We have a 200 year old farm house that is our weekend/country home. My Great-Grandfather purchased the farm in 1911, so it has a lot of sentimental value and I plan to die there some day.
The middle part of the house is a 15x20 log cabin. Last winter I raised/vaulted the ceiling from 69" to 96". The floor joists are poplar measuring ~ 2 1/2" by 6 3/8". They are on 24" centers and span ~14'. The floor is 3/4" T&G poplar.
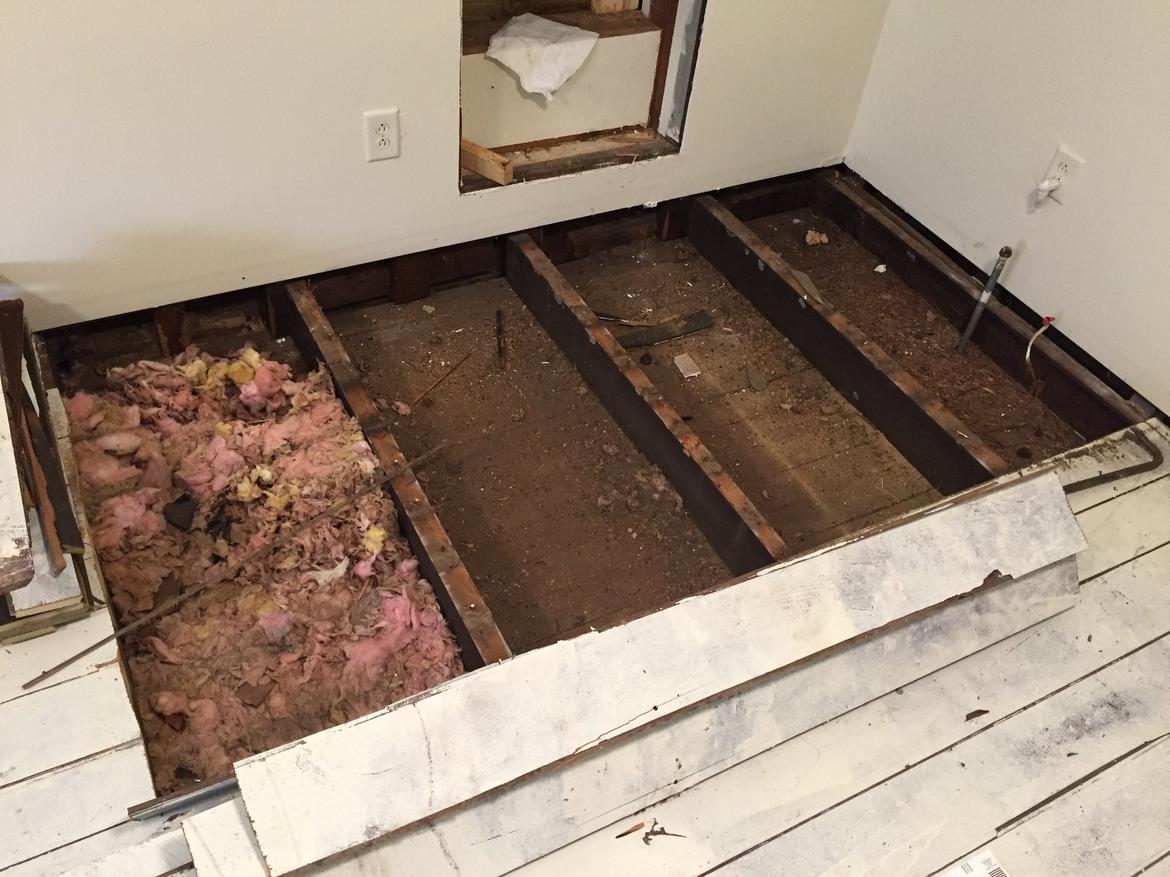
As you would imagine, the floor has plenty of bounce. My plan to fix/reduce that is to sister some 2x6s onto the existing joists with 3/4" plywood between them. Then I would bridge the joists with 2x6s and add some regular t&g decking.
Plan Z would be to sister 2x12s to the existing joists and deck as above. I don't really want to give up the ceiling height though and the 12s would have to be notched on the ends to get back to the logs. I don't think I can get anything wider than a 2x12s.
Any suggestions/comments?
Duke
MegaDork
2/26/18 4:08 p.m.
In addition to the flitch beams you are making, I would add another 2x6 halfway between each of the sistered ones. You'll have to shim the bearing ends 7/8" or so, so they are flush withe the tops of the existing framing.
