Today's episode brought to you by finding a Tractor Supply (oddly enough about five minutes from Patrick) that actually had argon bottles in stock. $120 later, I got a Hobart prefilled 20cu-ft unit that will probably last me two or three years. Also brought to you by uamee - IL-76 because I am in a hardbass mood.
Actually from yesterday - made the rear fill-in, then spent way too much time boogerwelding it in with flux core. Headphones hanging from harness bar because they interfere with the welding helmet.
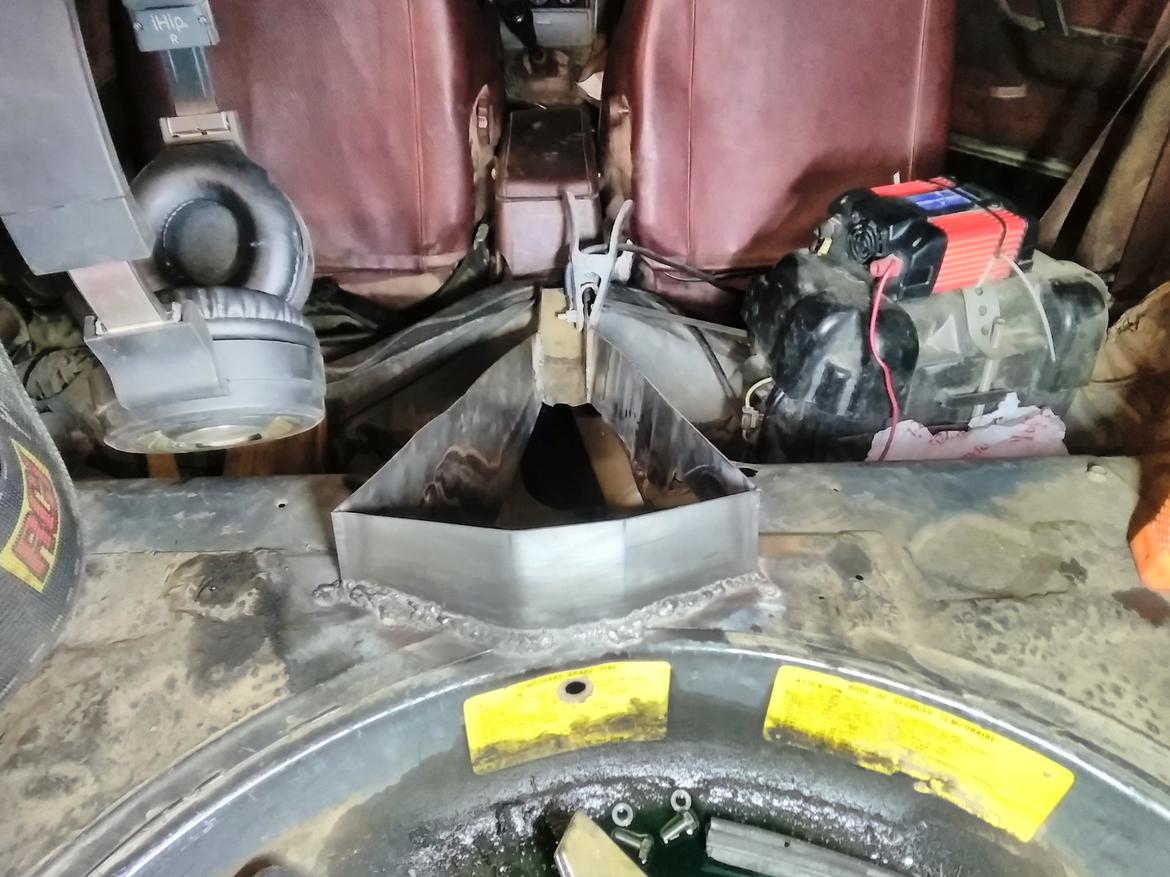
I'm actually surprised that the lake of 2 stroke oil in the spare tire well didn't catch fire.
Today: Now with 100% more argon/CO2, I went over all of the boogerwelds where I could see light through, then made this little cover pieces for the areas that broke out, and welded them in. Had a LOT of feeding problems. I'm using the .6mm wire that came with the welder, and it really sucks. Loves to kink and when it kinks it kinks in the sheath, so I have to cut it off at the spool and then pull it all back out.
