I'm building a custom clutch cable for my cbr-powered datsun roadster challenge build. It needs to be longer than the stock cbr cable, so I have taken two cable sheaths, cut them and spliced them together to make a sheath the right length. I have run cable through and the transmission end is a fitting I was able to crimp on and I feel confident about it. The clutch lever end I'm struggling with.
I'm trying to use one of these, but in general I don't trust these and I can't seem to get mine to bite hard enough.
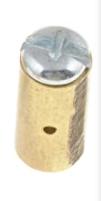
I even tried to add solder this morning, still didn't hold hard enough. Do they make this style in something I can crimp or swage onto the end of the cable? I'd rather not be worried about the reliability of my clutch cable!
When it comes to cable knarps I usually make my own. I do prefer a style with a hex on the body so it can be tightened without loosening

You can also use the phrase "wire rope ends" in your search to find the crimp on ball and stud variety
If it is a stainless cable you will need to use a liquid acid flux like Harris Stay Clean to get the solder to stick.
I posted this in another thread about cable ends - doesn't answer your question about the style that you need, but it does have a walkthrough of soldering ends. The link should drop you right after his post, just scroll up a bit.
I've never done it but this guy has a nice walkthrough on making custom length cables right here.
Mid Century Moto Mecca
That whole thread is pretty incredible. He posts some really nice stuff on Instagram too.
Find a local theater, hydraulic fab shop, or other industrial type place and ask to use their swaging tool.
It takes a ferrule much like the one you show and presses it on aircraft cable. The ferrules are typically something ductile like copper or aluminum, so you'll want to back it with a steel washer, otherwise the repeated use will just chew the soft metal. A properly crimped "neko" or ferrule will be stronger than the cable it's crimped to. The type of ferrule you're looking for is usually called a "wire rope stop." Once it is properly pressed on, it forces the ductile metal into the strands of the cable. One of the demonstrations I give at the theater is to install a copper stop on a cable, then use the band saw to cut it in half. You'll see that there are no voids. In between each strand of the steel rope is solid copper. Very strong.
If I weren't fuloughed from the theater, I'd tell you to send it to me and I would do it. It costs me about 4 cents.
The tool looks like this:
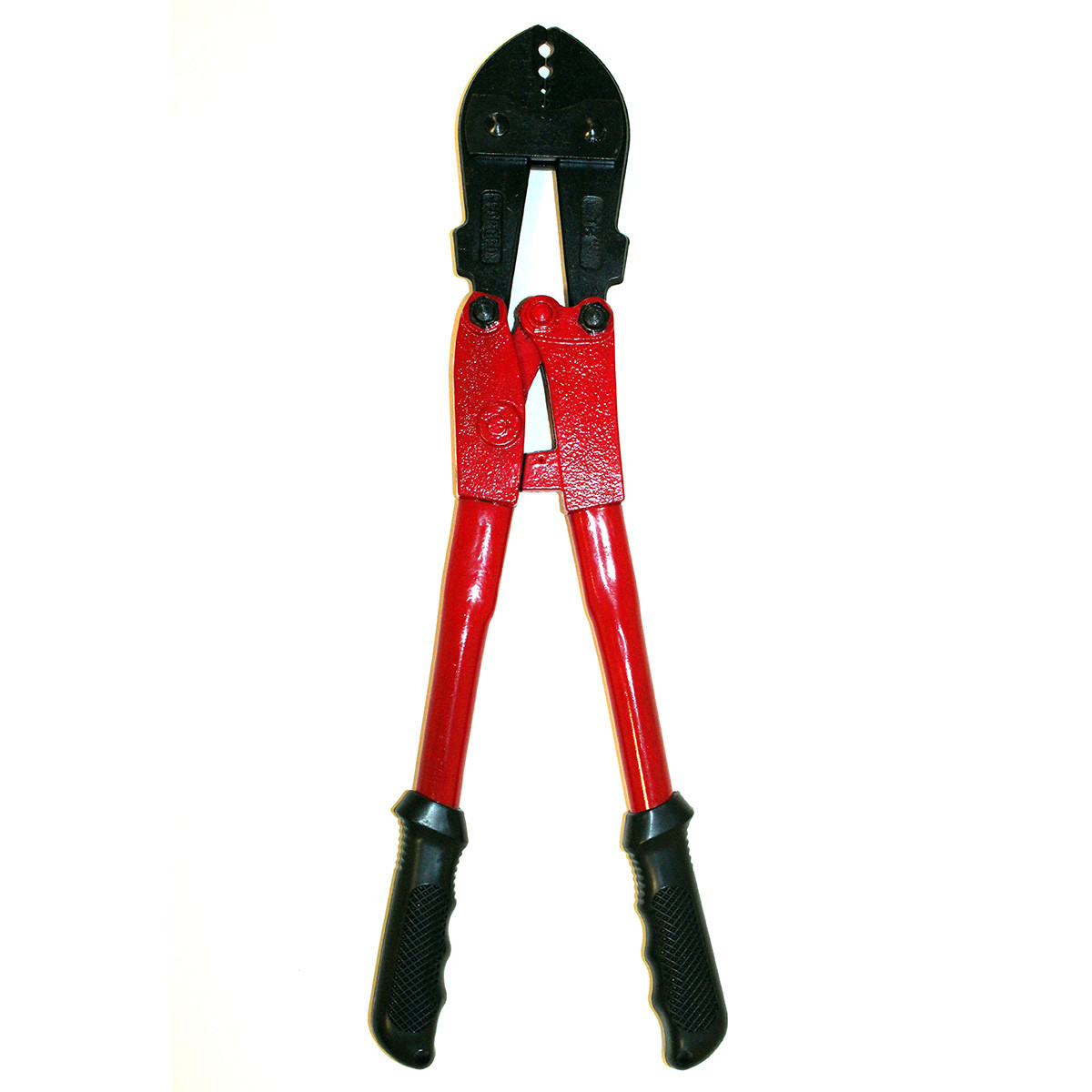
