I backed myself into a corner and now I'm screwed.
Reference THIS THREAD for more details.
Short story... need to build a 12' x 12' wall that folds down into a ramp. I failed to properly conceptualize the issue when I said "yeah, I can do that," because I'm Curtis and it's what I do. I assumed I could braze aluminum with that fun brazing rod stuff you see on TV where they fix a hole in a soda can with a propane torch.
I can't. I have a perfectly clean surface, scuffed with a stainless steel wire wheel. Unknown alloy, but it's sections of extension ladder. I have tried all sizes of torch tip (oxy acetylene) and every time, same thing. Test 1 was more like a soldering technique. Heat the joint up until the rod flowed into the gap. No bond. At all. Zero. Test 2-10 were all the same. I get things hot enough that the aluminum starts to puddle (and in some cases) a huge glob just dripped away. The rod flowed nicely into the joint, and still no bond. I can get some of them to bond very lightly. That is to say they stick about as well as a piece of scotch tape, but the slightest pull just lets them come apart.
I'm not getting carbon trails, so I know the torch is set right. I'm making it hot enough to melt the aluminum, but it still won't bond. I'm using Alumiweld rods from the Alumiweld company.
Tips? Thoughts?
find a guy with a spool gun for a mig.
Yep, that was my experience with that stuff when I tested it a few years back. I assumed then and now that I was doing something wrong, but never went any further. I was using a MAP gas torch though.
Time to resort to mechanical means of fastening if you're on a time crunch. Rivets and angle iron?
Gas welding aluminum is a fools errand, unless you are 69 years old and your grandfather taught you how he did it when he was fixing struts on a Sopwith Camel.
Fins a dude with a mig, and he may tell you that the alloy your ladder is made of is blended with Chinesium.
What kind of rod do you have? The stuff with flux in it?
Stefan
MegaDork
2/24/20 5:29 p.m.
The issue is that you need to preheat large items otherwise the heat just wicks away too quickly.
For something like a step ladder, you can't easily get an oven large enough to make it work.
I've used it successfully on smaller items, but the larger the item gets, the more heat you need throughout the piece and that gets more and more difficult. You only get one shot and you cant do more than one area on a piece or the first spot will melt.
I think proper brazing would work better, but there's a reason brazing isn't really done for structural pieces.
RossD
MegaDork
2/24/20 6:38 p.m.
What about the panel sealant stuff they use glue up monoques?
Stefan said:
The issue is that you need to preheat large items otherwise the heat just wicks away too quickly.
For something like a step ladder, you can't easily get an oven large enough to make it work.
I've used it successfully on smaller items, but the larger the item gets, the more heat you need throughout the piece and that gets more and more difficult. You only get one shot and you cant do more than one area on a piece or the first spot will melt.
I think proper brazing would work better, but there's a reason brazing isn't really done for structural pieces.
I agree with everything you said except the last line.
Brazing a joint that's properly designed is nearly as strong as a welded joint. The advantage of brazing is you don't have to melt the parts to be joined. I've seen some welded joints that later cracked right along the edge of the heat effected zone.
Is brazing the proper term here? We are using no brass. We are gas welding aluminum.
Don49
Dork
2/25/20 8:10 a.m.
Join with plates and panel bond adhesive? That stuff will tear the metal before it will separate.
I learned some brazing in engineering school. Properly done, it can be pretty strong. We're dealing with aluminum here, so it's already half the strength of steel anyway. Brazing aluminum is acceptable, and worth looking into.
I would second the recommendation for epoxy; bonding aluminum can make an incredibly strong joint, and is much less sensitive to process than brazing or welding.
Thanks for all the tips guys. Time crunch is really an issue. This has to be done by Friday and I'm working solo.
Already put the feelers out for MIG. I actually own a spool gun for my MIG, but just randomly deciding to weld aluminum is kinda like saying "I'm going to buy some rocket fuel so I can be an astronaut."
I also don't really have the time to research adhesives and get them here in time, and my budget is somewhere between zero and community theater.
You need a much larger tip on your torch. Get a "rosebud" tip the size of a shower head and that'll allow you to heat a big enough area to be able to melt your rod and form the joint.
Note - mig welding Aluminum with a spool gun is about as easy as it gets. The welds look a little splatery but they can be as strong as the alloy. The only thing with a spool gun is its better on thicker aluminum, don't know what your welding but that may be an issue. My miller welder had a plug in point just for the spool gun. Change the gas, plug it in and I was GTG (maybe had to switch polarity, I don't recall).
Otherwise, what about the ol pop rivet treatment?
Regarding the brazing. I found (using the aluminum can welding type sticks) that using a metal scrapper (dental pick) to scrape the surface under the melted pool, for whatever reason, seems to make it stick.
aircooled said:
Regarding the brazing. I found (using the aluminum can welding type sticks) that using a metal scrapper (dental pick) to scrape the surface under the melted pool, for whatever reason, seems to make it stick.
