dherr
Reader
2/11/18 4:35 p.m.
Okay so I now have the exhaust in the engine compartment but have some issues with clearance of the body, engine, steering, etc... So here is my idea..... The radius of a 2.5 90 degree bend is still too long to fit, I really need to do a right angle right off the turbo housing and then run my downpipe and mate with the exhaust. So my plan is to weld up a square box of stainless Steel to the v-band flange and then run my 2.5 pipe at a right angle (heading towards the wheels and then down to the exhaust, bypassing the steering and everything else. If I build the box of a 3" square tube and then weld the downpipe to it, it wil not flow as well as a nice rounded tube, but does anyone see any real issues here? See below for what it looks like. As you can see, if I built the box off the v-band flange and then out towards the drivers fender, it keeps the exhaust from going past the transmission flange, which is where the body starts. Thoughts???
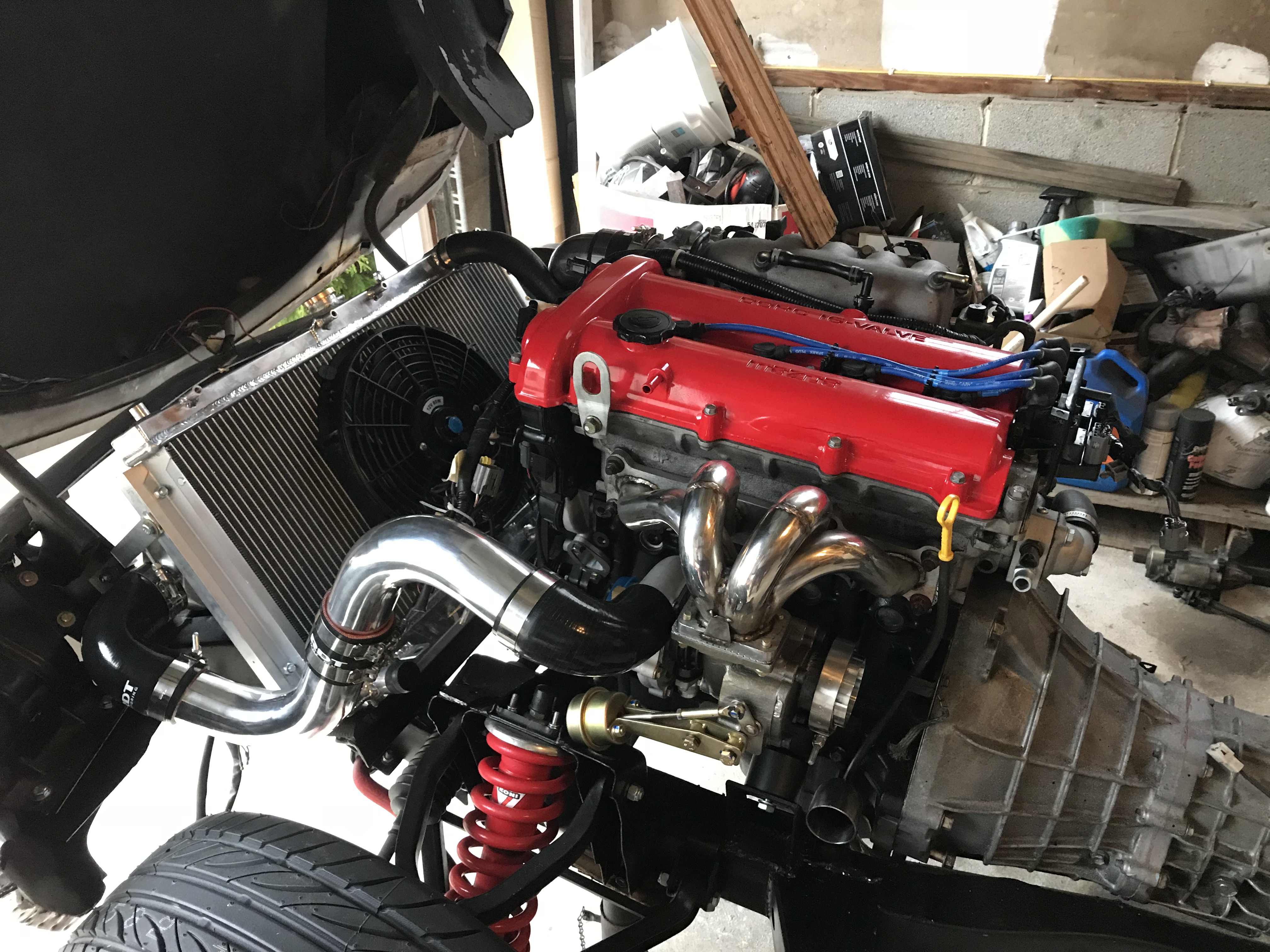
There used to be banjo type right angle turbine outlets available that supposedly flowed almost as well as a straight piece of tubing.
dherr
Reader
2/11/18 5:01 p.m.
