egoman
Reader
2/8/21 6:38 p.m.
Woke up Saturday morning to a temp of -50F.
My water was frozen and the cars wouldn't start, well almost all the cars!
My dependable Pontiac Wave (A Dae-Woo In disguise) fired right up. It didn't like it but it ran. If you had to guess which one I got running next I don't think you would have come up with my diesel yard tractor. That's right, after less than 20 minutes of being plugged in it fired right up! Of course it has 3 full size batteries on the front of it for weight to balance the snow blower and they are all wired in. Then the wives car needed to be plugged in for 2 hours and get a new battery. The old battery was slightly larger than it was supposed to be at this point. Then after surveying the water problem at home I called a local plumber to fix it. That's correct the plumber called a plumber! Don't worry it gets funnier. My nephews wife called me with a plumbing emergency of her own, so off I went to help her. That's correct, I was doing a plumbing job for free while I paid for someone to do my work.
These are the reasons that a lot of Canadians wait to start posting their build threads because a lot of time is spent staring out the window at ice fog and snowstorms.
I knew that would be the case when I started posting and I have a library of posts to come yet. That's right I endure these winters just for you guys, LOL
Those of you in the great white north, stay warm! Those of you in the south, well the heck with you EH!
egoman
Reader
2/11/21 5:44 p.m.
egoman
Reader
2/12/21 8:51 p.m.
While there isn’t much to see here, this is vital!
These pieces will hold the rear end exactly where it needs to be for the foreseeable future.
Nothing more than some 2x4 tubing with a 3 inch hole saw drilled through and then cut in ½ and cut to length. This locates the rear not only laterally but also at ride height. That’s why I have the tape measure picture of the tire and wheel diameter. By the way there was no trust in the cut at the bottom. All measurements were taken from the 3 inch DOM tubing set on top. Overthought for sure but if there are no variances to chase down later then we can concentrate on other stuff later?
This will not be the last time you see me do this to center pieces exactly where they will end up later.
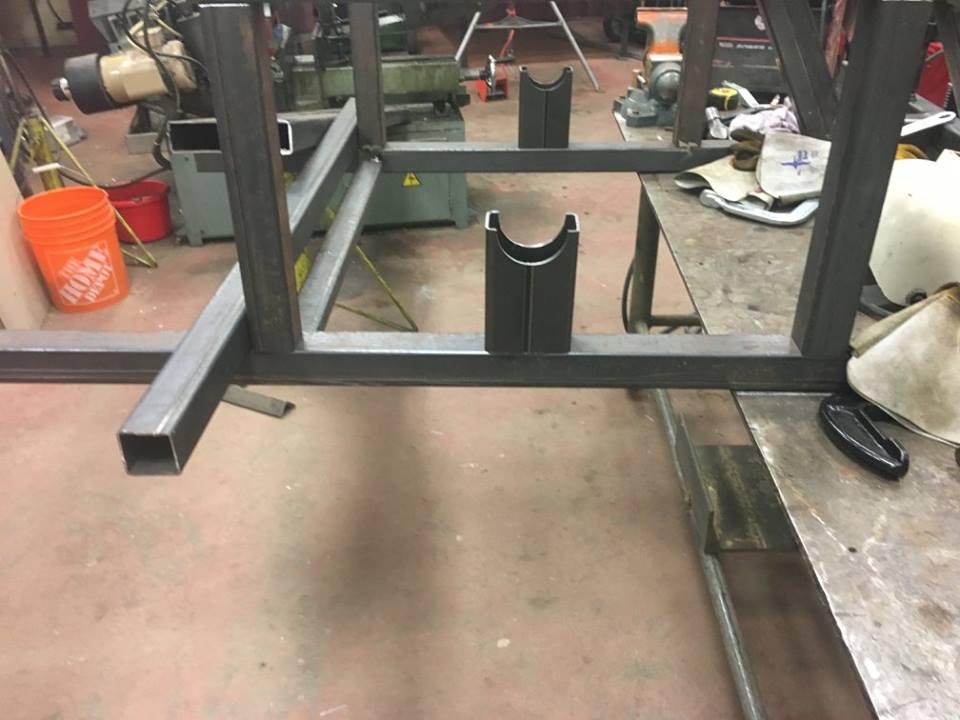
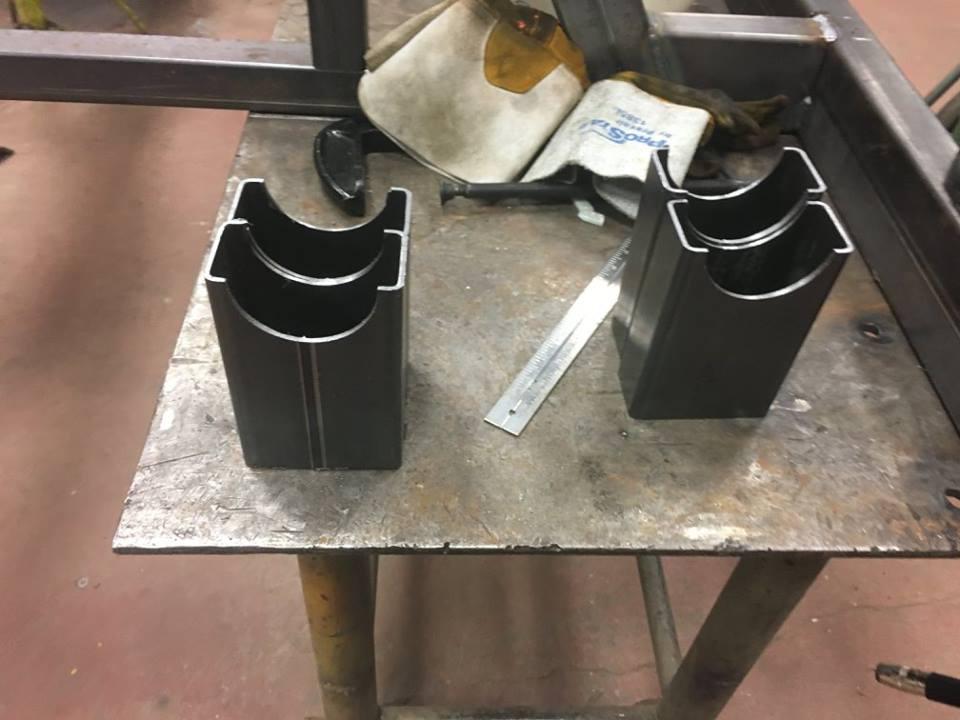
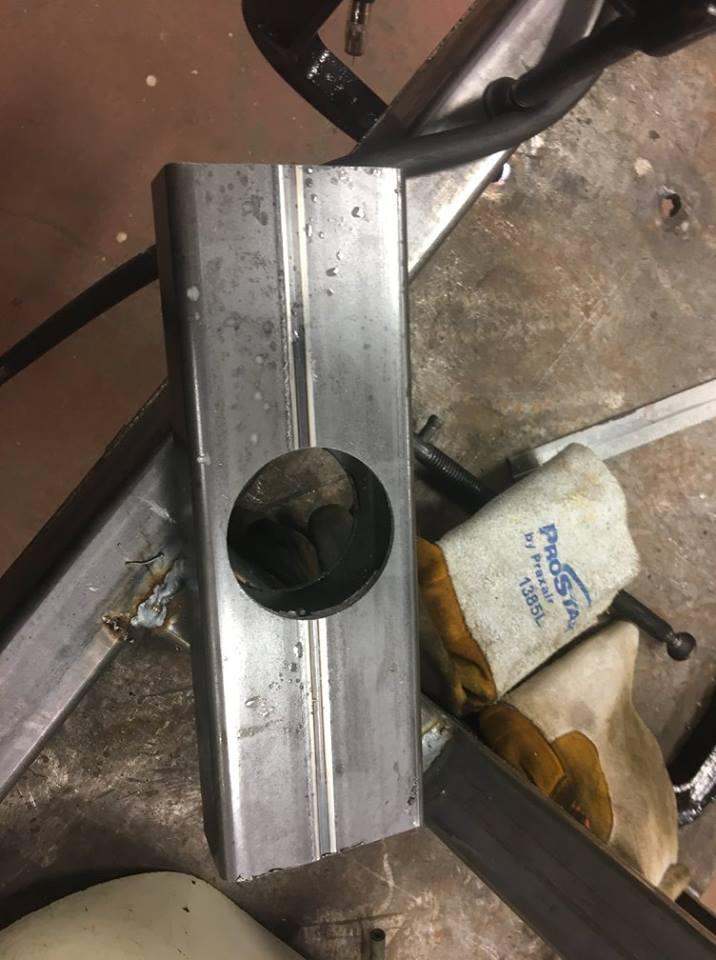
egoman
Reader
2/14/21 11:36 a.m.
egoman
Reader
2/17/21 8:34 p.m.
egoman
Reader
2/21/21 10:38 a.m.
egoman
Reader
2/28/21 7:35 p.m.
