Despite the heavier weight and similar size, an upright TKX is easier to install than a tilted T5 by a mile. Whenever I can actually get it to fit, it should be able to go in without any extra hands.
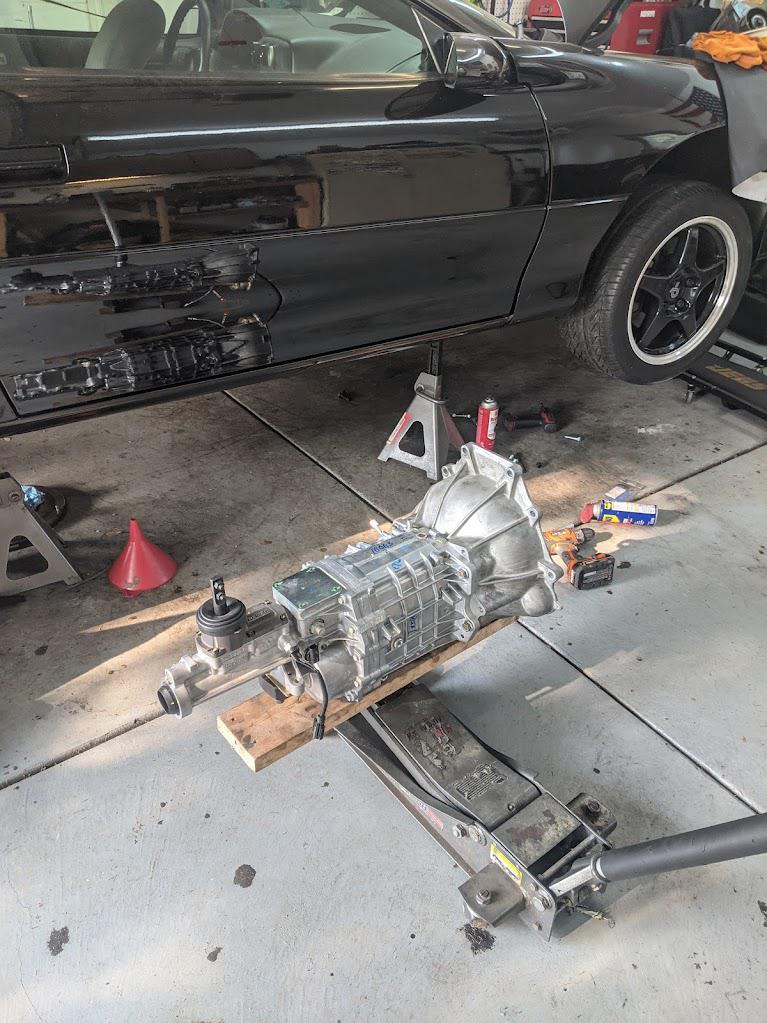
But it won't fit just yet. The shifter is too far forward.
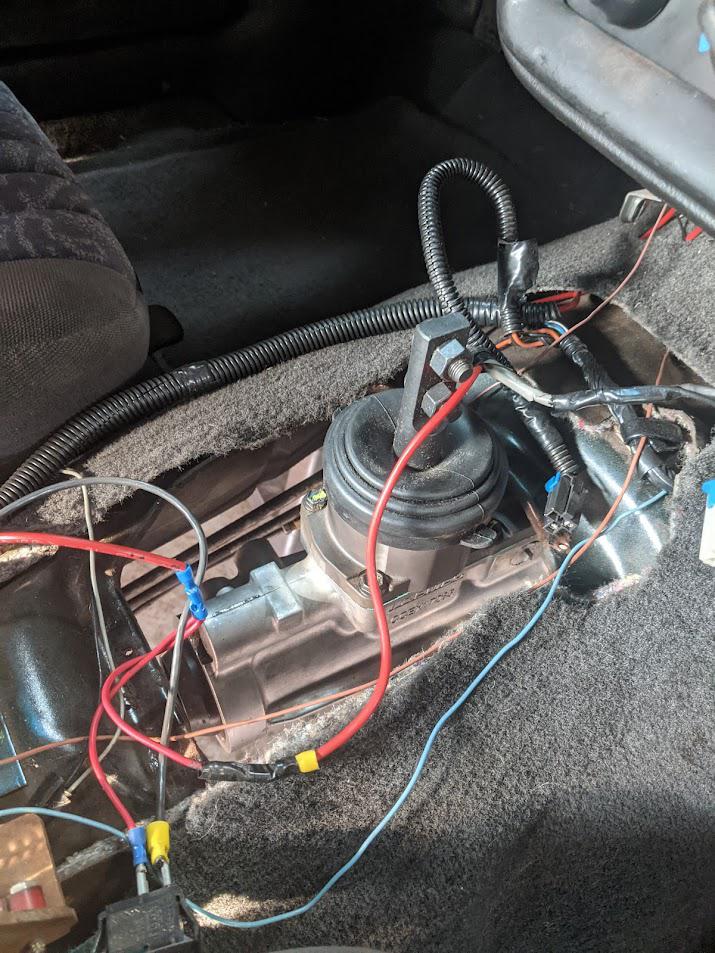
and the mid-shift block-off plate hits the bottom of the body brace.
