i haven't been very good at providing timely updates and taking pix recently, but i'll get back into that habit.
trans mount progress: because of how the powertrain installs, the mount has to be removable from the bottom. using the Audi mount, i was planning to use 1" square tubing legs out to the bottom surfaces of the C5 frame rails. i quickly ditched that plan when i realized how much of a PITA it would be to weld the mounting tabs in that position. so i sacrificed some weight gain to improve ease of assembly, and put the tabs on the top inboard corners of the C5 rails. i think it's a better design because it loads the legs more in tension and less in bending vs the low mount. either way, the plate shown in previous post doesn't change. i notched the corners to accept the 1" square tubing, and clamped everything in place (pic shows attaching at bottom of rail, but process is the same):
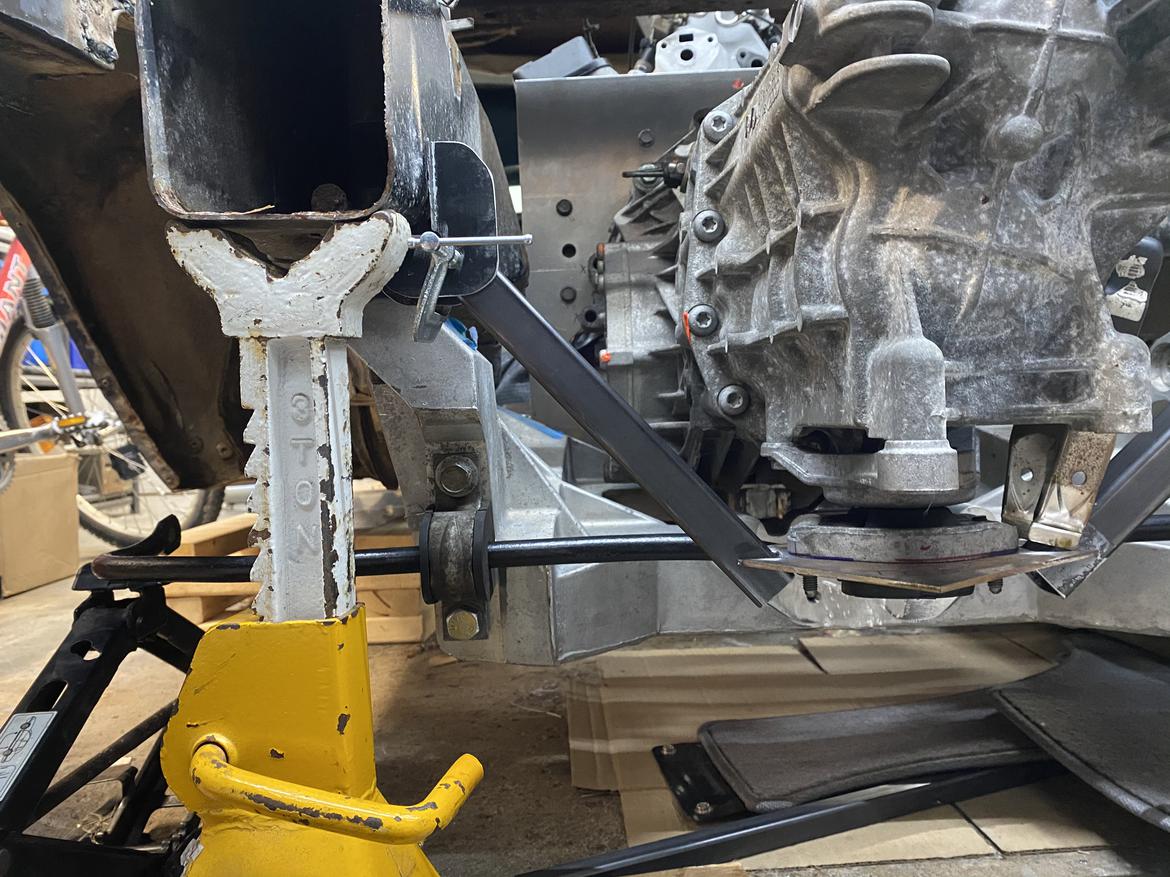
then used drill press to add bolt holes through mounting tabs and legs in one straight shot:
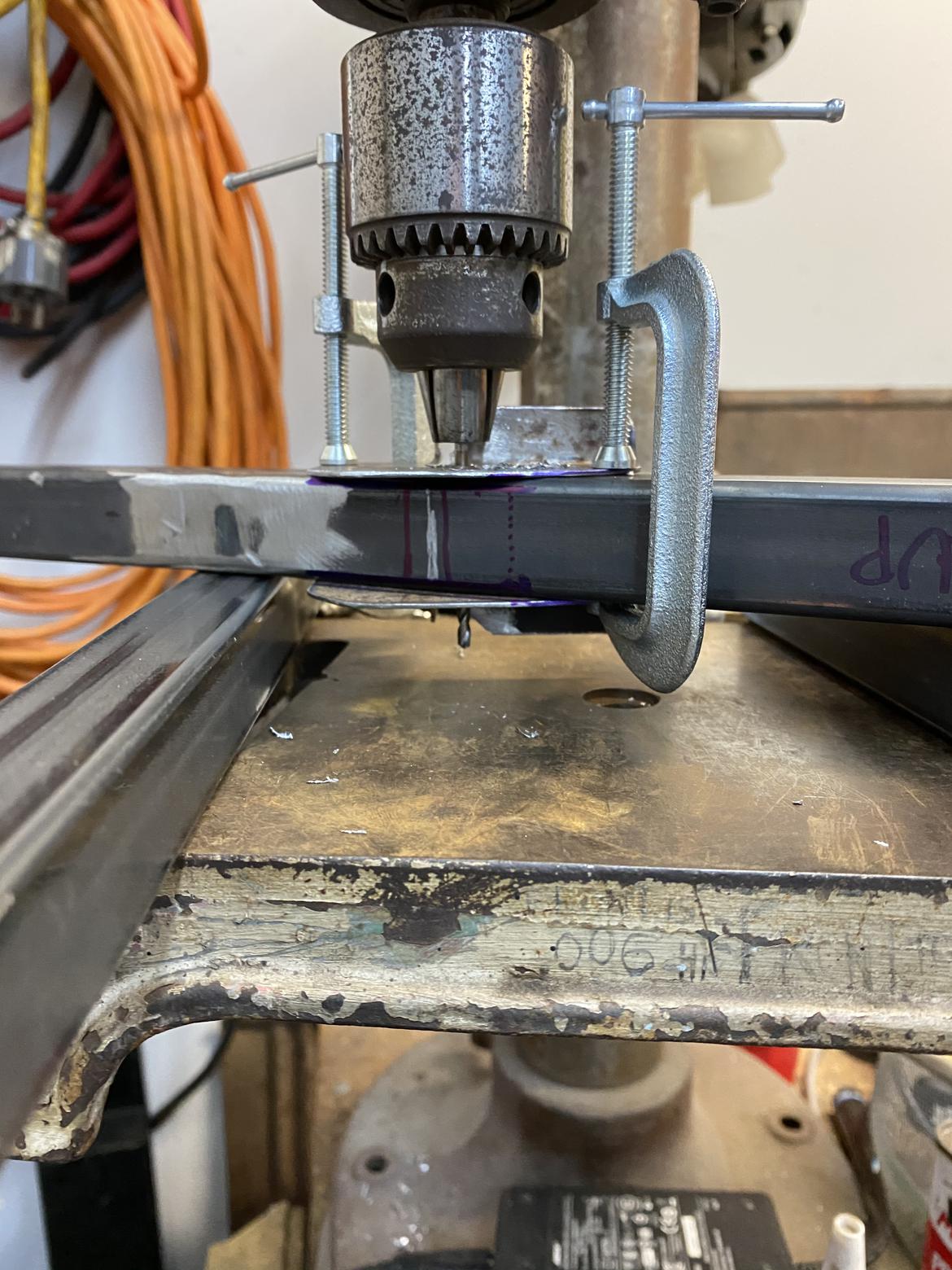
and tacked everything in place:
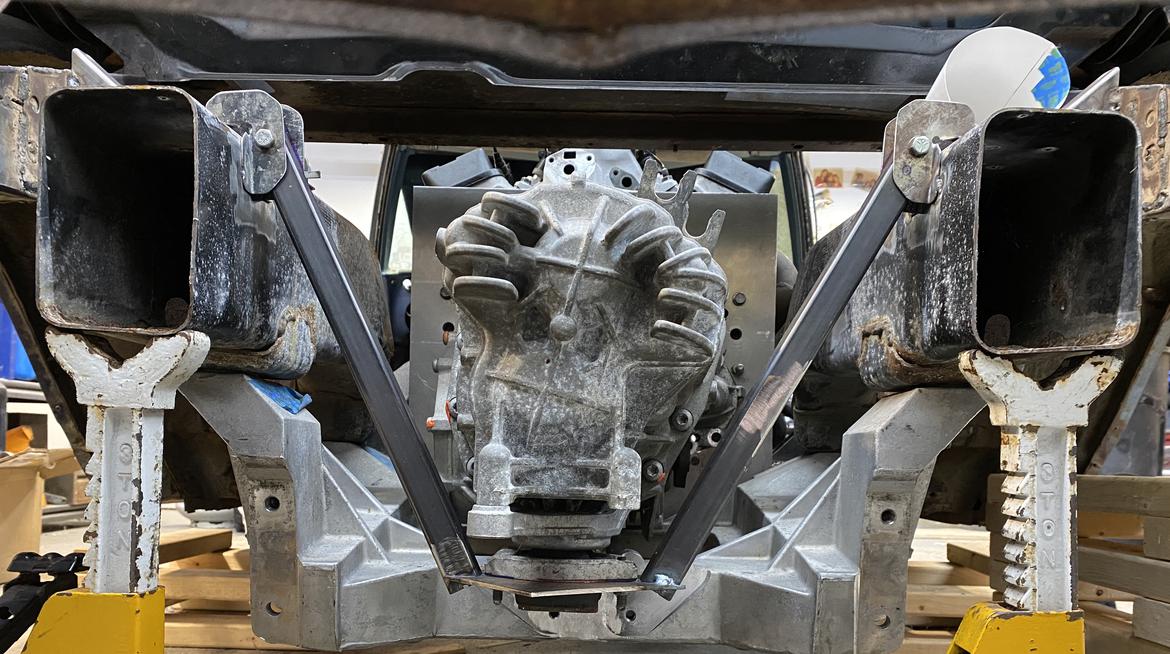
i'm going to trim the mounting tabs and add a piece to connect them together on each side. it will also attach to the upper surface of the C5 rails, farther outboard than the current attachment. this may only serve to make me sleep better at night, but i think it's a good idea to distribute the forces over a larger area. i also need to add a "spine" to the bottom plate to stiffen it against the bending loads where the legs tie in.
gas tank progress: as previously posted, i had to build a 1.5" riser to use the C4 fuel pump assembly in the boat tank. V1 was a "learning experience" for a lot of reasons, so i took a different approach to materials and process for V2. i started by laying out the gasket outline on a corner of the unused portion of the tank (rem: tank was 26" long, now cut down to 16").
