Im not sure how to phdase the title...
What i need to do: cut out rusty and incorrectly shaped unibody structure and framerails, make new rails for new subframe and suspension, install in place of the previous stuff.
The body will need cutoff roughly equal with the control arm mounts to provide the correct height for the new subframe mount. This has the benifit of cutting out TONS of rust, and probably weight.
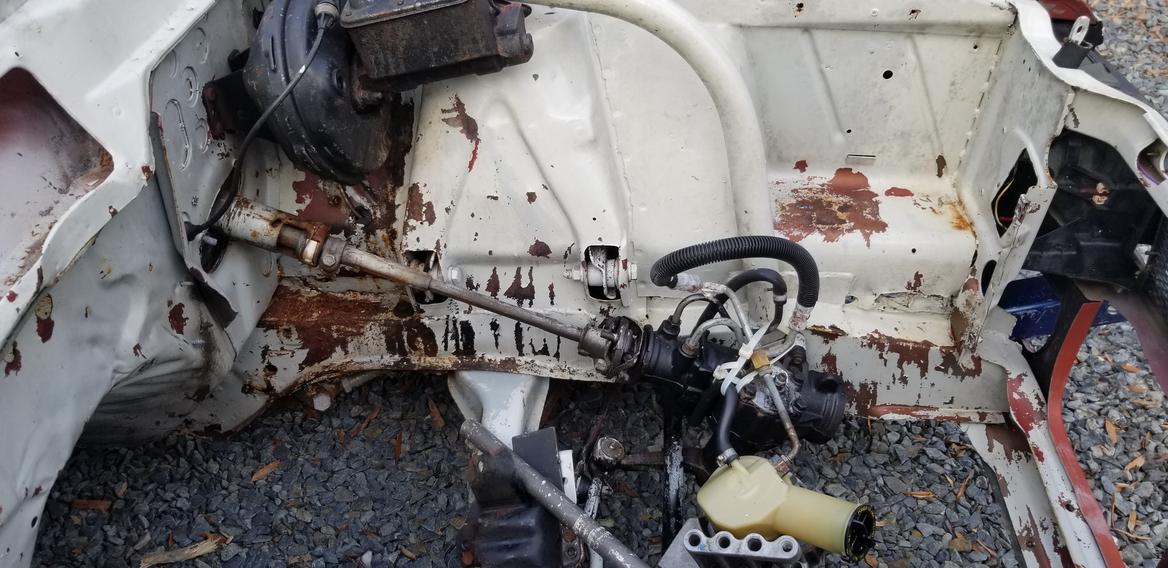
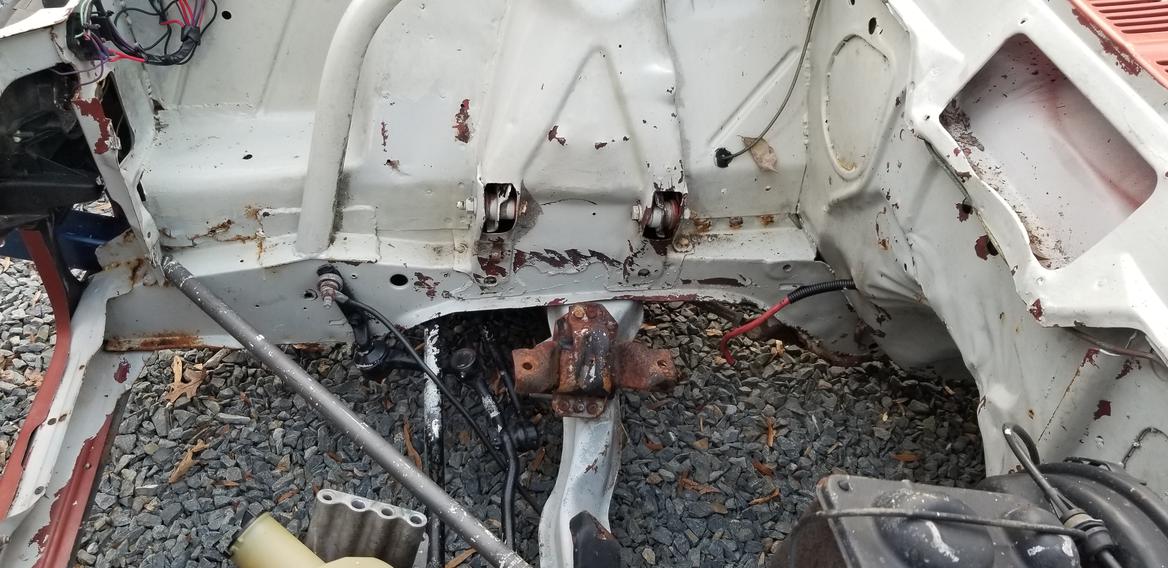
I will be placing this assembly in on the new rails, replacing everything in the front end.
