Here's my logic on luan or masonite. The inside of the oven will be 450F, which means the outside of the cabinet will be 450F. Then it has to make it through 3.5" of glass except where it contacts the studs.
So if wood burns at 400-450F, I don't imagine it will start to char unless I'm missing something.
Old fridges would offer steel sheet, as would old dryers, freezers, or washers. I'm just afraid that will be some serious leg work, lifting, and hauling over a long period of time and taking up a lot of space and cutoff wheels.
I also thought about drywall, but I think that would get destroyed quickly. Hardie backer would work but it's not much cheaper than buying steel.
I'm currently looking for corrugated steel roofing or aluminum siding. Going rate is about $1/ft for used steel roofing which wouldn't be terrible.... but also not very rigid.
can you be sure 450F is not 500F at times ?
Just wondering if you should engineer for a little more leeway ?
Curtis73 (Forum Supporter) said:
This would be with the four conductors. Is this kosher? Or at least not going to kill anyone? The fan is 0.3A
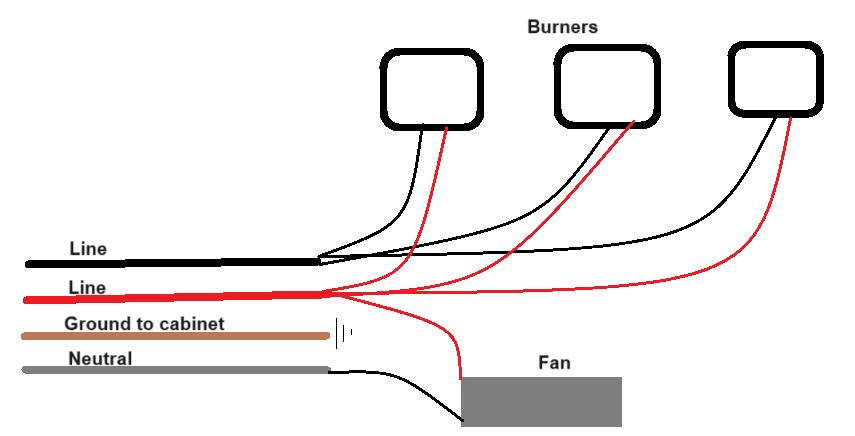
Technically, this would be considered inside of an appliance. Builder's codes go right out the window once you are inside an appliance. Your stove uses 120v from one leg of its 240v power source to run the electronics, fans, and light bulbs. This is no different. Do it.
californiamilleghia said:
can you be sure 450F is not 500F at times ?
Just wondering if you should engineer for a little more leeway ?
You're all not wrong, I'm just impatient and cheap
My whole oven is made from that kind of sheet. The only issue I have had is one time I was trying to cure a ceramic coating that required 750F. I know for a fact the top of the oven was above the 900 or so that galvanizing will burn off. I sat outside my shop as the oven smoked for almost an hour. I came back the next day to find a few dead lizards in the office area.
As for temps for curing, you won't need to go up to 450 ever for powder. You may need to go to 430 or so to outgas a used part so anything bad won't cook out at a 400F cure temp.
You can also talk to the powder supplier about cure temps. A powder that says 10 minutes at 400 can sometimes be cured at 375 for 15 minutes or maybe even 25 minutes at 350.
I don't think I have enough wattage to get that hot.
I'm getting impatient waiting for Amazon deliveries.
QUESTION OF THE DAY: The directions that came with my PID and SSR are... um... definitely not written by someone who has a deep understanding of English. I know the trigger from the PID goes on 3 and 4. Do I just put one of the lines through 1 and 2 and wire the other line directly to the burners?
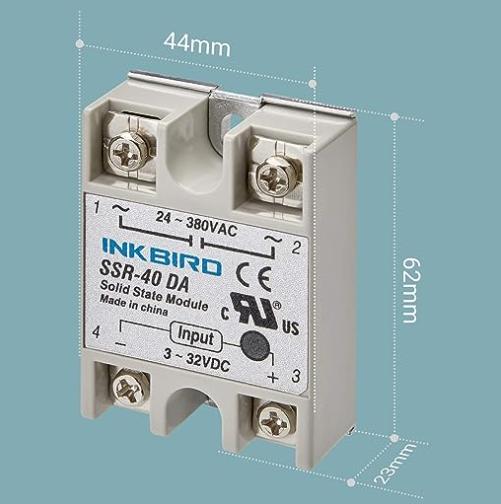
In reply to Curtis73 (Forum Supporter) :
Correct.