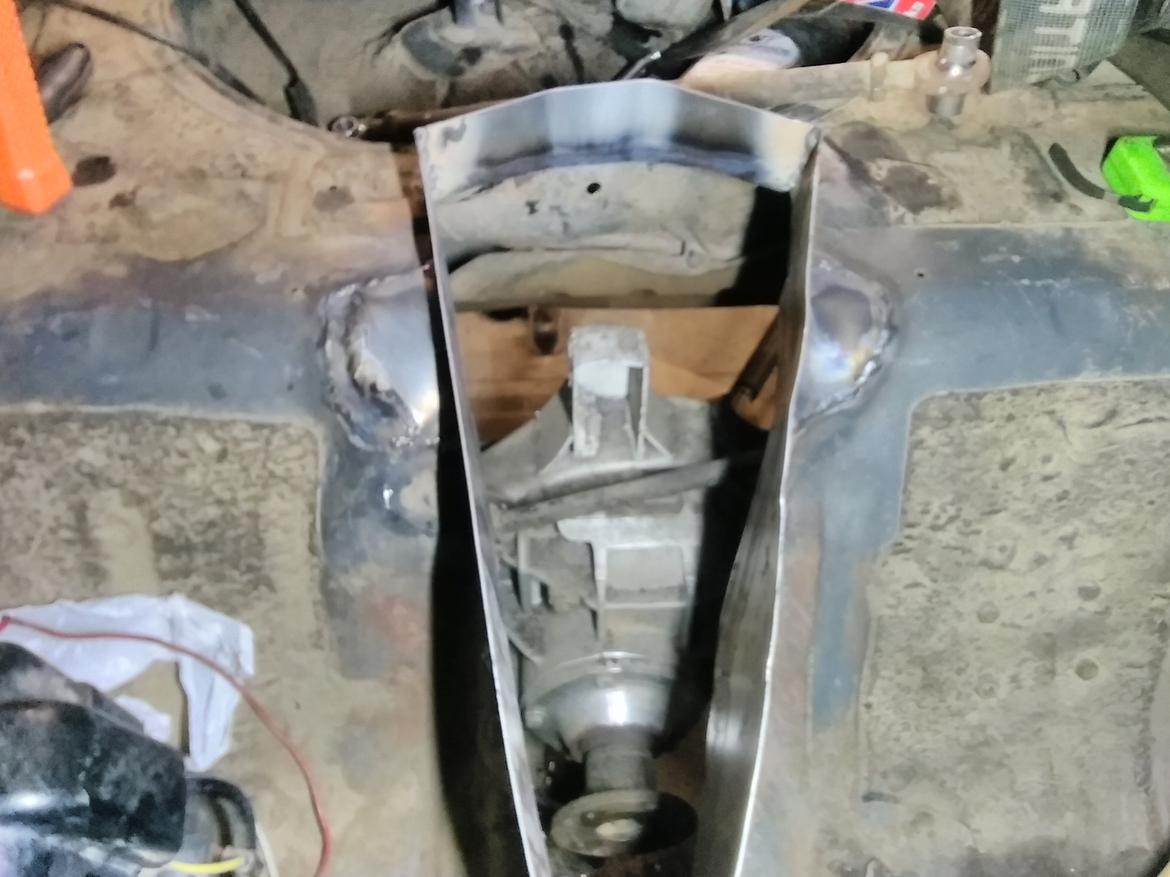
Not pictured: Redrilling the forward link mount up and forward to complement the up and forward change I'd made at the axle end to clear the raised Watts. I am hoping this will help keep my drivetrain angles from being so sensitive to ride height.
Cleaned, scuffed, and painted that, then went to work on the $22.50 pair of springs I bought at Summit. They're for the front of a Jeep, and the description said that they are 136lb-in as is. I have been keeping an eye out for some 150lb 13" long springs. Have 175s and they are a touch too stiff, have 125s and they are too soft. Spring in background is one of the 175s for reference.
