I have been turning my own solid aluminum bushings, mounts, etc for a while now successfully but tonight I'm bleeding from some new holes in my flesh and it makes me wonder what the berkeley I'm doing wrong.
when I'm doing the rough cuts at larger than 15 thousandths I get swarf streamers wrapping around everything and they don't break. they grow until I have to stop the lathe and take a freaking wire cutter to unberkeley everything.
speed is set right. tool is sharp. what am I doing wrong?
6061 sometimes gets gummy like that. I get that all the time on the manual lathe.
The_Jed
SuperDork
11/29/13 11:00 p.m.
What kind of aluminum and what is the feed rate?
Is it an inserted tool, ground carbide, ground HSS, etc.?
Can you take a bigger cut?
Knurled
PowerDork
11/29/13 11:04 p.m.
Wear gloves when you're cleaning up?
In reply to The_Jed:
6061, HSS, speed and feed are straight out of the manual and I can take a deeper cut but it makes it worse.
it wraps the work, the drive threads, and it whips all around slicing me to ribbons when I'm trying to stop the feed in exactly the right spot. small cuts help, so do long sleeves but I'm opposed to both. :p
Slow down, to go faster.
Seriously.
Trying to take off too much metal and then having to dick around with clearing chips takes more time than taking more cuts at less stock removal does.
By profession, making round metal smaller is what I do. But, not with a lathe. I run a centerless grinder.
The_Jed
SuperDork
11/29/13 11:38 p.m.
Do you have another tool you could risk ruining by grinding a bit more positive rake into and creating your own chip breaker?
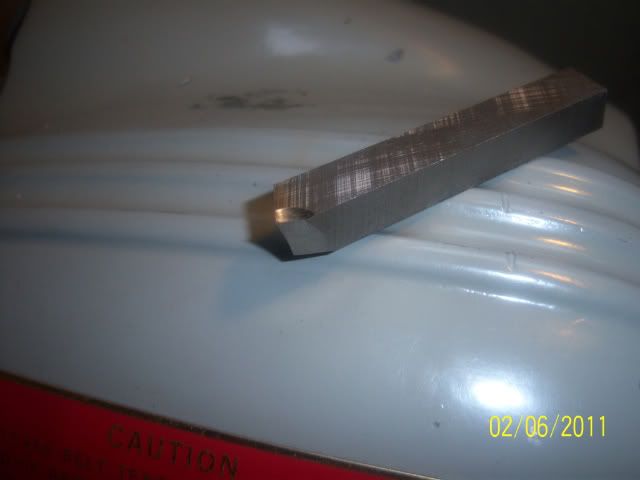
If all else fails you could get really nuts and mount the tool slightly SLIGHTLY below center to create more shear force and hopefully stack the chips forcefully enough that they break. 
Or it could just wipe out the edge of your tool and rub the part while making some bad noises. Keep your hootus well away from the danger zone.
The_Jed
SuperDork
11/29/13 11:45 p.m.
In reply to RealMiniDriver:
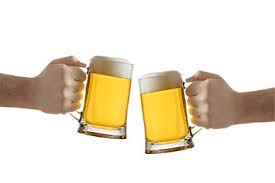
Me too, except I've never run a grinder. 
The_Jed wrote:
Do you have another tool you could risk ruining by grinding a bit more positive rake into and creating your own chip breaker?
Yup! Grind a chip breaker into it.
Unless you are using a carbide insert with the chip breaker shape already there
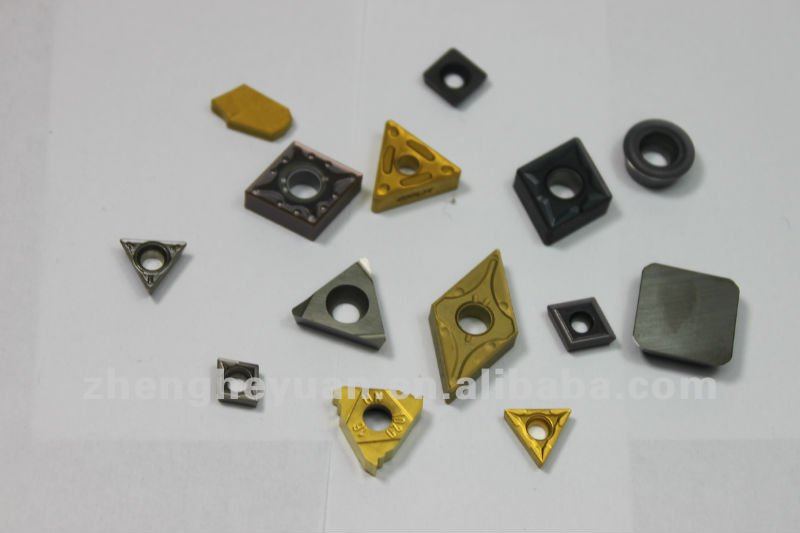
Then adjust your feed to whatever leaves "C" or "9" chips.
The_Jed
SuperDork
11/30/13 12:14 a.m.
Even further out of the box:
I assume you're leaving .005"-.010" of material for the finish pass. Could you put a small groove or two in the o.d. along the entire length of the part, equivalent to the depth of the rough cut?
