stroker
PowerDork
7/19/22 3:43 p.m.
I recently read "The Perfect Car" ---F1 designer John Barnard's biography. It details how he embraced carbon fiber as a chassis material but the book goes to great length to describe how Barnard was the driving force to "do it right" and follow the (literally) rocket science procedures to get it to do what they wanted. That required male and female molds, autoclaves, extraordinary material handling, clean rooms, etc.
My question is, since that first CF McLaren chassis was made about 30 years ago, how much more closely has the accessibility of proper CF manufacturing fallen to the "grassroots" level? Is the process still at a High Manufacturing status or are there CF manufacturing firms would would offer their services at a "grassroots" price? I know some FSAE teams are using CF but I don't know if they farm it out or build their own autoclaves and the other tools necessary.
Any thoughts?
kb58
SuperDork
7/19/22 3:52 p.m.
It all depends how good you want it to be.
You can treat CF like fiberglass and get to maybe 50% of "as good as it can get."
You can have the knowledge to orient the weave properly and get to maybe 75%
You can then vacuum-bag it and get to maybe 90%.
You can vaccum-bag it and then roll it into an autclave to get to 100%
Where do you draw the line? It all depends what's important to you: cost, looks, strength, strength-to-weight, etc. FSAE teams "cheat" (my term) by borrowing equipment that costs millions of dollars, and probably (I never did FSAE) don't include that cost on their spreadsheets. Anyway, you can do it at home but will need to fabricate a big enough oven with a proper temperature profile controller. It's not hard, just another side project :)
There is no shortage of people building real high quality parts from carbon fiber in their garages. As kb58 said: you can get most of the way there without all the crazy expensive stuff. I myself want to get into building carbon parts because i the splitter is huge on my car and could easily save 30+ lbs with carbon over a foam core and for around $5-600. My limiting factor is the space and heated/climate controlled shop required.
Some of the most in depth explanation, how to, and what not to do I've seen is on Throttle Stop Garage. Guy has made nearly every part of his Volvo from scratch. Considering its a small garage in middle of nowhere Canada I'd say thats about as grassroots as it gets.
Throttle Stop Garage - YouTube
Throttle stop is good. There is also dark aero, a group of three brothers making a homebuilt cf airplane!
Kubotai
New Reader
7/19/22 5:01 p.m.
I think it depends a lot on what you're trying to make out of CF. If you want to make a foam core splitter or a new hood, it's pretty reasonable to do that at the 'grassroots' level in your garage. If you want to make a CF chassis / tub or CF a-arms or wheels, you'll need some pretty specialized knowledge and equipment.
In reply to kb58 :
We fudged the equipment rental costs as "sponsor donations".
In response to the question - my friend (and at the time, manager) was the aerodynamics lead in my FSAE team for a year and he does CF on the regular. In fact, here he is: https://www.youtube.com/watch?v=Q5_Up6WgIA8
Flat panels such as front splitters, simple diffusers, wing mounts are all very easy to do at home. In FSAE we did carbon fiber airfoils for our front and rear wings and the only "fancy" equipment we used was a CNC hotwire to cut the styrofoam negative molds. We CNC machined the wing spars but you could easily 3D print the spars. Granted, this was for a relatively low speed (sub-65MPH) use case, YMMV for a large airfoil on a high speed track.
More complicated components that face complex load paths will require a lot more engineering, and more than likely require a lot more equipment.
Mr_Asa
PowerDork
7/19/22 6:01 p.m.
So for one, virtually no one is going to build their own autoclave. Its a precision machine. You might have people that can maintain their own, or even do modifications, but not build their own.
Think of it like a mill. Sure you could turn a drill press into a mill, and some people definitely do it, but in the end would it have been simpler and less headache to just buy one?
As for how DIY it is, scroll about halfway down this page, its a great representation of what's needed for the home enthusiast to knock this out.
https://grassrootsmotorsports.com/forum/build-projects-and-project-cars/c1500r-build-everything-full-chassis-build-obs-che/162404/page7/
And as a former FSAE member, I gotta address this:
kb58 said:
FSAE teams "cheat" (my term) by borrowing equipment that costs millions of dollars, and probably (I never did FSAE) don't include that cost on their spreadsheets.
That's not how FSAE works. Its also not how the real world works.
Just like in the real world, no one charges you directly for the machine you used to make the part. Its built into the labor and machining processes included in the FSAE cost report just like in the real world. Carbon fiber fabric is relatively cheap, what isn't cheap are the molds, knowledge, epoxies, ovens, and all the other stuff necessary to turn it into a part. You don't pay for the carbon fiber, you pay for the knowledge, parts, and the processes
There's carbon fiber and then there's structural carbon fiber. If you want a lightweight structure that's not highly stressed then there are several GRM accessible solutions including moldless layup over foam. That's how I did the dash in my Camaro.