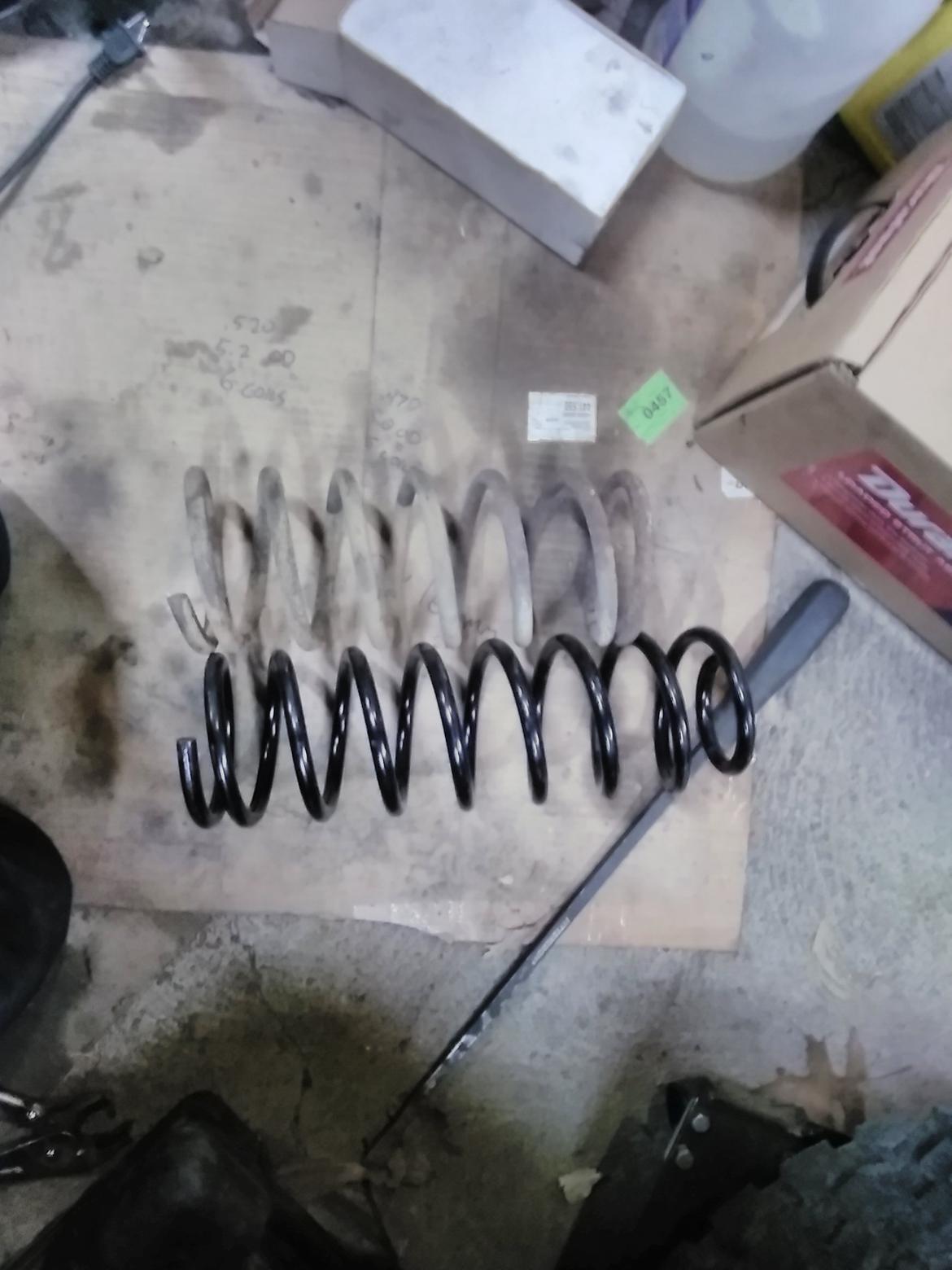
Math time! A coil spring can be thought of as a stack of many, much stiffer springs. As such, you can back-calculate the rate of each working coil, and then divide that by the number of working coils after you cut it:
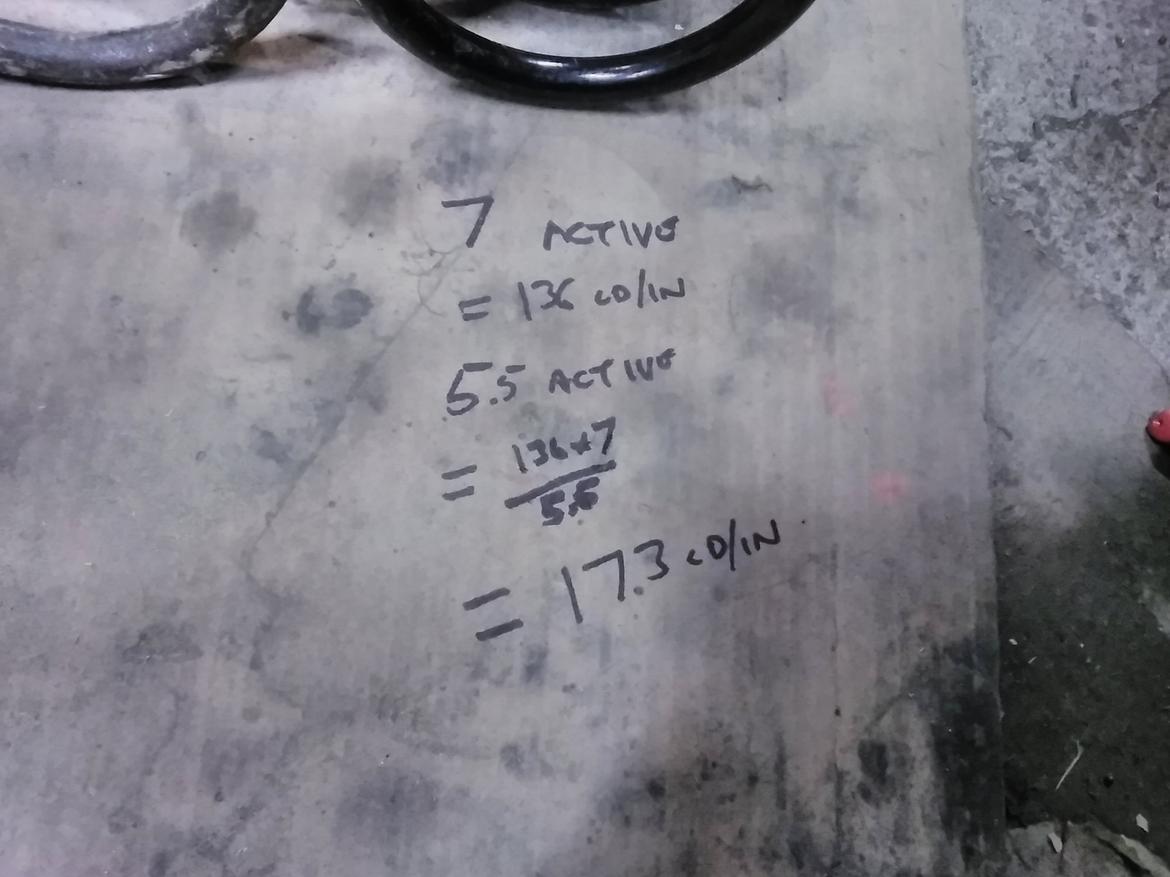
So, once cut to length, it will be just about exactly what I already have. Nevermind. Hey, they were $22.50, and I might still have a use for them someday.
