SkinnyG
SuperDork
4/23/17 10:06 p.m.
I know, it sounds backwards, but bear with me.
The Lethal Locost gave up the Innovate LC-1 to the Crusty Chevy in an ill-fated attempt to TBI the Chevy. In doing so, it was discovered that the Bosch wideband sensor itself had cacked.
I still had the OEM-style wideband from when I Megasquirted the Locost back in 2009 or so, so I installed it and wired it back up.
I told Megasquirt (this time running MS1Extra) that I had a narrow band, and it changed my AFR table to volts instead of ratio, but gave me wideband voltage.
I changed my cruise range to 0.49V, the richer parts to 1.00, and the super lean parts to 0.00. I also made sure that closed loop was ONLY during the cruise portion of the map.
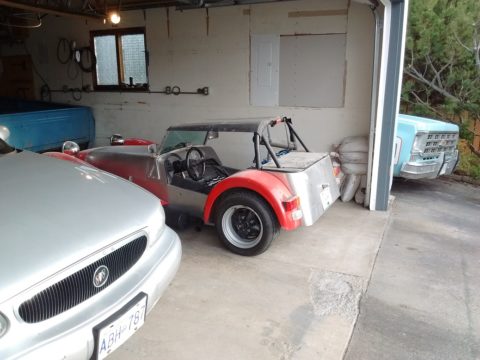
Took it out for a rip, and BOY HOWDY this thing is fun to drive.
A replacement wideband is currently in Calgary AB on its way to me now. Local auto parts house: $180CDN. Rockauto.com: $78CDN (and I forgot the stinking discount code).
On your WB sensor, what cracked?
If it was the heater- you need to be more careful when you turn it on....
alfadriver wrote:
you need to be more careful when you turn it on....
Say what. It is controlled by the wbo2 controller. I assume you mean more carful when installing?
dean1484 wrote:
alfadriver wrote:
you need to be more careful when you turn it on....
Say what. It is controlled by the wbo2 controller. I assume you mean more carful when installing?
No, careful when you turn it on. Even with the controller doing the work, it is still vulnerable to to drops of water in the exhaust cracking the heater.
It's only been in the last few years that the industry has figured out how to control the heaters so that they are robust to water.
And I know it sounds really odd that there is water drops in the exhaust- but even at 70F, the first few seconds of operation, water does condense out of the exhaust. The colder you get, the longer you have to wait to be sure.
For a 70F cold start, I wait 2-3 seconds before I turn on the heater.
The wide band should be only powered up when the motor is running.
The motor should never be run without the O2 powered.
This comes right from the horse's mouth.
I power the O2 from the fuel pump relay as that also dumps any electrical noise caused by the O2 sensor controller (which have proven to be very noisy).
bentwrench wrote:
The wide band should be only powered up when the motor is running.
The motor should never be run without the O2 powered.
This comes right from the horse's mouth.
I power the O2 from the fuel pump relay as that also dumps any electrical noise caused by the O2 sensor controller (which have proven to be very noisy).
What horse?
Cracking of O2 sensors is a real problem in the field, so we have to do everything we can to avoid it.
While you may not break a sensor, the risk of doing it is non-zero, especially the colder it is outside- perhaps people forget that exhaust is 15% water vapor, so it condenses pretty easily. All you need to wait is to have the exhaust get above about 120F before you turn the sensor on.
And I'm not sure why an engine should never run without an O2 sensor powered. That makes no sense at all. A good open loop calibration will deal with that quite well. Heck, we were doing PZEV calibrations 17 years ago and the engine was open loop for the first 13 seconds of running.
alfadriver wrote:
And I'm not sure why an engine should never run without an O2 sensor powered. That makes no sense at all. A good open loop calibration will deal with that quite well. Heck, we were doing PZEV calibrations 17 years ago and the engine was open loop for the first 13 seconds of running.
Most wideband manufacturers caution that running the engine without the sensor powered will trash the sensor. Not really sure why though.
As far as turn-on delay, that's a little tough to do with a lot of aftermarket setups. It would involve a delay-on relay to turn the wideband on a few seconds after engine start.
