I have watched all kinds of videos on how to homebrew an aluminum forge, but I want to do some copper stuff. Assuming I can get 2000 degrees somehow, can I transfer those techniques to copper?
I've been looking for copper sheet or stamped copper for the wall behind my fireplace, and I think I can just pony up the dough and buy that. I had been looking for slate for the hearth, but surprisingly that has been harder to find in a logical size that will logically fit without strange cuts and sizes.
So I thought maybe I could find a bunch of scrap copper; wire, old pans, roofing flashing, plumbing, etc, and make a cast copper plate or several copper tiles for the hearth. Give it a little pickling from vinegar and ammonia and glue it down.
Am I crazy? Well, yes, I am crazy... but am I crazy for thinking I can do this?
Melting and pouring pure copper isn't more complicated or dangerous for a homegamer than aluminum, just hotter as you say.
The problem is in the zinc content of the unknown scrap copper alloys you might want to recycle. Metal fume fever is no fun.
Mr_Asa
SuperDork
10/10/20 6:33 p.m.
Like he said. Should be no real problem orher than the zinc or other impurities
I noticed a few folks casting in steel molds, so I guess it doesn't stick to it. I would probably want to do some kind of design on it which would mean sand or some other formable material. Not sure if I want to get into buying all the stuff... but I might get the bug and want to do more.
The hearth is 52" long and 16" wide and needs to be 1/4" thick (or darn close to it) to prevent trip hazards on the floor. For that reason I need to make something either the full size (mono pour) or some logical division of it like 6.5" x 8" or 13" x 16" ... obvious adjustments of course if I choose to do grout lines.
Safe to assume that smaller sizes would be an easier pour?
Anything I should add to help the flow? Tin? I know that works for iron.
Mr_Asa
SuperDork
10/10/20 7:32 p.m.
If only in terms of shrinkage and warping, yeah the shorter ones would probably be easier
Copper melting video from a fellow GRMer:
https://www.youtube.com/watch?v=pxgeKum5Z_k
You may be interested in aluminum bronze which is an alloy of aluminum and copper.
Building a foundry furnace and a burner can be quite intensive till you get it right.
Best advice is find a guy that is already set up w/ foundry furnace, burner, tools and w/ sand molding.
Great videos. Watched a bunch of them.
Looks like I'm going down a Curtis rabbit hole again.
Mr_Asa
SuperDork
10/10/20 8:59 p.m.
You might be able to get by with something as simple as one of these
https://smile.amazon.com/dp/B0819LL8H2/
Just ordered a smelting furnace. If I don't succeed, I'll have started a new hobby.
Maybe it could be a really fast coffee roaster. :)
Honsch
New Reader
10/11/20 12:55 a.m.
Is it wise to use a material that is as thermally conductive as copper to contain fire?
That sounds like a recipe to light stuff on fire behind the copper.
Tk8398
Reader
10/11/20 1:59 a.m.
I have done it before in a small gas forge and it worked ok. It was only a small amount and I didn't make anything fancy from it, but i just used a stainless steel pipe with a plate welded to the end and filled it with copper scrap.
https://www.amazon.com/gp/product/B08HSN1LRH/ref=ppx_yo_dt_b_asin_title_o00_s00?ie=UTF8&psc=1
Thought I'd give this one a try. If it doesn't work, I'll be deep frying a lot of turkeys.
Now I need to get some sand.
All of the videos I see do a two-sided mold which makes sense for casting things with two distinct sides like knife blades, bullets, and copies of badges. For this project, couldn't I just do a one-sided pour? For instance, take my original die (maybe a ceramic tile with a design I like) and make an imprint in some sand, then just pour straight in? It would make an ingot so to speak with a design on the front.
Like if I took this tile and squished it into the sand making a 1/4" deep impression, then just poured it straight in?