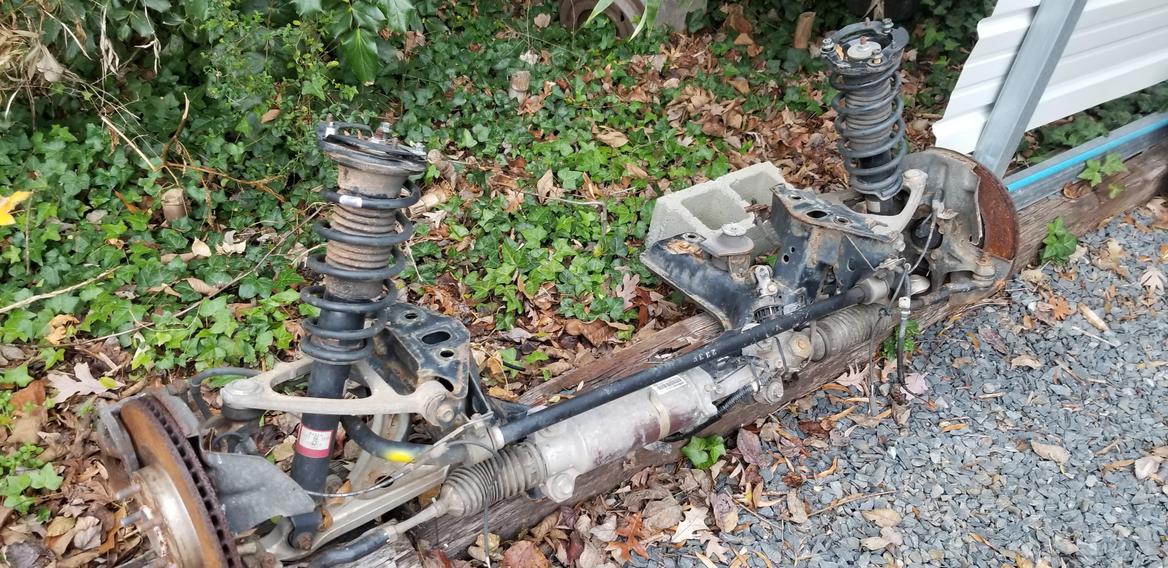
my thoughts are that i use 1/8 wall 2x3 tube to the core support, with a z in it behind the upper control arm, down to the bottom of the firewall and slid into the remaining factory rails. Make a new cage landing plate at the front, and then stitch the inner fender back together with fresh metal.
Ive never done, or helped with, or even thought about something like this. It makes me very nervous.
Staring at it has gotten me this far.
Can yall educate me prior to me picking up cutting tools please?
Step 1: Measure desired ride height of car before any cutting!
Step 2: Get some wheels/tires on it that have the correct overall diameter.
Step 3: Prop up the new subframe until the control arms are at the desired angles for normal ride height. Remove shocks. Use a furniture dolly with wood to shim the new subframe to the correct height. Now you can move your new subframe around easily.
Step 4: Cut old stuff out. But how much and where?
This stuff in red looks very structural right? I assume the new subframe mounts will be higher up than the old crossmember. This means you wil have to cut into the really structural part.
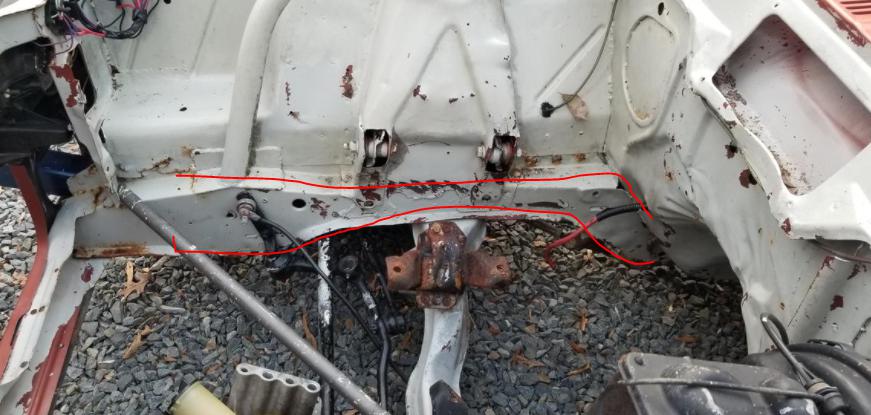
Your 2x3 frame rail idea is sound. I would try to leave as much original structure between firewall and new subframe, and between new subframe and core support. Basically use the 2x3 to bridge.
So I would only cut the stuff in red, then add the blue new tube, whose heigh is determined by your rolling front subframe thing.
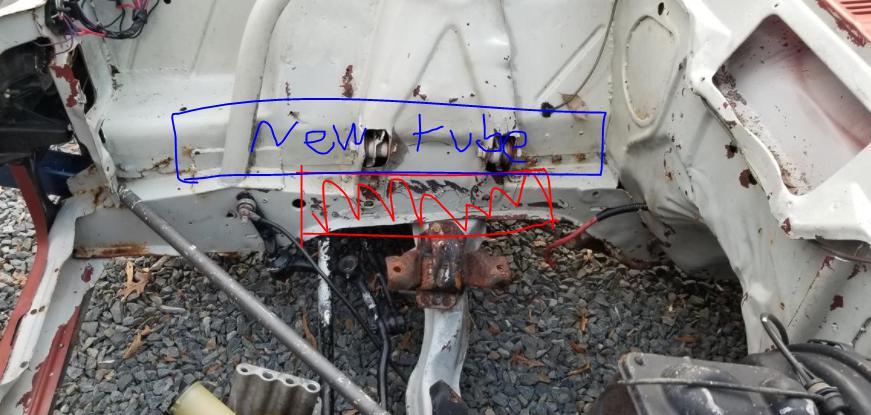
Step 5: roll the subframe under after lifting car up (pivot about the rear wheels - should be light enough to lift core support wiht engine hoist). If it doesn't fit, cut more out until it do.
Step 6: Determine new frame rail height, tack it in. Make sure subframe mounting holes work out.
Everything else works around that.
Step 7 is the rear mounting part of the subframe. I think that solution will make itself known once the front part near the UCA's is mounted. Probably another short piece of tubing jutting out 90 degrees from the bottom of the other tube you add.
