I started today by cutting a bunch of stuff off.
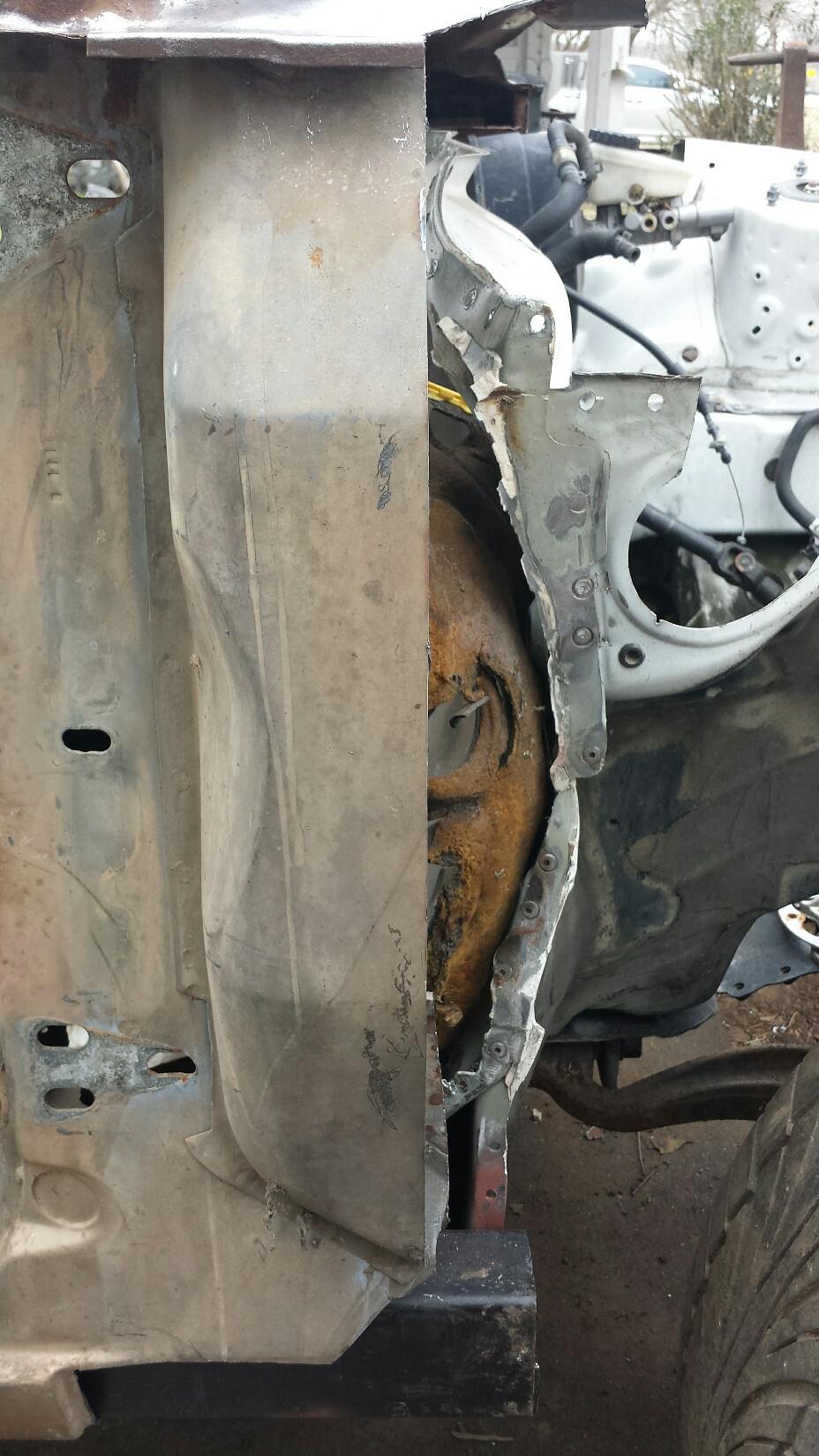
It never ceases to amaze me how close some of the parts off of these two chassis' are to each other. 30 years apart and from different continents and they are practically interchangeable!
I mean, look at how that outer panel fits to the lower bulkhead.