In reply to Toyman! :
Potentially dumb follow-up question. Any benefit to adding a second SSR for the second leg? I'm dealing with a 7-foot tall chunk of steel covered with steel studs and sheathed with more steel that is carrying 40A of 240v juice. It would be nice to know that "off" means no voltage instead of the potential for "maybe 120v if that one burner contact decided to bend over and touch the j-box when it got hot."
I mean, I don't exactly have a big R&D budget here, and a second SSR is $10.
I'm finding this to be a bigger project than anticipated. Nothing apocalyptic, just time consuming.
I got some galvanized sheet steel for cheap today. 4x10 sheets for $15. The downside is that it's a bit thicker than I need, so cutting and bending has my right hand in cramps.
- cut and bent the first steel sheet panel
- pulled off the paper from the back of the fiberglass (you convinced me)
- wired up a fair portion of the control box - PID, SSR, buss bars, SO supply line, dimmer for the circulator fan. I just need to get the skin on the oven so I can mount and mate the wiring from the oven to the box.
- Discovered that the load panel I wanted to use (had two knockouts still in place) for some reason has 16 knockouts, but only space for 12 breakers. It's fine, though. I have a double slot in a 200A panel on the other side of the room and I think just enough pigtail to get the oven outside. We'll see.
- Stole a rolling wardrobe rack from the costume shop so I have a place to hang and powder
It's coming along. I'm going to order some powder tomorrow.
In reply to Curtis73 (Forum Supporter)
It won't hurt because then you know there is no power anywhere. Is it necessary? The cabinet is grounded, and the j box is grounded. If anything with power comes in contact with any steel, it's going to let you know by either tripping the breaker or throwing a shower of sparks.
I decided to KISS on the electrical. I had enough 8/3 SO laying around to do the job, but buying 30' of 8/4 SO, a 14-50R, a 14-50P, the clamps, a J-box, etc, it was going to add another almost $200. I'm just going with the 8/3 and I added a 120v extension cord to the box to run the fan. I figure the minor inconvenience of plugging in two cords is less hassle than pulling two more bills out of my wallet.
Skin is almost done. I'm going to attach to control box to the side with some 1" EMT spacers to allow air space in between the cabinet and box. No need to overheat the PID and SSD.
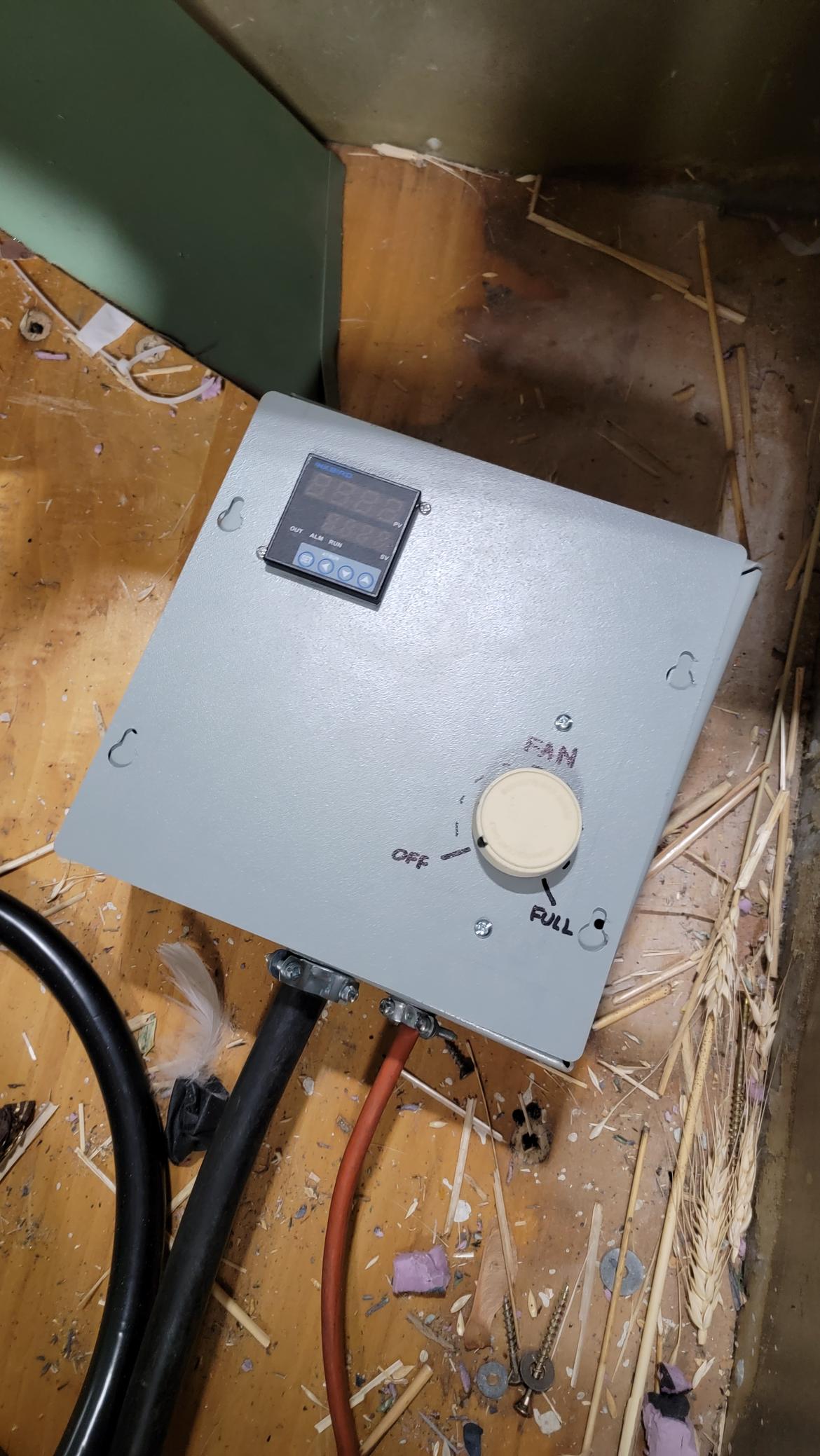
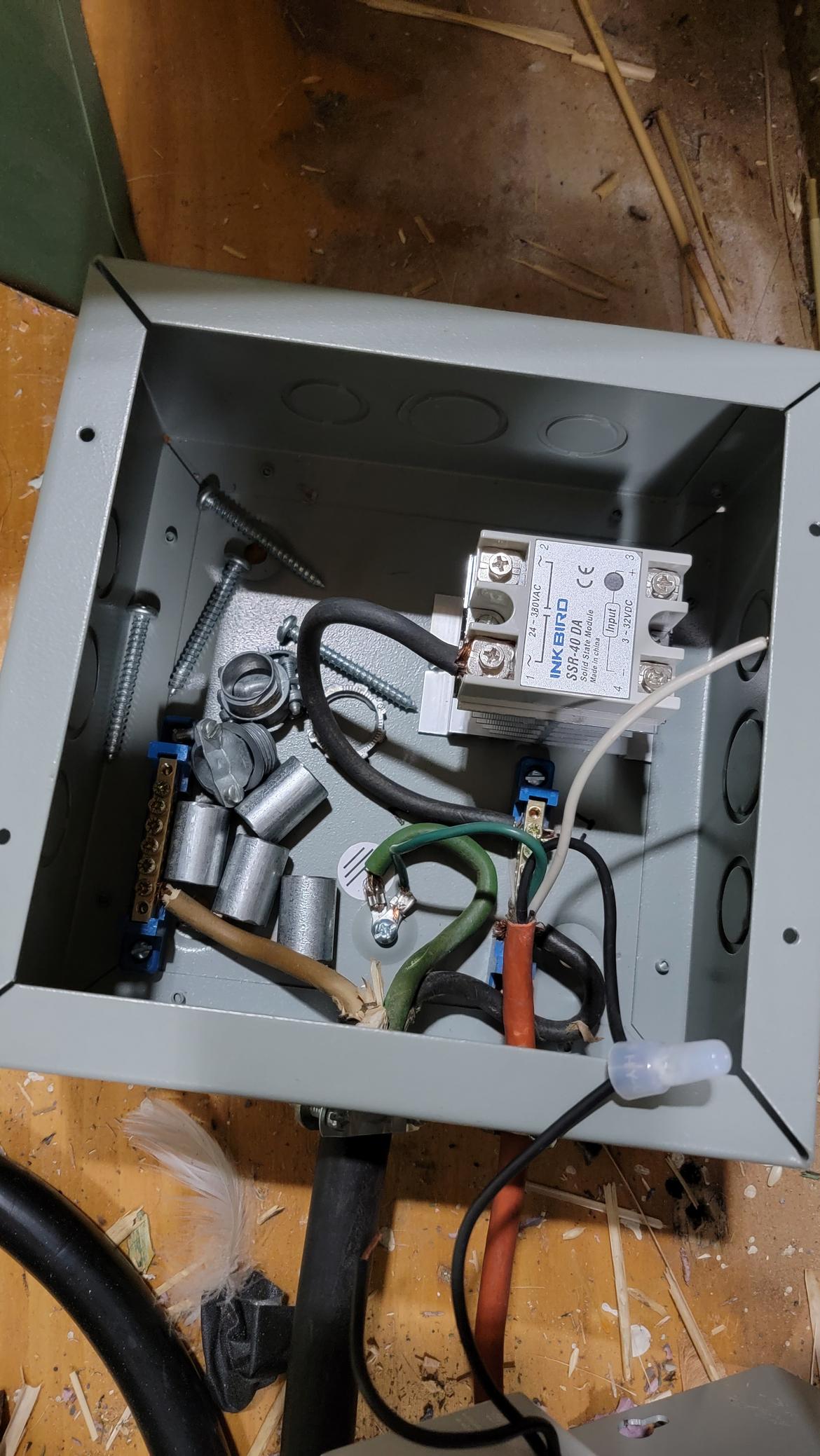
Ohmigosh... it's so close! Ran out of hi-temp wire to get juice to the circulation fan and it's running late on the shipping.
