So, i need to dial in a bellhousing. Ive read the articles and how tos.
Problem is that i cant for the life of me actually figure out how to get the dial indicator set up. I know i use the magnetic base and crank flange. Somehow. No clue after that. My brain has turned to pudding thinking about it.
Can one of you smart guys explain it/find a how-to/draw stick figures/SOMETHING???
needs to be set up properly before the next $400 clutch and $300 of trans parts goes in the duster....
I'm not sure what you're struggling with but this article Link has a good explanation and some pretty good pictures. One thing some people get hung up on is the idea that the indicator setup has to be centered on the crank and that's not true. You can stick it pretty much anywhere that it'll stay on and the indicator fits somewhere in the bellhousing hole.
The center of of the crank is what im hung up on. I just can't seem to get my brain to understand how to get a relative measurement from crank centerline to bellhousing without finding the center of the crank.....
Don't need to. The magnetic base, wherever it is stuck, is a constant distance from the center of the crank. As you rotate the crank, the dial indicator base moves in a perfect circle around the centerline of the crank.
So, dial indicator base stuck to crank, pin on dial indicator on the inside circumference of the bellhousing hole. Rotate crank, use sharpie to write the dimension of high and low spots on the face of the bellhousing. Divide by two, and move the bellhousing that far towards the smaller number.
Repeat ad infinitum.
In reply to Streetwiseguy :
Really that simple? Really?
How have i not figured that out in 4 berkeleying HOURS of staring at it????? (I wish i was exaggerating.....)
So whats the spec to shoot for? It seems the only real consensus is zero or as close as possible. Its an old Lakewood bellhousing and a small block mopar. They were both built with yardsticks.
I'm getting ready to do the same checks on a custom adaptor plate for mounting a manual transmission using an automatic bellhousing. I thought a picture might help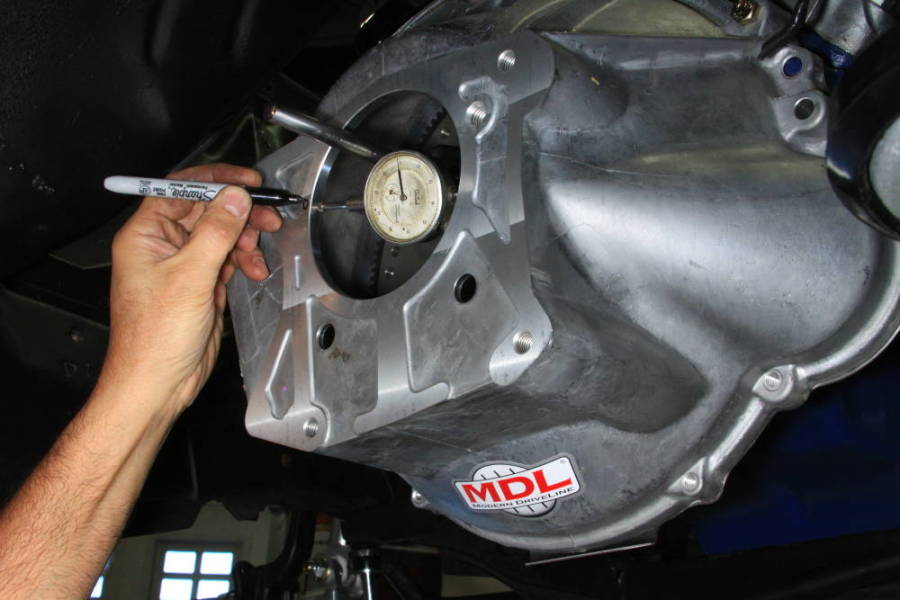
In reply to Dusterbd13 :
If it helps, I've been thinking of how to make a custom adapter for over a year and this part still mind berked me until Streetwiseguy posted.
The closer to zero the better, is there a tolerance yes, what it is depends on how long you want it to live and how much power you ar willing to loose by not having it at zero. You also should check the face run out as well as the bore. There is not much you can due about any face run out (where the trans bolts to) but it should be checked. If that bell housing seen a tranny blow up or been in a wreck its possible to bend the bell and not crack it. I know of several race teams that have chased there tail on noises and vibration after a hit to find the housing bent upward.
So I guess a follow-up question is how do you actually adjust where the bellhousing it is without special ordering offset dowel pins? Or is that pretty much the only option?
Measure first. If it's off, the offset dowels are the trick.
What transmission are you using?
If you're using any of the factory MOPAR 4 speeds then I wouldn't make an adjustment unless you're out more than +/- 0.007" (0.014" of needle movement). If you're using a Tremec or something like that then you'll want to go by their spec which I think is +/- 0.005".
Im using a tremec 3550, with a Lakewood bellhousing that i drilled and welded for the tremec.
Iys currently running the factory style dowel pins.
.005 is .01 of needle movement. Right?
Getting into much more accuracy than .1 is a struggle for my brain.
Yes, because one side is +0.005 and the other side is -0.005, so the total indicated is 0.010