My stock DSM downpipe is garbage. Leaking bad at the flex. eBay has these cheap units but they delete the car. Not good for those of under totalitarian rule (safety/emissions inspections).
As seen in the pic, the straight part near the terminus is where the stock cat sits on the stock unit. My plan is to chop out the straight part where the cat sits and reweld the flange to bolt up to the cat.
Okay, real question here. How well does this weld up? All I have is a Harbor Freight flux core unit (times are tight you see) so not sure if it’s possible to weld.
Possible or no? 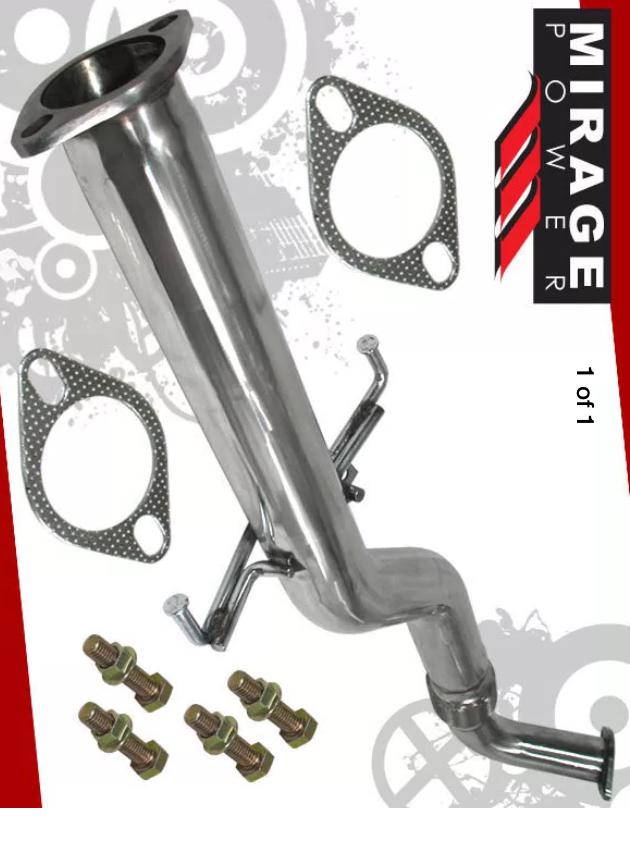
Is that stainless? If it is, then you can weld carbon steel to it, but you really need to use stainless wire and argon or argon mixed gas to shield it. You might be able to weld it with your HF flux wire. Go find a piece of 304 stainless somewhere and hit it with your welder and see what happens. Actually, find a piece of 304 and a piece of carbon steel and see if you can make them stick together.
wae
Dork
3/25/18 8:03 p.m.
I have used stainless steel flux core wire before to weld up some stainless tube construction boat stairs and it worked pretty well. I realize that isn't exactly the same thing, but it's the only data point I have to offer.
Stefan
MegaDork
3/25/18 8:44 p.m.
Modify your HF to provide DC voltage and you’ll have better results, lots of hits on how to do that via Google.
Use a good quality flux wire (the HF stuff is garbage) and determine if that is stainless, chromed steel, etc. to figure out which wire you want to use.
Worst case, you could use the large band clamps to clamp it all together and take it to a shop to have them weld it for a few bucks.
Would it be easier to get a generic flex bit and fix your stock downpipe?
There is stainless steel flux core gasless MIG wire. I used it once on exhaust tubing and it was tricky to figure out. It didn't run like copper/mild steel. I don't remember too many details but I think I was using pretty high power. If I was doing the job, I would have to buy two downpipes and sacrifice one into slices so I could butt-weld it a dozen times until I figured out the settings and technique.
I don't know anything about turbos. Is there a reason you can't just fab up one from scratch with aluminized steel and paint the welds? 2 Walker 45-degree mandrel bends would get you that s-curve for a total of about $12. Throw in a 90 degree mandrel bend, a flex joint, and a couple flanges.
You can weld SS304 to SS304 using mild-steel flux-core wire pretty easily. It will rust pretty quickly, but a lot of cheapy exhaust shops do exactly that.
For a better result, use the stainless flux-core that's been mentioned. It's a bit tricky because it does require more heat than mild steel (fine since you are welding thin stuff) and the wire is stiff and harder to feed thru the machine. But you must passivate your weld after. If you don't, you won't have much better corrosion resistance than if you had welded with mild steel.
I've welded mild steel 3/8" rod to 304 stainless attaching hangers for the exhaust I built on my RX7. This was using the el cheapo HF flux core welder and mild steel Lincoln flux core wire, because that's all that I had. Can't say yet how well it will hold up long term to corrosion (probably not well), but it seems pretty well attached at the moment.
I've used flux core mild steel wire to weld 409 stainless before as well as a 409 to 304 joint. Surprisingly, the welds don't seem to be experiencing rapid rust (only did this a couple months ago).
Yeah I'm guilty of welding aluminized mild steel tubing to 304 stainless mufflers with regular MIG wire and CO2 shielding. It's easy and it behaves pretty much like mild-mild welding. Hit it with some spray galvanizer and it doesn't seem to rust.
Should be fine on the welding - just remember that AWD and FWD cars use different downpipes.