Hey guys,
This has been rolling around in my head since replacing the differential in my REPU a couple of months ago. It seems that with the exception of the venerable Ford 9" (maybe others)that the American, and Japanese manufacturers build their axles differently. I was wondering why, and if either have an advantage over the others?
The major differences I see are in the axle housing construction. The Japanese use what looks like think sheet metal to make thiers, and the Americans use cast iron or some other much heavier duty looking steel to make thiers. Also the Japanese have the whole differential come out as a unit from the housing where as the Americans have you access the differential via a cover. Any advantge to either? I see the cover as being convenient, but maybe not any easier to work on perhaps. It seems to me the American way looks a lot stronger, but then I think about the Ford 9" and it is constructed more like the Japanese.
I am sure there are advantages, and dis-advantages to both, and I'm probably missing the most logical reason(cost probably). I have never understood why they do it differently. Enlighten me GRM.
Chris
RossD
PowerDork
9/12/14 1:03 p.m.
Use an IRS from an RX-7. No need for solid axle ponderings! 
Axles with the differential housing built in and a cover on the back are called Salisbury type axles, while ones with a removable housing are called Hotchkiss type. There are a couple American Hotchkiss type axles besides the 9" Ford, such as the Mopar 8 3/4".
The more torque you're feeding it, the thicker the housing needs to be. Especially the part that supports the differential.
Putting the carrier in the housing vs a separate chunk is pretty much a matter of preference. You can do some checks on a Salisbury type axle without having to pull out the axles and driveshaft. On the other hand, a removable differential housing lets you take the whole diff off and work on it on your workbench, or swap it to a different gearset quickly.
ncjay
Dork
9/12/14 4:00 p.m.
It's a whole lot easier to replace a ring and pinion in a ford 9" style removable center section. If something goes terribly wrong with a removable center section, odds are pretty low you'll have to replace the whole rear end housing, but if a pinion decides it's had enough in the other style, there's a good chance it can take damage the housing enough to have to replace it.
oldtin
UberDork
9/12/14 4:18 p.m.
there's also these things - solid axle and IRS
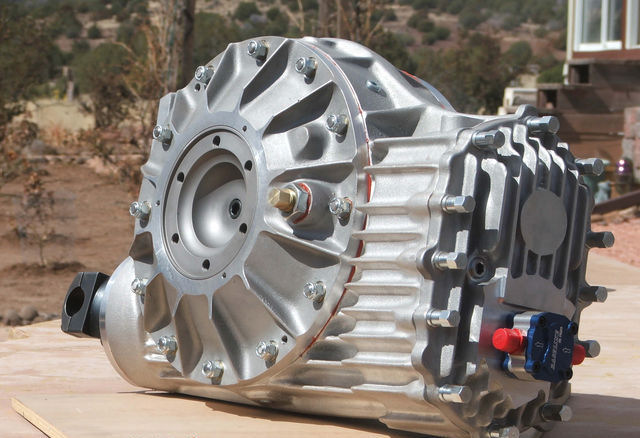
The advantage, to me, of a removable center section, is the ability to change gears without the need for adjustment or major dissasembly. Pull the axles, drop the diff.
Setting the crush sleeve on a GM 10 bolt is nerve racking. I didn't even draw blood dropping the diff on the 4Runner.
So is one better than the other? I liked working on the one on my REPU, but I'm not sure it is the strongest setup.
Are you thinking of doing an axle swap?
No, just wondering why the differences, and if there are advantages of one over another.
The 9" has a few strength advantages over most other light duty American designs: the angle that the gears mesh at and the extra pinion bearing being the most obvious.
A GM 12 bolt (and Ford's copy of it, the 8.8) is almost as strong and takes less power to turn, but gear changes are easier on the 9", which is the biggest reason why they are so popular in the racecar world..
44Dwarf
UltraDork
9/13/14 7:34 a.m.
novaderrik wrote:
but gear changes are easier on the 9", which is the biggest reason why they are so popular in the racecar world..
Not just easier but QUICKER. you can pull a chuck and swap it out in less then 20 minutes form the time the jack hits the bumper. I used to carry 10 different chucks with different ratio's me to the track. Never seen anyone even try to change gear ratios in a rear cover type at the track as you'd have to set pinion depth etc..
Knurled
PowerDork
9/13/14 12:36 p.m.
Mazdax605 wrote:
So is one better than the other? I liked working on the one on my REPU, but I'm not sure it is the strongest setup.
Well, banjo style rearends require that the axles be retained by the bearing, while cast center/cover style are typically used when the axles are retained by C-clips.
Besides allowing you to lose a wheel if the axle breaks, and allowing end float which drives disk brakes nuts, C-clip axles typically run the rollers directly on the axle surface, which wears the axle and tends to create a canyon over time, right where the stress is highest, which is an excellent way to break the axle. Also, using a C-clip to retain the axle means that you have to be able to install the C-clip, which means C-clip rearends generally have only two spider gears instead of four, and they can never have "Salisbury" style differentials. Or, for that matter, spools.
So major advantages for banjo in that respect. BUT they require a lot of stamping and welding, which costs money (electricity isn't free) and is labor intensive. Cover style rears just sort of have a tube rammed into a big casting, so they are cheaper to produce where energy and labor are expensive.