In reply to mblommel :
Yes sir, used a Core 200 for this scan (probably should have went with a 300) It's always good to hear from happy GOM users. What's your application?
By the way, I definitely dig the large router idea. An ATOS system combined with a multi-axis CNC router would be a dream come true!
In reply to WillHoonForFood :
Industrial gas turbine. It's a fantastic system, the software is so dang good.
Awesome build, will definitely follow this. I'm up on the other side of Charlotte; let me know if you need help with any of the mechanical design. Happy to knock out some CAD work if you need anything done.
275nart
New Reader
8/25/18 11:46 a.m.
Keith Tanner said:
Oh, definitely encouragement. I've moved designs from the digital realm to the real, and then made adjustments once I actually saw it. I think you're doing just the right thing.
Plus those wireframe models look so cool.
Okay, I wasn't sure how to read that! What Jon (willhoon) is doing is very important to my build and the accuracy of my body. The wire buck may have some purpose after I'm done- yard art at the very least.
unevolved said:
Awesome build, will definitely follow this. I'm up on the other side of Charlotte; let me know if you need help with any of the mechanical design. Happy to knock out some CAD work if you need anything done.
Appreciate the offer!
275nart
New Reader
2/8/19 2:39 p.m.
This is obviously a long overdue update. I was presented an opportunity to have nose and tail portions of the car 3d printed... yes, 3d printing part of the body buck! I bet this is the first time you will read that. While 3d printing full scale may not be an economic solution for building a whole car, there are a lot of opportunities to print detailed parts or molds (very quickly). I didn't even consider this earlier on in the build, because I just didn't know printing in this scale was possible. The massivit printer prints something like 1foot per hour for something of this size- it's nuts, and puts my rinky dink desktop 3d printer to shame.
While I could use these printed parts to build sheet metal panels directly from, I will be bodyworking and painting these printed pieces and pulling splash molds from them and will build the sheet metal from a fiberglass part instead.
After slicing to my liking, preparation of the model and printing was done by the sign connection in Gastonia, NC on their Massivit 3d printer and anyone who's serious about printing larger parts should definitely be talking with them.


In reply to 275nart :
I didn't see that one coming. You're full of suprises. In a good way 
84FSP
SuperDork
2/8/19 4:58 p.m.
Holy carp - that’s amazing. Is dimensional accuracy as good as expected? I would worry about war page on cooling but know nothing about those monster printers.
275nart
New Reader
2/8/19 5:52 p.m.
Warping is not a problem, thankfully. It is made of a resin which is extruded (not heated) and then cured instantly by a UV light that follows right behind the print nozzle.
mke
Reader
2/8/19 6:03 p.m.
Love it!
Edit: with a little more time to write my question is about the windshield and lights. A few years back i had an idea to make a modern 275gtb (small and light unlike the new stuff) and found an actual car designer interested in helping....he was really talented, this is what he came up with:
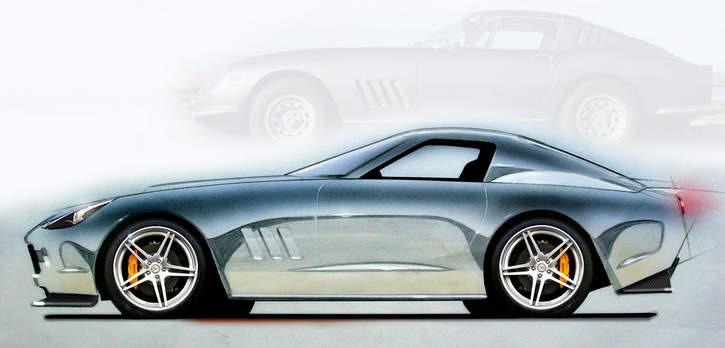
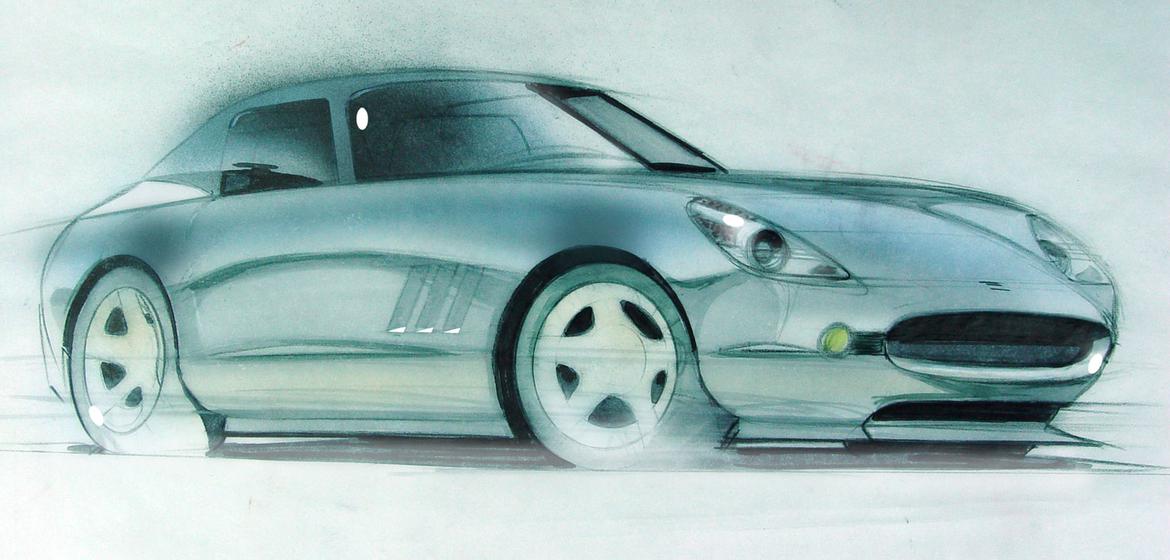
The big issue in getting it to look right though was the windshield.....he ended up using an actual 275 windshield. The other issue was the headlights, I didn't believe him and thought we could just pick something but when he did the sketches Porsche lights made it look like a Porsche and so on, the ones shown here are Ferrari California and worked pretty well. I've never had the time or really the budget to move it forward with the frankenferrari never ending but those were the design issues we ran into, hope it help you.