- Skin is done with the exception of the last few screws. Still need to reach in to fish the fan wiring up to the access
- corners and seams are all taped, which is partly to keep air in/water out (in case rain blowing under the roof while it's outside cooking), but also to prevent sharp metal edges and cuts.
- got the door on and hinged with a handle and latches.
- installed the BBQ gasket tape around the door and got a pretty good seal.
- added another handle to the far side
Part of me wants to paint it purple and put a big googly-eye on the front. That way, I can call it the one-eyed, one-door, frying, purple powdercoater.
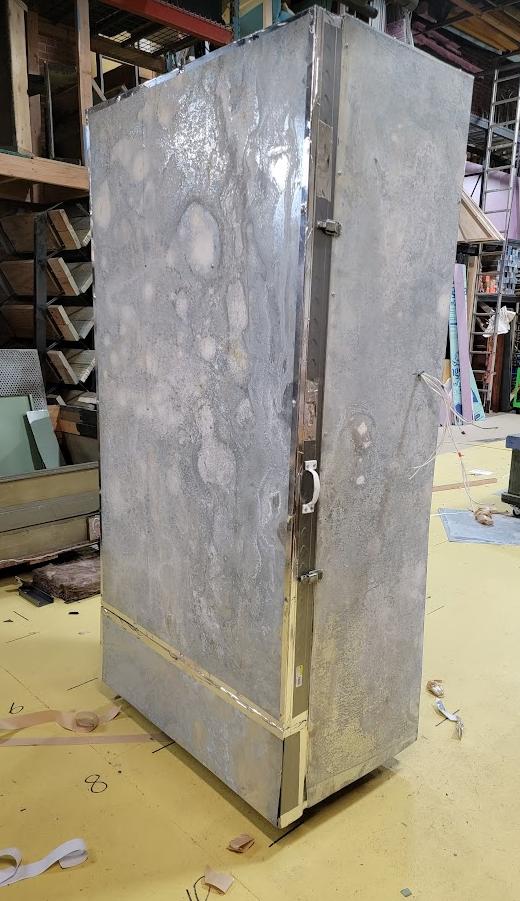
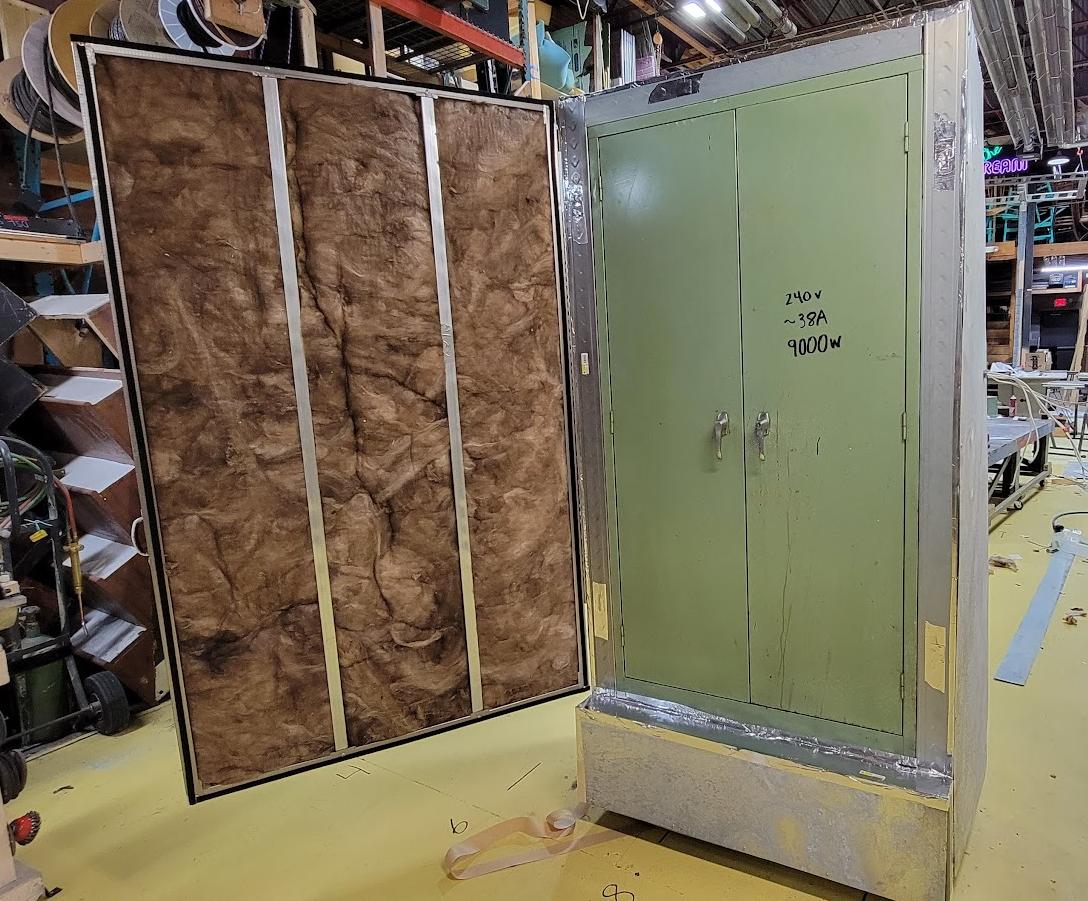

Well, it's about as done as it's going to get.
Finished the wiring and screwed the control box to the side. Still need to make up a schematic for my own reference later, but for now I just scribbled my color code on the control box. Next step is to stab the 40A breaker in the box and wire up the 6-50R.
Question of the day: If I want to merge two 120v circuits to one bay in the panel, do I have to get a skinny double breaker, or can I just move the black to another breaker and have two blacks on one pole? That wall of the shop has breakers for outlets along the workbench, all of them 20A, but each breaker only feeds one outlet. I get why they