The plywood flitches will definitely help the stiffness, but distributing the load over more members will help as well. It will also reduce flex of the flooring between the 24" centers.
Duke
MegaDork
2/26/18 4:14 p.m.
By "bridge the joists with some 2x6s", do you mean add another layer of cross framing on top of these? If so, I wouldn't. I would halve the joist centers by adding one in the middle of each bay as described above. You can also use these to put your subflooring sheet joints at exactly 48" OC, even if your existing framing is a bit off.
On another note, are we looking at the top side of a drywall ceiling below? Because if that's dirt or a mud slab, you need to excavate that down at least 8" below the bottoms of the joists, stat.
By bridge I mean 2x6s cut to fit in the bays, perpendicular to the joists. They're probably not called bridges - I think bridges might be the diagonals installed in an X between the joists- but you get the idea. The problem with adding joists is getting them to bear on the log walls. Those joists were originally logs notched into the wall logs. To add additional joists, I'd have to notch the wall logs. However, joist hangers would probably work if I can get to the logs.
The photo shows the upstairs floor partially removed, revealing the top side of the 3/4" poplar ceiling of the downstairs. When the kids carry on upstairs, all that fluff and debris sprinkles down through the cracks and onto your head, into your coffee, etc. There was a family of flying squirrels living in another part of the house and they used those uninsulated bays as a foyer to the outside.
Deeper member is the answer to reduce flex. But that'll mess up your ceiling, so engineered lumber, like microlam is probably next best.
My logic: You MAY be able to get some select structural grade 2x8 and rip it down to 6 3/8" deep but you can definitely get engineered wood that is strong. 14' span is really long for 6" deep wood. Don't buy 2x6. Every inch of depth is valuable. If you only need a handful, spend the extra eighty bucks on microlam.
And do what Duke said about 12" o.c. - joist hangers are fine.
T.J.
MegaDork
2/26/18 8:42 p.m.
Is all the bounciness from the joists or do the floor boards also bounce? 3/4" thick poplar with a 24" span seems like it would be ok, but these boards may have been up there for a century. Just asking because if you go through all the trouble of adding new stronger joists but the floor boards themselves are the weak link you would've spent a lot of effort and not fixed the problem. With a 14' span, I suspect the joists are the main issue, but just wanted to bring up the possibility of the floor boards being the culprit or a partial culprit.
T.J.
MegaDork
2/26/18 8:45 p.m.
Is there any way you could put a beam in the room below to cut the span down from 14' to half that? Maybe not lower the entire ceiling down there or raise the floor upstairs, but just add a beam across the room below along the ceiling?
The floorboards are going away. They do have some spring to them and are nailed down with type B square cut nails so they’ve been there a while
Cant do a beam downstairs. There is a door on one end and a fireplace on the other.
I’m not sure why I only realized it now, but you’re right about the 2x6s. They’re 5 1/2” wide so I’m basically an inch less than what’s there. I can probably work with full 2x8s and not affect the stairs too much.
Thanks for the input so far. Would liquid nails do anything for the flitch beam and/or the new subfloor?
Duke
MegaDork
2/27/18 8:03 a.m.
In reply to Apis Mellifera :
Glue would be a good idea, in somewhat of a belt-and-suspenders kind of way. Enough screws through the flitch / sisters - think 2 or 3 rows, 8"-12" on center, staggered - will hold it. But glue will really bond them together so they work compositely with the existing members.
Glue on the top face of the framing when you set the subfloor will help prevent squeaks, and add some compression stiffness where you need it.
SVreX
MegaDork
2/27/18 11:35 a.m.
I agree with what Duke is saying about the framing.
I wouldn't use regular T&G decking. Use Advantech T&G engineered panels, and glue them to the joists. They are MUCH stiffer than T&G decking.
In reply to Apis Mellifera :
Find a sawmill. Have custom Timbers sawn. One source if you don’t know any is wood miser
solid beams gain stiffness with width not only depth. I needed to span a 20’x16’room the charts required more than the 10” I could fit until I went to a 14 inch wide by 10 inch deep beam.
Since Ash was cheap at the time a 20’ long 14” wide X 10”deep beam gave me the required stiffness and only cost me $56.
If I bought such a thing from a lumberyard it would have cost over $500.00. But by buying it from the right sawmill it wound up being $56.00. You have to shop sawmills aggressively and find out what wood they have that is surplus.
ncjay
SuperDork
2/28/18 4:09 p.m.

Thread title had me thinking of this, or which I'm probably more qualified to repair than a real wood floor.