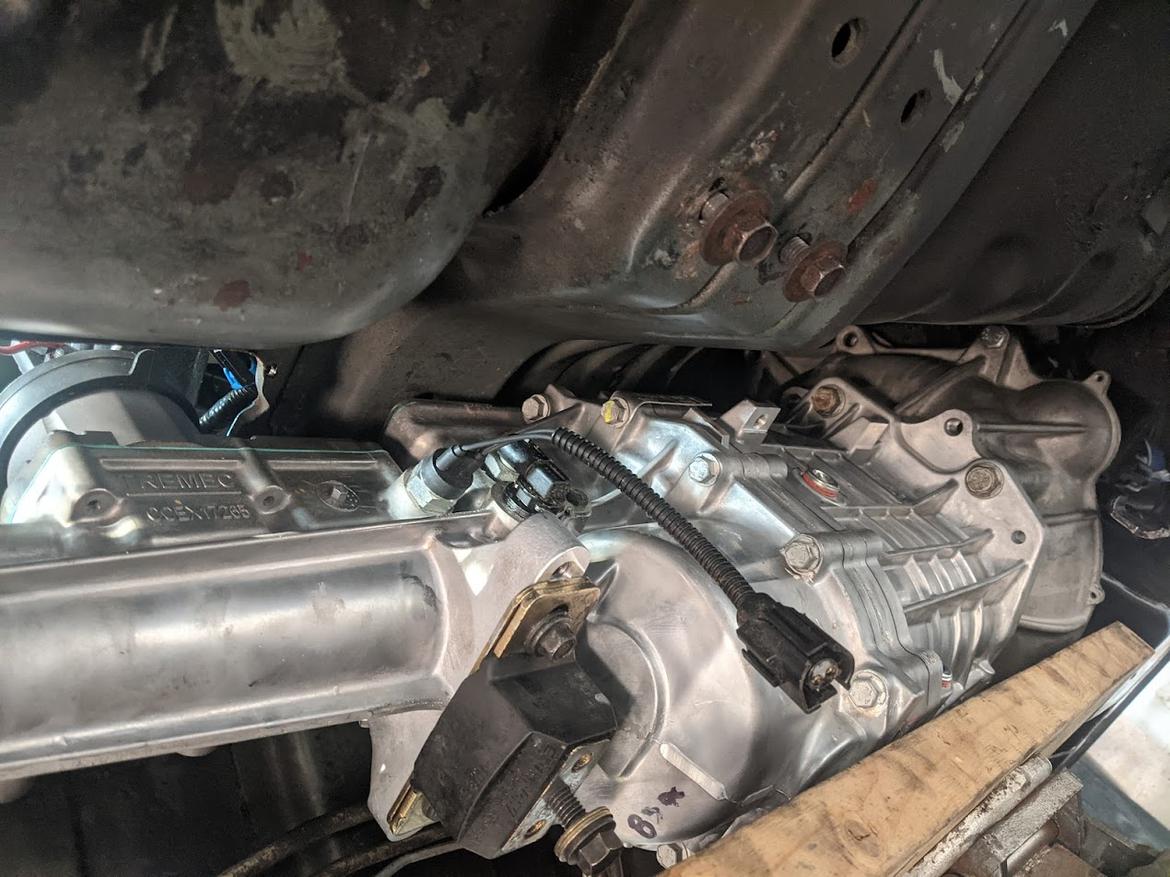
However, it's really close! I actually had one bolt threaded in. I'm going to start by cutting a little notch in the shifter hole. I don't really want to cut the cross brace if I can get away with just beating on it with a hammer. While the anticipation was killing me, (still is) I needed to force myself to complete some other stuff while it was still easy.
Out came the gooey driver side motor mount, and in went a poly insert. I didn't take a lot of pictures because I was hot and incredibly dirty. By the way, it's probably easier to do a motor mount with the trans installed because the trans connection to the cross-member might help keep everything aligned. Oh well! It's done now.