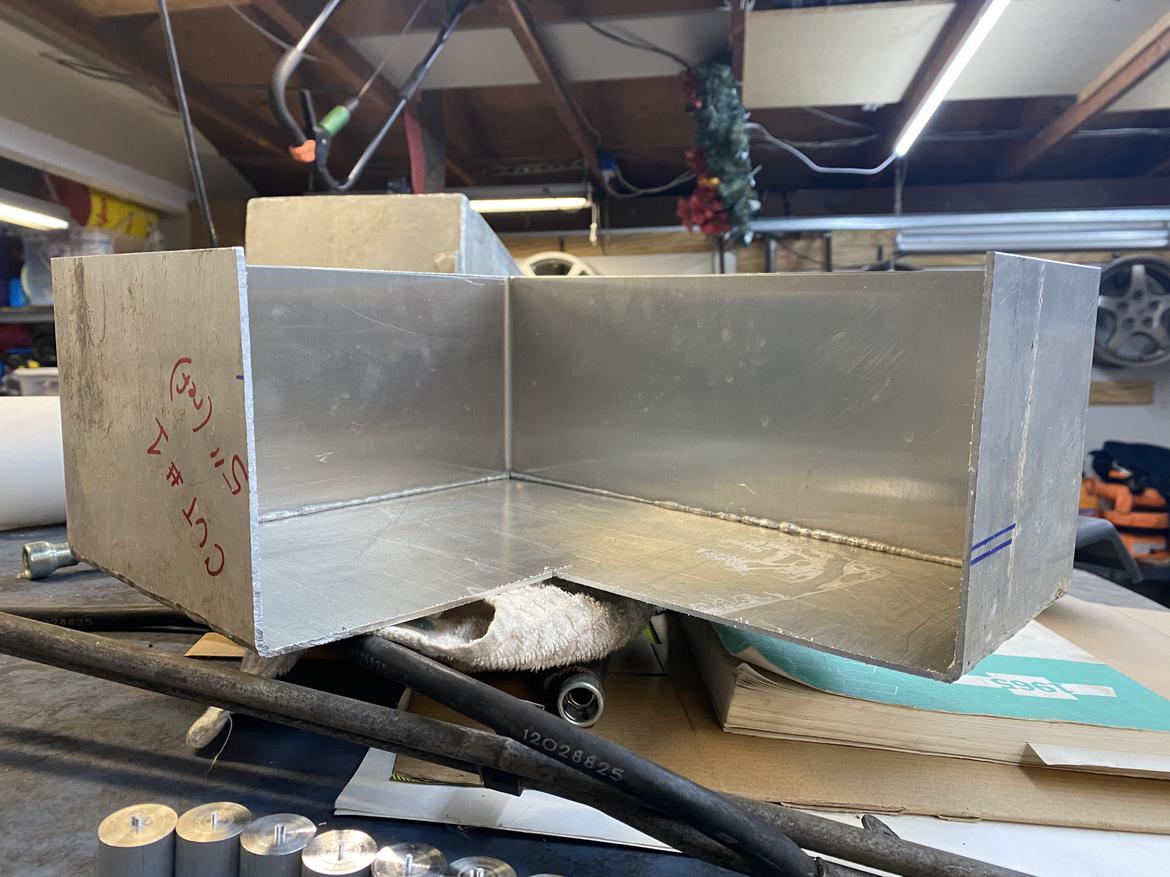
using this corner gives me the top and 2 of 4 sides in one piece. so i cut it 3" high, then took a 1.5" slice off the bottom. this gave me the other two sides in one piece. a little cleanup of the corners and a slight trim of the lengths and it was ready to be welded.