In reply to egoman :
These should be the last brackets that will allow me to use the Corvette C6 ZO6 brakes and E-Brakes on the 9 inch floater for the Cougar! Going to get them cut probably next week with all the other brackets for the rear suspension.
I cheated and made it so one drawing allows for the cutting of two different brackets. You can see what I did in the cutting instructions in the lower left corner. The double shaded drawing is the revision...... kind of. Both will need hand trimming.
So just minutes after posting that I had it all figured out I double checked the measurements.
Yesterday this stuff was so hot that it burnt my hands just to carry it in the building. (That was just from sitting in my truck not even in direct sunlight!)
Now that the calipers and the bracket have cooled down. My measurements didn’t remain the same. Double and triple checking still won’t prevent all mistakes but should help reduce the overall number a bit!
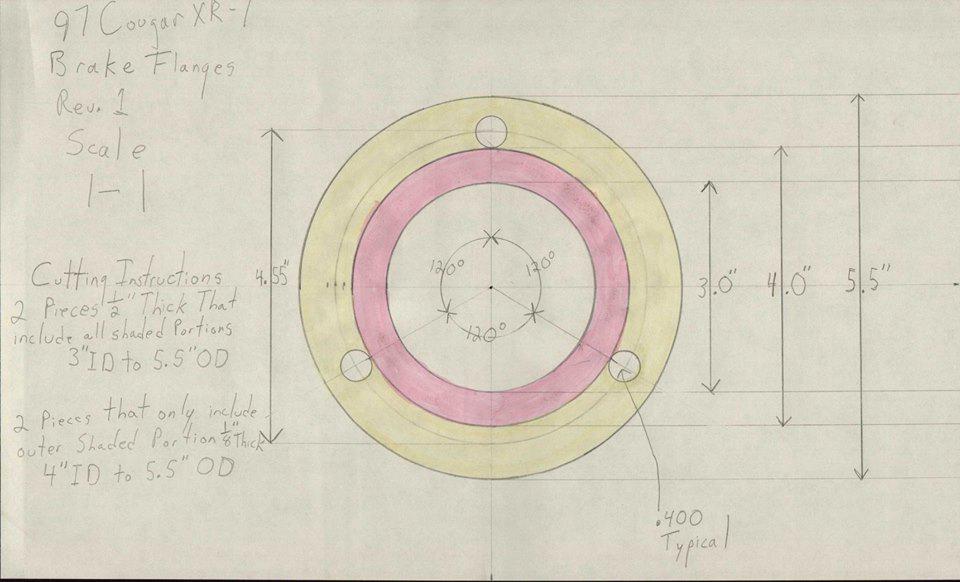
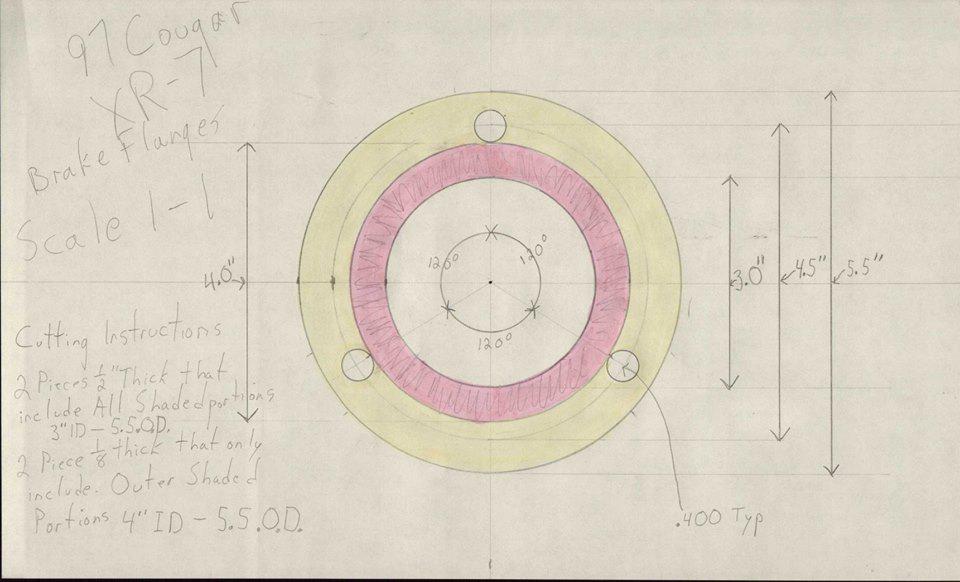
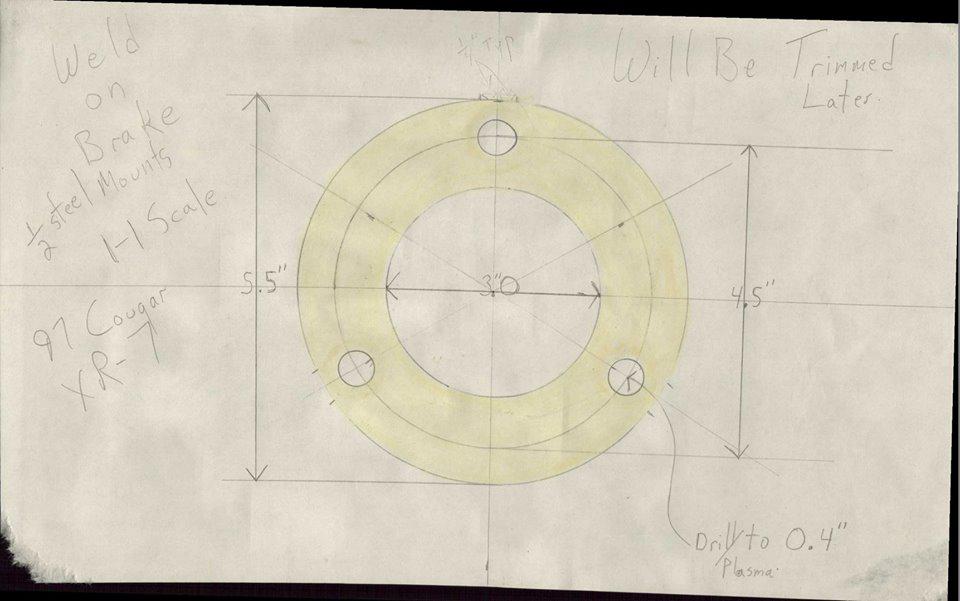
egoman
Reader
3/6/21 2:51 p.m.
egoman
Reader
3/7/21 7:08 p.m.
egoman
Reader
3/8/21 10:24 p.m.
This thread delivers! Stoked on the chassis fab and looking forward to seeing the finished brake solution. Good idea cutting down the spindles.
egoman
Reader
3/9/21 8:43 p.m.
