Many factory rails have individual clips that snap them in at the top and then the rail bolts in to keep them in the manifold bungs. If you buy blank rail and drill it - what is the typical way to secure the injectors to the rail?
Can you buy the "cups" for the rail (Ford/Bosch top feeders) instead of drilling o-ring sized holes like you can get the weld-on bungs for the intake? If so... a linky? My google-fu finds lots of bung applications, no rail-side ones.
MSD used to sell a solution that would mount individual injectors that you could route individual lines to via a fuel block.
Or they had fittings that slid over stainless tubing, then you had to tig the fittings in place.
The clips are more of an assembly aid than anything else - if the rail is held firmly in place by some sort of mount, the injectors will remain secured in place by the O-rings and the wide part of the injectors preventing them from moving up and down.
not on an M50 rail that walter is talking about, its only held in place with two 6mm bolts and the factory rail has enough flex in it where you can pop one o-ring half out, so I wouldn't trust it under pressure without the retaining clip. My only guess is to fab up a better mounting system or you can possibly machine a grove (if you have a lathe handy) for the retaining clip in a bung like yo:
http://www.racepartsolutions.com/proddetail.asp?prod=RPS-InjB&cat=108
You can "weld" in hold down brackets in a custom made rail. We did a half-assed way on the GRM challenge car I made. Didn't leak at least.
BTW, the systems are silver soldered, not welded and not brazed. I tried brazing mine- what a PITA, since the metal is thin. Good silver solder, good flux, clean surfaces- solder all day long.
I wish I could help you on where to get the cups. Mine just showed up one day in my hand.... 
(probably can get them from a junkyard. again, they are soldered in- a good propane or MAP torch and they should come off quickly. Uh- do make sure they are clean of fuel.
)
alfadriver wrote:
You can "weld" in hold down brackets in a custom made rail. We did a half-assed way on the GRM challenge car I made. Didn't leak at least.
BTW, the systems are silver soldered, not welded and not brazed. I tried brazing mine- what a PITA, since the metal is thin. Good silver solder, good flux, clean surfaces- solder all day long.
I wish I could help you on where to get the cups. Mine just showed up one day in my hand....
(probably can get them from a junkyard. again, they are soldered in- a good propane or MAP torch and they should come off quickly. Uh- do make sure they are clean of fuel.
)
That is interesting. The rail stock I bought is thick aluminum - I just assumed I'd be TIGing anything that needed attachment (which I'm really not very good at) but I can solder well with a torch. Maybe given that I should use some thin steel tube for the rail and a junkyard trip for used cups instead.
I also considered turning some round stock in the lathe, cutting it to half-inch increments for press-fitting it into the aluminum rail... slicing them to accept a c-clip.
In reply to Giant Purple Snorklewacker:
I have seen some aluminum- can't really solder with that- I think most production rails are stainless, and the solder is designed to work very well with it.
Well, there may be something that can solder aluminum. The point, though, pressures are not all that high, generally, and the strength of solder is fine.
Meant to ask this before, but are you just trying to run a larger line to the OE rail? I'm running a -6 feed line and all I did was cut the inlet tube off the OE rail, enlarge the hole and then braze on a steel -6 bung like this:
http://www.racepartsolutions.com/proddetail.asp?prod=JOD%2D5991
I think I spent more time getting the parts out of the car than I did fabbing this up...
gLockman37 wrote:
Meant to ask this before, but are you just trying to run a larger line to the OE rail? I'm running a -6 feed line and all I did was cut the inlet tube off the OE rail, enlarge the hole and then braze on a steel -6 bung like this:
http://www.racepartsolutions.com/proddetail.asp?prod=JOD%2D5991
I think I spent more time getting the parts out of the car than I did fabbing this up...
This would be a 70 Chevelle with a big block V8 so... not like that at all really :)
ah gotcha, was thinking this was for your CM car, cary on then
...
SVreX
MegaDork
6/21/12 10:41 p.m.
Paging 16VCorey...
He did some wizardry with copper tubing fittings from Home Depot a few years ago in his Rabbit.
Giant Purple Snorklewacker wrote:
Many factory rails have individual clips that snap them in at the top and then the rail bolts in to keep them in the manifold bungs. If you buy blank rail and drill it - what is the typical way to secure the injectors to the rail?
You don't have to secure the injectors to the rail. As you point out, the rail holds them in place. Many OEMs didn't and most aftermarket rails don't.
When I make a rail, I grab a fuel rail from a Chrysler with a steel rail, cut the too-long sections out with a tubing cutter, and weld it back together. Have never had one leak. The 4.0l Jeep engines are great donors for making rails.
Ok, I am thinking of modifying some OEM Ford fuel rails off a 5.0 Crown Vic to work with the intake flipped (a la Mustang). I don't have an easy source for the Mustang version so I was thinking of taking what I've got and silver soldering something together that's useable for my BMW project car. I am NOT spending $560+ on some aftermarket rails and regulator.
Has anyone done something like this before and if so, any pitfalls to watch out for?