did it, so you could run multiple tools at once, like the radial arm saw, the chop saw, and the router table without overloading one circuit. I'm the only person who works in this shop, so multiple tools aren't happening, nor do I think any two of those tools would draw more than 10A each.
For instance, in this photo, could I move the black from the #6 breaker to the #4 breaker, thereby giving #4 two blacks from the pole? The goal is to free up the #6 slot so I can use 6 and 8 for my two-pole breaker. I know I've seen it done before, but wasn't sure if it was legal.
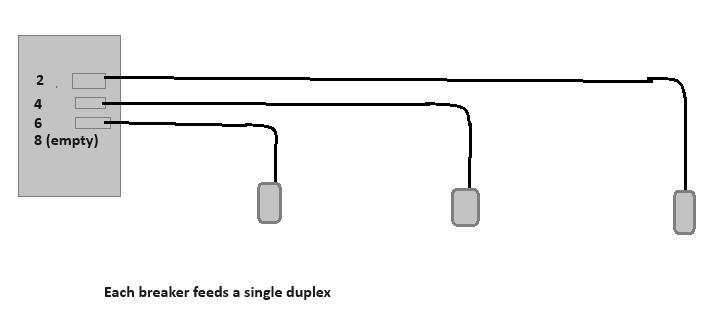
I am not an electrician so take this with a grain or 2 of salt. I believe it would be more correct to daisy-chain the outlet on circuit 6 to circuit 4 vs having two feeders connected to the same breaker. The screws on breakers are not made to be double-tapped. You could also buy one of those skinny breakers and move the wire from 6 to one side of a skinny breaker.
You can make the connections between the outlets either in the outlet box (respect fill limits of course) or a separate junction box, but not in the panel.
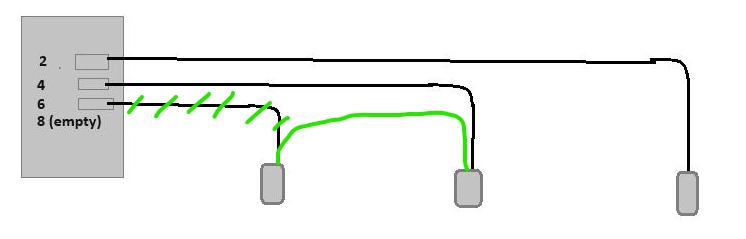
Curtis73 (Forum Supporter) said:
Part of me wants to paint it purple and put a big googly-eye on the front. That way, I can call it the one-eyed, one-door, frying, purple powdercoater.

