Nebraska ... you're overthinking it, nothing wrong with that. My suggestion is go ahead and do it with basic coolant tubing and fittings (no valves, wiring nor thermostats) then experiment with those. Use a temp sensor to switch the pup/fan when the heads are half warmed up so no thermal shock.
I have a first gen Camaro, 350 mild cam daily driver, has had radiator under the trunk for 4 years and 10k miles.
Fabricated coolant log manifold in 1.5" x 16g al tubing that replaces the SBC waterpump, 90^ radiator hose bend down to al tubing past the steering box then follows chassis rail over axle to factory brass radiator with relocated inlet/outlets. Passenger side returns over axle to DaviesCraig EWP 150 under the rear seat void. Out of there towards the propshaft and along past trans, fabbed a heat exchanger using in-radiator GM type trans cooler element inside a 2" brass tube, then up beside headers to intake manifold thermostat housing WITH NO THERMOSTAT.
All al tube sections are grounded to prevent galvanic corrosion.
Some bends are rubber OE type 1.5" bends to provide flex. Underbody brackets are rubber flex mounts so no stress in tubing.
Note, I have sidepipes from front wheels to rear wheels. With undercar exhaust there would not be enough space to package the al tubing .
DaviesCraig electronic fan controller switches radiator fan at preset temp (110*) at cyl head. Then 10 sec later switches the EWP.
So ... the coolant system is totally open, no valves, no thermostats. Coolant warms up in similar time to OE. You can cover the grill opening with 1/8" clear polycarb sheet for fuel economy.
Our climate here in Melbourne Australia is temperate, similar to Northern CA. Mid 50s in winter to 80s in summer. Low humidity.
HOWEVER ... airflow in my application is restricted by lower than stock ride height, and the fact that I didn't want to cut ducting into bodywork.
Raised trunk floor approx 4" is still barely enough to package the radiator and electric fan (2.5" is thinnest I can source), the fan is pulling air from above radiator and blowing towards the ground. The crossflow radiator is in the original gas tank space, mostly horizontal but tilted down 3" at front and tight to floor at rear edge. I have al ducting attached to the rear axle tubes to deflect air upward then sealed to a floor-mounted shroud with surprisingly effective sliding seals. Fabbed al framework holds radiator and looks like a diffuser from the side/rear.
From LOTS of experimentation (I have 7 digital temp gauges and 3 cameras in the car), airflow under the car is ok up to 80 kph (50 freedom units) but after that it is too turbulent to flow up behind the axle and into the ducting. Driveable for 45 minutes before it heat-soaks. Tire squirt also a factor, screwing the pooch. Bumper-to-bumper traffic really needs those rubber flaps in a fan shroud, but my situation cannot have a shroud cos I need airflow, and rubber flaps don't work laying down.
DO NOT RELY ON AL TUBING TO DISSIPATE HEAT ON THE RUN FROM THE ENGINE TO THE RADIATOR ... IT WILL NOT!
NEVER use an electric fan in front of the radiator. Efficiency takes a dive.
As a result, my car is not driveable at ambient temps over 90*. (coincidentally, having aluminum interior, no carpet, no a/c, my body doesn't WANT to drive over 90* so no downside effectively).
Would I do it again??? Only if I had more/better incoming airflow, maybe stand the radiator up in a rear mount installation.
Probably HAVE to go with side inlet ducting similar current Corvette, and shrouded outlet ducts exiting between taillamps low pressure zone.
Reason I did it??
- Covid lockdown boredom, I had raised the trunk floor for this project when I built the car 20 years ago. 48/52 weight distrubution with driver and half tank fuel. Noticeable on turn-in and speed humps, even at suburban speeds.
- Because RACECAR.