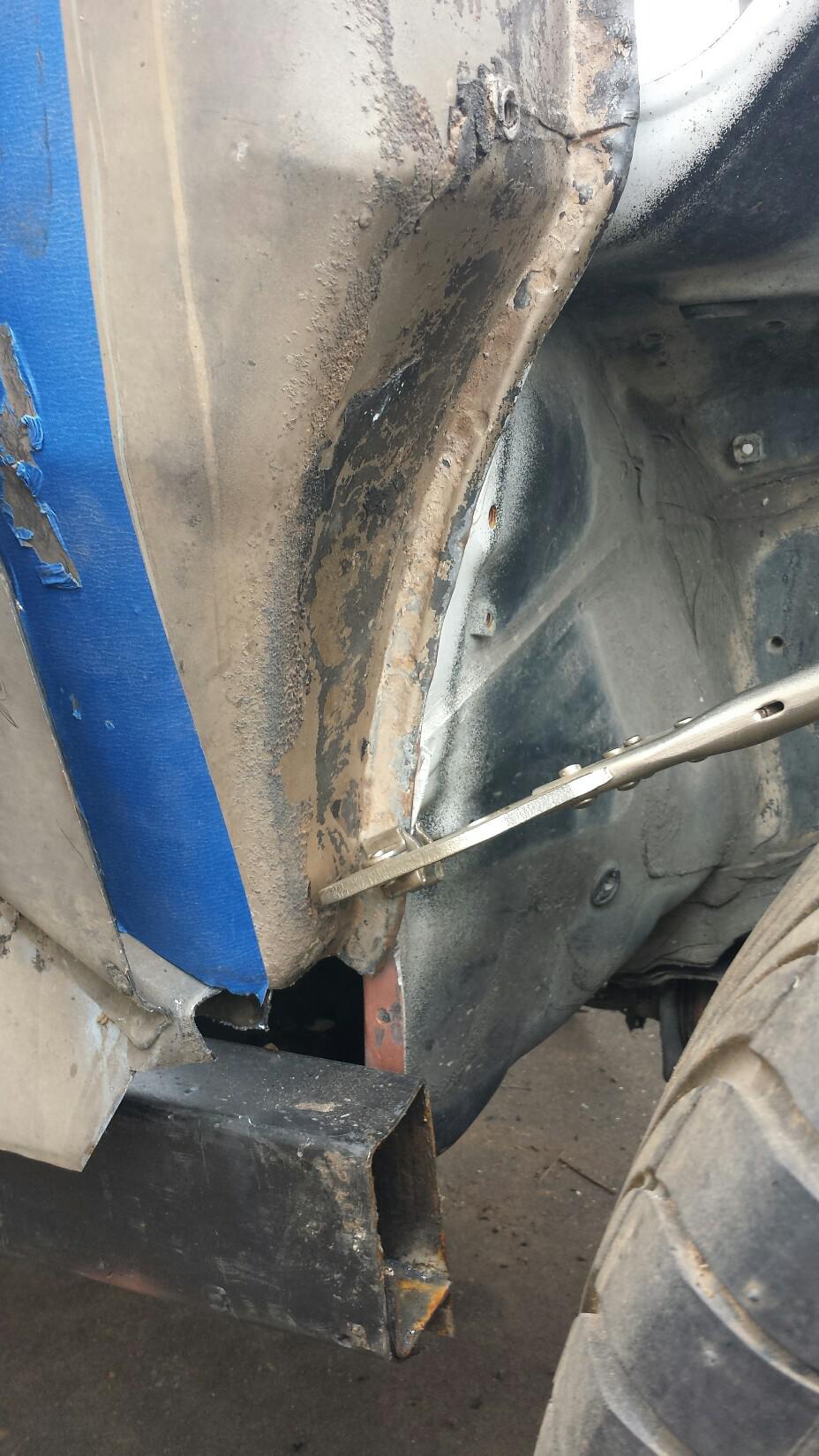
Well, it doesn't photograph well, but they have the same arch at the bottom, and at the same height no less. Only problem is they're about 2" away from each other, and the top half also needs to move back about the amount.
So I made some relief cuts across the compound curves and started moving some metal around.