Basically the v-band would dump into the box and then the downpipe would come out the side and run down to my exhaust
dherr
Reader
2/11/18 5:09 p.m.
My other option is to weld a hard 90 degree , so instead of an nice flowing curve, it would be restrictive, but would it be preferable to dump into a larger chamber and then flow down, or does it not really matter as both are going to be more restrictive than a nice curving bend. The turbo housing outlet is small (2") so I wanted the dump pipe to be larger and then go down to the 2" exhaust. Keep in mind this is a 1.8 and won't likely see more than 10-12 pounds of boost.
I think you want to ditch the V band and make your own downpipe bell. This is what I did on my 7 replica (also Miata engine, but TD04 from a WRX). I don't have any great pictures at the moment, but if you squint:
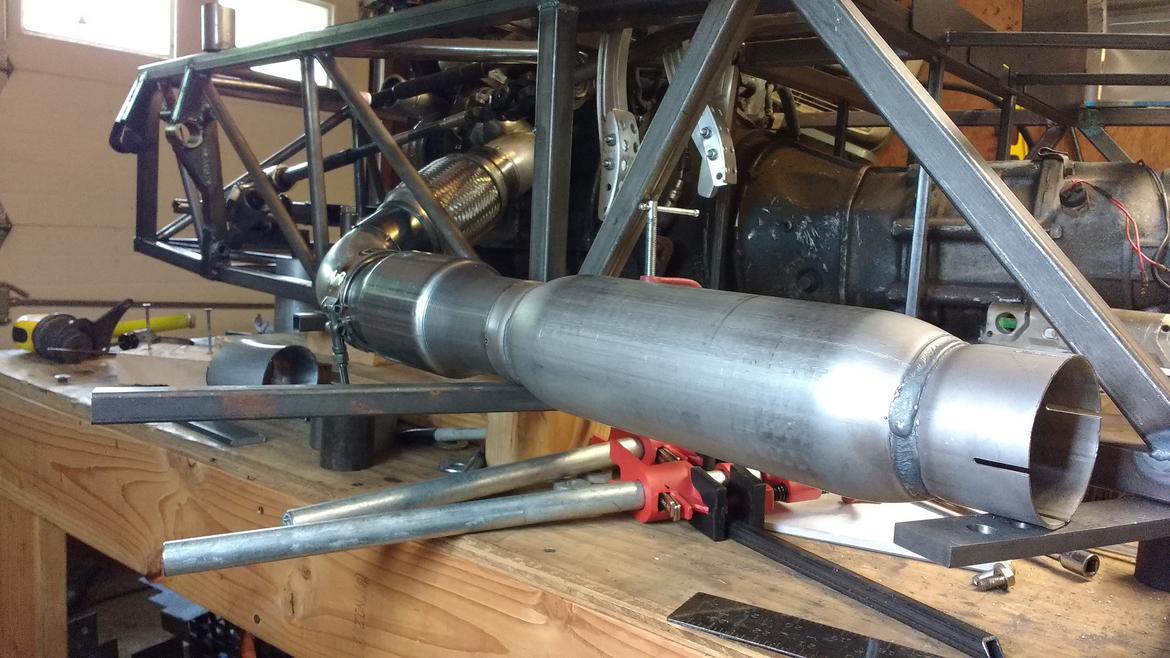
The footbox on the 7 is right behind the turbo, so it needed to make as pretty sharp turn. I think it ought to flow just fine. I'll finish my beer then brave the cold for a better picture.
dherr
Reader
2/11/18 5:23 p.m.
My other option is to weld a hard 90 degree , so instead of an nice flowing curve, it would be restrictive, but would it be preferable to dump into a larger chamber and then flow down, or does it not really matter as both are going to be more restrictive than a nice curving bend. The turbo housing outlet is small (2") so I wanted the dump pipe to be larger and then go down to the 2" exhaust. Keep in mind this is a 1.8 and won't likely see more than 10-12 pounds of boost.
dherr
Reader
2/11/18 5:26 p.m.
No that is why I ask the GRM crowd, There is no real reason that I can't just remove the vband turbo endplate and cut off the V-band and weld on a downpipe heading where I need to go. Please do finish your beer and send me a picture, but that is a great idea if I am thinking that I understand where you are going with this.