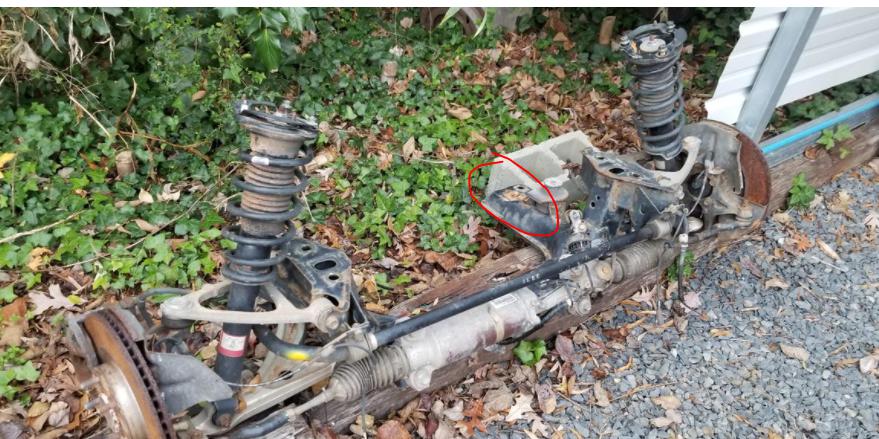
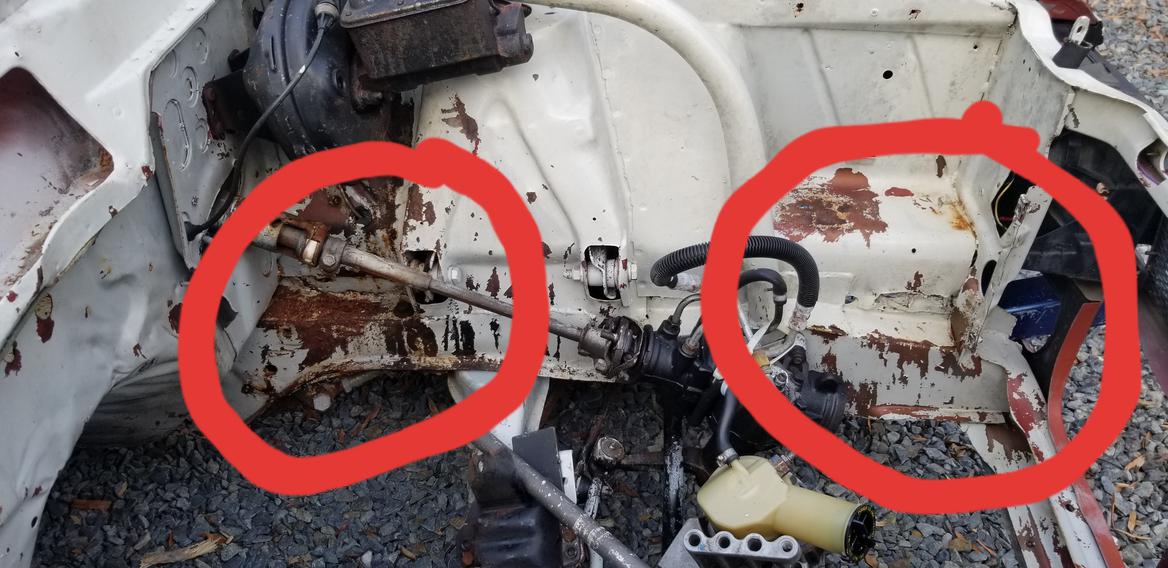
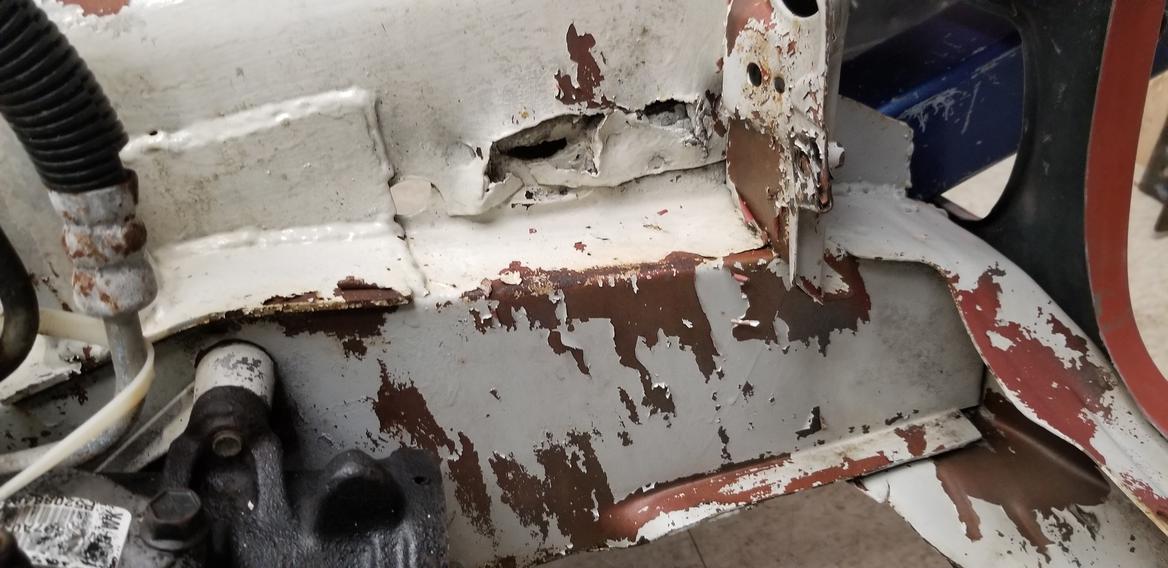
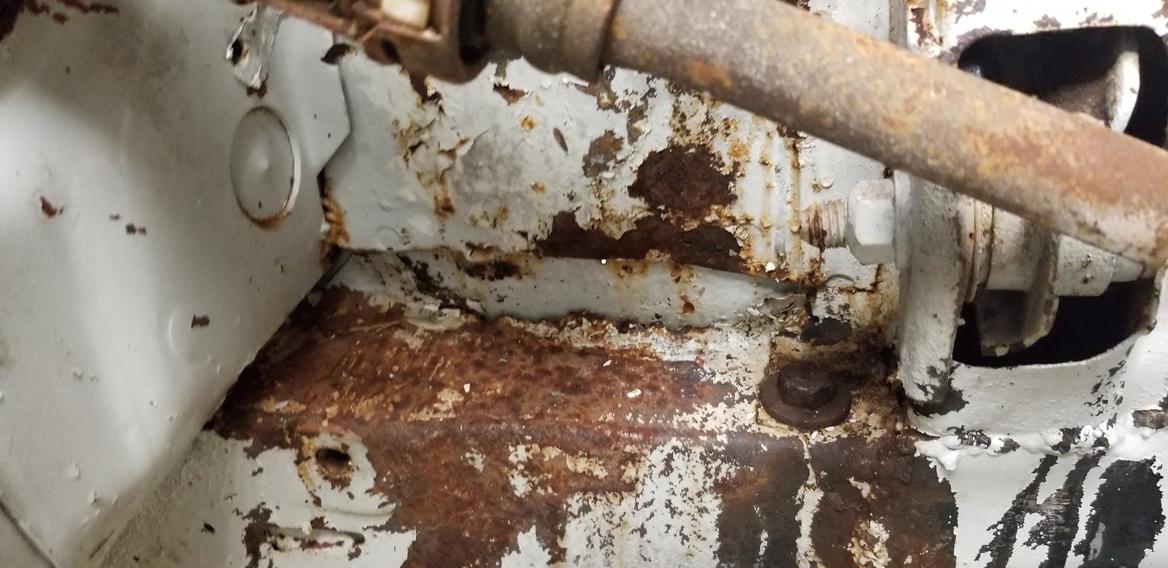
The circles are the close ups. Both sides have structural rot in these areas. Enough to scare me in retaining them.
The tape measure shows that the upper control arms (factory) are right about where the bottom of the new tubing will want to live.
But the method makes sense. Really does
Watch Project Binky's earlier episodes, where they made their own frame horns/strut towers from scratch, to get some general idea of one way to tie in to a flimsy unibody.
Where's all this rust you speak of? This northern fellow sees a pretty solid looking car with some surface rust.
nocones
UberDork
12/16/21 6:08 p.m.
Take a picture looking toward the firewall from the top and then one of the bottom of the car so we can MS paint CAD your design better. Also a pic of the new subframe would he nice also
Maschinenbau's plan is sound.
DeadSkunk (Warren) said:
Where's all this rust you speak of? This northern fellow sees a pretty solid looking car with some surface rust.
I've worked on enough old unibodies to be thinking the same thing!
DeadSkunk (Warren) said:
Where's all this rust you speak of? This northern fellow sees a pretty solid looking car with some surface rust.
It's a torsion bar Mopar. Where other manufacturers used a galvanizing dip, Ma Mopar used a saltwater bath.

In reply to Pete. (l33t FS) :
I swear, you're close. This is an amc that has been in the salt...
Nocones: when you say bottom and crossmember can you be more specific in what you want? Ill gran them.in the morning.