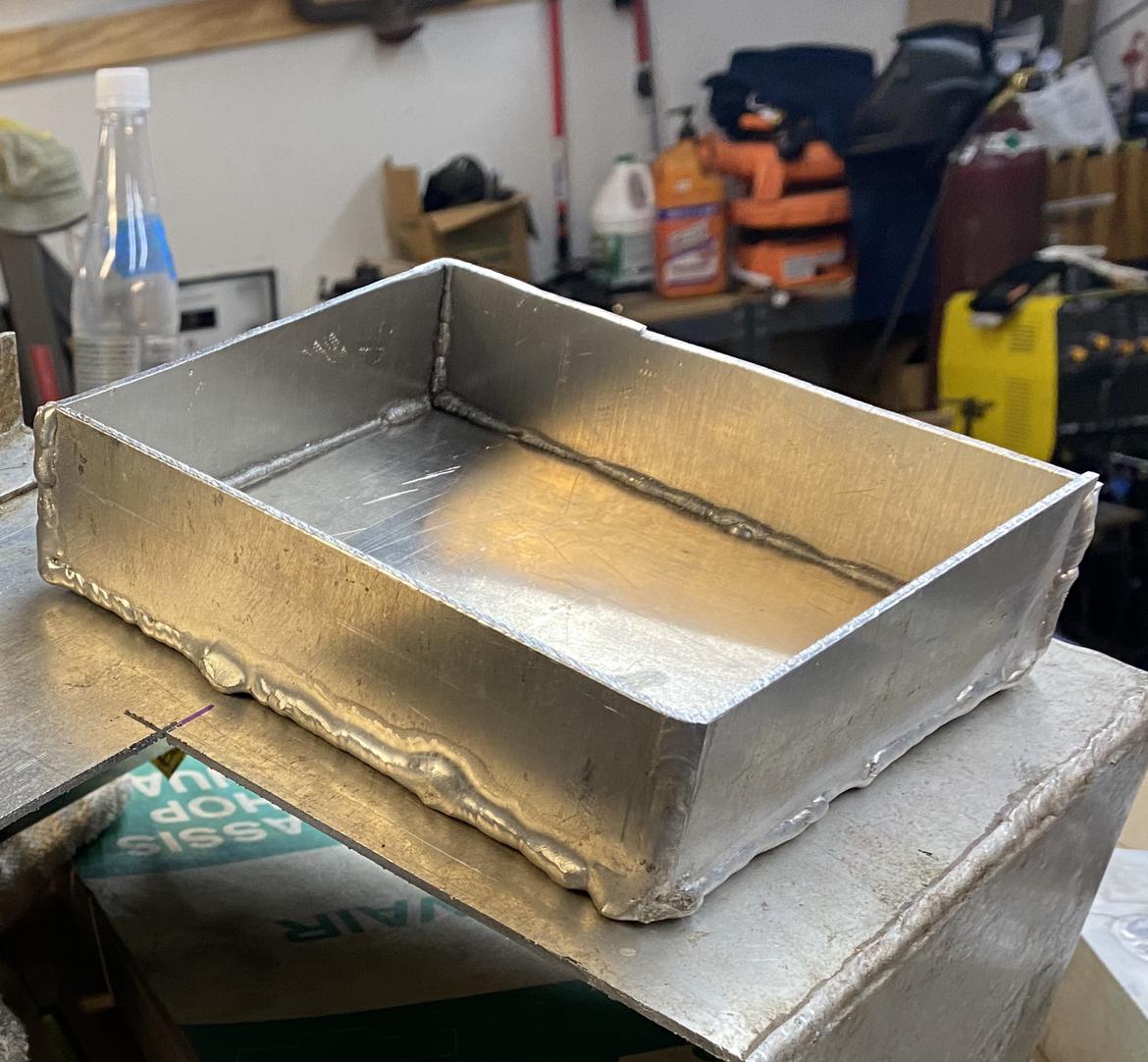
from V1 i learned to use the 1/2" step bit for bolt holes, then measure each hole and turn a shoulder on each insert to make it a light press fit that sat slightly below the surface. this gives me a nice seam to weld and will only require a light skim cut to make the gasket surface flat. so here's V2 and the 9 inserts, fit up and ready for welding:

note that there are four big holes in the top. yeah, V3 wouldn't have them at this point in the process, but i was already set up on the drill press so i opened them up. having those holes there robbed me of thermal