SkinnyG
SuperDork
3/26/15 2:57 p.m.
Had some conflicts with the exhaust. Things moved and/or settled, and the mufflers ended up being placed too high - this would require clearancing the floor, and the exhaust heat might set the seat on fire.
So I decided to cut out the frame through-rings for the exhaust (which had broken my corded drill chuck and cordless drill speed switch) and make them bigger. Luckily, I now had a good source for large diameter pipe. I'm sure the kids won't notice.
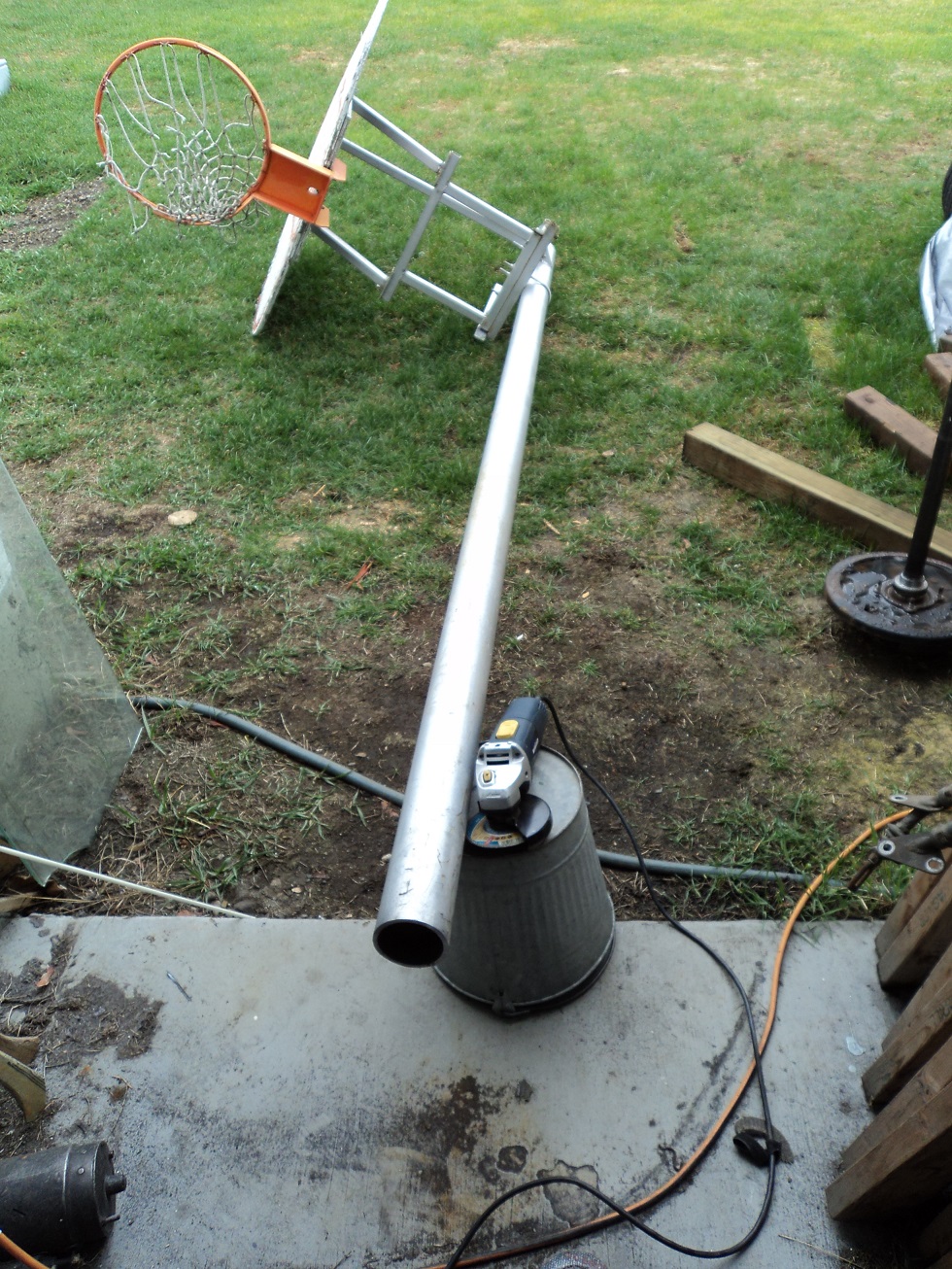
Instead of destroying more drills, I hacked them out with The Death Wheel, and welded in new.