In the case of my Jeep, delaying wideband turn-on is not an option at all. I've got the wideband controller feeding narrowband output to the stock ECU. If it's still outputting 0v a few seconds after engine start, it'll throw a CEL and then it just runs open loop and ignores the O2 sensor. So the controller has to power up immediately at key-on for everything to behave electronically (takes 2 - 3 seconds for the controller to boot up and then it outputs 0.45v while the sensor is warming up, which keeps the stock ECU happy).
rslifkin wrote:
alfadriver wrote:
And I'm not sure why an engine should never run without an O2 sensor powered. That makes no sense at all. A good open loop calibration will deal with that quite well. Heck, we were doing PZEV calibrations 17 years ago and the engine was open loop for the first 13 seconds of running.
Most wideband manufacturers caution that running the engine without the sensor powered will trash the sensor. Not really sure why though.
As far as turn-on delay, that's a little tough to do with a lot of aftermarket setups. It would involve a delay-on relay to turn the wideband on a few seconds after engine start.
In the case of my Jeep, delaying wideband turn-on is not an option at all. I've got the wideband controller feeding narrowband output to the stock ECU. If it's still outputting 0v a few seconds after engine start, it'll throw a CEL and then it just runs open loop and ignores the O2 sensor. So the controller has to power up immediately at key-on for everything to behave electronically (takes 2 - 3 seconds for the controller to boot up and then it outputs 0.45v while the sensor is warming up, which keeps the stock ECU happy).
Since every aftermarket WB seller out there uses the same sensors that we use in production, their advice isn't valid. We do it every single time an engine is started. It's not bad for the sensor at all.
As long as you realize that you risk the same thing that happened, go ahead and power it all the time. Just be aware that cracking the sensor heater with a drop of water is a real risk.
As for aftermarket ECU's not being robust to a sensor not working- well... that's rather odd. I'd really want to do some careful shopping next time to make sure you can start and not cause a fault when the sensor is warming up. But basically, we have a ECU controlled heater that roughly uses a relay to turn the heater on at a specific time.
FWIW, we have to make sure that the emissions system lasts for 120-150k miles without breaking, or we pay for whatever breaks. And replacing UEGOs and HEGOs isn't trivial.
alfadriver wrote:
As long as you realize that you risk the same thing that happened, go ahead and power it all the time. Just be aware that cracking the sensor heater with a drop of water is a real risk.
As for aftermarket ECU's not being robust to a sensor not working- well... that's rather odd. I'd really want to do some careful shopping next time to make sure you can start and not cause a fault when the sensor is warming up. But basically, we have a ECU controlled heater that roughly uses a relay to turn the heater on at a specific time.
In my case, it's a stock ECU with somewhat limited tuning ability, so I have no control over when it starts to care about the O2 sensor coming live. I haven't cracked a sensor yet, but even if I do, I can live with replacing a single $50-ish sensor every couple of years. In my case, I've got the sensor mounted in one of those heatsink thingies Innovate sells (solved a sensor overheat problem I had a couple of times at WOT in hot weather), so that probably makes it harder for water drops to hit the sensor.
rslifkin wrote:
alfadriver wrote:
As long as you realize that you risk the same thing that happened, go ahead and power it all the time. Just be aware that cracking the sensor heater with a drop of water is a real risk.
As for aftermarket ECU's not being robust to a sensor not working- well... that's rather odd. I'd really want to do some careful shopping next time to make sure you can start and not cause a fault when the sensor is warming up. But basically, we have a ECU controlled heater that roughly uses a relay to turn the heater on at a specific time.
In my case, it's a stock ECU with somewhat limited tuning ability, so I have no control over when it starts to care about the O2 sensor coming live. I haven't cracked a sensor yet, but even if I do, I can live with replacing a single $50-ish sensor every couple of years. In my case, I've got the sensor mounted in one of those heatsink thingies Innovate sells (solved a sensor overheat problem I had a couple of times at WOT in hot weather), so that probably makes it harder for water drops to hit the sensor.