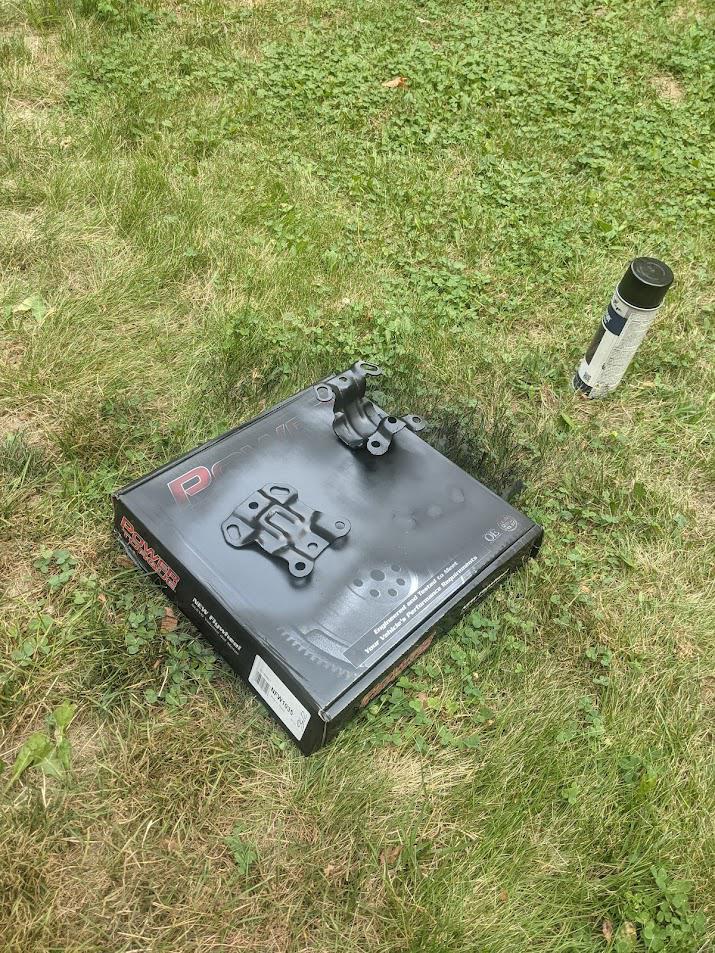
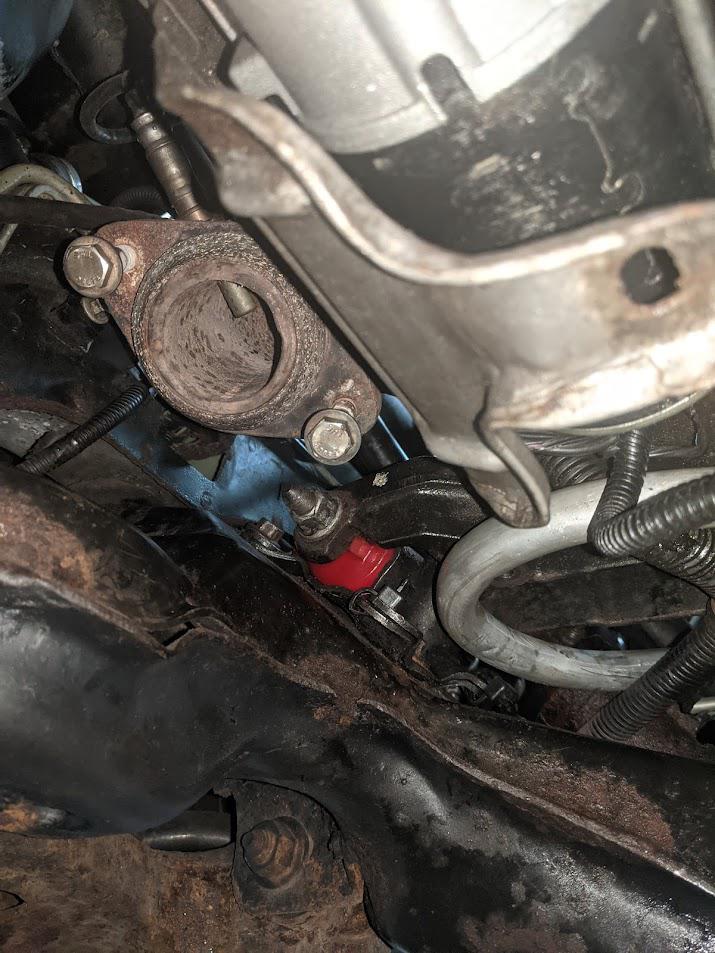
What a difference that made! I knew it would be substantial after I pulled the disintegrated rubber apart, but I thought that the looseness in the engine was mostly from not having a third anchor at the transmission. There's hardly any movement to be made by hand now. While this should be great for putting the power down, I hope I don't regret it in the form of a harsh ride. We'll see.
Not pictured is the flywheel and clutch being installed once and for all. I managed to find the wrong torque spec for my pressure plate and snapped a bolt. I couldn't extract it either, and damaged the flywheel. I got a new flywheel, drilled it for the bigger ARP bolts, started installing it, and stripped another hole int he crank. *eye quivers* I pulled the flywheel again, heli-coiled the crank, crossed my fingers, successfully torqued the flywheel, and installed the clutch with the correct torque spec.
NOW I'm finally ready to start cutting the car up and do another test fit, but I'm going on vacation tomorrow. The anticipation is just going to have to eat me alive for the next week. lol