Now I have good clearance between the floor and mufflers. Yay!
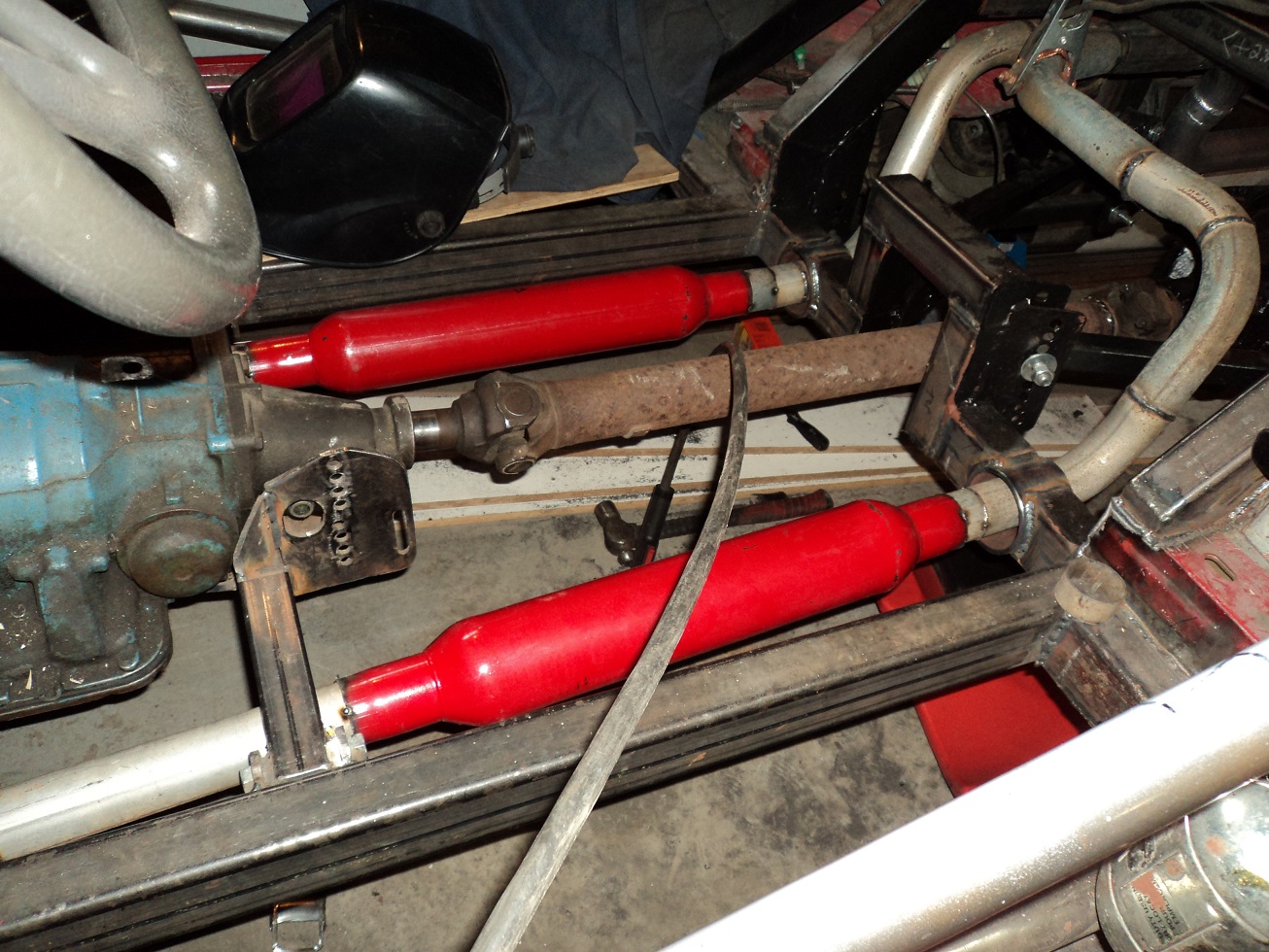
So it's better - but I'm not further ahead.
easier to fix and weld up things now rather then later when the floor is installed. You don't want to have flanges for separating the exhaust/servicing later on down the road? looks like you might run into troubles with that.
Death wheel? What is that? I must own one.
NOHOME
UltraDork
3/26/15 7:10 p.m.
Dusterbd13 wrote:
Death wheel? What is that? I must own one.
Real "Death Wheels" don't have guards!
SkinnyG
SuperDork
3/26/15 8:30 p.m.
Fake Death Wheel, then. I'm too chicken to remove the guard in most cases. But I did remove the extra handle, and the trigger is a "stay on forever" style that keeps going even after you've died. This is why we wear a face shield and gloves, children. Went through two of these:

Also got the brake master re-installed, along with the combination valve. I can't remember where I put the brake lines to connect the two.

crazycanadian wrote:
You don't want to have flanges for separating the exhaust/servicing later on down the road? looks like you might run into troubles with that.
Right now, it's trying to stay under budget. The headers still disconnect at the collectors. If I'm going in there again, it will be (hopefully) much later to replace the blown out glasspacks with something less budge-constrained.
Not sure how best to separate the exhaust, now that I think about it. I can't think of anything that would fit through the metal rings. I could do a slip joint with some method to squeeze it, but.... Hmmm. How big are v-bands?
On the other hand, it should be possible to pull the trans and the axle without pulling the exhaust, so it might be ok. I hope.
SkinnyG
SuperDork
3/26/15 9:10 p.m.