and the stop looks like this:
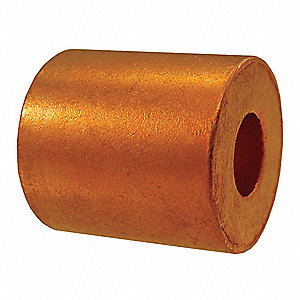
Oh, also.... the type of stop you use will be dependent on the type of rope you're using. Finer strands (greater number of strands) need softer materials and vice versa. Also, stainless vs galvanized vs steel also need different materials for [insert] reasons. The ferrules are sold in black oxide copper, aluminum, tin-coated copper, and a few other flavors. I can't say if the reason is bi-metal corrosion (which would be important for you) or for maintaining the strength of the tensile rating of the cable for overhead lifting safety (not as important in a clutch situation), but it's worth looking into.
In reply to Mr_Asa :
I've never used that style, so I can't really comment. The only ones I have used were like the ones I pictured above. This one is $44 on walmart.com
The key to using a swaging tool is to get at least 80% of the ferrule compressed. With smaller ones that might mean two crimps, but bigger (like 3/16" or 1/4") might mean 4 or 5. Always start in the center and work your way out (or one end to the other) so the trapped air has somewhere to go.
This has been on YouTube for several years, dunno if it would work on a automotive clutch but you get the idea.
https://www.youtube.com/watch?v=Ysd8JkWclmc
Steel pipe of the proper OD (1/4"?). Drill a small hole , put cable through, muss up the end. Solder with a MAPP torch.
It was good enough for Binky. Only, I believe yours will be perpindicular to the cable.
I actually have a swaging tool, and I was able to use it for one end. That end I'm not worried about. But my wire needs to be perpendicular to the 'barrel' on the other end, and I have no idea how to swage that style end.
For soldering, I didn't use flux, so that might be my issue there. need to get some flux, unless flux for soldering copper water pipes is the same stuff.
In reply to cmcgregor (Forum Supporter) :
Here is the real good info from that link - they sell a $40 assortment I might just buy!
http://www.flanderscables.com/
In reply to Robbie (Forum Supporter) :

For that small of a part you should be able to braze it using MAPP gas with a propane torch head. I had to make a cable end that had a cylinder style end as you need. Get a piece of steel tubing, like steel brake tubing and drill a hole completely through it and fit the cable through it. Then using the Mapp gas and some flux coated brazing rods heat the end red hot and the flow the bronze into the tube. I've also done this when adding a "ball end" to a cable. I just drill the ball for the cable to slide through and braze it.