Jim Grant
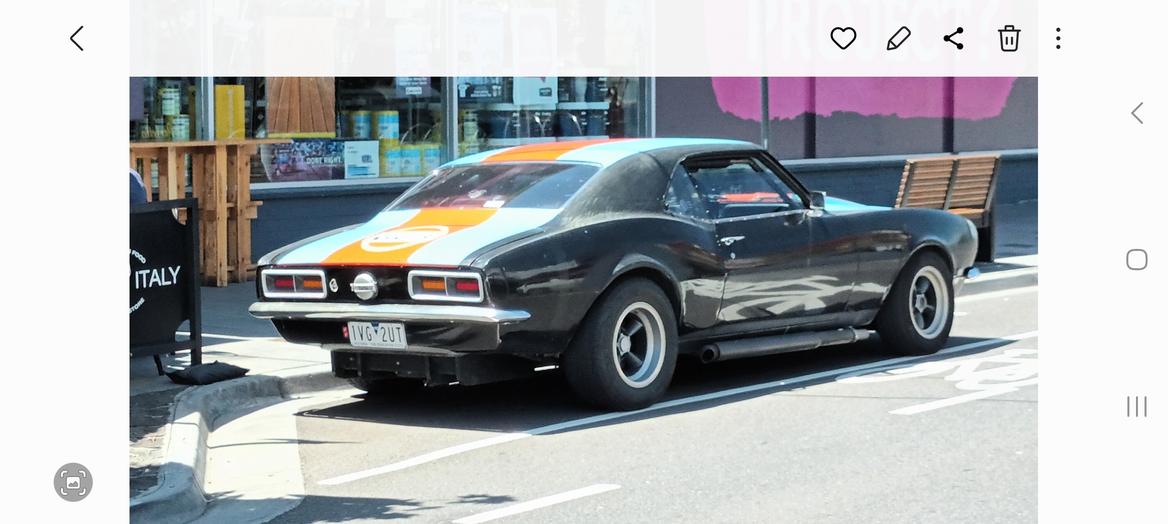