Princess Auto has a keyless chuck to turn your 3/8" drill into a 1/2" drill. Around $15 CDN as of this writing. Seems to work dandy, and the Hitachi lives to fight another day.
SkinnyG
SuperDork
3/28/15 3:16 p.m.
Patterns. I took this picture mainly to show my students that "The Old Man" uses cardboard to shape the sheet metal.
I figure if I do enough of these, they might be inspired to believe that it is easier to make it fit in cardboard before they waste their time and money in metal. "If you can't make it out of cardboard, you won't be able to make it out of metal." I know, I know, "the Old Man don't know nuthin." They'll learn.

Meanwhile, cardboard patterns, sheet metal, and getting some bead roller practice. Yes, I changed my mind on the patch on the right. "Make your big pieces first, that way when you screw up - they become your smaller pieces."


SkinnyG
SuperDork
3/29/15 10:44 p.m.
Patch panel for the left side of the rear frame kick up. Fun with the bead roller, rolling an inset around the perimeter, and raised beads through the center.


Rust on the wheel well actually goes right through - it gets patched later on. Also drilled holes to help run brake and fuel lines from the front to the back without getting too close to the exhaust pipes. Hard to figure out. No pictures on that yet.
SkinnyG
SuperDork
3/30/15 11:51 p.m.
Notice anything new?

If you said "I see that you have finished plumbing the front brakes," you'd be right!
SkinnyG
SuperDork
4/4/15 11:21 p.m.
crazycanadian wrote: You don't want to have flanges for separating the exhaust/servicing later on down the road? looks like you might run into troubles with that.
You were so right. And it hasn't even been down the road yet. I have run into a snag.
I went to remove the transmission crossmember so I could cut off the now unused Firebird Torque-Arm mount, and found I could not remove the crossmember. Or at least, I certainly would not be able to once the floor is in the car. So.... I need to figure out something that is easier to deal with.

3 bolt header flanges bolts and gaskets shouldn't be to pricey. I have been ripped off with kits before. So I get generic flanges and gaskets.
SkinnyG
SuperDork
4/6/15 12:00 a.m.
After a bit of thinking, this is where I am. Crossmember needs to be easy to remove. Previously, it was designed very robust to deal with the Firebird torque arm, which I am no longer using. This is a bit less robust, but should work fine.

Cool thing: this is all steel I found in my back yard. The ends of the cross member will be sliced at the ends to fit the "ears," which will be bolted to the tabs welded to the frame. Good idea on the exhaust. I'll do something like that when I cross that bridge in the future.
NOHOME
UltraDork
4/6/15 6:22 a.m.
SkinnyG wrote:
crazycanadian wrote:
You don't want to have flanges for separating the exhaust/servicing later on down the road? looks like you might run into troubles with that.
You were so right. And it hasn't even been down the road yet.
I have run into a snag.
I went to remove the transmission crossmember so I could cut off the now unused Firebird Torque-Arm mount, and found I could not remove the crossmember. Or at least, I certainly would not be able to once the floor is in the car.
So.... I need to figure out something that is easier to deal with.
If it does not mess with the budget, why not use the butt-join exhaust clamps?

Got the crossmember sorted out, and primed:

New tabs off the frame. Crossmember will bolt to the underside of the tabs. Not ideal, but neither is this project.
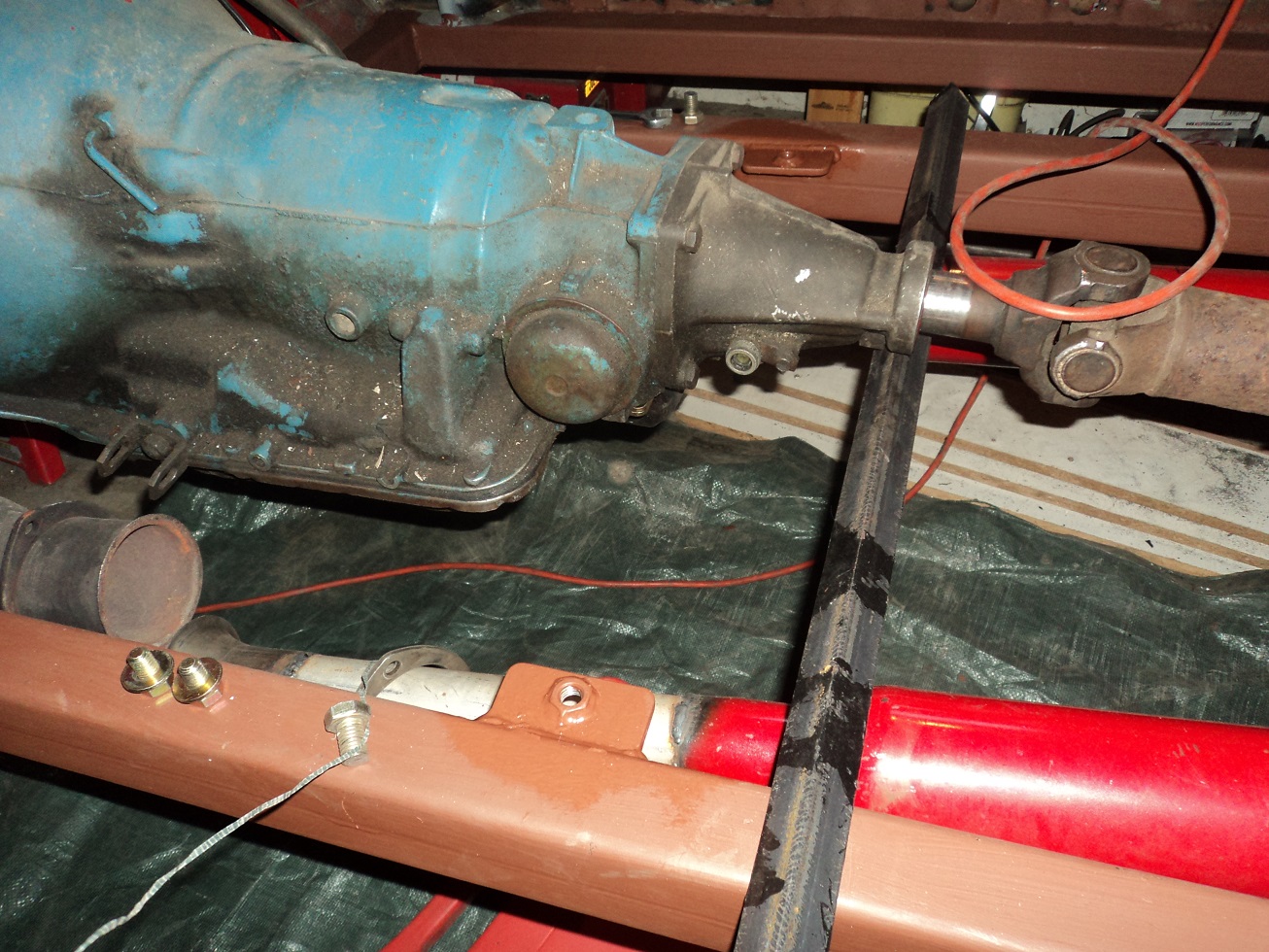
Also finished bead rolling and primering the patches on the rear sides. Also patched a rust hole in the left rear wheel well (seen in earlier pics).

The freezer still has quite a bit more life left in it. I might be able to make this work really well! 

SkinnyG
SuperDork
4/12/15 1:02 a.m.
I started working out how to build radiator tanks, and I think I've decided what the dimensions have to be. Not sure if I have the right aluminum at home or not - it was left over from the sheet of used aluminum I bought for the floor on The Lethal Locost.
Also finished cutting and folding the interior panel for behind the seat backs. Used the 3' sheet metal brake I fabricated last fall. Worked AWESOME!
I intended to bead roll something cool into the panel, but it seems I am not ready for that level of complexity. I wanted to emboss "FIENDISH", but then changed my mind to the Pontiac symbol, then decided to just do a perimeter shape and move on. Fun challenge too, because I didn't think about the limited reach of this bead roller.

Also tried rolling flames into some scrap, and I experimented with my tipping wheel and trying to figure this stuff out. I am a long way off. It's kind of fun getting lost in the garage for hours.
SkinnyG
SuperDork
4/12/15 11:02 p.m.
Back panel put in. It seems a bit "drummy." I'm thinking a couple of raised beads through the center might have reduced that. Too late now. Wait for a sale on Peel-n-Seal I guess.

Also working out rad tanks. That there is the core from a Ford Ranger that I got because a tank had split. Rad should fit under the hood easily, and not protrude below the bumper. I also have been enjoying a spot weld cutter, and removing old bracketry that is no longer needed.

Oh yes - the new and improved transmission crossmember - now actually removeable. Such a treat.