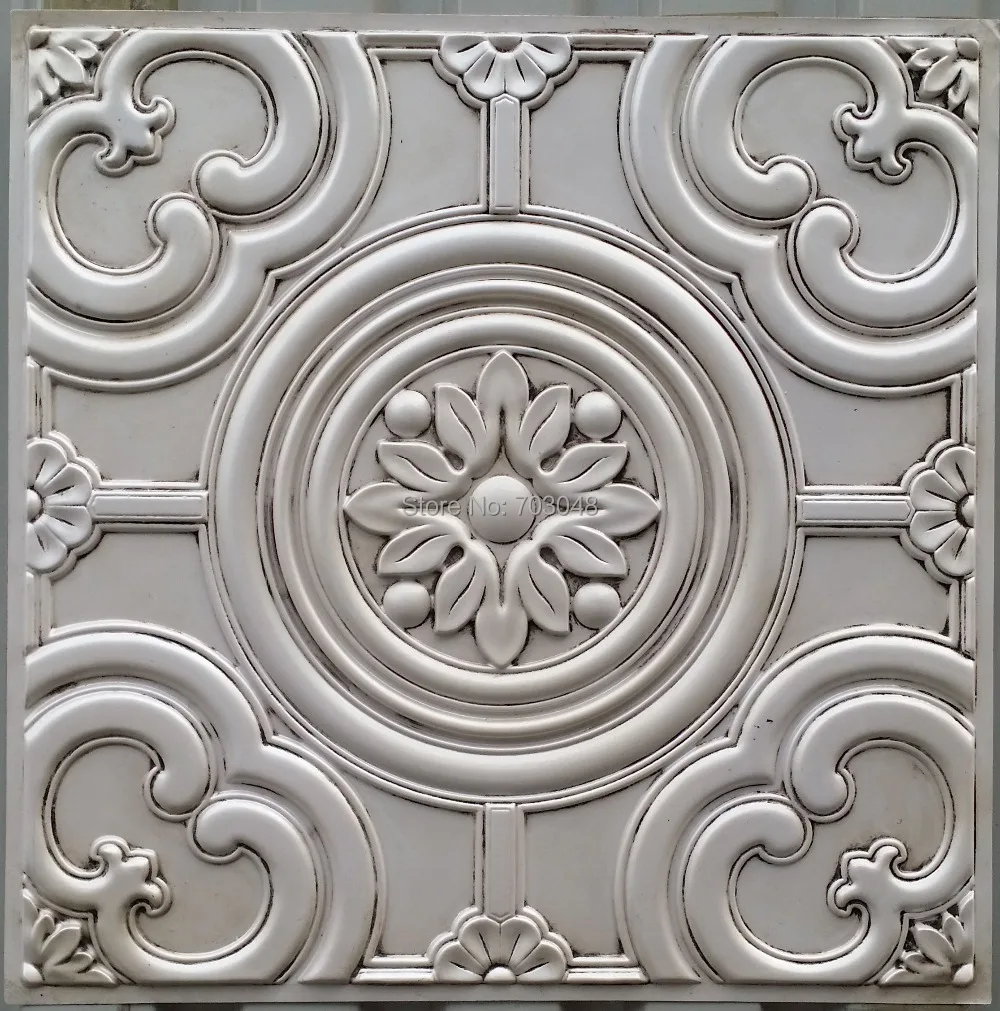
Mr_Asa
SuperDork
10/11/20 10:11 a.m.
I seem to remember that there are a couple possible issues with open molds, but I can't remember what they are right now.
With a well designed closed mold you get all the impurities that you cant skim off in the cup and gate. Maybe thats it?
Uneven cooling as well, which could lead to warping.
Here is another metal casting YouTube channel: https://www.youtube.com/c/swdweeb/videos. Perry covers all the basics of metal casting. There are several other channels worth watching but can be way more advanced for your needs.
Alloy Avenue used to be the go to metal casting forum but AFAIK they are not active anymore, archives may still be available.
http://forums.thehomefoundry.org/index.php is my current go to for casting. They can be highly technical at times but welcome any beginners.
Edit 10/12: bigstackD does a lotta copper melts