mke
Reader
2/9/19 7:55 a.m.
275nart said:
After slicing to my liking, preparation of the model and printing was done by the sign connection in Gastonia, NC on their Massivit 3d printer and anyone who's serious about printing larger parts should definitely be talking with them.
That seems like an awesome solution...Do you mind me asking ball park what a print like those costs?
This is one of my favorite builds, I just love all of the work that goes into a one off creation like this.
NOHOME
UltimaDork
2/10/19 6:20 a.m.
Indy-Guy said:
In reply to 275nart :
I didn't see that one coming. You're full of suprises. In a good way 
I knew that it was coming, and even then I am blown away by the whole thing.. I have two Formalbs SLA printers that run pretty much full time at work so the 3D printing is no longer magic, but the scale of this blows me away!
Pete
275nart
New Reader
2/10/19 8:48 a.m.
Thanks y'all.
MKE- Wow that looks pretty slick. I agree that the windshield has to be right- one of the reasons I went with the p1800 is that the side glass, vent windows, and windshield are pretty close to the 275gtb. IF the windshield isn't looking right I will go with a ferrari windshield.
NOHOME
UltimaDork
2/10/19 11:28 a.m.
So what is the game plan for transferring the 3D shape to aluminum sheet? I am more familiar with the traditional "Station" body buck and am trying to decide if there is any significant difference when you work off a solid shape? Clamping partially formed parts to check for fit is one that comes to mind.
Pete
759NRNG
SuperDork
2/10/19 8:57 p.m.
I'm in awe......what beautiful work.....I'd hang those pieces on a wall in the house .....with a tiny brassish looking plaque pontificating nonsense.....and no one would know the difference....
not to mention that 'Bobzilla' in this same forum has a V6 Tiburon (thread) with an uncanny similar profile.....just sayin'
275nart
New Reader
2/11/19 9:33 a.m.
Pete,
I don't know that there is any huge advantage other than giving more visual reference. Obviously you can't use it as a form to hammer over!
NOHOME said:
So what is the game plan for transferring the 3D shape to aluminum sheet? I am more familiar with the traditional "Station" body buck and am trying to decide if there is any significant difference when you work off a solid shape? Clamping partially formed parts to check for fit is one that comes to mind.
Pete
Those pieces look amazing. I've been itching for an update on this thing
I'm only on page one, but this is freaking incredible. Your welding is dang impressive.
jdogg
New Reader
10/22/19 9:49 p.m.
I've said forever the Jag V12s were way better than most of the cars they were made for. Nice project. I hope you are doing Weber downdrafts that's gonna sound nice
Yooo.. I just found this thread. Buckle up! Hope nobody needs anything at work tomorrow. I'm assuming Frenchy is all up in here.
Everytime I post here, I feel like a caveman drawing with blood and feces (probably both mine), giving finger-painting tips to Michelangelo. That said...
If you want to go full analog on handforming aluminum body panels, grab a beer and watch everything on the RÜNGE CARS YouTube channel.
And embrace occasionally tig welding without using any filler. I'm just learning, so that was a thing.
Sweet CB750K btw, I used to commute on my '74 into NYC in the early 80's, 811 Weiscos, Kerker 4-1, Barnett clutch, Accel coils & wires, Dyna S ignition, control wires through the inside of the GP bars, tapered roller bearings in the steering stem, progressive springs and revalved the forks. A long, long, looooong time ago. Can't remember what I had for lunch today, but I can recall - with advantages - 2 gear block long wheelies and stoplight smokey burnouts from ...35 years ago... like it was yesterday.
love the build.
In reply to mke :
I too would like to know ballpark costs. This and a freelance designer could give me the styling I want for my own build...fiberglass is something I can handle, if I've got a shape to mold from.