I recently spent some time with my friend Liam of Burr Fabrication (Armstrong), who helped me immensely in fabricating a gas tank, and gave me tips in welding my own rad tanks to the Ranger pickup core.
Today, I worked on the lower radiator tank (no pics - boring), and the lower rad house outlet. Lower water pump inlet is 1-7/8 diameter. That makes the circumference 5.89". I cut a strip from the same scrap aluminum I used for the tanks.
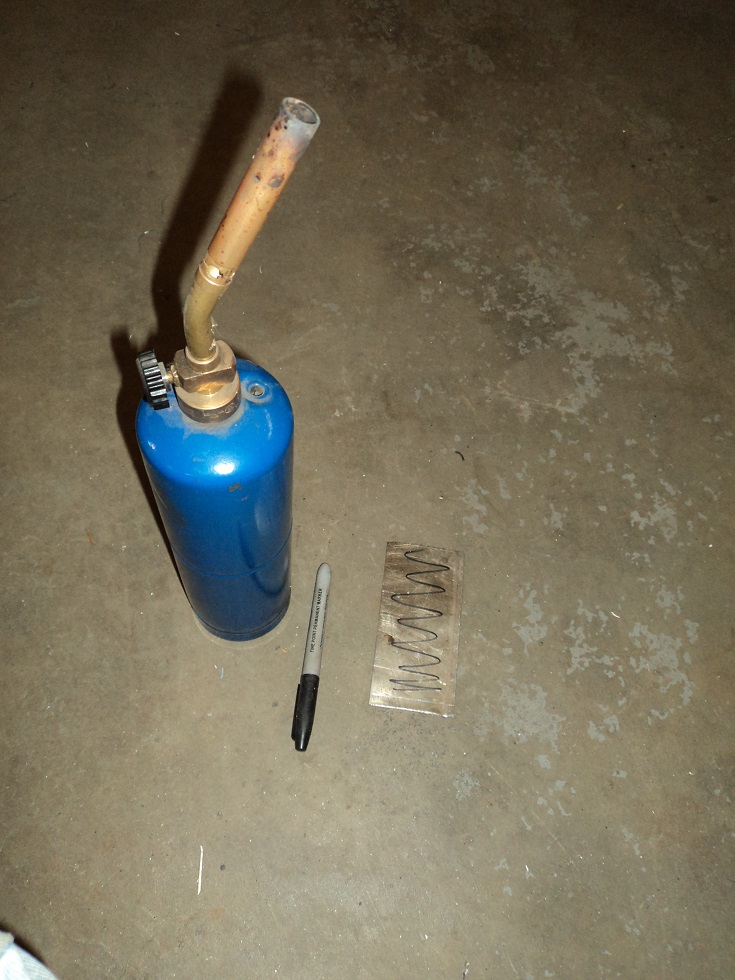
Anneal the aluminum by scribbling a Sharpie on the aluminum, then heat it with a torch until the ink is gone.