Moving_Target wrote:
Has anyone done something like this before and if so, any pitfalls to watch out for?
My first attempt held water at 80 psi but when I hooked it up on the car at 55psi it resembled more of a shower head than a fuel rail.
Gas has a very low surface tension that allows it to seep thru stuff water won't - even at much more pressure. So... pressure test your solder/weld/braze somewhere safe with gasoline before you try to use it near heat and fire.
Giant Purple Snorklewacker wrote:
My first attempt held water at 80 psi but when I hooked it up on the car at 55psi it resembled more of a shower head than a fuel rail.
Gas has a very low surface tension that allows it to seep thru stuff water won't - even at much more pressure. So... pressure test your solder/weld/braze somewhere safe with gasoline before you try to use it near heat and fire.
Off the top of my head, there is a fluid available that has similar properties as gas, but is less dangerous. Not free of danger, just less.
can't think of what that is, though.
SVreX wrote:
Paging 16VCorey...
He did some wizardry with copper tubing fittings from Home Depot a few years ago in his Rabbit.
Yep. Let me find some pics. Your standard 1/2" type L copper tubing is the perfect size for a regular Bosch style fuel injector to fit into snuggly. The only thing the clips really do on the stock fuel rails is keep the injectors on the rail when you take it apart, so you don't dump fuel everywhere. The injectors are sandwiched in between the rail and the head or intake manifold, so as long as your rail is fastened securely the injectors won't move. I'm eventually going to solder tabs on mine, but right now it's fastened to the intake manifold with zip ties, and it doesn't leak a drop.
PS - Photobucket is loading SUPER slow right now. I'll add photos later.
In reply to Moving_Target:
I'll have to ask around.
Vigo
SuperDork
7/30/12 9:26 p.m.
Photobucket IS super slow right now. I hope that ends.
Photobucket is working much better today.
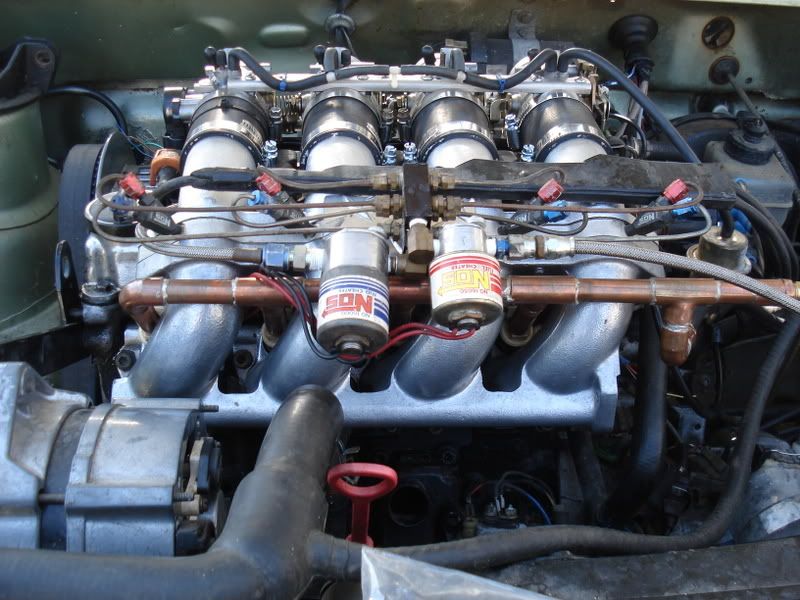
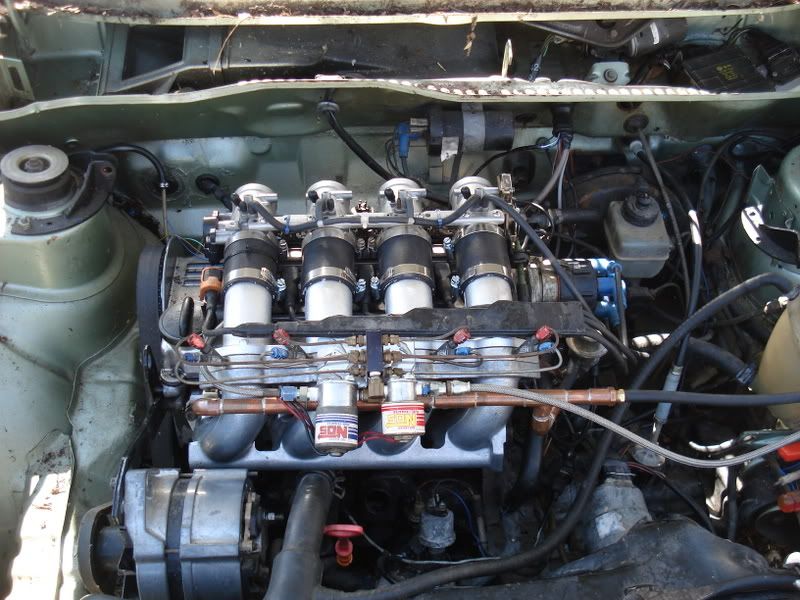