Where I work we need to be able to precisely uncut thin sheet metal without bending the end and the end must be a clean cut so both a sheet metal shear or plasma cutter are not really viable solutions. We have been getting pieces EDM cut but that is expensive and having an inhouse capability would be nice.
So water jet or laser cutter which would provide the most cost effective solution for us. Or is there another technology that I should look into. I have a feeling laser is going to be much cheaper for our thicknesses of material but from what I have read water jet is more accurate.
Screen print and acid etch.
That's how they make thin metal parts for the model industry.
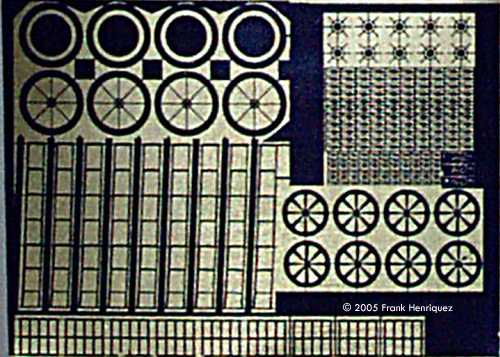
It would probably depend on how thin you are talking.
I would think accuracy would depend on the machine. I have had stuff waterjet cut and it was very accurate. They charge by the hour. Why not take your cad work and material to a local water jet place and see what it looks like?
The good doctor is probably right. I have also had some stuff water jetted and Laser cut. I like the Laser much better but it was also done on a machine that is several million dollars. The water jet was done on an industrial unit but not nearly the same caliber as the laser. Funny thing is that the water jet cost more in the end but that is mostly do to quantity breaks. How many parts you running?
There's a few moving parts in the deceision. What's the material, how intricate are the parts, what are the tolerances, and how many are you making? I designed a product made of 22 gauge Galvalume steel which is formed into U channels about 2x4" in lengths from about 16" to 64". Ideally it would be run on a roll forming line with inline punching, but due to the finance structure of the projects it was being used on, they had to buy it on a by-job basis, which was never eneough volume to justify dedicated machinery and tooling.
So we had it laser cut and brake bent. This was fine for the runs of a few thousand parts per job, but relatively expensive. When the company was acquired by a large semiconductor silicon concern used to eking out tiny margins on huge volumes, they immediately committed to tolling a dedicated line at a roll form facility and building progressive stamping dies for the few parts that couldn't be roll formed. Cost dropped by 30%.
So if you're making super-finely detailed spoked wheel inserts for 1/32 scale cars out of .008" stainless, you're probably etching. Moderately complex steel or AL up to about 3/16" is a good fix for laser, and thick plate likes water jet.
fanfoy
HalfDork
10/2/14 7:54 p.m.
motomoron wrote:
So if you're making super-finely detailed spoked wheel inserts for 1/32 scale cars out of .008" stainless, you're probably etching. Moderately complex steel or AL up to about 3/16" is a good fix for laser, and thick plate likes water jet.
Yeah this.
Like others have said, accuracy is more machine than process dependent.
What you do with the part after it is cut can also have an influence. For example, a lot of steel grades will harden at the cut line when they are being laser cut, so if you want to ream a hole that was laser cut, you will wear out the reamer really fast.
1008 steel basically in the .010"-.025" range.
I'd vote laser too - I used to work in the laser cutting industry. A laser cutter may have a higher buy in (although you don't need a 4 kW beast to rip through 0.025" steel), but fairly low running costs and a very high feed rate that'll let you cut more parts in an hour.
I spent a bunch I time with some large water jets used to strip aero parts and will say they have a lot of moving parts and are prone to breakage later in their life. If
Laser works, get it. I can see them being as much of a pain as these water jets.
When I was in the sign bidness we had a laser etcher that had a working surface about 2'x2'. It cost about $5k new eight or ten years ago. It could be rigged with an upgraded laser to cut metal as thick as you are talking for another grand or so (IIRC). Buy in on small cutting lasers for thinner applications has dropped significantly since then. I'd certainly be looking for some laser suppliers to talk to or a tradeshow to go to.