Stampie
PowerDork
1/15/19 12:52 p.m.
I need to weld some stainless for a project. Talking to my welding gas place they're concerned about MIG welding thinner pieces. Most of it will be 1/8th to 1/8th but I do have some 1/8th to 16 guage to do. It must be a water proof weld. This will be my first gas shielded welding but I like to think my flux core welding looks pretty good when I actually take my time. Think it's worth a try or best to pay someone to TIG it?
NOHOME
UltimaDork
1/15/19 1:15 p.m.
1/8" is not that thin and neither is 16 gauge. You should be able to weld that with the MIG to a watertight seam. Maybe not on the first pass, so are you going to be able to QC the job before the fluid goes in?
If Must Be Watertight, depending on what it is and how much, I'd consider subbing it out to a TIG professional. If watertight is not important, then MIG it. I do 16ga all the time. That's most of what I do. I have also done sanitary tubing for coolant pipes, and that had to be watertight, with my MIG. After welding, fill with water, check for leaks, drain, touch up, etc.
Stampie
PowerDork
1/15/19 1:43 p.m.
Yeah I can and will test before it gets installed in a working environment. I don't know why I listen to naysayers. I've spent most of my life saying I can do that and rarely am I wrong. Now it may take me thirty tries and I may spend 10 times as much but I'm a stubborn SoB.
How critical is getting it right the first time? Give it a shot with the MIG and if that doesn't work have someone with a TIG save the day?
If that's the case that should be doable with MIG as long as you aren't using fluxcore. CO2/Argon mix gas and .023" would be ideal, keep the amps low and stitch it. For the 1/8" to 16gauge joints, concentrate the heat on the 1/8" wall piece and let the puddle melt the 16gauge piece.
From what I understand you do NOT want to use a CO2 gas mix while MIG welding stainless. If you do, the welds will rust. 100% Argon is what you need.
There is an Argon/CO2 mix that is especially for stainless. They say the small amount of carbon enters the weld and lets it flow out or something. I use 100% Argon so that I can MIG weld aluminum if I need to. I don't need to very often, but when I do, it is nice to have the gas. 100% Argon is used for TIG welding stainless.
Stampie
PowerDork
1/15/19 3:22 p.m.
I think I'm going with a 98% Argon 2% Oxygen mix. That's what I see recommended the most. Thanks for the tips and I'll welcome more.
I use the 035 wire in my HF MIG. I think it works better for me than the thinner wire. I buy it by the 10 lb spool. Just bought a new spool a few weeks ago. You probably just want the 1 lb spool for this.
I MIG'ed a stainless fuel tank made from 0.040" sheet. Found a few small pinholes when I leak checked it with water and a little bit of air pressure. Touched up the pinholes with the MIG and job done. If you can, try to get the edges bent so that you are welding the edges of the panels where they are pinched together instead of just the sheets meeting in the corner. See the bottom left of the image below...
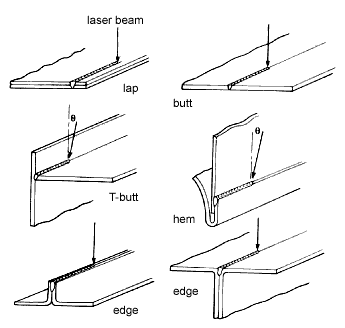
That gives you a little bit of help in getting the bead continuous and watertight.
Found another set of examples:

I use 100% argon on SS with my little buzz box Lincoln 140. Works well. Go slow and get the material flowing together. Best to get a couple pieces to practice with before hitting the real thing if you have not done it before but if you have welding experience you should do fine. If you can weld with flux core going to gas shield should not be an issue at all. You may never go back LOL
I use MIG to butt weld 16 gauge stainless exhaust all the time, and leakage is not an option.
The biggest problem with welding stainless is that it sucks at transferring heat. It doesn't like to start a puddle wicking around, and when you do get it going, it is very easy to blow a big hole in what you're doing because the heat isn't going anywhere, especially with a butt weld. This is not a big deal if you are using a TIG welder and can play with the heat as you're welding. With a MIG, you have that lovely fixed current and feed rate, so you need to develop you some technique.
I'd get a lot of scrap bits and experiment. What I usually end up doing is turn UP the heat, and only weld about a half inch at a time, then go around somewhere else for a bit. If the weld is staying cool, of course I'll keep going. The trick with this kind of welding technique is starting back up again and not getting a little pinhole tunnel. Again, lots of practice on scrap pieces before you start the important bit.
Good advice here. I suggest practicing on some small pieces and getting your settings right. I think that you should do it. If it leaks and you can't fix it take to welding shop and they can get it sealed.
I must be behind the times but I have always used tri-mix for mig on stainless, co2/Ar/He, and straight argon for TIG.
Stampie
PowerDork
1/16/19 9:59 a.m.
In reply to oldopelguy :
The places around here either won't sell tri-mix to new customers or they'll only sell large bottles at high prices. Seems there's a helium shortage going on.
Good advice from Knurled. Stainless welds nicely, but it is NOT like carbon steel. It needs more heat and it seems like the distance between "just enough to get a pool formed" and "blew a giant cratered hole" is a lot narrower.
What joint will you be welding? Practice that joint a bunch in crappy positions and you'll do fine.