Needs a Han Solo (or Curtis) embossed on the front
Ok now that you have it enclosed. I wish I'd have seen this earlier. The way you have the wires run will cause a problem in the future. Even if they are high temp wiring. Being compressed between the metal box and the metal studs will cause them to eventually fail. Should have just ran then straight out and piped them on the outside in conduit. Just my $.02 of 35 plus years of playing the part of a commercial/service electrician.
Other than that it looks about how I imaged how I'm going to build one myself.
In reply to stafford1500 :
Yesssss!
In reply to brad131a4 (Forum Supporter) :
I suppose it's not too late for that but that would be a truckload of work and ordering more wire. Glad I have a good ground :D
I guess we'll see how long they last.
In reply to 93gsxturbo :
I have seen it with two wires on one breaker before, but that doesn't mean it's right. I did speak with a friend last night about it. I knew he did electrical stuff but I didn't know he was an actual, licensed electrician before. He mentioned that on the back or bottom of the breaker it will tell you the max number of conductors permissable on the breaker. It has to do with how the lug/clamp is engineered. As long as you have the same gauge (and same type, like solid/solid or stranded/stranded), the breaker will tell you if you're allowed to put more than one on the pole. If the lug is designed in such a way that it only really clamps on one side, then multiple conductors would be a no-no.
