Hi guys, working on getting the floor finished in the Courier. One of the last items (aside from drilling holes for spot welds) is setting up the floor for the body mounting bolt. I came up with an "answer" today that is close, but is really warping the metal on the 2nd test piece I did. In brief, it's a pocket, and I run a bolt through a "spacer", the sheet metal and the plates, and is driven into a nut with an impact gun.
Below are the two trials. For the 1st one, i used a 1.5" hole saw, and rounded out the inner piece to compress. Turned out well, but it's not deep enough or big enough across. So i stepped up to a 2 1/16" hole saw, and in 2 steps went from the initial spacer to a thick 1.5" diameter space. It could just be the piece of metal I used, but it got a very large crease. Would love to avoid this when I am actually working on the formed floor pan.
Pics below. Does it need to be shrunk beforehand? or stretched? Not experienced enough with this!
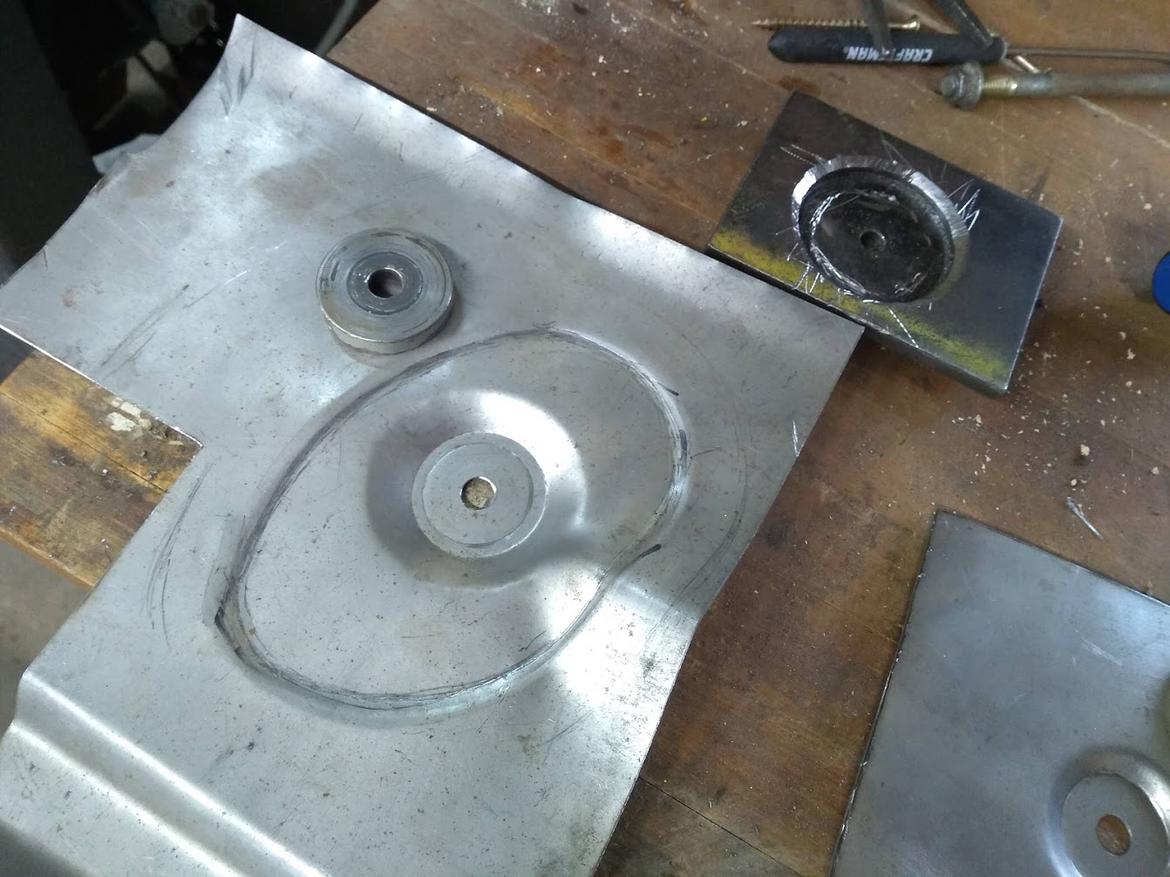
And the 1st attempt.