And re: rust
Theres quite a lot of swelling, pinholes, and missing layers of multiple layer panels. In addition to the holes and shoddy rust repair and accident repairs i did the first time I built this thing.
Id also hope this new setup can drop some weight, but im not optimistic. Just need to be strong, reliable, and simple. And, of course, adapt rx8 front suspension to the amc shell.
nocones
UberDork
12/16/21 7:44 p.m.
Take a side view of the subframe so we can get an idea of the mount points relative to the wheels.
Take a picture standing at the front bumper back towards the firewall. Then take the camera as low as you can in the engine bay to get a view of how those side rails tie into the floor and firewall structure.
First, and foremost: You cannot just cut at the firewall and butt weld a 2x3 to it. You either need to replicate what you have there, with rails, an apron and a top member, all welded to each other and to the firewall in a similar way, or go back to at least the middle of the car and add fabricated frame rails that weld to a crossmember at the rear, to the floor, to out riggers going to the sills, and a substantial gusset/bracket at the firewall.
For a frame section, If you look at a first or second gen Camaro, you can see the substantial box sections the front clip bolts to, and they need help to not flop around.
To reproduce a unibody like you have already, you need to reproduce what you already have, just in the right spot. Remember that triangles are your friend, and the farther apart your upper and lower mounting points are, the less substantial they need to be.