Agree. The first time I heard about "Alumaweld" was years ago. At that time the process was to scratch the surface under the molten pool of filler metal to remove the oxides to get better
adhesion. You can use the rod itself for this or a piece of stainless steel welding rod. The key is heat control, if your use the filler rod as the scratching rod you have to keep the material just at or below the melting point of the rod. With a SS rod you can just rub away.
Don49
Dork
2/25/20 5:46 p.m.
Curtis, your local auto body supply or parts store will have the panel bonder. Try Colours inc.
Well, for better or worse, I got this far today. What you're seeing is 1 x 2-7/8" lumber as a frame with the iso glued in with marine epoxy and a little bit of microfiber powder to prevent it all dripping out.
From here, I need to cut and fill in the other panels near the top and finish the rough assembly. Then a couple coats of contact cement and luan on both sides nailed to the 1-by. I'm basically building a big theatrical flat wall, but using the iso foam to fill the voids so you can walk on the luan. I will take my I-beam and epoxy and screw it on the hinge end. If the top proves too floppy, I have another piece of I beam I can put up there as well.
Then I think I'll lay a bunch of 3/4 ply on top and drive my lawn tractor on it until the contact cement cures.
As far as the rest of things, I'm going to cave. I'm going to build a structural ramp that sits on the floor to actually carry the weight. That way, this thing only needs to lay on the structural ramp.
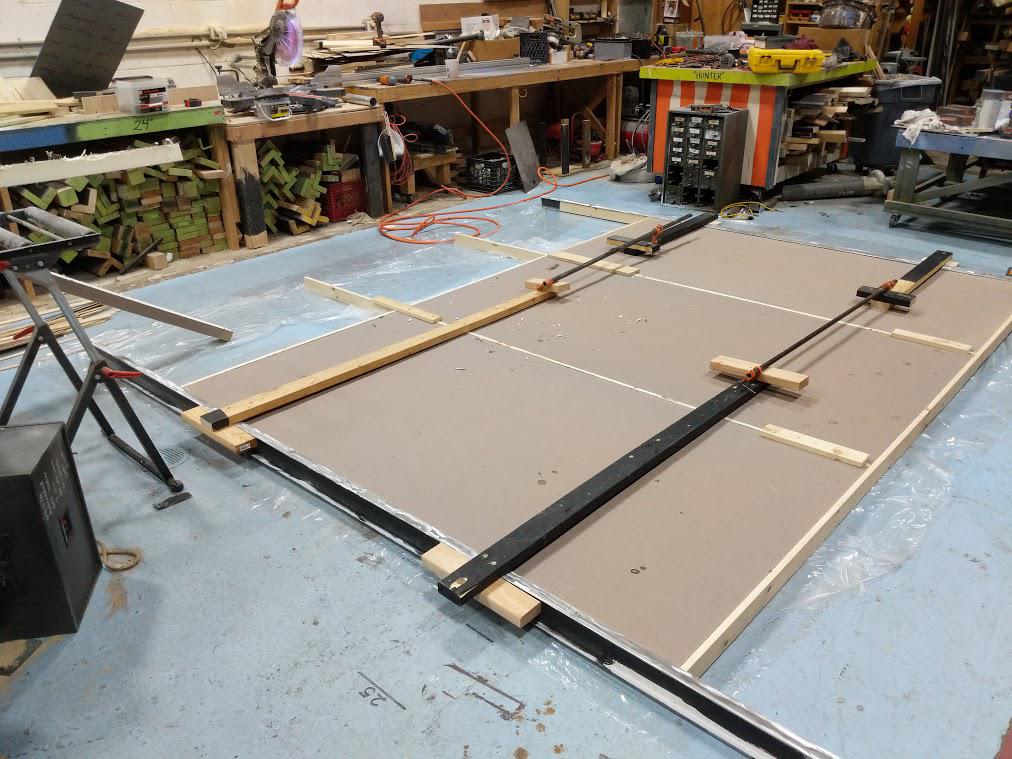
I will definitely try that panel adhesive sometime. I just didn't feel confident with the learning curve. Nothing says "performance review" at work like a set failing in the middle of a production.
My spool gun is one of those things thats rarely used but when you need it, you need it. Been able to get good results with a Lincoln 185c, argon shielding gas, spool gun, and a little MAPP preheat plus some proper technique. Cautionary note, it draws some decent power. 230 at 30A minimum to get anything respectable.
My welding cart has a bottle or argon and a bottle of tri-mix and I swap regulators between the TIG and the MIG depending on what I am working on.
Ransom
UltimaDork
2/25/20 11:45 p.m.
It's not really useful info at this point, I suppose, but the very first thing I did (after a test) upon buying my MIG welder was to weld aluminum stub manifolds for the 2002's ITB setup. No spool gun, just laid everything out so there was little twist in the line. They weren't gorgeous, but they worked fine for years.
My job was not on the line.
Gary
UltraDork
2/26/20 12:19 a.m.
Curtis, my man. Go to a pro. I think you need a good MIG or TIG welder to do this work. Make somebody else responsible. Pay a bit more for this to be done the right way, and absolve you from responsibility.
(I personally would not rely on epoxy glue without an "engineering professional" assuming responsibility).