The good news is (if I'm allowed two conductors on that one breaker), the two loads I would be supplying on it are 5A for the radiant gas heater and 11A for the radial arm saw - which I'm likely ditching anyway because it rarely gets used. I think I've used it a dozen times in 10 years.
If I'm not allowed multiple conductors on one, the easy button is a skinny 2-throw, but I'm trying to avoid expense where I can, and breakers are kinda pricey.
gsettle
New Reader
12/9/23 4:09 p.m.
So, when are you gonna coat the roof rack?
If you happen to have a SquareD QO panel. The lugs are able to accept two wires under the screw. There are plenty of 240/120 transformers that you could use in the box. Just come off the main lugs of the contactor over to the transformer. If you really want to you can set a fuse block in there as well and fuse it down to ten amps for safety sake.
gsettle said:
So, when are you gonna coat the roof rack?
Hopefully before I die. Welcome to my life. If all goes well, within the month.
It's officially done. New 50A breaker installed to a 6-50 outlet. Making a new label for the load panel and I'll be ready to test.
... but I'll wait until tomorrow when co-workers are around to hold a second fire extinguisher.
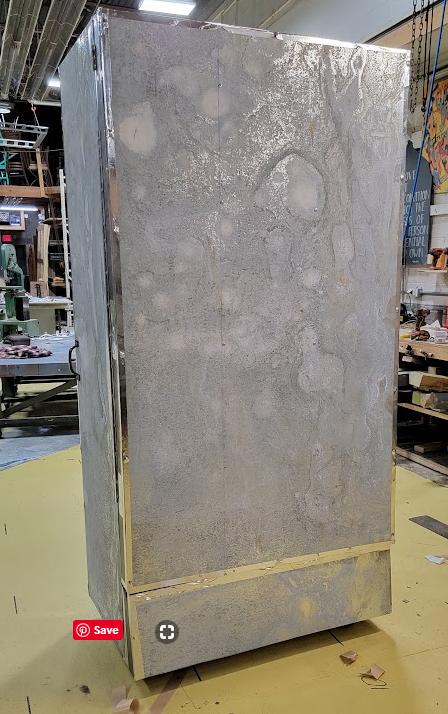