mass in welding the inserts, and i got a shrinkage crack because of it (not a problem though, as it's in an area that will be removed). those holes are different sizes because my 1-3/8" step bit isn't sharp anymore. i'll be connecting them with the jig saw anyway, so an exact match on the radius isn't strictly required. i still need to set it up on the mill and skim the gasket surface, then flip it and level the height of the perimeter where it will be welded to the top of the tank. V2 with inserts welded:
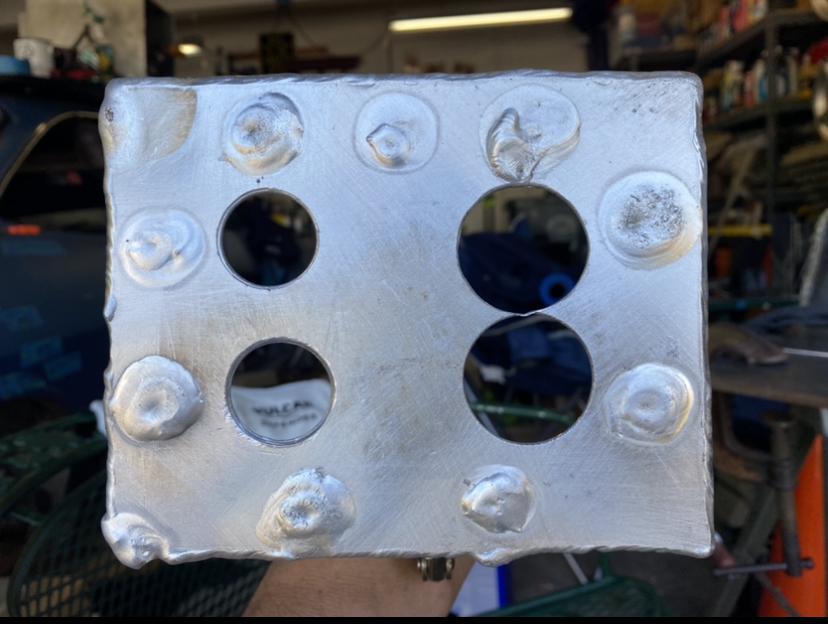