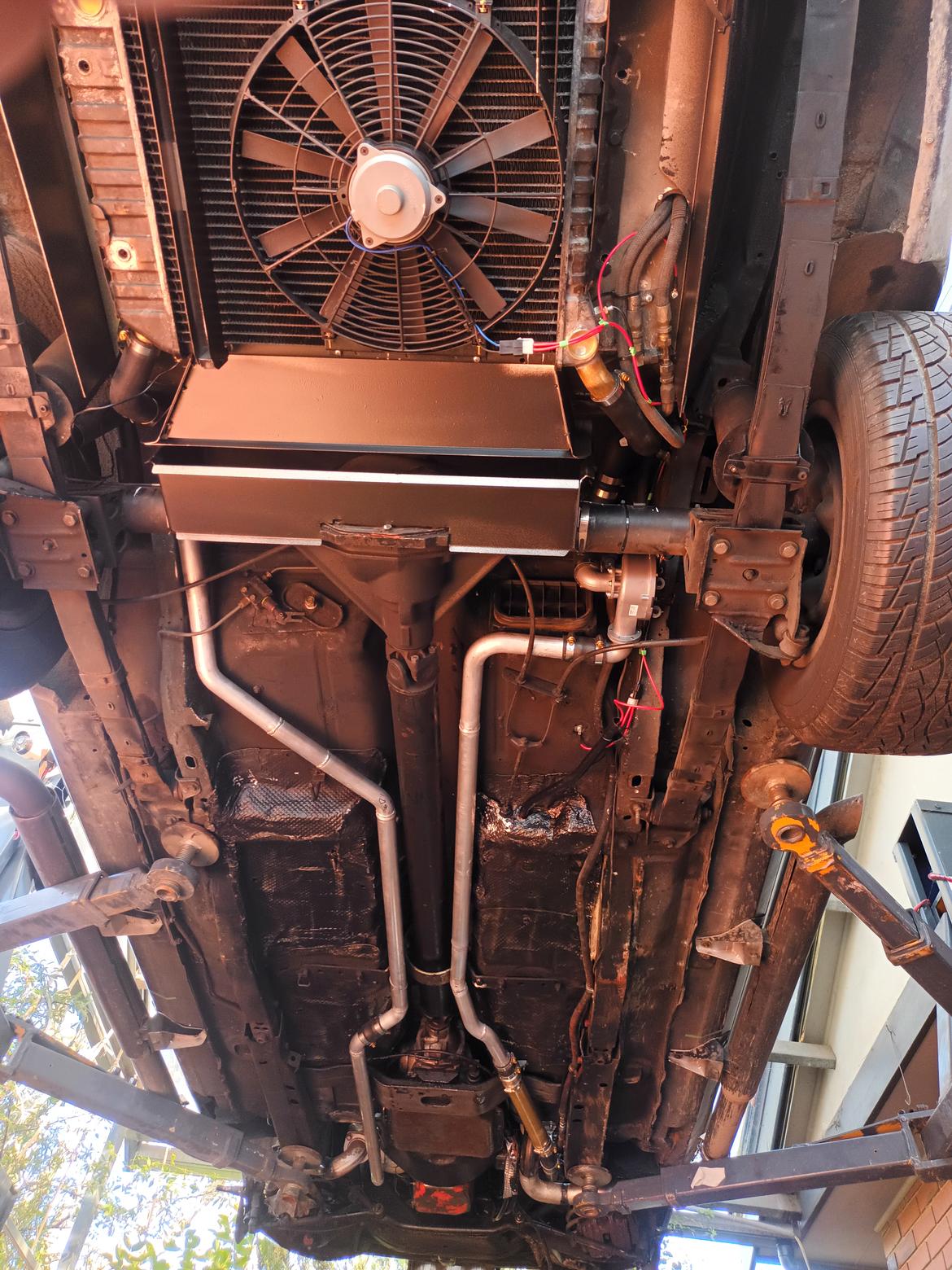
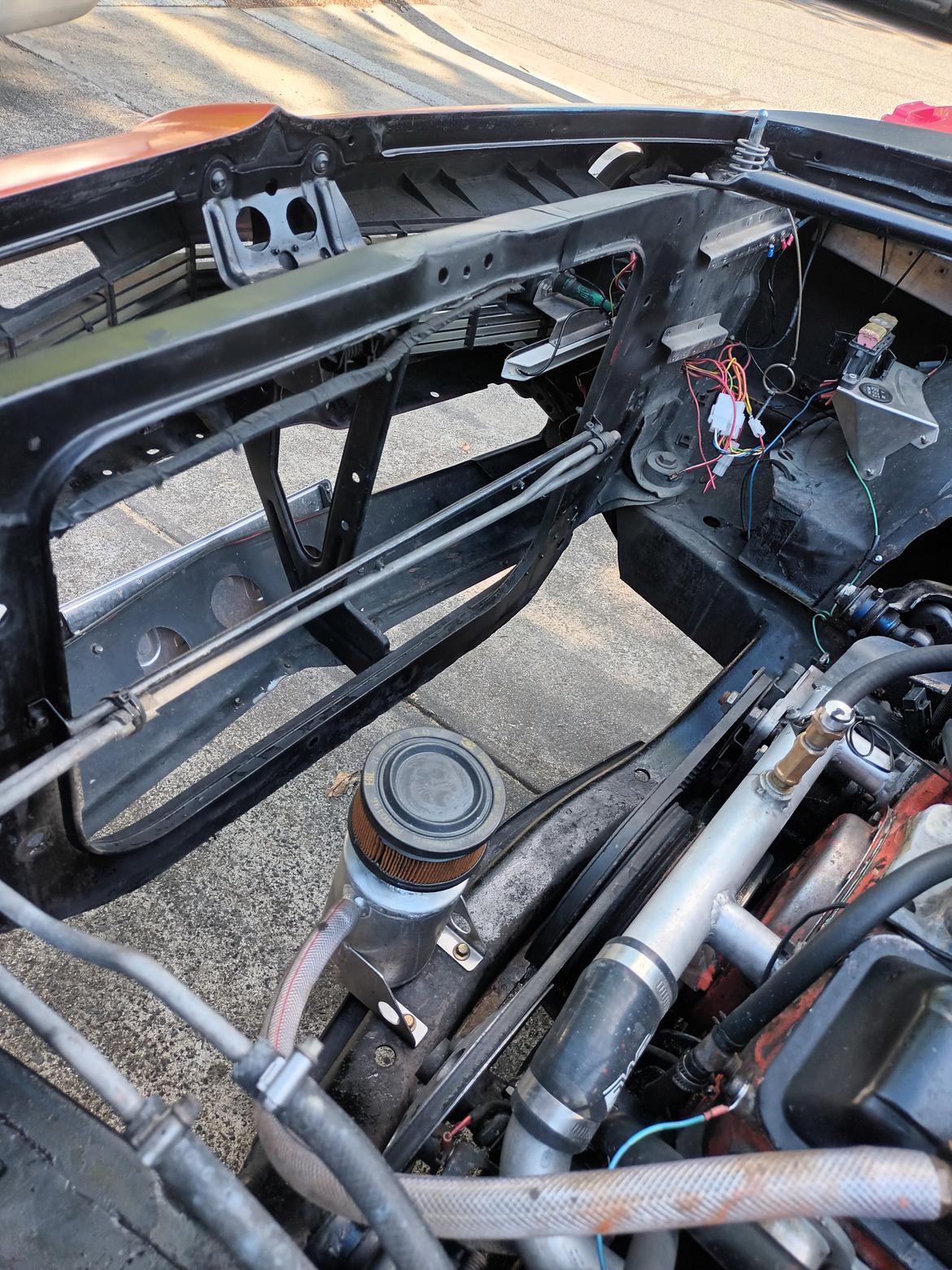