Beer finished. Cold braved. Picture obtained. Ignore the hamfisted stud...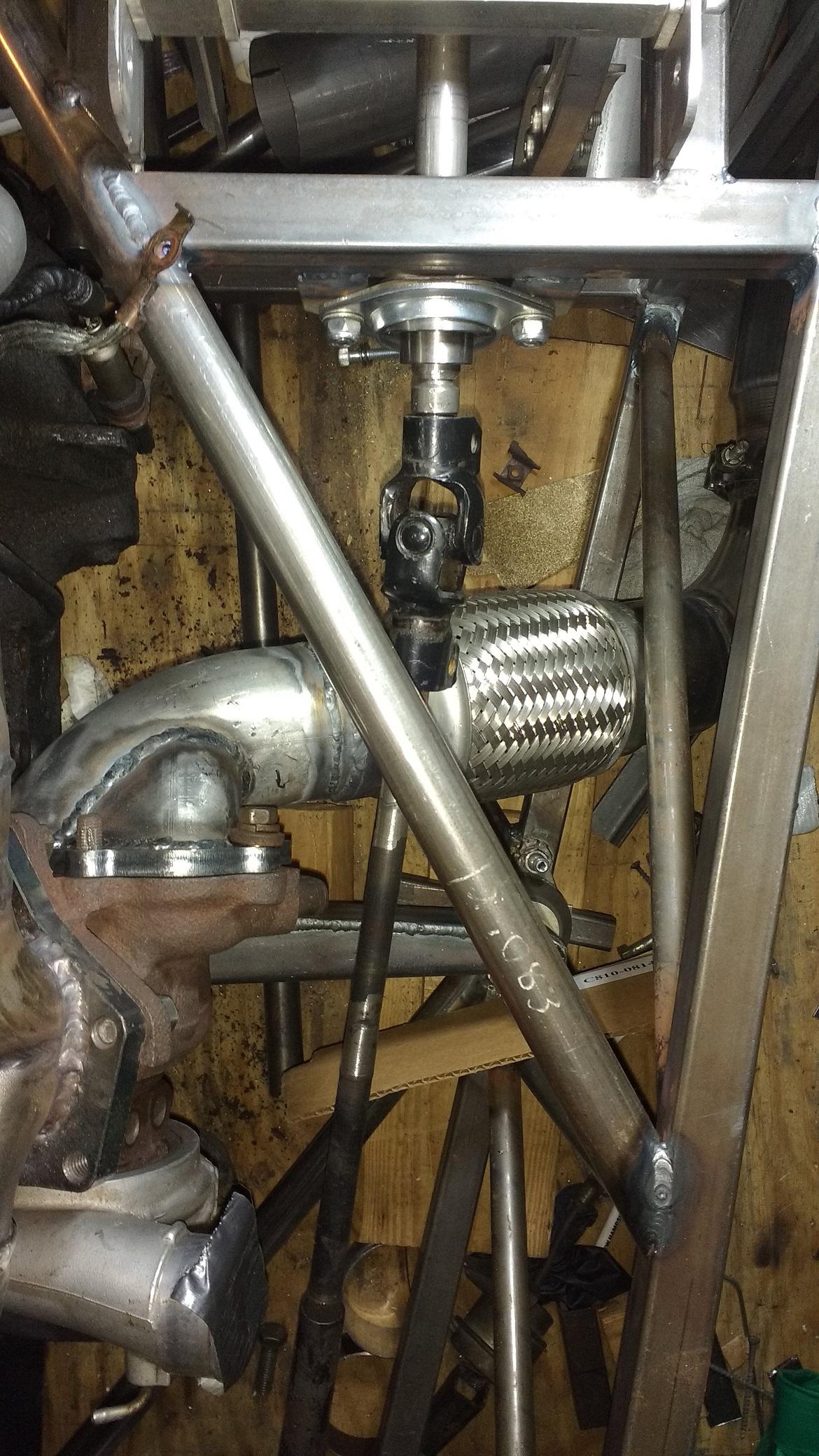
I started with a 3" stainless J-bend from Summit. You can see that the downpipe doesn't enter exactly perpendicular to the turbo flange, but the transition is pretty smooth.