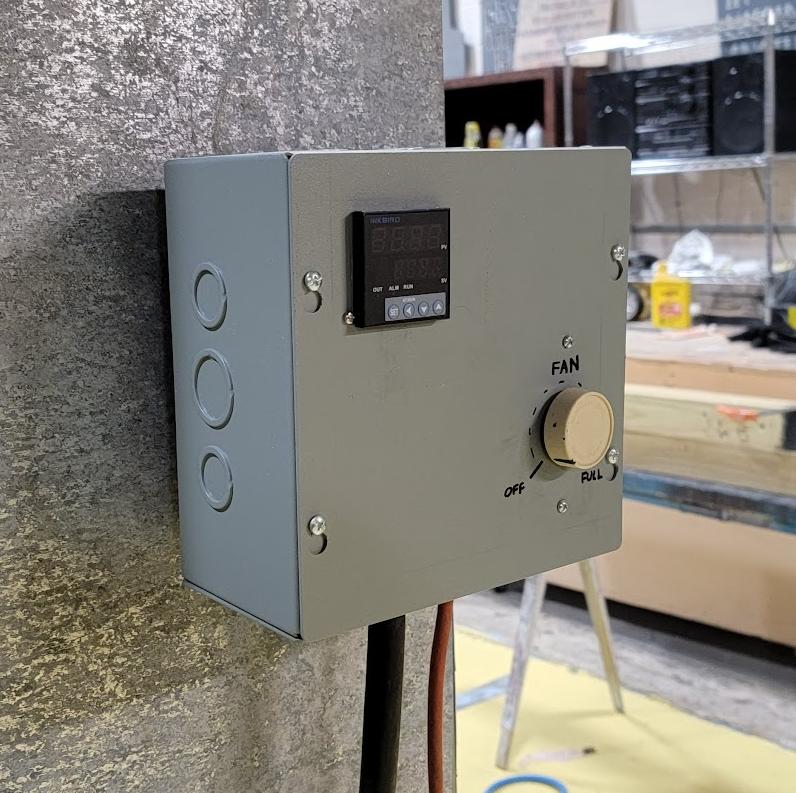
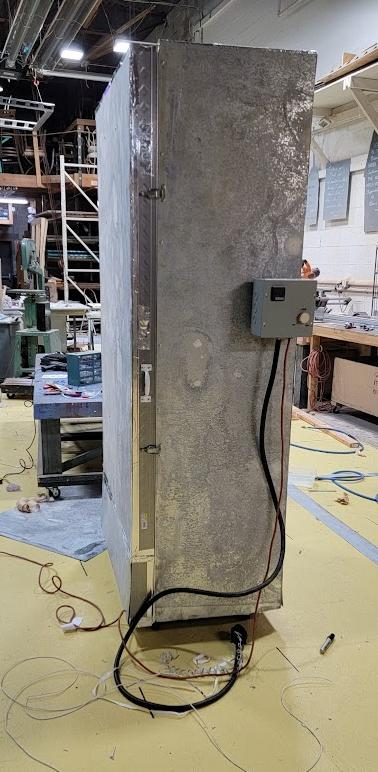
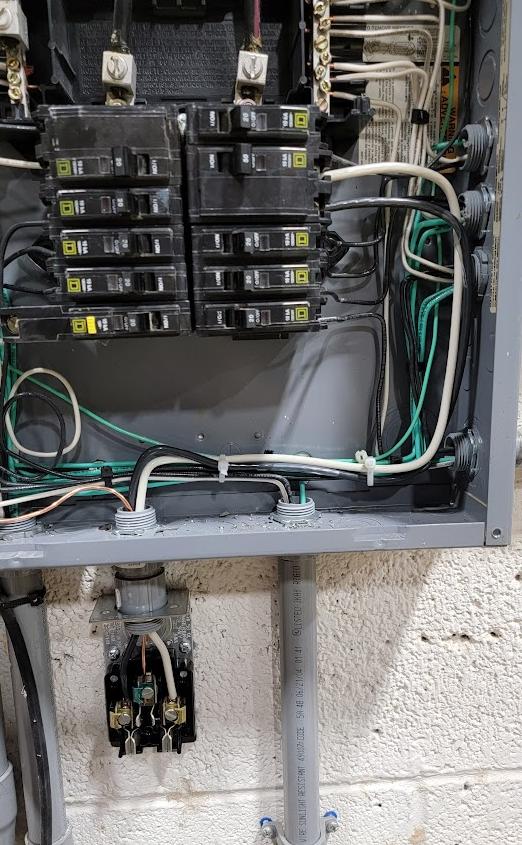
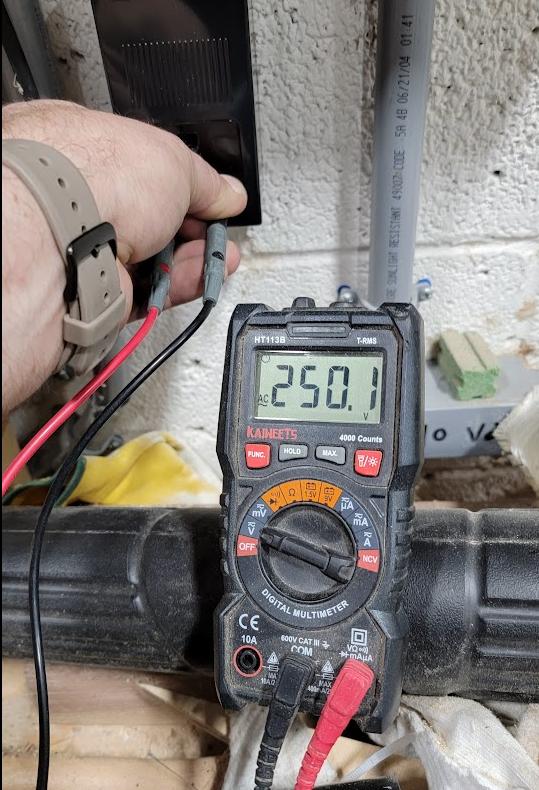

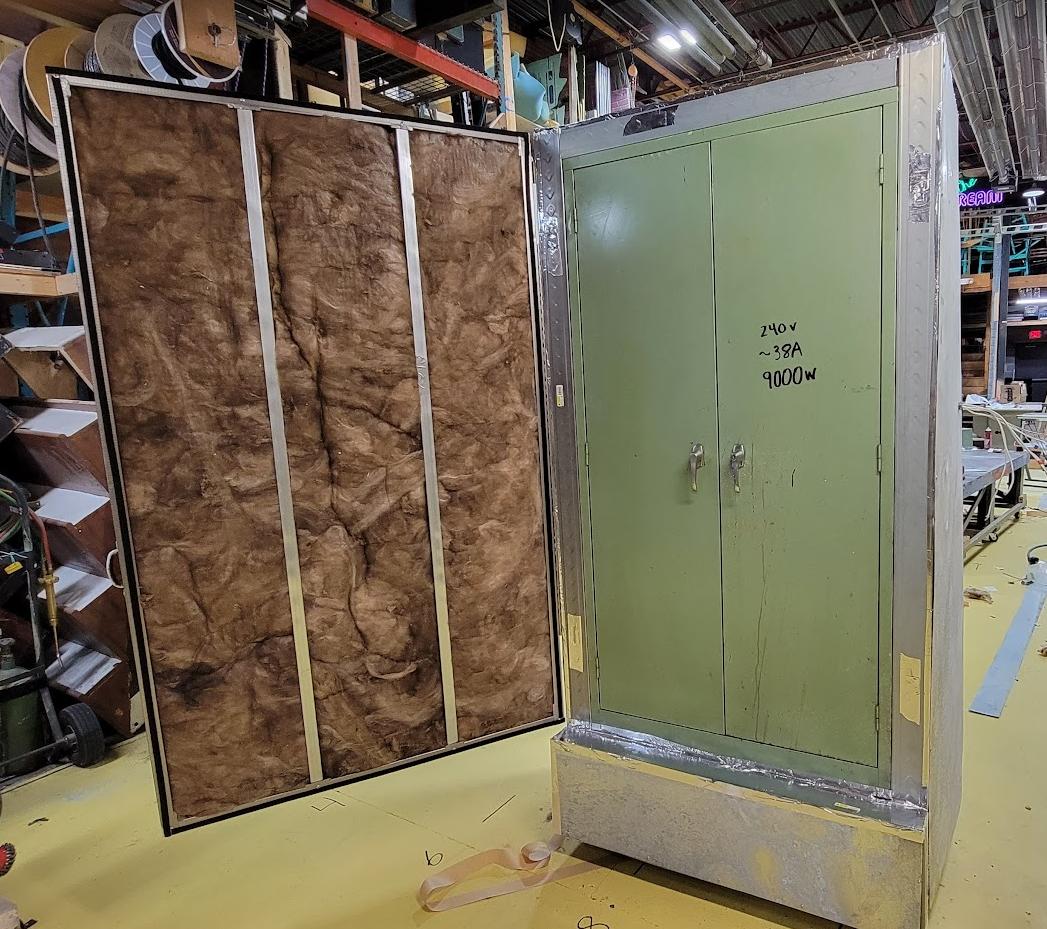
IT WORKS!
At first, I realized I had the polarity reversed on the thermocouple. Once I fixed that, it worked flawlessly. Even though it was a very windy 40-degree day outside, it got to 400 degrees in 20 minutes. Outside skin (thanks to the wind, I'm sure) never got hot. The seam near the door where it meets the cabinet was warm, but I could leave my hand on it indefinitely.
Smoke was noticeable, but not terrible. I will have to move the circulation fan (if it isn't dead). Since it was on the bottom of the oven, it was close enough to get pretty fried by radiant heat from the center burner. I suppose I'll move it up top and deal with the potential loss of space.
The other thing I noticed was that there is definitely enough thermal mass - likely from just the big quantities of steel in the walls. The PID would take it to 400, shut of the relay, and it would continue to 420 or so, and it very slowly came down. Maybe 15 minutes until it had to kick on again. When it does kick back on, it rapid cycles the burners to gently keep it around the same temp instead of just leaving it on.
To say I'm happy is an understatement. PID worked like it should, insulation worked like it should, I'm stoked.