I have probably a thousand miles on my custom throttle cable for my 190 Microsquirt project and no issues so far. It took a bit of learning to finally figure out how to do it. Since I had to essentially meld a '03 Mercury Sable throttle cable (TB end) with a 190 cable, I judged the Mercury end to be more fiddly and bought a replacement cable for it. I then promptly cut off the pedal end and cut the length down to what I needed.
The tricky part is of course the soldering. After much thrashing about, what I came up with was roughly the following (going by memory) -
- Get a chunk of aluminium, and drill a hole all the way through in the diameter you want the cable end to be. You may need to drill a 2nd hole at 90* from that to put the cable in, depending on the cable end arrangement.
- Tap roughly half of the hole, and put a bolt in there so you now have a closed little "pot" for the solder to melt in.
- Snip off some bits of solder and stand them up in the hole. Keep a little more at the ready.
- Fray the last little bit of the cable - basically anything that you want to be encased in the solder - and dip just that part in flux.
- Fire up your torch and aim it at the underside of the aluminium and/or the head of the bolt. Keep it focused there until the solder starts to melt in the hole (think the end of Terminator). Once you have a full pool of solder, stick the frayed, fluxed cable end in the hole and remove the torch. Keep the cable in place until the solder starts to cool.
- After it's fully cooled, remove the bolt, and use a punch to get the cable end out of the block of Al. You can trim any rough edges with sandpaper.
Here's what I ended up with:
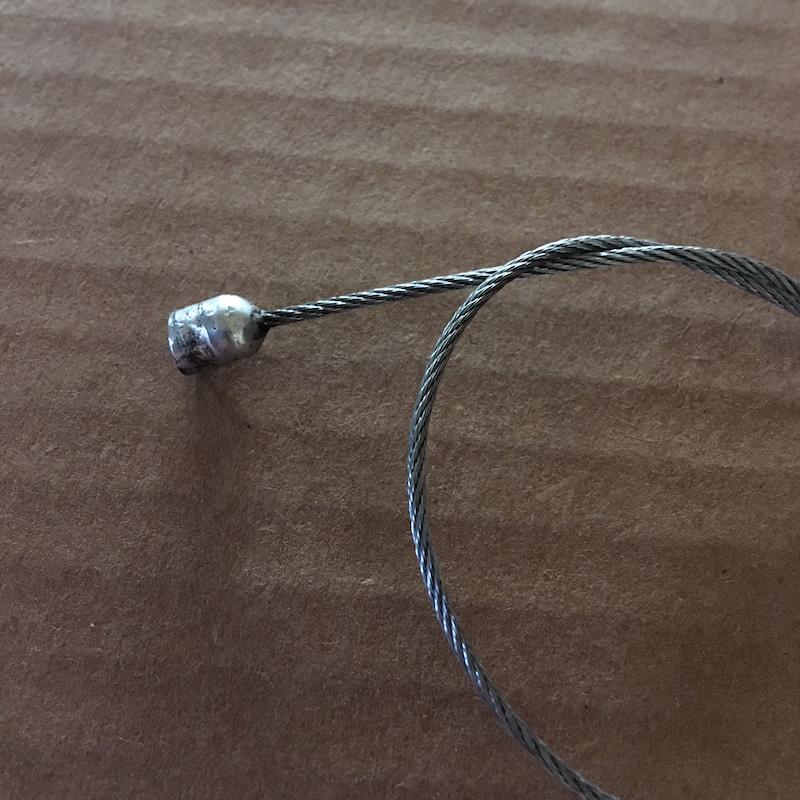
I'm not against making a nice cable end, but... I've done this twice, and you know what i did? Took a nut, and crushed it onto the cable. The first one i did out of semi-desperation because i needed my clutch cable to be able to drive my car and it's been NLA forever. Anyway, the first one i did, i literally stuck a bottle jack sideways inside a steel wheel (not one i needed, obviously) thus turning it into a form of curved-jaw vise
and smashed the nut onto the cable. The next one i did in my shop press. 
That first one though, is still on my turbo caravan that has a dual diaphragm clutch pressure plate and has never failed (~12 yrs so far). If you don't know what that means, it means take the resistance of the clutch to the cable, DOUBLE it, and then still not fail. I'd do it again if i needed to!
What if you found a suitable "barrel," drilled it for the cable, then put one of my swaged stops on the end. Cable stop pulls on the barrel.
For that gimmick, I might try a search for a cross-dowel nut. Stick the cable through, put a stop on the end. If you want to get saucy, fill the hole with solder.