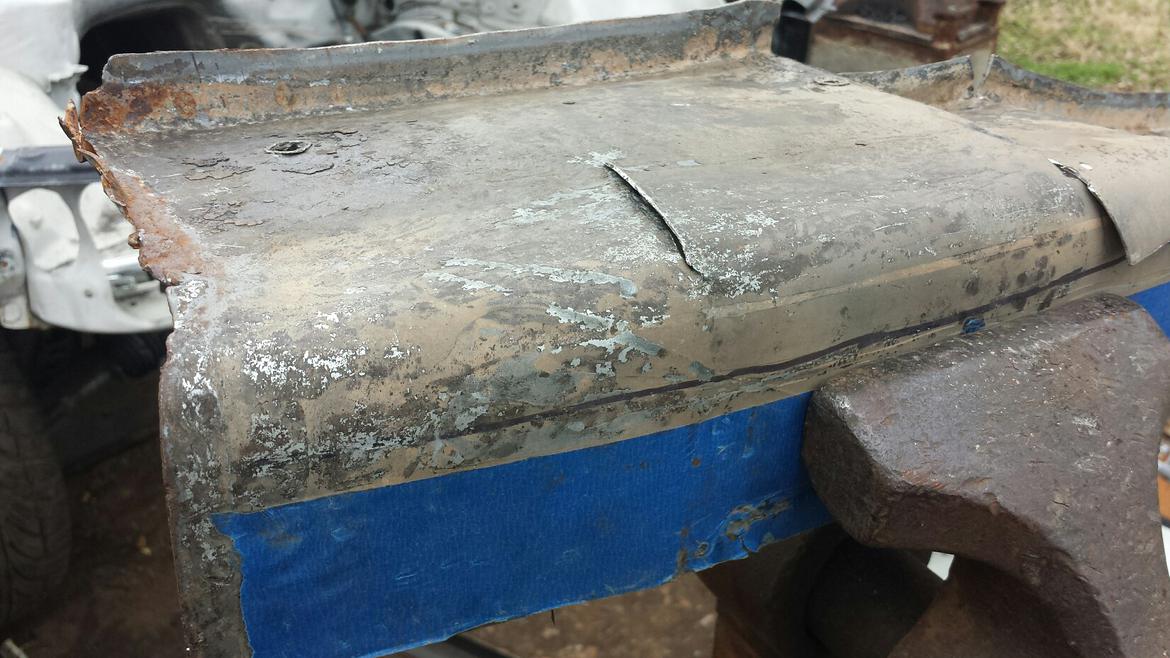
I figured since the flange needs to move inward and rearward the same amount I could just rework the panel and make it fit. That slit is where the corner was originally.
I figured right, but it took a lot of work to move a corner with compound curves in it even with the relief cuts. It took a lot of shrinking/stretching with the hammer/dolly/anvil/stake anvil.
Mid process.
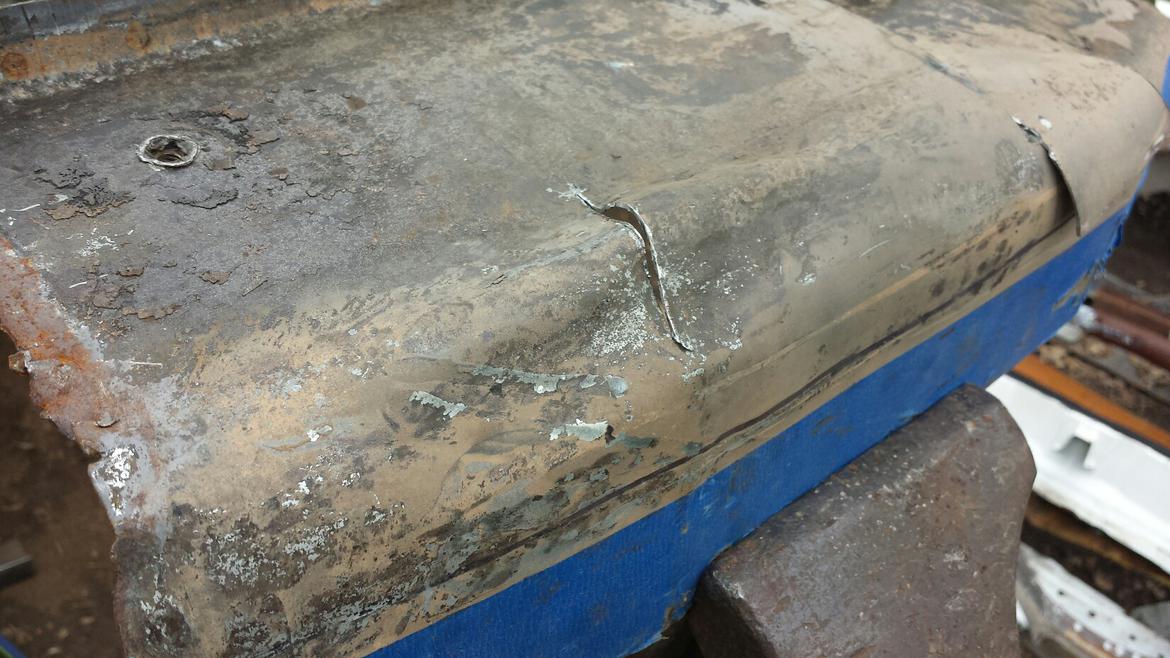
You can see the "lump" around the relief cut that shows how much material had to be shrunk down to make the compound curve go away since it was now going to be a flat section.