In reply to Shavarsh :
Its just getting started. Thank you for following along!
egoman
Reader
3/10/21 7:13 p.m.
egoman
Reader
3/10/21 7:25 p.m.
egoman
Reader
3/13/21 7:51 p.m.
egoman
Reader
3/17/21 4:35 p.m.
egoman
Reader
3/17/21 4:45 p.m.
egoman
Reader
3/21/21 11:35 a.m.
I love that this will all end up in a cougar.
In reply to Shavarsh :
Same, I need this kind of custom suspension on mine!
egoman
Reader
3/24/21 7:17 p.m.
In reply to Shavarsh :
Honestly when this all started it was supposed to be a Thunderbird SC. A good deal turned it into a Cougar.
egoman
Reader
3/25/21 7:13 p.m.
egoman
Reader
3/25/21 7:24 p.m.
egoman
Reader
3/25/21 7:41 p.m.
egoman
Reader
3/27/21 9:49 p.m.
When I started this thread I wanted to have enough material so that I would finish the car with the people who follow along. I have also indicated that I have a lot of material for you to peruse.
Well seeing as I have become a school teacher and am now taking spring break it is nice to be getting some more work done. Honestly this is the first progress on the car for several very cold months.
But the storage vault can keep us going for a few years at least. I did state that we would have progress to show even when I am not busy.
And again I am welcome to field comments and suggestions from the people that follow us.
Of course as always have a nice day!