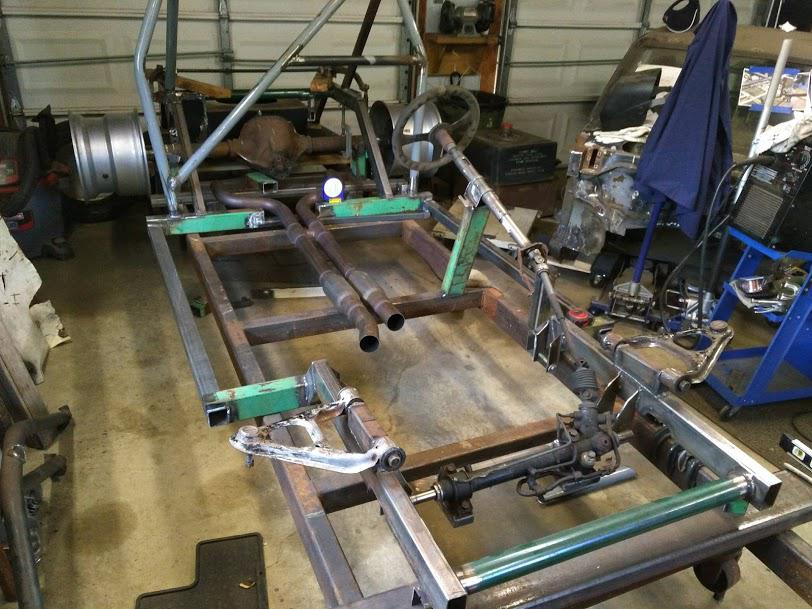
When I started the Corolla I built a front clip to do what you're trying to do. It has since morphed into a complete chassis, but ignore that for now. I used Miata suspension and I had a cross member for it. I chose to not use the cross member and instead mounted the upper and lower A-arms directly to the tubular frame rails. I did that because it gave me more room. The Miata (and RX-8) have a relatively high stock frame horn to sit on top of the cross member. Putting the frame rails down lower, between the upper and lower arms left me more room up top for the width of the engine and space for brake booster and steering column. That may or may not be necessary if the AMC and thr RX-8 suspension are significantly wider, just something to consider if space is tight. My frame rail spacing was dictated by the distance between the two upper A-arm pivot points.
You can figure out what altitude the rails will be at pretty easily. Set the Mazda suspension up with some wheels on it and the lower A-arms set parallel to the floor. That will allow you to measure the height of the mounting pads from the floor. Compare that to where the pieces are in the AMC and you'll have a good idea if the new, higher rails are going to be a problem or not.
Look at how the drag race guys front-half a car, thats your blueprint. While you will need something to tie the framerails into the upper firewall like your original inner fenders, it can be tube instead of sheetmetal if you are OK with no inner fenders.