On to the muffler. Racing Beat changed suppliers or something, because the new muffler is significantly different. It no longer collects, so my car will now technically have a true dual exhaust system. Not sure if that is good, bad, or indifferent. The resonated tips are huge in diameter as well, which may translate to more noise. Since they are so large, you can peek in there and see how the muffler is constructed.
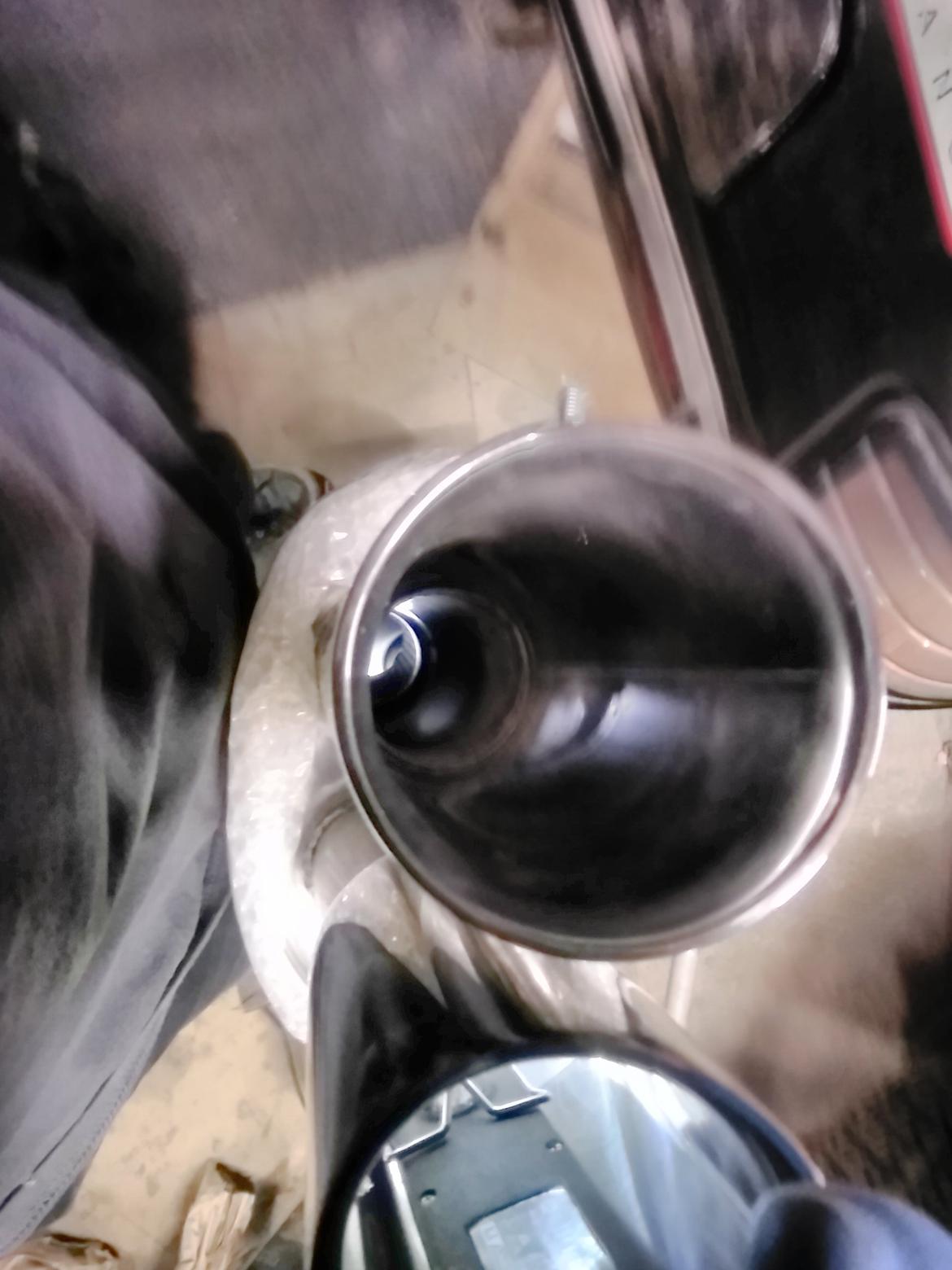
It looks like the front half to 2/3rds of the muffler is a perforated core packed type muffler (I believe RB uses/used stainless steel swarf instead of fiberglass), and these two pipes exit into a termination box, and the resonated tips are just the outlet. Will find out tomorrow how it sounds.