A little more hammer/dolly work and I was close enough to weld the relief cut shut. At this point the upper flange now fits to the Lexus flange.
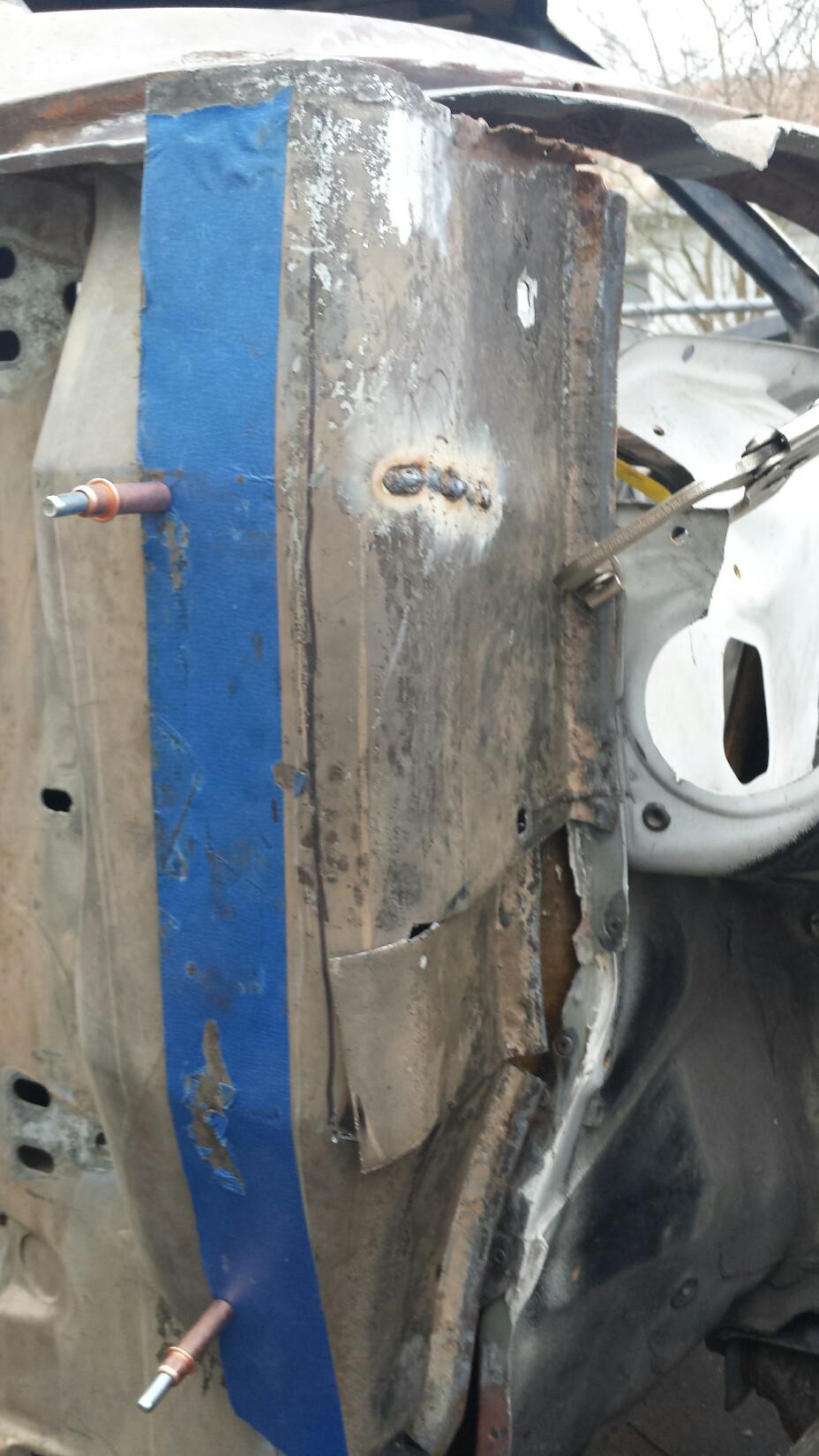
I intentionally shrunk it a little while welding too. I mean hey, why waste the heat, right?