Core support looking forward 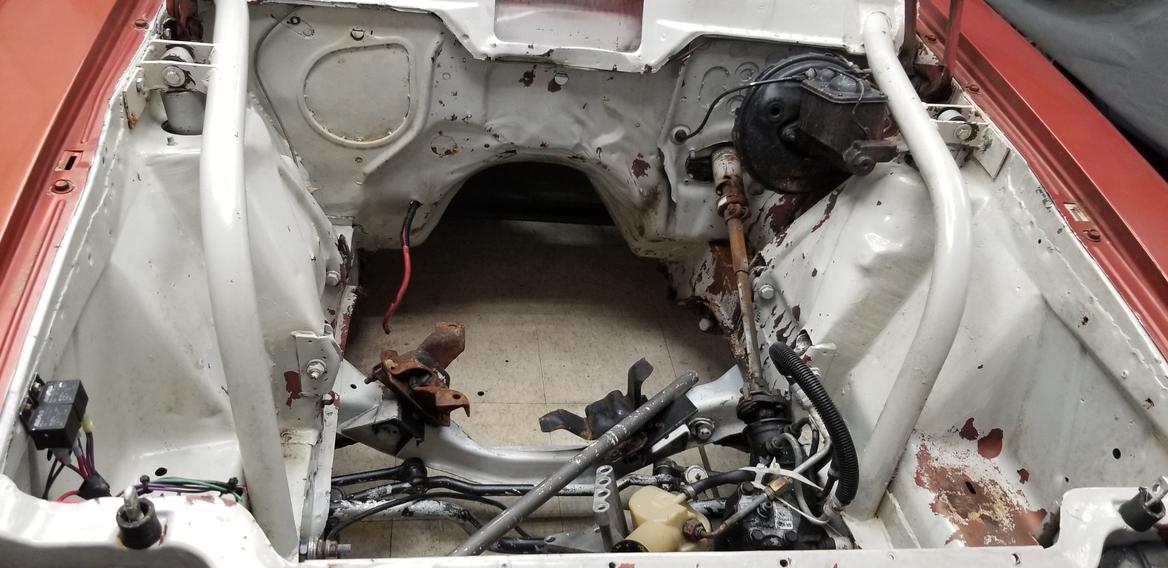
Wider angle of inside structure
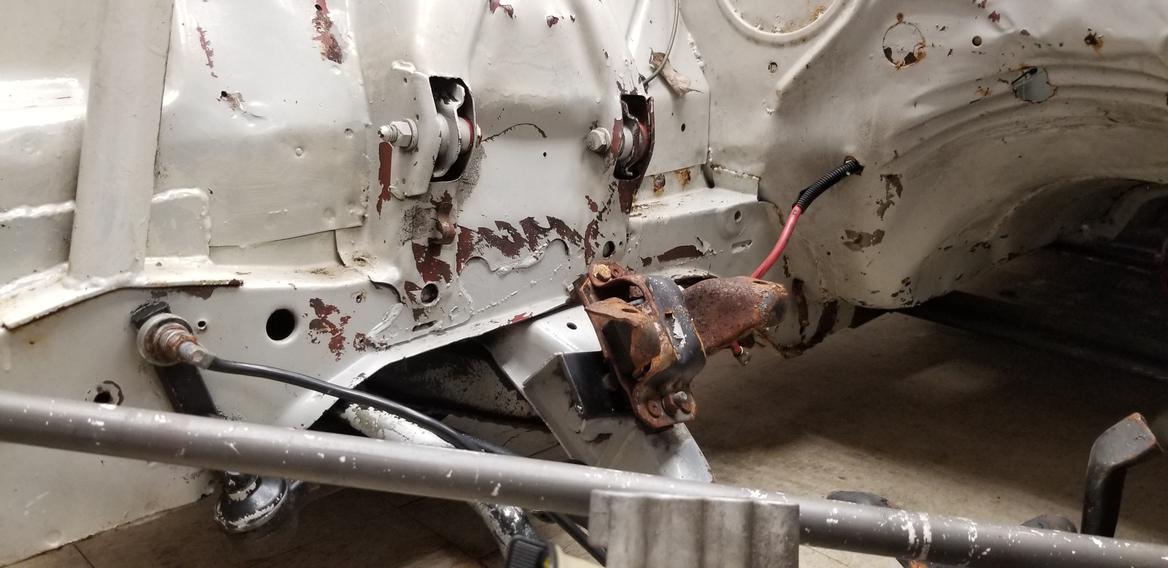
Wide angle of outside of structure at firewall and under front floorboard
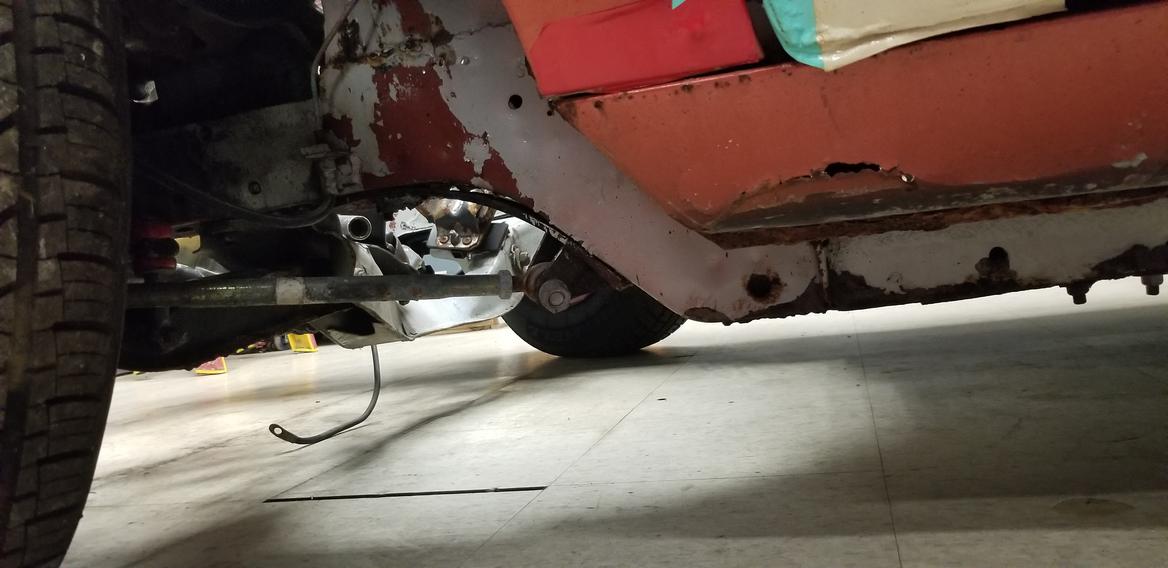
Crossmember pics
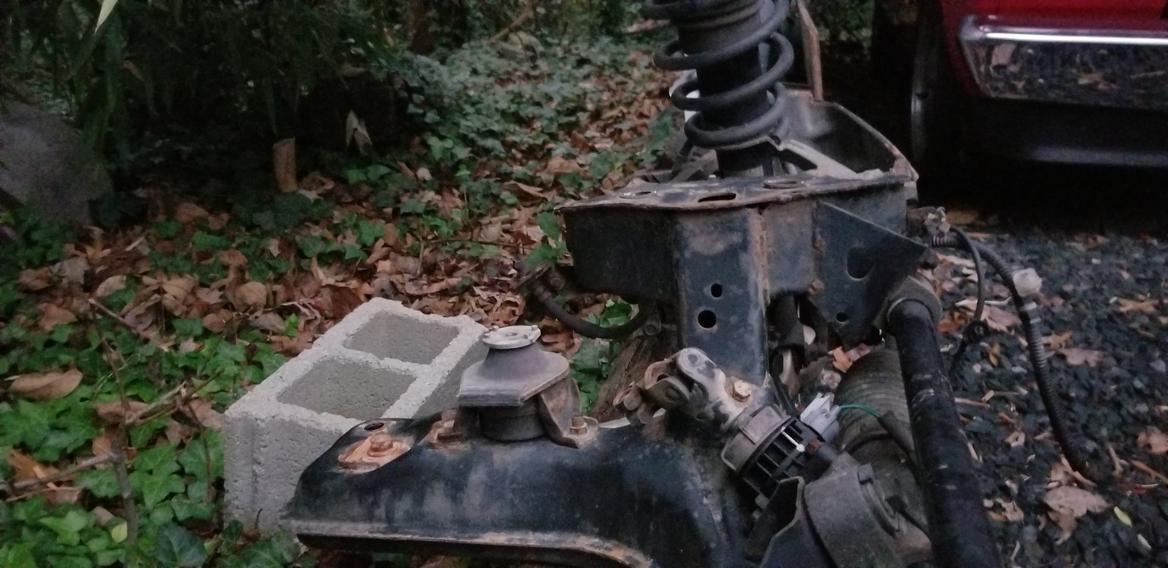
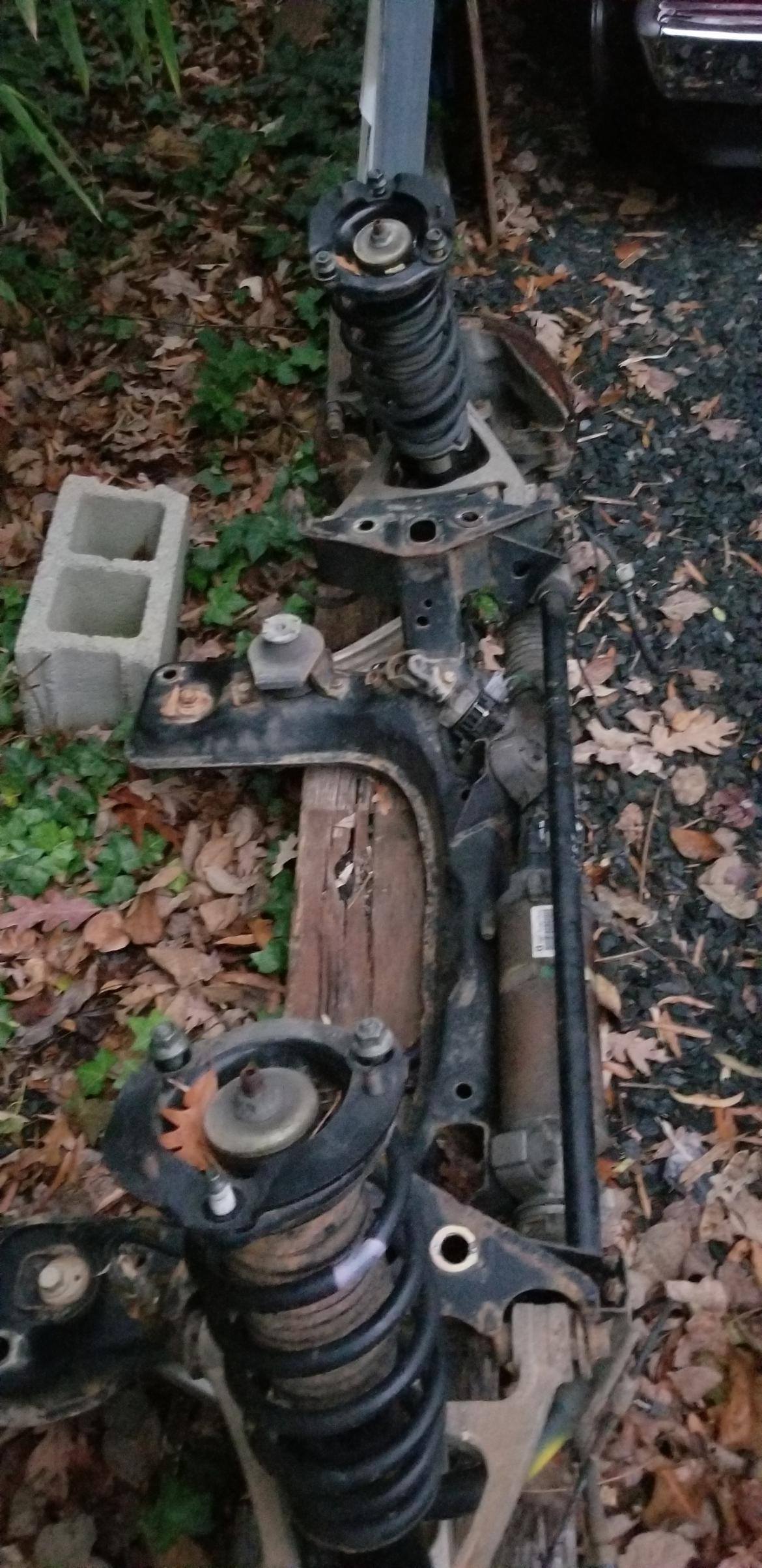
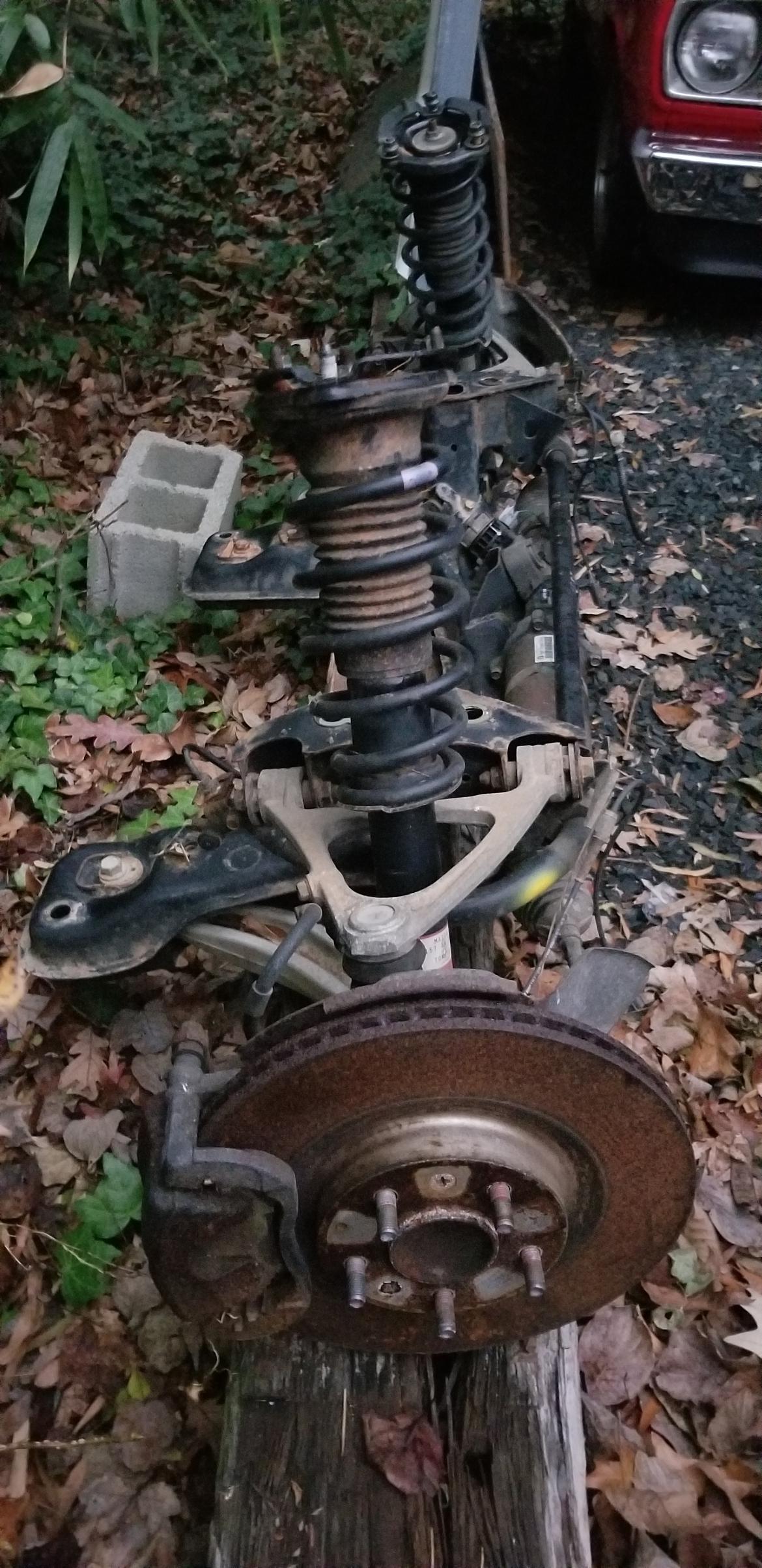
In reply to Dusterbd13-michael :
You need to look at the JaguarXKE. It's a front sub frame with a rear unibody that has actually been crash tested according to government standards and passed safely.
The trick is proper triangulation. They used thin walled (22guage) 1" square tubing brazed together. The flanges that bolted onto the firewall were made of 1/8th inch thick steel. With the tube brazed to the steel flange.
That held a 700 pound engine ! The whole front sub frame weighed only 22 pounds.
It would appear that the main chassis strength is in the upper rail, hidden by the fenders. The springs and shocks tie into that.
They did it this way to spread the loads out so they could use less steel, like Ford did with MacPherson struts in 1950.
This is the picture I saw that first got me going on a front clip. It's straight forward fabrication once you know what your dimensions need to be. Add two stubs at the back to pick up the under floor AMC frame rails and two plates at the outboard ends to mate up to the inner side of the A-pillars. Then bracing from the front end , over the top of the struts to the firewall area where Pete indicated .