The muffler itself is a lot smaller than the old style one, too. Weight is about the same, within guesstimation, so even though it is stainless it must be very thick walled stainless.
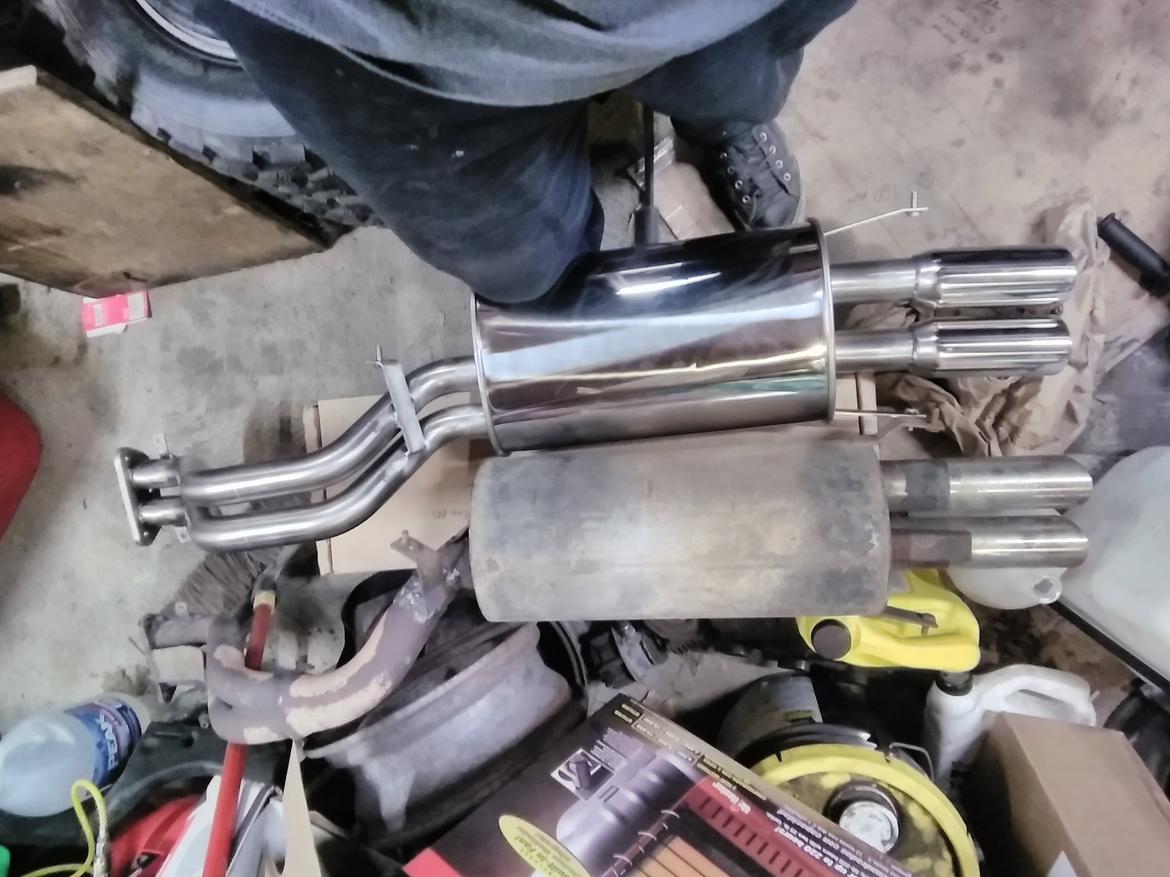
The left side pipe gets VERY CLOSE to my Watts stud.
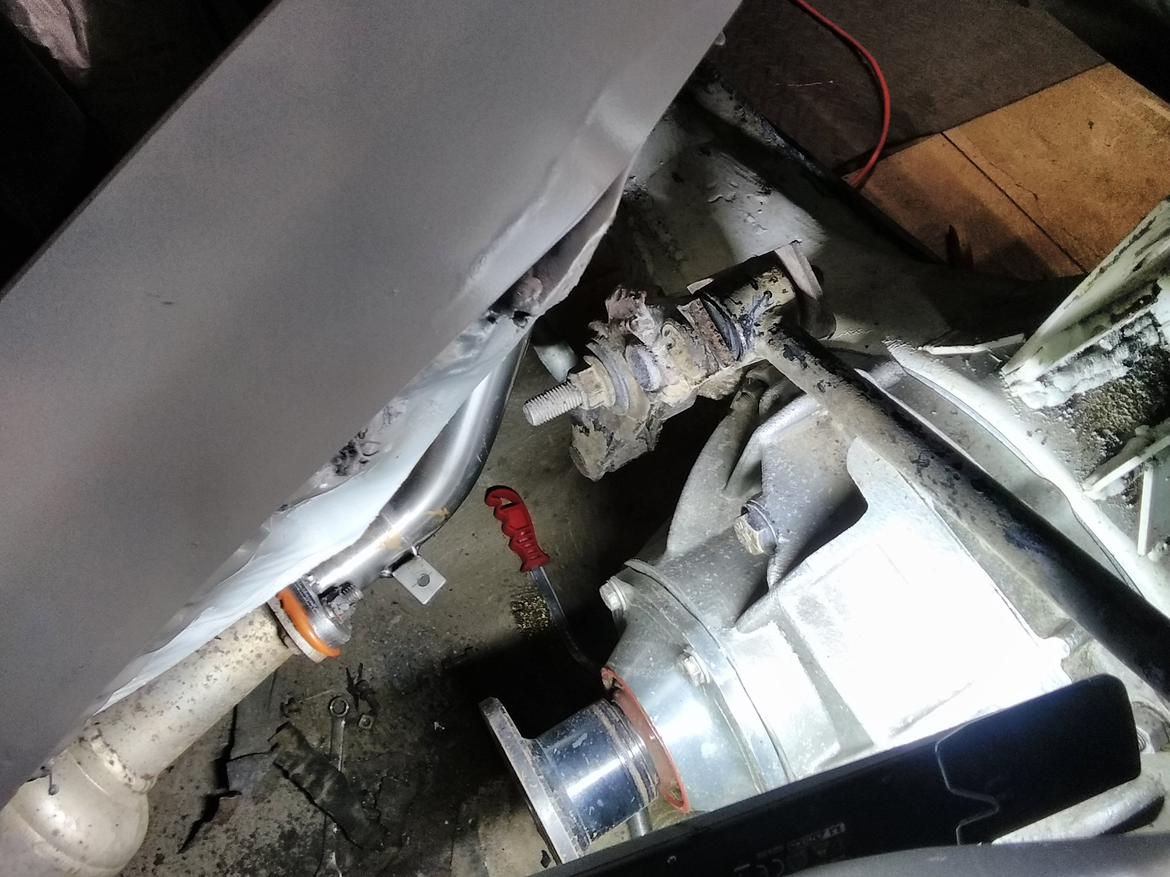
I popped the upper link in and jacked the axle up. The stud got so close that it could easily touch the pipe, but it never actually did touch.