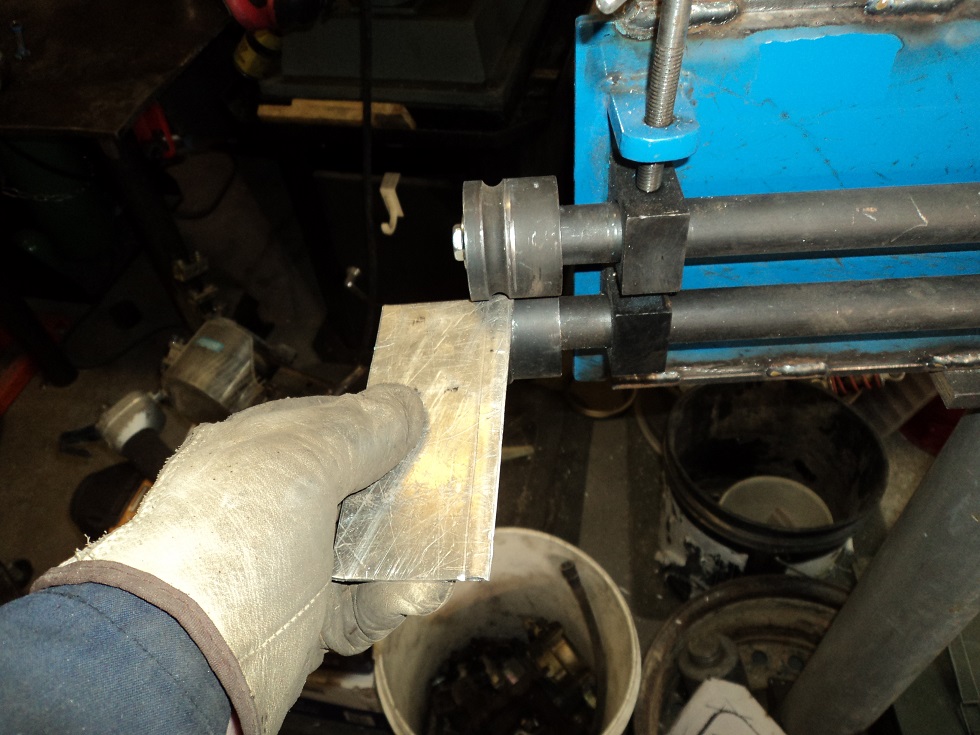
Then I ran one side of the sheet through the bead roller for a hose clamp antipoppinoffinator.
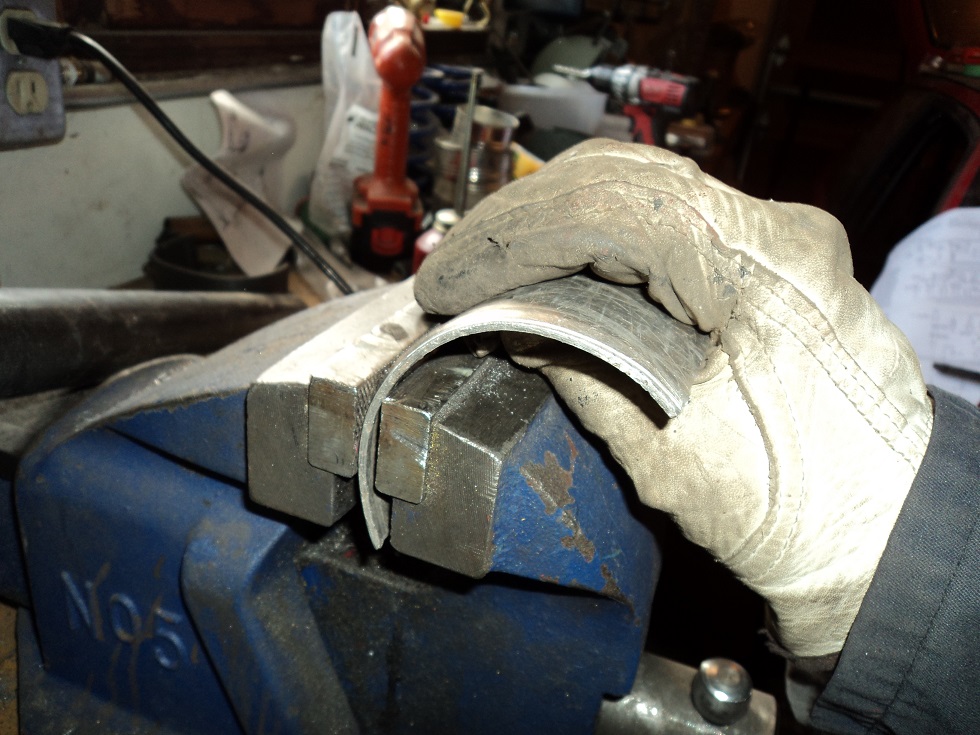
I started curving the sheet by bending it bit by bit by hand in my vise.
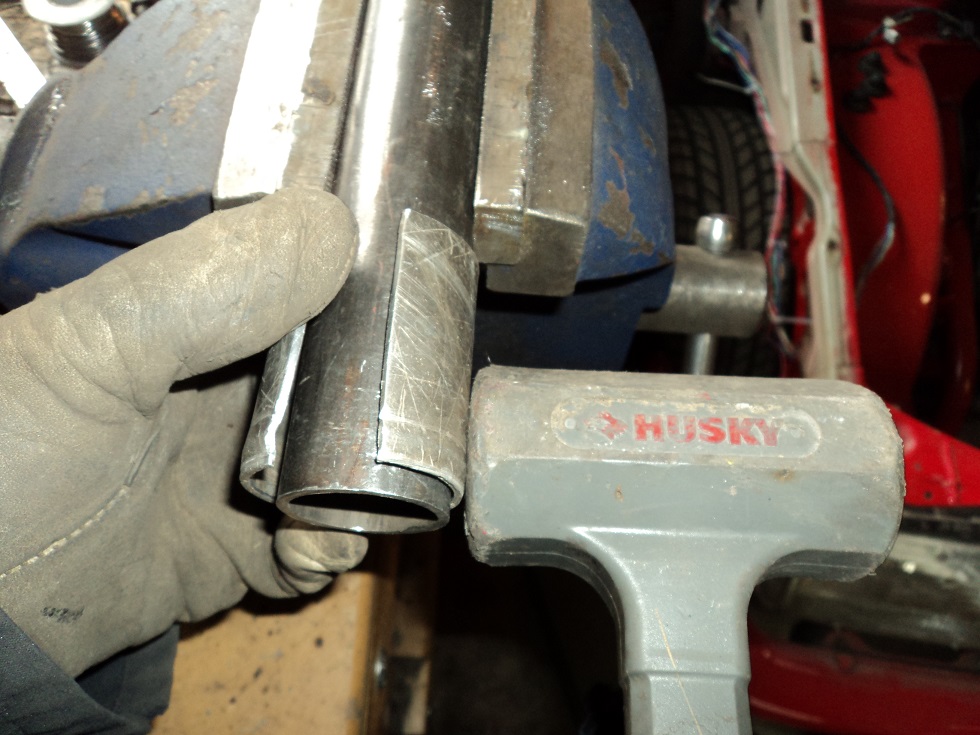
Then persuaded it into round using a dead-blow hammer around a piece of tubing.
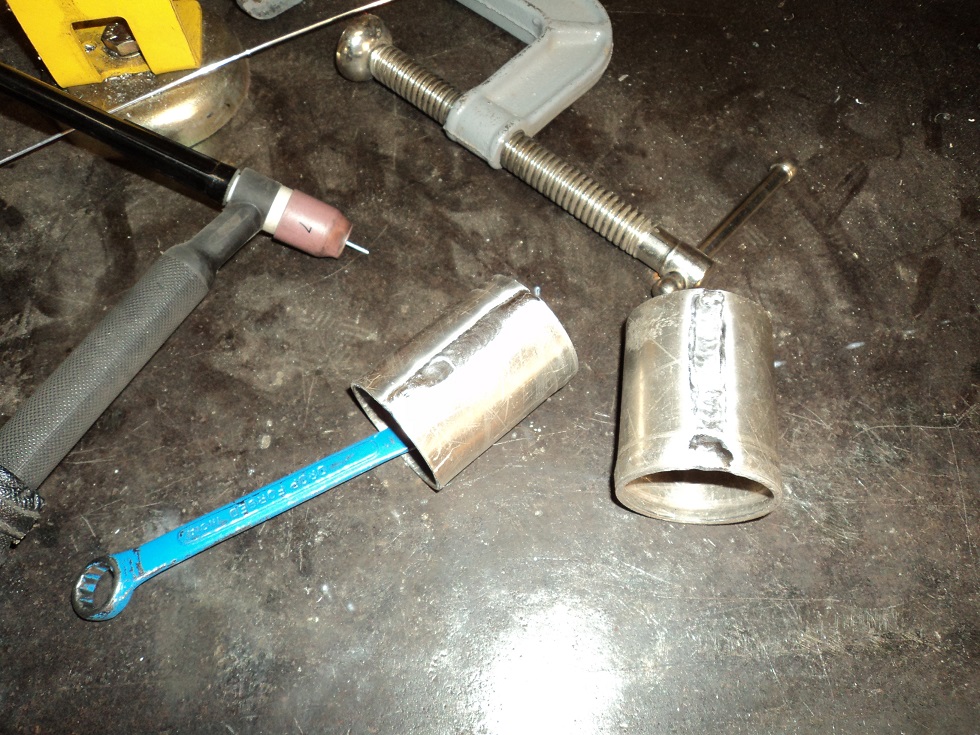
Then TIG welded the seam inside and out. Top hose inlet is there too.