Then I worked on the lower section and got it welded up.
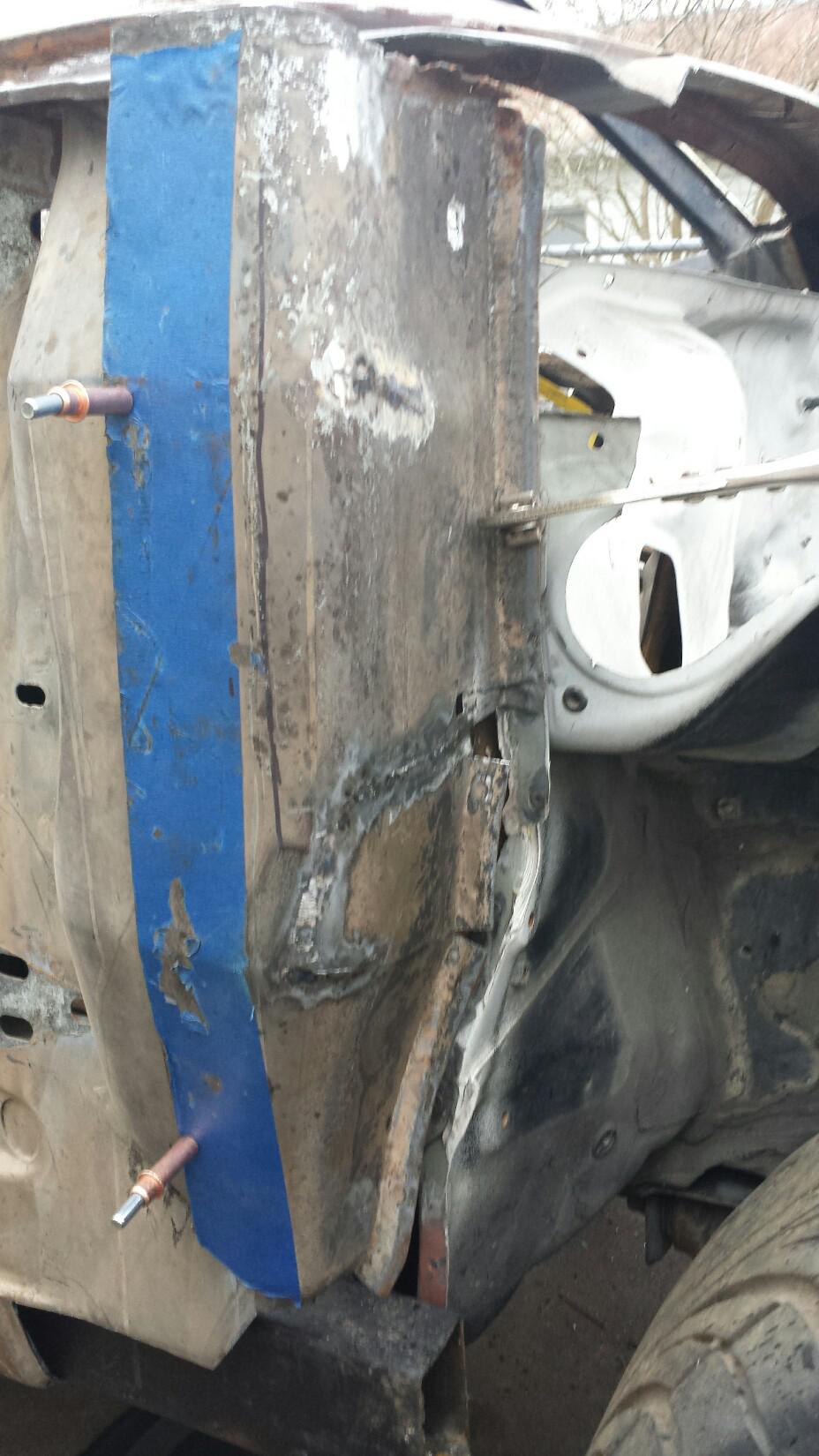
All that was left for this panel was to close up the gap at the bottom.