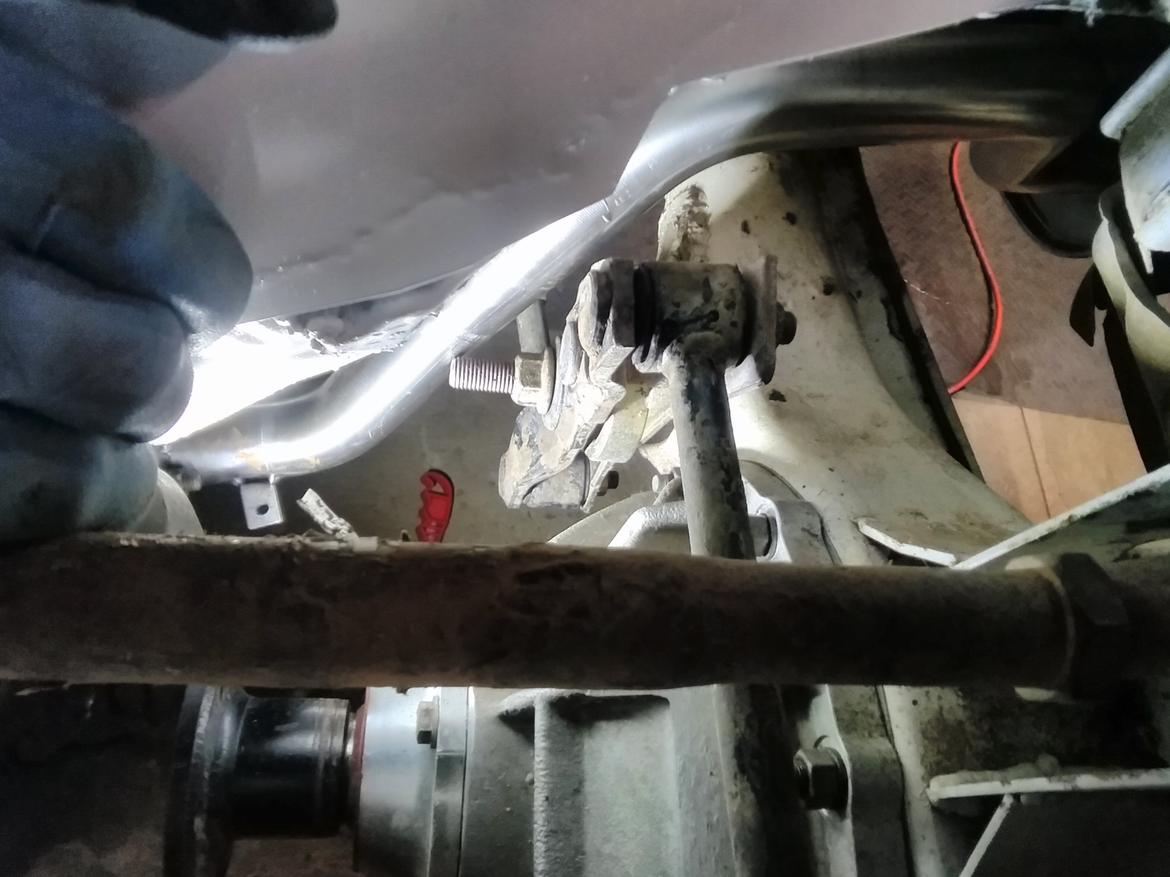
I whacked off about 12mm or so. I want to leave it long because I still think I want to mount the Watts in double shear, and I do have a pinion support bracket to use as a starting point for a brace.