as for the tank itself, there were three ports on the top surface i needed to remove and close: 1-1/2" dia fill tube, 3/4" pickup tube, and 5/8" vent tube. for the large one i cut a patch with the jig saw and smoothed the edges with a flap disc. for the other two, i turned plugs from 3/4" round stock. inspired by the Nelson family, i added lightness by counter-drilling the underside of the plugs :-)
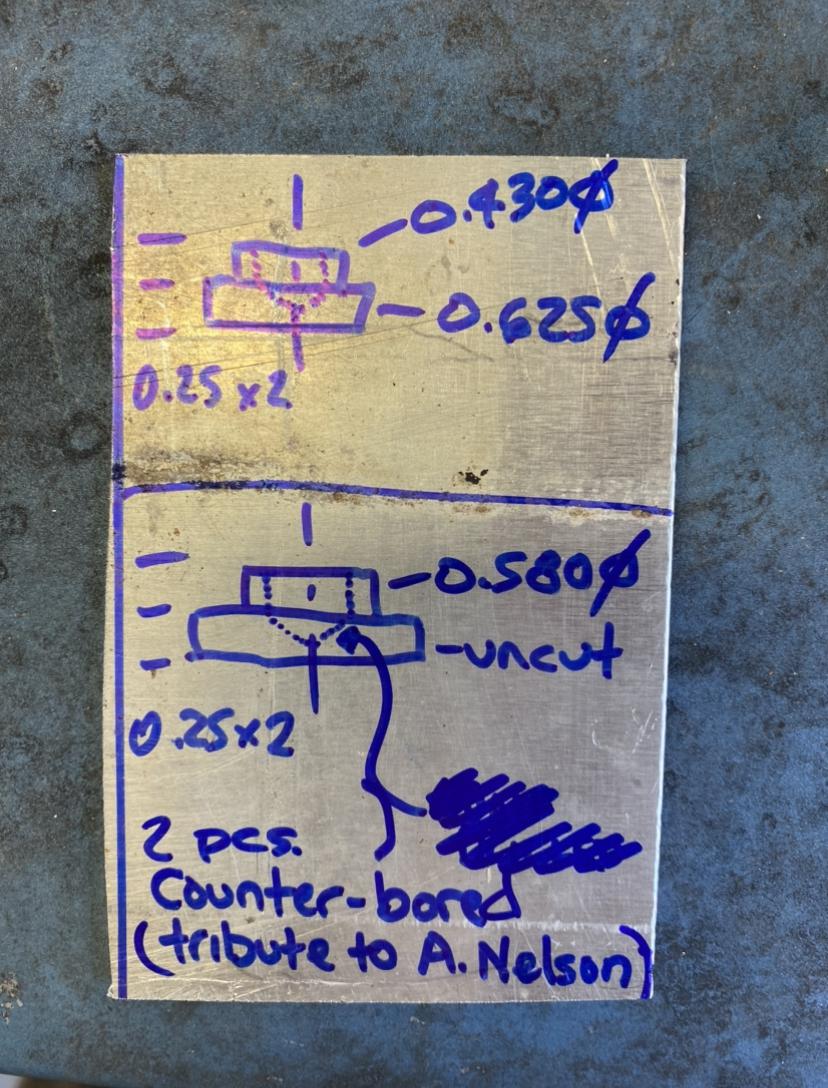
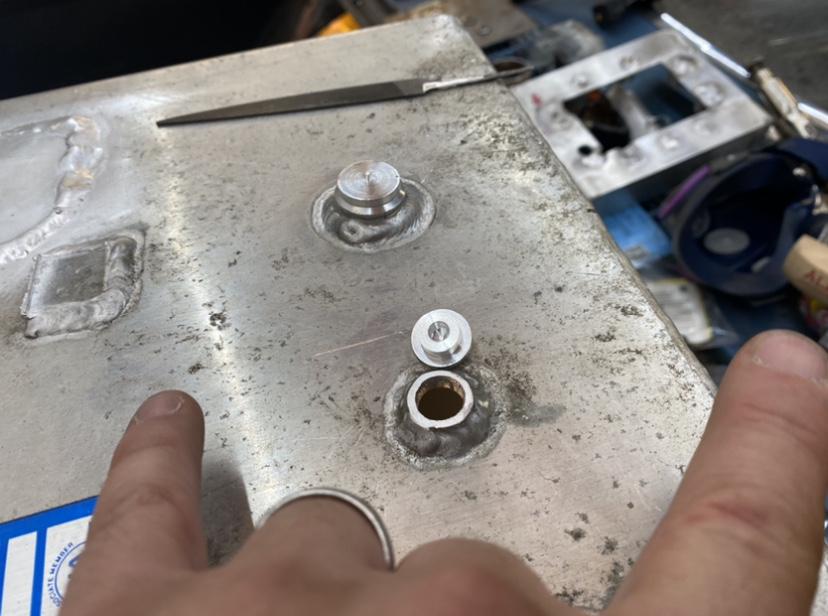
then everything went straight to Hell when i welded them in place:
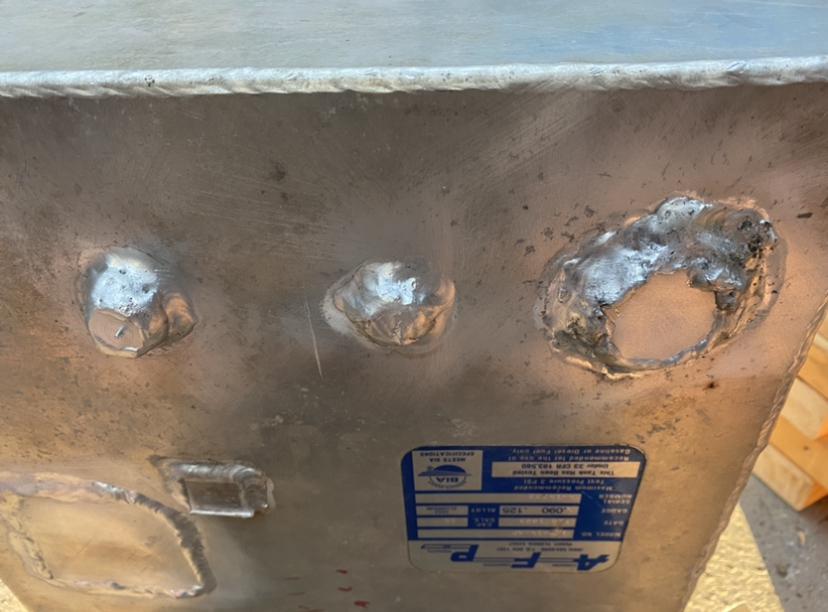
