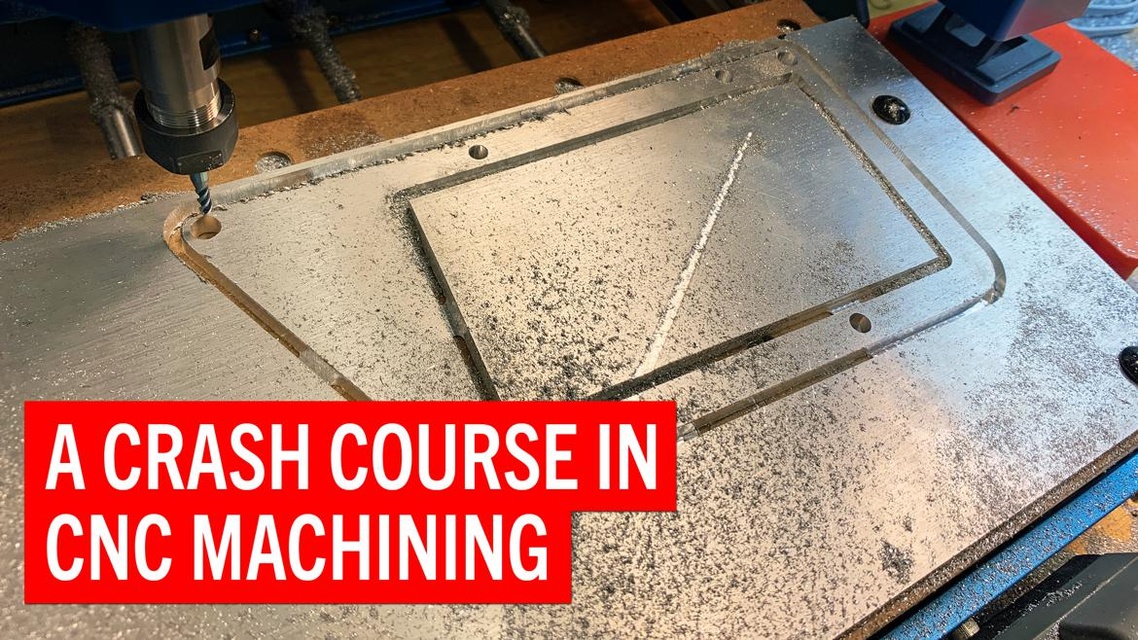
Our series on helping every fabricator build better parts started with the basics: How to draw those parts, design them with a computer, and instruct a sub-$200 3D printer to bring them to life from plastic. Now it’s time to start cutting metal.
Our series on helping every fabricator build better parts started with the basics: How to draw those parts, design them with a computer, and instruct a sub-$200 3D printer to bring them to life from plastic. Now it’s time to start cutting metal.
Hehe, did I hear someone say CNC crash?
Jokes aside, this is a great article series. I've been drooling at small CNC mills for a couple years.
Some forum members have had good luck with mail order custom machined parts, any chance of an article on those options?
The Mercury Capri of routers hahahaha this had me rolling! Great article.
<<We couldn’t find a clear set of rules that categorizes machines as one or the other.>>
I'm reasonably sure that a mill has a stationary cutting head, while the part is mounted to a moving platform,
and a router has a moving cutter head and a stationary platform.
In reply to BimmerMaven :
Depending on the machine the platform or head or both is moving on a CNC mill. The platform might be responsible for certain axis and the head others. Just depends.
I covered that in the first part of the series: https://grassrootsmotorsports.com/articles/technical-drawing-universal-language-making-stuff/
In reply to BimmerMaven :
I don't know if there is a hard and fast rule but I have run both routers and mills, of every imaginable size.
The spindle moves in three of four axis on this monster, but it is definitely a mill.
In a previous job I ran a bellotti 5-axis router. That was cutting composites. fiberglass, graphite and kevlar. If you've ever been on a plane, I probably made part of it.
The main difference as I understood it was the spindle itself. A mill is a torquey machine with soindle speeds up to 5000 rpm. My routers would spin in the neighborhood of 35,000 rpm.
You'll need to log in to post.