The outlet is squished on one end to fit the tank. The hole was shaped with a carbide cutter on a die grinder. Spraying the cutter with WD40 keeps the cutter from bunging up with aluminum.

Magical TIG goodness.
I'll finish the top tank and hose inlet, flush the rad clean, then cap the ends.
f6sk
Reader
5/2/15 8:39 p.m.
very cool. I love reading your thread. Always something unique.
SkinnyG
SuperDork
5/3/15 12:50 a.m.
Attached the top tank, hose inlet and filler neck.

My fingers were cooking after this one.
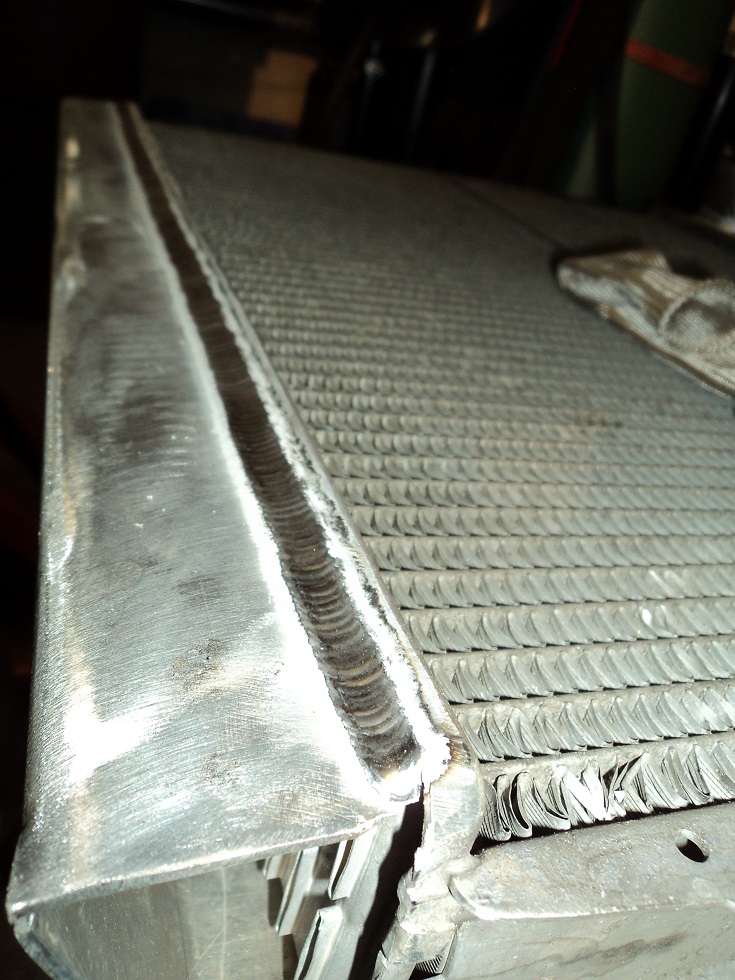
Basic weld bead, then another pass using the only the pulser to "wet" it together nicely.