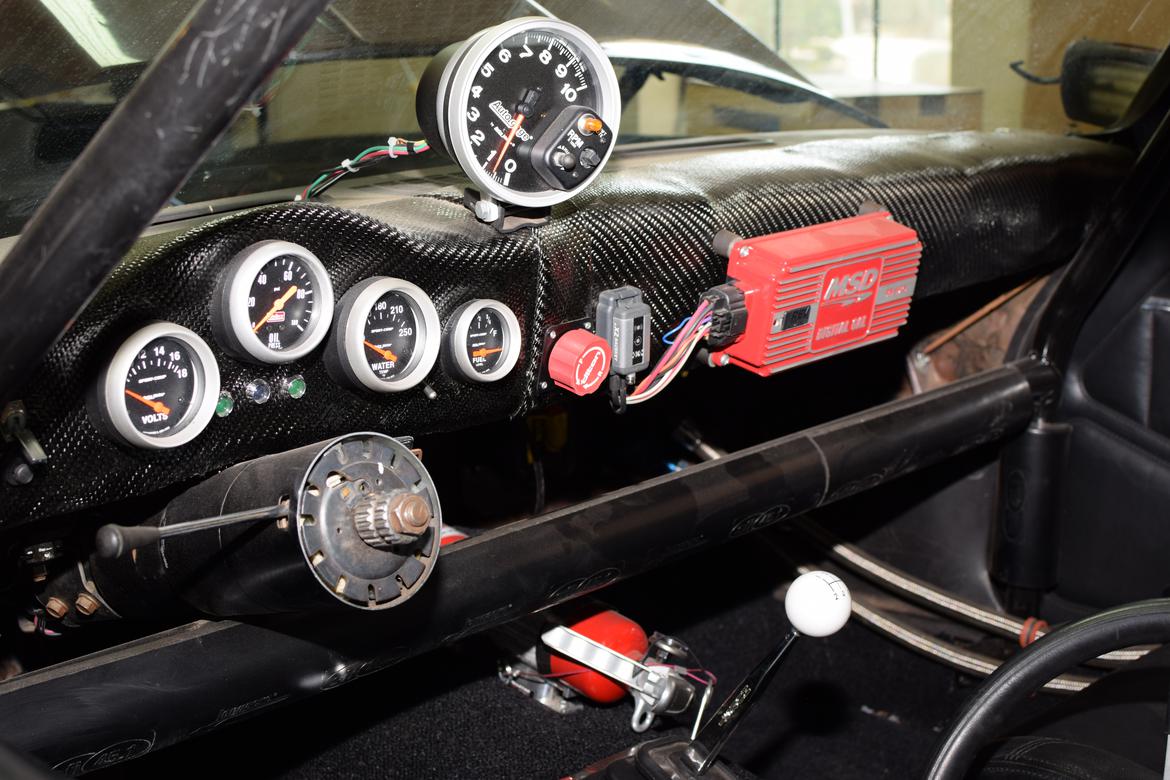
If you're making a highly stressed structure like a chassis then not only is the production process more difficult, the design is challenging. Since carbon fiber is anisotropic it's strength is highly dependent on the layup it's difficult to do FEA.
kb58 said:
SAE teams "cheat" (my term) by borrowing equipment that costs millions of dollars, and probably (I never did FSAE) don't include that cost on their spreadsheets. Anyway, you can do it at home but will need to fabricate a big enough oven with a proper temperature profile controller. It's not hard, just another side project :)
Not all of them, the most sophisticated equipment we had access to was a couple of vacuum pumps and a somewhat sketchy lighbulb oven whose insulation probably gave me lung cancer. And we only used the oven for the highly structural stuff that was probably technically supposed to be autoclaved. But you can do a lot with the ambient temperature vacuum cure (or not even vacuum cure if it's a simple enough shape) resin and basic layup processes. It won't be quite as light or strong as doing it the "right" way, but pretty close. That said, I would hesitate to use it in purely structural applications. Even at the FSAE level the risks associated with a part failure are pretty low, I wouldn't want to apply that to full size cars in the real world. But for things like lightweight body parts, yeah it's pretty accessible to the DIYer with a bit of ingenuity and reasonable expectations.
kb58 said:
It all depends how good you want it to be.
You can treat CF like fiberglass and get to maybe 50% of "as good as it can get."