I decided the the fastest way to make it happen was to cut the old flange off and make a new one. In fact, it was so fast I couldn't find time to take any pictures, but here's the mostly finished panel clamped in place.
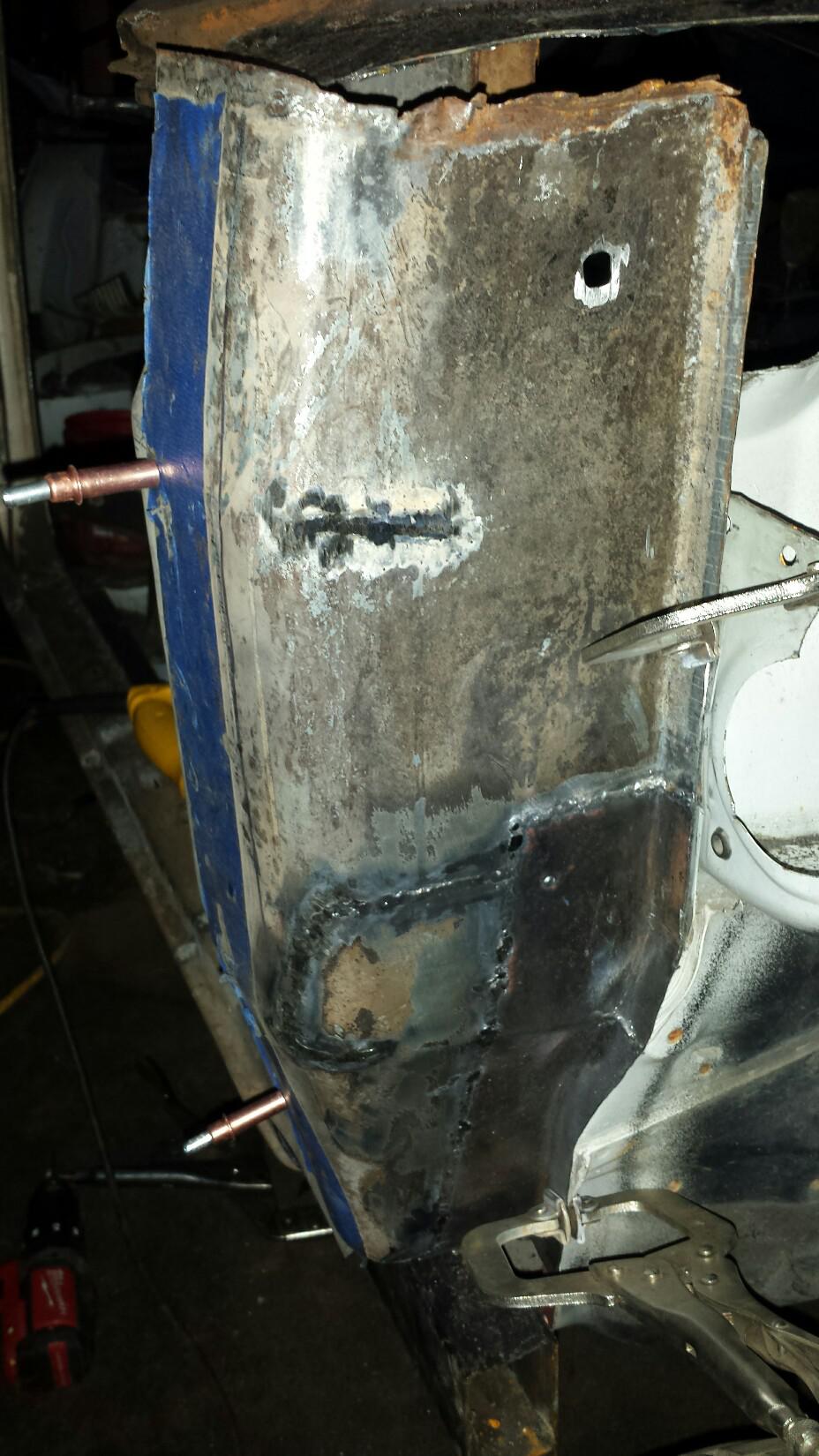
I still need to shrink down the top of the panel so it matches the cowl, but that's easy stuff after what I've already done.
Then I get to do it again on the other side! I think the other side will go a little faster. I'll probably employ the O/A torch and not do it all cold like a retard.