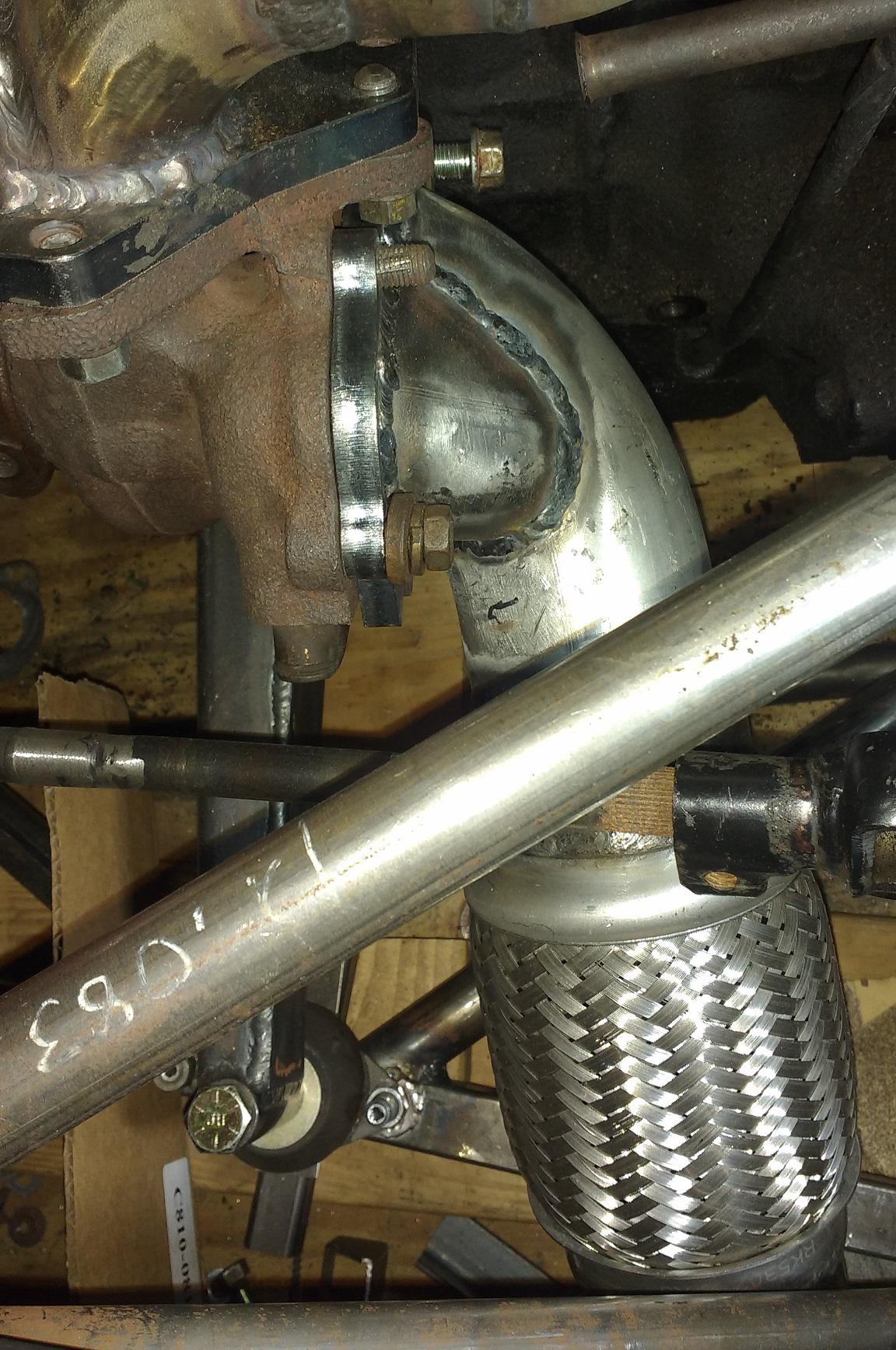
dherr
Reader
2/11/18 5:42 p.m.
Yes, I can do that :-)
Thanks, solves my problem. I owe you another beer!
JoeTR6
HalfDork
2/12/18 8:16 a.m.
That's a nice solution. Way to go, Brotus7. It should be better than the box idea.
dherr
Reader
2/12/18 1:12 p.m.
Yes, funny how these things work, I kept on thinking I had to start from the V-Band flange when, it it is not necessary and gains me back the 2 inches I needed. I ordered a 3mm thick 2.5 90 degree bend and will cut off the vband and weld it directly to the plate.

kb58
SuperDork
2/12/18 3:48 p.m.
I've seen turbine engines which are used "in reverse", where the exhaust turns through a tight 90 degrees, then though another gradual 90 degrees. The key is to feed the exhaust into a larger spherical volume, which trades velocity for pressure, then feeding that volume in the direction you want to go.
Basically, if you added a softball-sized volume right at that sharpest part of that turn, it would work better*.
*"Better" is some amount that's probably really hard to calculate.
If you can, oval it and enlarge the opening enough to expose the wastegate.
GVX19
Reader
2/12/18 7:26 p.m.