- maybe because i used a wire wheel that wasn't stainless and wasn't dedicated to aluminum? i did follow the generic wire wheel with my Al-only stainless brush, if that matters.
- maybe because of the thickness difference requiring so much heat only on one side of the joints?
sure, they look like E36 M3, but do they leak?
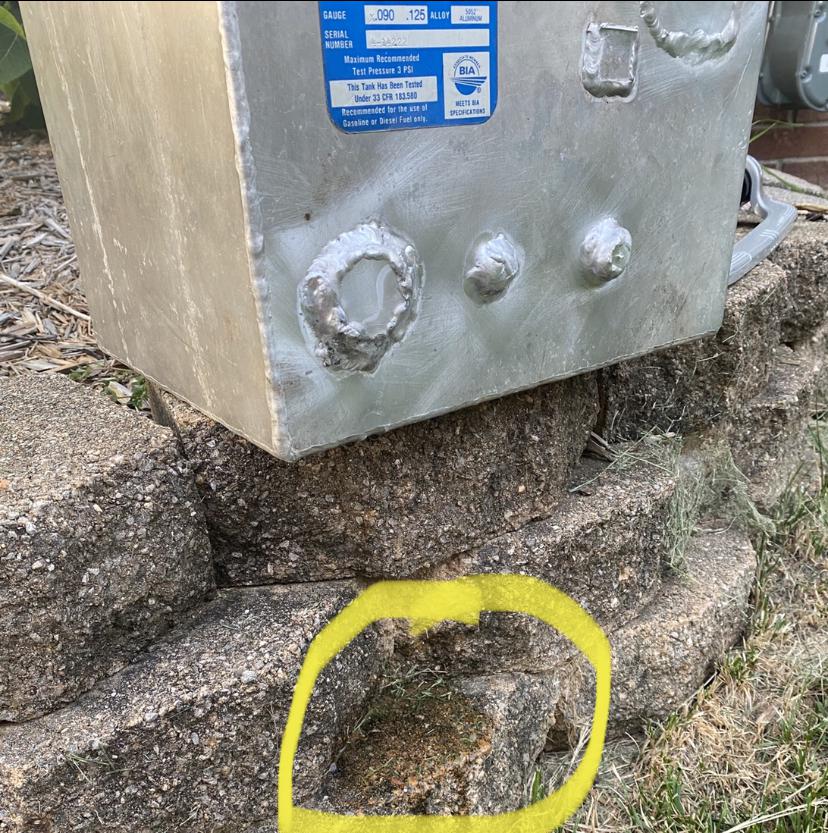
berkeley.
anyway, another lesson learned. these look so terrible that, even if that one didn't leak, i'm cutting them out and replacing with a single flat patch from the leftover tank bits, which gives me an easier-to-weld lap joint of equal materials.
learning by failure takes a lot of time, but I'm getting better at it.