Touch the o.d. with your turning tool between the jaws (with the spindle off, of course) turn the cross slide in an additional .005" or so and use the rapid traverse handle to broach a groove from the chuck to the tailstock. Repeat until you hit .015".
What reference? Machinery's Handbook, Machinist's Ready Reference?
Running any type of cooling? Even just a pointed compressed air flow will help alot with aluminum. The heat in the turning is being carried away with the chip - quick cooling it makes it britlle and break. Is your lathe plumed for coolant? If not check into a mister - less mess. Harbor Freight should have one.
Speeds and feeds in these references are not an absolute. When I got my AS in machine trades back in '99, we were taught it still was not an exact science. You need to play around. The 20-30 year + journeymen in the trade used to amaze me! They never looked up speeds and feeds, just went by feel and what the chip was telling them, and quality and cycle time were great. I learned more from them than I did in school. It is an artform mastered by time!
Also helpful is knowing if you're grinding your own tooling or not. If you're grinding your own, you can grind a chip breaker relief into the tool. If store bought, maybe try lowering the tool, maybe try raising it. Again not exact science.
Been out of the trade since '08 so I'm a little rusty, but my gut says higher speeds and feeds no matter what the book says 'til about .060 out, then drop feed rate for finish cuts.
Man, I must type slow. . . 5 posts as I was typing my post up!
Swarf if from a grinder, you're dealing with chips. (Stringers actually)
In reply to 914Driver:
I respectfully disagree. Swarf is any waste from a production process.
The belt system that removed chips from the high speed CNC machines I used to set up and run was called a "swarf conveyer".
Swarf
If your using the cross feed to make your cuts and not cranking the saddle manually then just
de-clutch the feed every few seconds and the interruption of the feed rate will cause the ribbon of aluminum to break. The more often you do this the shorter your ribbons. On roughing cuts this should not be an issue as you will see lines on the turned piece from the interrupted feed. On your finishing cut you just take a light cut and a slow feed and you should get a good finis.
Bear in mind that, depending on your machine, material and tool, there may be some disparity between the cut you dial in, and what it actually taken off. Most typically this happens on very light cuts - my Turn-Pro 13x40 is a fairly solid machine and it's well adjusted, still, using the high speed steel inserts I really like (Arrhur Warner Co. - they're great!) an .050" roughing cut and a .005" light cut come off within .001" or so, but trying to take .002" may take anywhere between .001" and .004".
So I try to rough down to .010" off final size, dial down, lock the cross slide and start the cut.
In reply to phaze1todd:
Technically, yes, swarf is any waste from the process. However, I agree with 914, that swarf is from grinding and chips are from turning. 
noddaz
Dork
11/30/13 11:23 a.m.
How about a shield to deflect the junk out of the way?
Alrighty... so thanks everyone. I had been making my own tool from blanks on the grinder. I had one new-in-box one that takes "blades" like ditchdigger posted above I had never used. I popped it in a few minutes ago and viola... no concertina wire flying off the part.
So, now I have to learn the magiks of making my tool with a chip breaker cut into it.
phaze1todd wrote:
What reference? Machinery's Handbook, Machinist's Ready Reference?
Machinery's Handbook
Running any type of cooling? Even just a pointed compressed air flow will help alot with aluminum. The heat in the turning is being carried away with the chip - quick cooling it makes it britlle and break. Is your lathe plumed for coolant? If not check into a mister - less mess. Harbor Freight should have one.
Just a paint brush with cutting oil.
Speeds and feeds in these references are not an absolute. When I got my AS in machine trades back in '99, we were taught it still was not an exact science. You need to play around. The 20-30 year + journeymen in the trade used to amaze me! They never looked up speeds and feeds, just went by feel and what the chip was telling them, and quality and cycle time were great. I learned more from them than I did in school. It is an artform mastered by time!
My lathe is not infinitely variable either so I typically pick the closest match to the book erring on the next slowest side.
Also helpful is knowing if you're grinding your own tooling or not. If you're grinding your own, you can grind a chip breaker relief into the tool. If store bought, maybe try lowering the tool, maybe try raising it. Again not exact science.
Yes. 1/2" HSS cut on my bench grinder. This last bit appears to be the huckleberry... the store bought tool I popped in to test today makes chips. So, I just need to learn to make a proper tool. If you couldn't tell, I'm kindof new at this ;)
Even still - with all of my lack of talent I am suprised at how well some of my parts turn out. Simple things, granted, but satisfying none-the-less.
The_Jed wrote:
Even further out of the box:
I assume you're leaving .005"-.010" of material for the finish pass. Could you put a small groove or two in the o.d. along the entire length of the part, equivalent to the depth of the rough cut?
Touch the o.d. with your turning tool between the jaws (with the spindle off, of course) turn the cross slide in an additional .005" or so and use the rapid traverse handle to broach a groove from the chuck to the tailstock. Repeat until you hit .015".
Assuming the lathe in question is beefy enough, I like this plan.
44Dwarf
SuperDork
11/30/13 3:18 p.m.
Buy a chip hook too this way you manualy break the chip should it form.
http://www.mscdirect.com/product/91852616