) usually has a few, but they're often PNW. Not sure if the Montero scratched your itch for a project vehicle, though. I'd be interested in the fenders still, but unfortunately, as before, the time isn't right economically.
Outasite, I probably don't have a use for it, honestly. The M/C on there now is brand new (and the seals seem to be good), and when I update the rear end I'll probably go to a different M/C anyway. Thanks, though!
Irish, I actually have the measurment written down on a newspaper in my Expedition. I'll try to check that tonight and get back to you Asap
Better late than never? I wrote down 29" firewall to rad support. A lot of guys will cut out the radiator support or take the firewall back some though. 150hp would be a blast in a courier/similar mini truck!
Well, I brought all the important stuff home from school for the semester:

The bare block to help test fitment, the 1/8" plate and 1/4" scraps for custom mounts (if the stock/existing cast aluminum mounts don't fit the frame), 3/8" plate to serve as a welding table, and the blue is just some scrap I picked up - not sure where that'll go yet!
I only spent a few minutes in the garage tonight, hopefully tomorrow I'll get some more time.

I switched over the front sump oil pan to the "test" block, got a cardboard template made to match the height/width of the bare head, and started scraping the ugly blue paint off the valve cover. I will probably use some Aircraft Paint Stripper on it over the next few days but I had to hold off as there were other cars in the garage tonight.
I figured out today that if I do use the stock motor mount on the passenger side, I won't be able to run the Stinger Stainless exhaust manifold, which makes me sad. It's much prettier and lighter than the stock (already fixed by weld) manifold, so for that reason alone I'm almost hoping to have to make custom mounts. I'll be able to get some work in up until about Christmas, so we shall see what happens!
Doug
Go ahead and make the custom mounts now. you won't be happy until you use that header.
Skervey
HalfDork
12/18/16 8:29 p.m.
I vote new mounts to. Still pumped on this truck. There is a really clean on that shows uo at the cars and coffee Charlotte meets and every time i see it I this of ur build. Kinda makes me want a mini truck
Well, I did get the block loaded up and dropped in today.

Ideally, I'll be able to reuse the stock body mounts to avoid having to make/weld both sides.
Passenger side: Stock motor mount uses the hole with a bolt in it, the one underneath it, and the first one to the right side. I would like to use the hole immediately to the left instead given custom mounts are going to happen.

Driver's side: Again, the bolt attached to the chain is the furthest left mounting hole on the stock mount, with the 2 stacked holes on the right. I'm not sure which holes I'd try to use on this side.

Looking at clearance on a complete engine, the crank pulley hangs down a little below the lower edge of the oil pan, so there's a clearance concern there.
Here's the general frontal clearance on the front side to the sway bar. I will have to make some sort of measurement to make sure I'm not right on the sway bar there. Nothing is completely set yet front-back, I just wanted to get some general approximations tonight.

Furthest forward part of the engine is the water pump pulley, no matter which pulley it is.

Here's my template process. Started out with a full sheet of paper and rubbed down the general shape of the body mount surface. Second sheet is fresh with the correct shape, and it gets a rubbed outline of the holes. Then, Taped to cardboard, bolts pushed through, and outline cut out then shaped! Voila, cardboard template of the area and bolt holes.

So that's where I'm at now. I am open to suggestions on how to make mounts in such a way that i can still use rubber/ hockey pucks, or anything so that I don't have solid steel mounts. Stay tuned and I'll try to keep updating!
Skervey
HalfDork
12/21/16 9:38 a.m.
I feel your pain with the swaybar my rx7 had a similar issue I had to move the bar forward to clear the oil pan. Thankfully I was able to weld up some new endlinks. But I need to do them again because im not taking any advantage of the stiffer setting on my adjustable aftermarket bar.
You may be able to do like I did and move it forward. I used the holes from the front of my swaybar mount and used them for the rear of the mount then added a new bolt for the front. It moved it about 3".
Interesting thought. Skervey do you have any pictures of your custom endlinks? So I'd need something custom to relocate this forward.

I could chop some of the front tow hook off and continue that bracketry up. The endlinks would be new territory, though. It would buy me a lot of extra space!

Skervey
HalfDork
12/22/16 6:01 p.m.
Oh man I didn't think about you having that style of endlink. This is what the RX7 has.
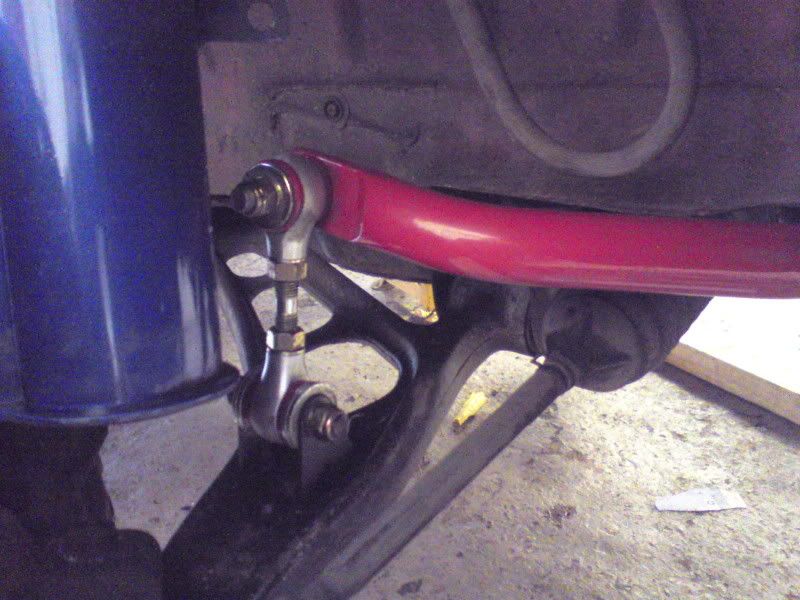
You could still move it forward a few inches and then make it longer or just buy a longer one but you are going to run into binding if it moves to much.