I guess every body is an expert but me. But I wonder how many of you that think you know how to determine spring rate, or claim that springs aren't heat treated actually know anything about springs.
If a coil of a coil spring is at all compressed between when the spring is in a free state and when it is installed, it is stressed in the installed state and is absolutely an active coil and must be included in the calculation of spring rate. Period. I'm not going to say another thing about it. If you disagree, provide facts.
And coil springs are in fact heat treated. There are many kinds of springs, alloy steel and heat treating. Heat treating does not make something brittle, unless that is the intent. The correct alloy and hardness is what makes a spring a spring. How do you think it works otherwise?
pstrbrc wrote:
bravenrace wrote:
Coil springs are heat treated. The vast majority of the time, when they are torched they lose their hardness. This happens whenever the springs are not normalized afterwards. This allows them to fatigue over time and fail. Bad idea for a long term street car.
Wow. For a guy telling everybody else they're wrong...
No. Springs are definitely NOT heat-treated. That would make them brittle. In fact, all calculations for springs/bars/etc is based on a general constant for the elasticity of steel. Plain ol' steel.
Therefore, if cutting a spring with a torch, all you have to do is let it cool all by itself, with no pressure on it, and it will maintain its spring rate.
Be happy to refer you to a couple of material books, since you think that's so handy...
Wow, for a guy telling engineer with a background in spring design that he's wrong, you have no idea what you are talking about. And I mean that in the nicest, most welcoming, and non-argumentative way. (Where's that sarcasm emoticon???).
Some people in this thread are smart enough to know a bottomed out coil is no longer active.
foxtrapper wrote:
Some people in this thread are smart enough to know a bottomed out coil is no longer active.
From my experience, when cutting a coil that the cut end of the coil isn't bottomed out when it's sitting in the perch (i.e. jsut the tip of it is actully touching the perch), therefore the full lenght of it is active.
But I've only done this on a few dozen cars including autocrossers, so what do I know, right?
How about this one.
Compress the spring (method otional) put it in an oven and bake ( heat) at 400 degrees F for one hour.
A friend asked me about this, after laughing, I told him to try it .
Don't know if he ever did.
One other thought.
when heating an installed spring, it is virtually impossible to heat it evenly, thereby creating stress points.
In reply to foxtrapper:
First, like you implied, I'm not smart enough to be discussing this, but I'll take another wack at it anyway.
When calculating the spring rate, you start from a free state, not installed. That means that any coil that helps support the load is included in determining the overall rate. This is independent of whether or not a coil is bottomed when installed.
The spring rate is effected by a lot of things, and one of them is the number of active coils. If an open end spring has 5 active coils and one dead coil, and you remove the dead coil, you now have 4 active coils and one dead, thus changing the spring rate. But in reality, you don't have dead coils in an open end spring, because all the coils share the load equally.
Getting back to the original question, you can cut a spring safely as long as you don't add excessive heat. You shouldn't cut a closed end because the spring will no longer seat properly. Heating isn't a good idea, but even if it works, cutting without heat will always be a better option, so do it that way.
My students and I lowered this Sentra without any heat at all. We removed 100% of the coils.
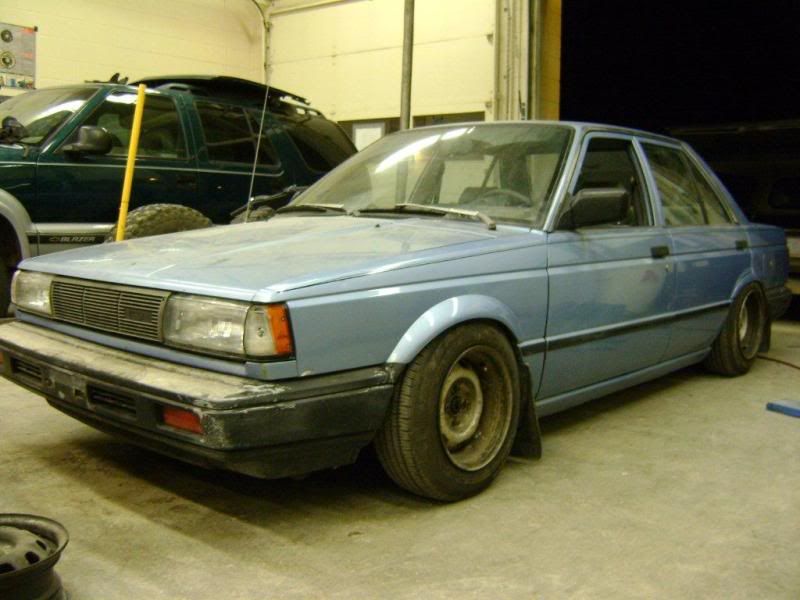
It rides like a backhoe.
In reply to bravenrace:
If helps, I agree with you and so does my Machine Design book.
http://www.motoiq.com/magazine_articles/Id/1439/pageid/1888/frankenmiata--handling-with-a-hacksaw.aspx
I copied Dave in the spring dept, but with bilstien's.
JThw8 wrote:
you will risk it dislodging from the spring perch on full droop.
Common problem with Toyota rwd front struts. Simple solution is to remove the small dust shield @ the top of the strut located between the upper spring seat, and the strut mount assembly, and replace it with a 4' long (or as needed) x 2" tiedown strap. Actually you use a heating iron and cut a 5/8" hole in the center of the strap, and then drape the strap down around the lower perch, and using 2 SS hose clamps capture both sides of the tiedown strap inside the hose clamps. Lean down a bit to add a bit of pre-load, and tighten the hose clamps

A good example of why the equation is for number of active coils, not simply number of coils.
The 1/2 coil at the top is out of the equation because it cannot be deflected. Same for the 3/4 coil at the bottom. Those segments will contribute nothing when it comes to deflection.
Under compression the next 1/2 active coil at the top and bottom will quickly bottom out against the dead coils. At that point they will make no further contribution to deflection resistance. The spring becomes stiffer because the number of active coils has been reduced, and the spring formula changes as a result.