Here is what I came up with for a suspension bracket for my Midlana on the front suspension, lower rear point (the one that takes most of the braking force). The bracket is angled to be inline with the rear leg of the A arm. The rod end on the jig is set at the correct elevation and angle of the rear leg of the A arm, and is the book value back from the front pick up point.



I will add some gussets between the forward part of the bracket and the vertical tube in the final version. Thoughts? Should I fully overlap the rear of the vertical tube like the template shows? This will add some strength, but has a potential for corrosion in the area of overlap, and will make attaching paneling slightly more difficult.
Critique my design! 
Centered in the flat of that square tube is the weakest location on it. I would say you would do better to relocate the flange to the outer edge of the square tube, and then use a spacer to locate the heim joint where you wish.
Due to the funky angles the forward part of the bracket is centered at the top, but is actually at the edge of the tube on the bottom. The hiem is where I want it as it sits on the jig. It could be moved forward, but that would require a slight re-work of the A arm. I guess another option is to add a backer plate to the face of the tube in the vicinity of the bracket.
I don't see much room for a nut for the bolt that I assume you'll use to hold the heim in place. I'm sure you can get one in there but I thought I just point that out now before you weld something together.
Yeah, that would be important! I think there is room, but I will confirm before I weld anything.
I'd probably use steel instead of cardboard.
44Dwarf
SuperDork
3/20/14 6:06 p.m.
Move the plate to the edge then drill a 3/4 hole and weld in a spacer tube (3/4 OD 1/2 ID) and use a long 1/2 bolt. Yes the angles strange and the spacer will likely cut through the edge of the 1x2 but after welding it will be strong again.
Spacer tube is easy to find many circle track places sell it as steering columns but I buy it in 20 lengths from Marmon keystone.
bgkast
Dork
3/20/14 11:31 p.m.
The bolt actually clears the corner of the tube.
Here is a revised version with a doubler plate. As long as it doesn't get wet I think it will be strong enough.
I will sleep on it and make it out of metal tomorrow.

You've got what looks like an all but insurmountable bolt clearance problem in that last picture.
You might be able to just clear a nut on that inside edge, with the bolt installation reversed from what you have in the picture.
If the bracket in the last picture would serve - what purpose is the rod end? It does not appear that it can articulate. Spread out the flanges and add some cone spacers?
To get around the bolt clearance - weld a nut on the back of one of the plates so you can thread the bold right in to it from the clear side.
If you must be at the odd angle on the weaker part of the tube, plate the bottom and maybe even add "winglet triangles" to the upright tube on the outside around the nut you weld on there.
Tralfaz
New Reader
3/21/14 6:58 a.m.
It would be better to not impart an axial load on the bearing as you will have under braking.
IIRC axial load is around 15% the rated radial load
^Good point. You usually see bushings oriented this way, spherical bearings on wishbone-to-frame mounts are usually mounted on a vertical axis.
tuna55
PowerDork
3/21/14 10:37 a.m.
foxtrapper wrote:
You've got what looks like an all but insurmountable bolt clearance problem in that last picture.
You might be able to just clear a nut on that inside edge, with the bolt installation reversed from what you have in the picture.
What does this thing do again? I might weld a nut onto the bracket where you have the bolt head now.
Otherwise, like GPS said, why does it need to articulate?
Sorry, I've been so close to this thing I didn't give enough background information. This bracket will connect the rear leg of the front, lower suspension A arm to the chassis. The A arm looks something like this:

There are basically 3 ways to do this joint: With the bolt passing through the rod end vertical, horizontal and along the pivot axis, or horizontal and not along the pivot axis. Having the bolt vertical is probably the best solution, but due to the bracket location on the chassis it makes final reaming and bolt installation difficult. This is how it was done on the prototype car.

Because of these issues the designer suggest doing it another way. The second option also has downsides, mainly lording the joint axially, and causing a bending load on the joint threads because the joint is not in-line with the arm:
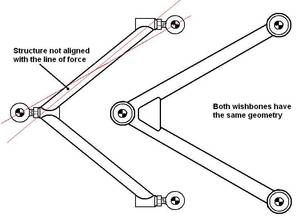
That leaves the third option, which I am using...having a horizontal bolt, and angling the bracket to be inline with the arm, sort of like this:

With this orientation the pivot axis is not along bolt through the rod end, it is parallel to the center line of the car (the green line is the pivot axis).

This orientation will allow me to ream the bolt holes to size after they are welded in place and makes bolt installation much easier (it does clear the tube, even though it does not look like it in the pictures).
The final design will have some boxing and gussets like those shown in red. It appears that I will have adequate suspension travel without the joint hitting the bracket, but the only way to know for sure is to make the thing out of metal and lightly tack it on.
Hal
SuperDork
3/21/14 2:27 p.m.
In your picture above I would move the top left corner of the boxing plate out to the left edge of your doubler plate. That would allow it to also serve as a gusset similar to the bottom one.
Tralfaz
New Reader
3/22/14 7:37 a.m.
If you go this route it seems it will be at best a headache to adjust. Why not swap to bushings on this lower arm and leave all the adjustment to the top?
T
Knurled
PowerDork
3/22/14 7:57 a.m.
If at all possible, wrap the doubler plate around the tube slightly so the seam is on the side. This gives three benefits for only a slight weight penalty:
The doubler plate will have two bends in it so it will have its own inherent strength, instead of just giving a thicker place to weld to
You won't be welding a line down an existing 90 degree bend where the metal has already been weakened slightly, which can easily lead to a crack forming right there
It will allow you to weld the gussets to "fresh" metal instead of welding to a weld, which has a lot of suckage factors involved.
I'd suggest moving your big plate to wrap around the inside edge of the vertical tube and the smaller plat to the outside. Bolt and skin will both get easier. What you have now will ripple issues through other parts of the project.
Thanks for the suggestions. I was busy all weekend, so it's still made out of cardboard. I will look at wrapping the doubler plate around the forward outside corner. I'm not sure my bolt head will clear the corner if I do this though.
Oldopelguy- what future issues do you foresee? If I move the smaller plate to the forward face of the tube like I think you are suggesting, but don't change my A arm geometry the rod end will still be located in the same place it is now, and there will be about 0.5-0.75" of "exposed bolt" that will need to be taken up by a spacer. This isn't the end of the world, but it will introduce some bending loads onto the bolt.
Don49
HalfDork
3/24/14 7:32 p.m.
Looking at your set up, I believe you should go to a vertical installation for the bolt. That way you will be loading it in its strongest orientation without any bending forces on the bolt. You should be able to make the horizontal brackets work based on your pictures.
Never mind me, I was thinking that the joint in question was for a rear arm and oriented differently, carry on disregarding my previous comments.
If you are concerned about the strength of the plates cut off a chunk of steel tubing with an ID bigger than the Heim joint to the thickness of the Heim joint. Cut that chunk in half for a pair of half circles. Weld in between your plates with the open end to the arm direction before you weld the plates in place.
One last option, which could be cost effective if you haven't already bought your joints, would be to use stock car upper ball joints with their bodies mounted to the frame and shafts mounted to your arms. Bolt or screw in would be best, oriented so the shafts point at each other.
Leafy
Reader
3/25/14 11:19 a.m.
God, every time I look at any of these locusts/homebuilt 7s/etc my penis tries to hide back up in my stomach. They're so f'in scary. Make the rod end go away, stop using those damn things. Use berkeleying sphericals already, they costs the same damn amount of money, will last longer, and you wont have to worry about the threads breaking, and you wont end up with crappy hack looking control arms with useless "adjustments".
Oh, and that bracket sucks too. ;)