You can have the knowledge to orient the weave properly and get to maybe 75%
You can then vacuum-bag it and get to maybe 90%.
You can vaccum-bag it and then roll it into an autclave to get to 100%
Where do you draw the line? It all depends what's important to you: cost, looks, strength, strength-to-weight, etc. FSAE teams "cheat" (my term) by borrowing equipment that costs millions of dollars, and probably (I never did FSAE) don't include that cost on their spreadsheets. Anyway, you can do it at home but will need to fabricate a big enough oven with a proper temperature profile controller. It's not hard, just another side project :)
In my experience unless you are going to race at F1 levels DIY carbon Fiber is plenty strong. Your appraisal underestimates strength to weight ratios by a significant amount.
I've used expired prepeg as an affordable source of carbon Fiber. Fresh resin seems to re-activate it enough to make it viable.
In reply to dps214 :
If we are talking about making suspension to formula 1 levels for Challenge money then I'll agree that DIY isn't ready for that level.
However. A simple squeegee carefully working excess resin off removes most of the excess weight. Maybe a vacuum pump and bagging it will remove the final 10% of surplus with no loss in strength.
With a light enough and relatively low power engine you might be able to build a chassis out of carbon Fiber and have it slightly stronger and lower weight than you could do in Aluminum.
kb58
SuperDork
7/19/22 9:53 p.m.
frenchyd said:
Your appraisal underestimates strength to weight ratios by a significant amount...
No where do my % appraisals mention strength to weight. Anyhow, getting to 80% is easy. I made the intercooler duct via the moldless method and it turned out great for my needs. F1 it is not and strength to weight is sufficient.
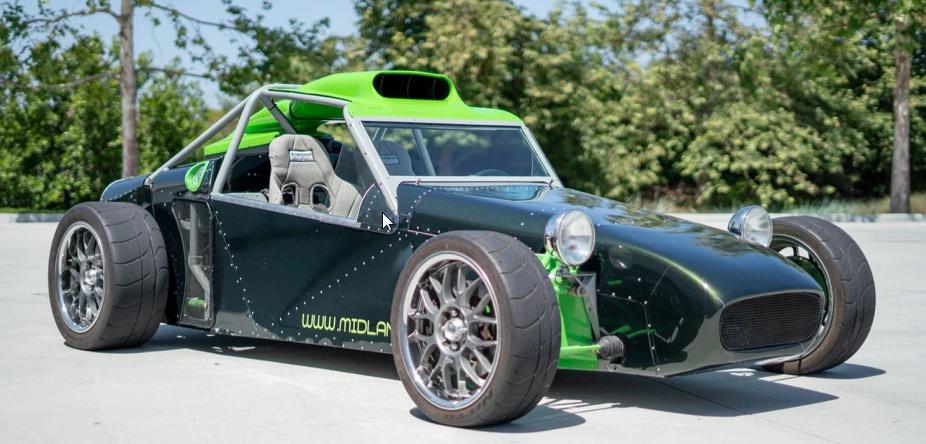
Excellent.
nice work by the way.
stroker said:
My question is, since that first CF McLaren chassis was made about 30 years ago
I hate to make you feel old but, the MP4/1 came out in 1981 and that's 41 years ago!
kb58
SuperDork
7/19/22 10:34 p.m.
While I was on the HW/SW side, I worked for a defense contractor that produced composite aircraft. To do it right does take a lot of skill and equipment, but as was said, we here aren't designing aircraft or F1 cars and can get away with "pretty good" for anything we might need for our amateur ventures, just don't try making A-arms...
To be honest, using carbon is kinda pointless for most everything we would need. I mean, if it's not vacuum-bagged, a lot of the epoxy remains in the finished product, making it so much heavier it loses its weight advantage over plain 'ol fiberglass. Yes, CF is stiffer and stronger, but it has to be used such that those properties are exercised. If you just want a carbon look, make the component out of cheap fiberglass and add one or two layers of thin carbon as the top ply. As far as making it strong, regardless of material, the key is to separate the two sides for form a beam assembly. For high force applications, "uni" is used, but that's getting into the design side of things again.
Asphalt_Gundam said:
Some of the most in depth explanation, how to, and what not to do I've seen is on Throttle Stop Garage. Guy has made nearly every part of his Volvo from scratch. Considering its a small garage in middle of nowhere Canada I'd say thats about as grassroots as it gets.
Throttle Stop Garage - YouTube
I like that guy. His channel is a good primer on DIY carbon fiber fabrication (although I do wonder if he'll ever get the car finished.