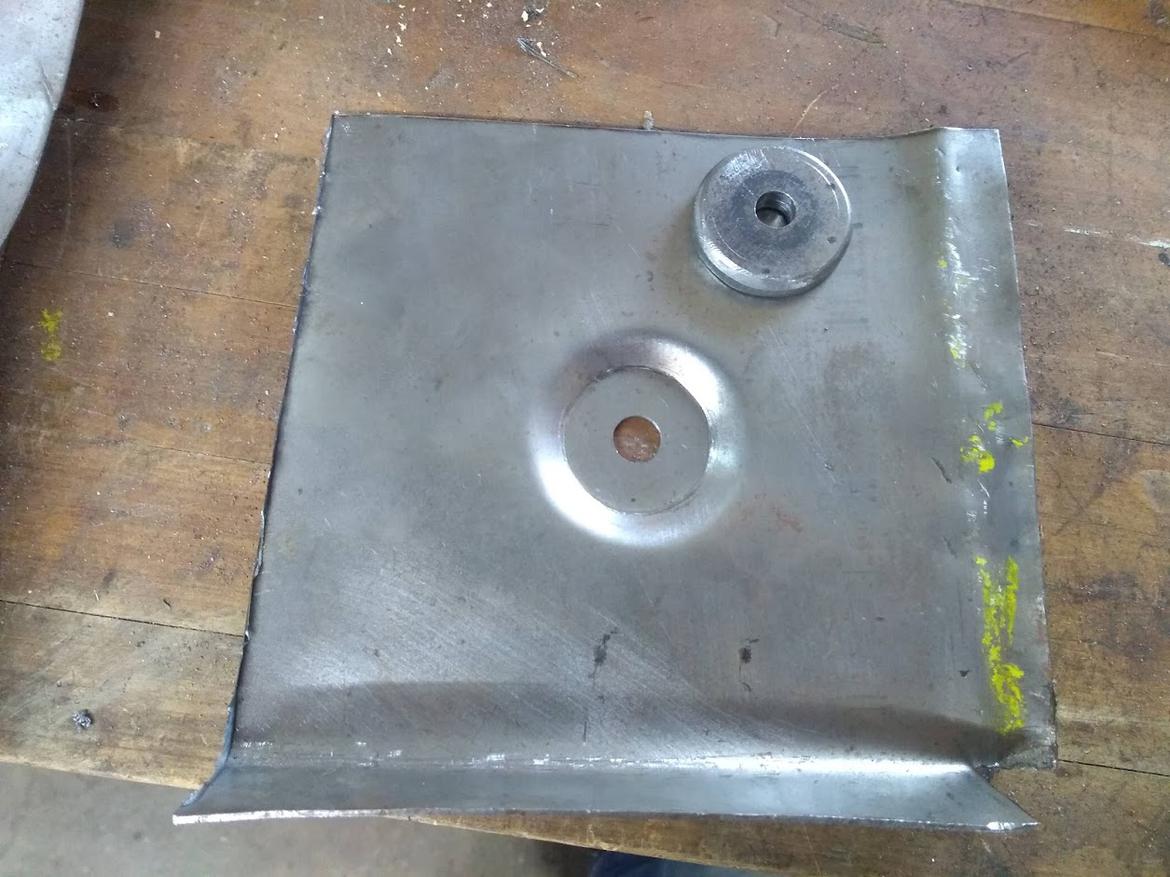
Every die I have ever seen for this sort of thing has a backing plate on the convex die for just this reason, not just a simple puck like you have. It constrains the metal from warping too much and then it flattens it back out again.
You need a big backing plate as stated with a concave die to match the convex die, and you need a flat around it.
A guy could make a pretty good die out of three 6x6 pieces of 1/2" steel. One as the backer. One as the middle. Cut the slug of the dimple you want out of the middle and weld the slug to the center of the top plate. Now you will have something you can work with.
Bummer. No 1/2" material around, no welder that strong, and not 6" clearance around the necessary pocket, ha! Looks like I'll need to find an alternative method.
An alternative method is to press your hole in whatever piece of material you have, then cut it out and weld it into the real piece with an appropriate hole cut into it.
WonkoTheSane (Forum Supporter) said:
An alternative method is to press your hole in whatever piece of material you have, then cut it out and weld it into the real piece with an appropriate hole cut into it.
I walked by the pieces this morning and kinda figured thats what I'll do. Looks like the pocket i formed on Saturday will work, I'll just chop it out and get it set into the actual floor pan..
classicJackets (FS) said:
WonkoTheSane (Forum Supporter) said:
An alternative method is to press your hole in whatever piece of material you have, then cut it out and weld it into the real piece with an appropriate hole cut into it.
I walked by the pieces this morning and kinda figured thats what I'll do. Looks like the pocket i formed on Saturday will work, I'll just chop it out and get it set into the actual floor pan..
Yeah, reality kinda sucks sometimes, eh? :)