In reply to DeadSkunk (Warren) :
You pretty much summed up what I was trying to say. Only differences:
Will the cage tube that runs to the frontvover the top count for triangulation? And i will weld the inner fender structure back to the length of the rail as well.
Id prefer to keep tbe subframe bolt in for accident repair. Because i know it will happen at some point.
You can run an extra tube or two from the upper tube down to the main frame rails. If you do the bolt-in cross member it won't be very far to bridge the gaps with sheet metal and it will be plenty strong. Hard to tell from photos alone, but I think your frame rails are going to end up somewhere above the stock upper A-arm pivots on the AMC.
In reply to DeadSkunk (Warren) :
Tape measure guess is about even with the uca pivot point for the bottom of the new rail.
Theres a contour in the inner fender about the same height
Are the AMC and Mazda upper pivots about the same width? Any variance there may influence the overall width of the engine bay and putting your new frame rails higher may cause you some heartburn on things like headers. Measure about 300 times before you weld anything and only tack it in place for a trial fit. That way you won't have to do this three times , like I did.
If I remember correctly, Mr Tanner did something like this in his MGB. He, kind of like Warren, replicated the (miata) geometry on fabricated frame rails, but what is maybe helpful is, he ran tube along the factory "frame rail" (unibody box section). I'd consider doing subframe connectors at the same time, tieing in front, rear, and all points in between. Maybe even cutting the floor so your tubes could be welded the whole way.
Fitzee's Fabrication video for some inspiration here.
Are you keeping leaves in the back? This is the time to build a complete frame, if you're going to do it. A torque arm solid axle has been proven to be a hot set up. It could also rid the car of all it's AMC inherent suspension height, once and for all (as I recall, this car had parts trying to scrape once lowered). I know it is snowballing, but it is worth going big from the start if you are going to do it eventually.
Pretty picture of torque arm rear suspension:

In reply to wheelsmithy (Joe-with-an-L) :
I had intended to keep the leaf springs. I found a place here locally that can deArch them for lowering purposes. The reason that we were having so much trouble before is the spring pack is a hybrid pack that is part SUV and part AMC. They have an absolutely ridiculous amount of arch and require a 5 inch lowering block to get proper rear ride height which forces everything into the asphalt as far as shock mount and lower spring plate goes. Having a platter pack will allow me to actually tune the rear suspension ride height. The leaf spring and slider combo is incredibly stable and sticks superbly for what the car is. It's also super simple to work with. I'm not sure that I've actually gained anything with change into a different rear suspension for my intended purposes of this car unless it was changing to an independent.