)
Well we don't agree that we ( DIY) can't benefit from Carbon Fiber.
I made a carbon Fiber bonnet for my XKE V12 race car. The stock steel bonnet is over 200 pounds. In Fiberglass I got it down to 99 pounds in carbon fiber it was down under 40 pounds.
In addition I dropped the fiberglass part and it cracked. The Carbon fiber piece was also knocked over and other than minor surface scratches no damage.
Plus the fiberglass bonnet was way more flexible than the carbon fiber. No actual numbers to confirm that. However it just felt that way when I tried to flex it like I did with the fiberglass.
buzzboy
SuperDork
7/20/22 8:08 a.m.
kb58 said:
To be honest, using carbon is kinda pointless for most everything we would need. I mean, if it's not vacuum-bagged, a lot of the epoxy remains in the finished product, making it so much heavier it loses its weight advantage over plain 'ol fiberglass. Yes, CF is stiffer and stronger, but it has to be used such that those properties are exercised. If you just want a carbon look, make the component out of cheap fiberglass and add one or two layers of thin carbon as the top ply. As far as making it strong, regardless of material, the key is to separate the two sides for form a beam assembly. For high force applications, "uni" is used, but that's getting into the design side of things again.
Absolutely right here. In my industry I see tons of carbon fiber used incorrectly that acts only aesthetically but non-knowing buyers lap it up because it's CF. Surfboard manufacturers can charge more for it but it's a pain to work with and expensive to buy. Properly speced and aligned fiberglass is fine by me.
I'm going to explain my method of making something like a Jaguar XKE hood. that pivots on two points ahead of the radiator and is exposed to 150+ mph speed.
I use the original hood as a pattern and look for the divide lines needed to avoid trapping the part in the mold. The divide lines I cut 2 cardboard strips to build a flange to unless I'm making a production mold. Then I'll use cardboard to make a pattern and use 2 strips of plywood. How thick depends on how many parts I expect to make. 1/8 Luan will be good for about 10. 1/4 plywood 25 1/2 plywood 50+ 3/4 plywood 100+
Next I clean and wax the pattern. Auto cleaner wax the first coat. But Furniture wax preferably Carnuba wax for the next 3-4 coats.
careful patient waxing. I spray a heavy coat of PVA*and let that dry
If it's a light splash mold I don't use Gel coat. I'll only get a couple of parts at most.
But beyond that I spray a thickish Gel coat.
once that hardens I brush on a coat of resin mixed to give me an hour of working time. I've got the Matt I'll use cut and laid out so I can get it with sticky gloves. Each layer goes on before I brush on another coat. And then another layer goes on and finally the last layer.
If the only Matt I have is thicker I'll settle for two layers. Then I use the serrated roller to get all the air bubbles out.
Let that dry. Using plastic/ nylon wedges pop off the mold. Wash off the PVA from both the mold and the pattern. It's water solvable
* PVA is poly Vinyl Alcohol. Or mold release.
Once the mold has aged a few days. Wax that with furniture wax. Make it shine so you can see any flaws. 4-5 coats. Then PVA again. Spray a. Thick coat of Gel coat, don't get overly aggressive with the hardener. Let that harden while you are cutting out the fiberglass cloth or carbon fiber or Kevlar use a fresh pair of pinking shears for those. I prefer Fisker Brand they tend to be the sharpest.
I lay one layer straight. Squeegee off the excess The next at 45 degrees, squeegee
The third at another 45, squeegee. Then I use that perforated and cut foam to add depth and a final coat on top of the foam. Squeegee. If I were going back to SCCA instead of the foam I'd do two layers of Kevlar.
Stampie
MegaDork
7/20/22 11:26 a.m.
In reply to frenchyd :
So you've made a carbon fiber XKE hood using this method?
In reply to Stampie :
Yes for my XKE V12 there should be pictures of it somewhere.
It was sold on Bring a trailer.
In reply to frenchyd :
I didn't know you did carbon fiber.
In reply to Stampie :
Back in the 1980's I was introduced to it by Gerome the guy who taught me fiberglass. We still had NorthWest Airlines and the first things I did were prepeg. I knew the guy at NWA if their autoclave wasn't in use on the weekends I could go there and cook things. I didn't know the squeegee trick until about 2000.
I've only done I piece using the vacuum bagging process. Too expensive as far as I'm concerned
The nice thing about fiberglass work is when you're done the materials don't take up much room to store and they are all light. I just roll the material put it in plastic bags someplace up high because they are light and have all the space back.
I used to ruin whatever clothes and shoes but the cheap plastic suits save me from that.