I'm confused now.
If you are running a stock ECU set up, it's already very capable of controlling when the sensor heaters turn on, AND it knows to ignore the senor while it's heating up.
If you want a good signal for that control- use the original heater control wire- it's already capable of high current. As long as it's not a PWM signal for heater control- it should be enough to power a WB sensor. Or use it as the switch for a digital relay.
(as a side note- it's good to know that Innovate's fix to over heating is a hardware problem instead of a software one.... saves me some shopping time, too)
SkinnyG
SuperDork
4/24/17 9:58 a.m.
Cacked
Died suddenly. Typically used to describe the improbable outcome of death due to unusual or unlikely circumstances.
The guy was a marathoner his whole life, model of fitness for everyone we know. He was taking out the garbage this morning when he just cacked.
http://www.urbandictionary.com/define.php?term=cacked
In reply to alfadriver:
I did contemplate using the stock heater circuit, but I'm not sure if it would properly control the heater in the wideband (as opposed to the stock narrowband sensor). And the wideband controller would probably freak if the heater circuit isn't hooked up...
Basically, I deleted the stock narrowband sensor and hooked the wire in the ECU harness that took output from the stock sensor to an analog output on the wideband controller. The controller feeds the ECU voltage to simulate a narrowband based on the data from the wideband and whatever value I set to be the "stoich" point.
AFAIK, their intention for the heatsink is for situations where the sensor is a little too close to the exhaust output and in an area where there's not a lot of airflow around the sensor and the sensor body is getting too hot. I'm pretty sure that was the issue in my setup, as it only happened on very hot summer days when the sensor body would have been running hotter. That was with an older LSU 4.2 sensor though. The spec sheets show a little higher body temp tolerance on the LSU 4.9 I'm running now (looks like 600 C vs 570 C), so it's possible I don't need the heat sink. I just never took it out when I swapped sensors.
T.J.
UltimaDork
4/24/17 10:06 a.m.
In reply to SkinnyG:
LOL. I had to go back and re-read your original post, as I too thought we were talking about cracking O2 sensors....
Anyway, glad your locost is running well and betting that it is a ton of fun.
SkinnyG wrote:
Cacked
Died suddenly. Typically used to describe the improbable outcome of death due to unusual or unlikely circumstances.
The guy was a marathoner his whole life, model of fitness for everyone we know. He was taking out the garbage this morning when he just cacked.
http://www.urbandictionary.com/define.php?term=cacked
LOL. Like TJ, I read cracked, not cacked. Mostly because I've never heard of that term.
In reply to rslifkin:
Well, we run the sensors regularly up to 800 C. And sometimes as hot as 900C. So if Innovate isn't robust to that, well....
BTW, if you are overheating the sensor on a hot day- something else is going on. The difference between a good day (70 F) and a really hot day (call it 120F) is 50 F, or about 30 C. Which is not much relative to the exhaust temps.... 
alfadriver wrote:
In reply to rslifkin:
Well, we run the sensors regularly up to 800 C. And sometimes as hot as 900C. So if Innovate isn't robust to that, well....
BTW, if you are overheating the sensor on a hot day- something else is going on. The difference between a good day (70 F) and a really hot day (call it 120F) is 50 F, or about 30 C. Which is not much relative to the exhaust temps....
Sensor tip temperature is rated to 930 C on both types. And yeah, the exhaust temp is far hotter. I'm thinking that the radiant exhaust heat was getting the sensor body too hot, so moving the sensor a hair further away from the pipe helped. There's not a lot of airflow where the sensor sits and there's a good bit of exhaust pipe around it to throw off heat. The cooler days probably were just enough of a difference to keep the sensor a few degrees cooler.
I may be looking into switching to a different setup anyway, as the thing didn't power up correctly on a couple of the cold days this winter (but was fine after a power-cycle). So something is dying in there...
SkinnyG
SuperDork
4/24/17 9:11 p.m.
No worries.
This has, however, certainly been learning experience for all of us!
(grin)
on a tangential note I like the top