I'll likely cap the tanks tomorrow, add a drain cock, and hopefully be done with the rad.
SkinnyG
SuperDork
5/3/15 12:56 a.m.

This what I started with, way back in July of last year.
Nice progress, I enjoy reading your thread and finding all the neat little tips and tricks
Got the tank sides done and capped, and drilled a hole for the soon-to-be-attached draincock.


Not much different than you have seen already. Working out how to mount it.
I have an idea on how to do the gas tank. Liam (Burr Fabrication) and I threw together a basic gas tank, currently not quite finished. The pretty welds are his.
I'm using the '88 Firebird fuel pickup, so the tank was made to suit. We built a basic sump, with a hole forward so fuel can get in, with a more difficult time getting out. I'm not worried about trap doors and maximum g's - I'll likely roll it long before fuel starvation becomes a problem.
Once I got home and my sub-conscience stewed on it for a while, I widened the hole and added a divider, so in a corner, the only way the fuel can get from one side of the tank to the other, is through the sump (shown).
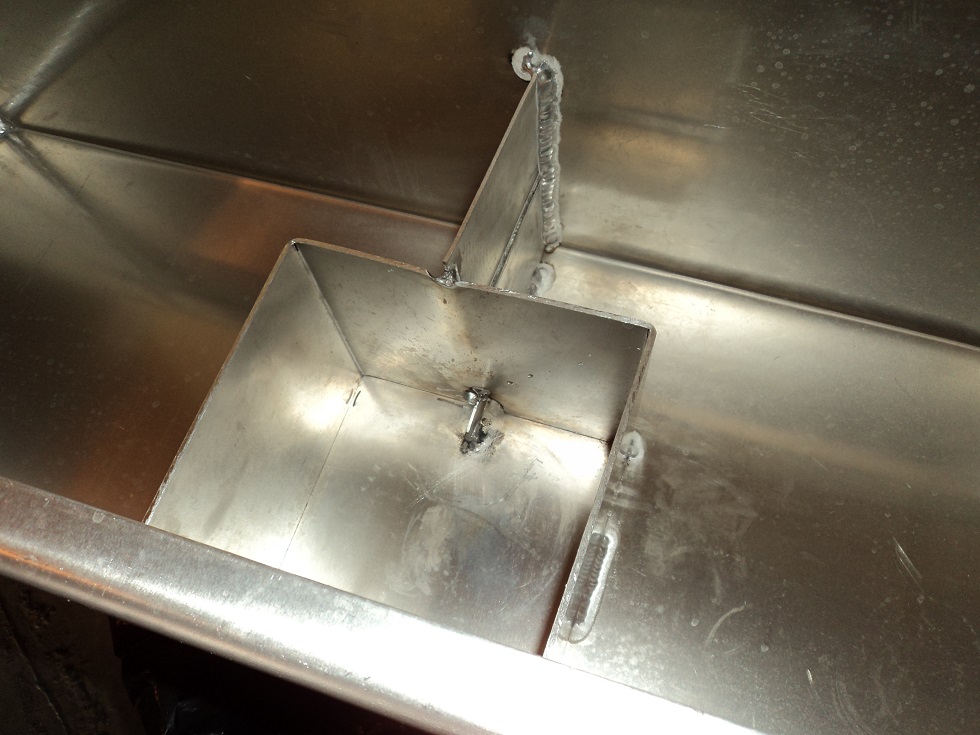
The top looks like this, with the pickup and o-ring sandwiched between a ring welded underneath, and a ring bolted through the top into it.

That might be as far as I go with it this weekend. Going to check on my building permit - it's been two months of waiting.....
SkinnyG
SuperDork
5/3/15 11:01 p.m.
Trimming the back hatch area to fit the tank. What's that bogging down my cutting disc??? Oh. That.

You don't fully own a project, until you've bled on it.