Installed the springs, set the car down on the axle, bounced it a bunch, and then set the pinion angle. I set the pinion angle to exactly the drivetrain angle. I know this is without a load in the car, but you have to start somewhere. Then I popped a driveshaft in and measured the driveshaft angle. For the record, the way the car was jacked up, the pinion and drivetrain are at 1.5 degrees from vertical and the driveshaft is at 1.8 degrees from horizontal. So there is .3 degrees of U joint angle.
But... remember when I said I'd redrilled the forward pivot? Now the top of the rearend doesn't come forward as much under compression. So, now the rearend hits the spare tire well... and also will destroy the metal I just installed, if the suspension compresses that far.
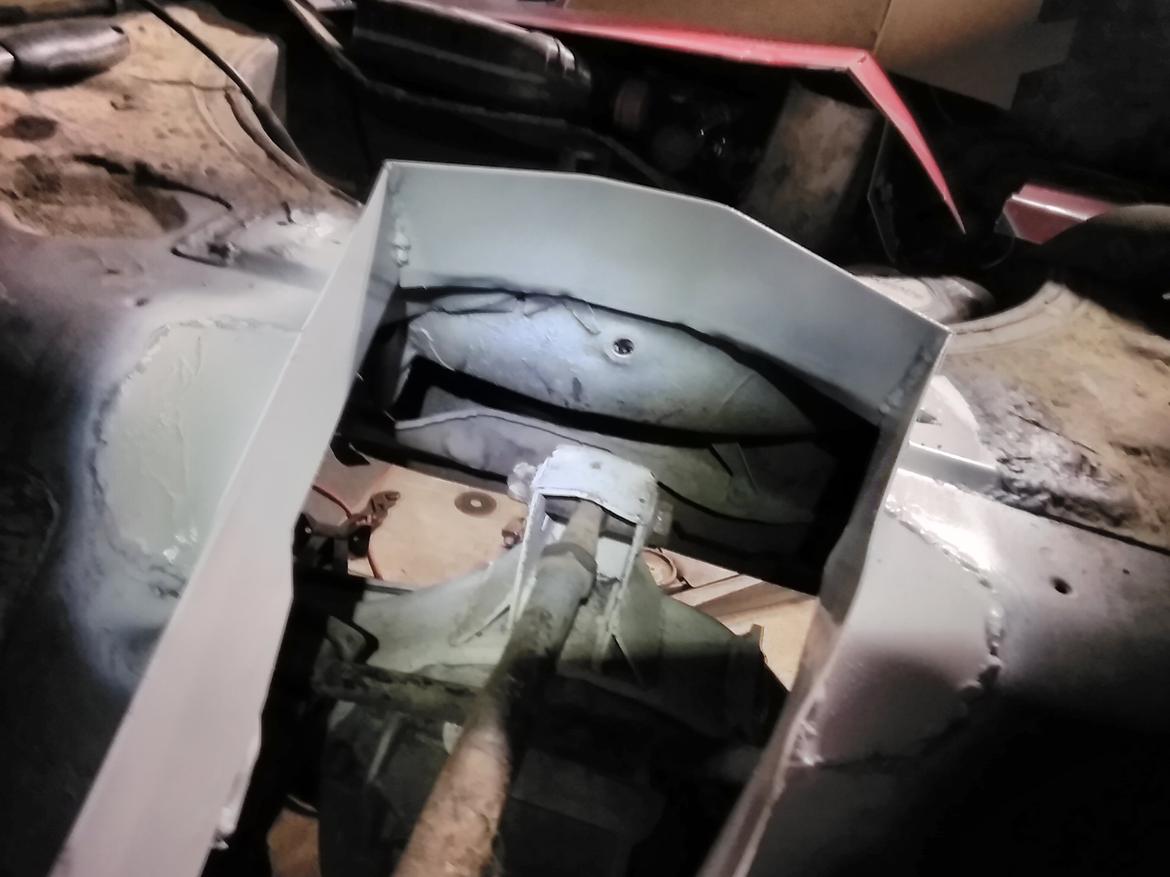
Need to have a think.