Looking at the wiring diagram I'm a bit intimidated. While I've wired all my past race cars, working with an ECU is going to be new to me.
I don't have a Grizzly old Geezer to dope slap me and tell me to just get busy. So I'm looking. Is that something that is commonly done in major cities by a few specialists or strictly DIY?
If done by a specialist, how do I know if the quote is reasonable? Or perhaps he's too busy or intimidated himself so he will double it to be sure?
How much time to do a from scratch ECU is fair? Or is it by dollars?
It's reasonably DIYable, the trickiest parts will be laying out the grounding correctly, and running any twisted pair wiring if there are CANbus devices involved.
You should do it yourself. That way you know the workmanship is sound, and down the road you will be the one repairing or troubleshooting it so you'll know all the little details.
Building a reliable wiring harness requires fairly little in the way of direct skill, but at least a moderate investment in specialized crimping tools and a lot of time, patience, and attention to detail.
codrus (Forum Supporter) said:
Building a reliable wiring harness requires fairly little in the way of direct skill, but at least a moderate investment in specialized crimping tools and a lot of time, patience, and attention to detail.
This. Also do not use butt connectors. Also, keep grounds simple/easy to access/well connected. Keep grounds for sensors away from the rest of the "dirty" ground. Spend 80% of your time researching connectors, crimpers, wiring, fuse panels, relay harnesses, wire, etc and 20% of your time doing the work. Know that any shortcut will be revisited at a later date and most likely in the pits/trackside and will definitely be harder to access.
Keep all terminations as visible/accessible as possible.
Redoing my engine fuse panels now and trying to improve it. Only failures from the first go was trying to butt-connect 2 wires to 1 and some grounding groups that made some of my sensors a bit haywire. People have different feelings about use of relays versus use of switches. Check out paneltronics for fused switch panels that are cost effective. Many marine electrical parts are quality, water resistent and more cost effective than their automotive counterparts.
I am NOT good at wiring but have fumbled my way through full vehicle wiring including standalong engine, abs systems, dash, sensors, etc and have survived so I got that going for me.
Olemiss540 said:
codrus (Forum Supporter) said:
Building a reliable wiring harness requires fairly little in the way of direct skill, but at least a moderate investment in specialized crimping tools and a lot of time, patience, and attention to detail.
This. Also do not use butt connectors. Also, keep grounds simple/easy to access/well connected. Keep grounds for sensors away from the rest of the "dirty" ground. Spend 80% of your time researching connectors, crimpers, wiring, fuse panels, relay harnesses, wire, etc and 20% of your time doing the work. Know that any shortcut will be revisited at a later date and most likely in the pits/trackside and will definitely be harder to access.
Keep all terminations as visible/accessible as possible.
Redoing my engine fuse panels now and trying to improve it. Only failures from the first go was trying to butt-connect 2 wires to 1 and some grounding groups that made some of my sensors a bit haywire. People have different feelings about use of relays versus use of switches. Check out paneltronics for fused switch panels that are cost effective. Many marine electrical parts are quality, water resistent and more cost effective than their automotive counterparts.
I am NOT good at wiring but have fumbled my way through full vehicle wiring including standalong engine, abs systems, dash, sensors, etc and have survived so I got that going for me.
What scared me was trying to figure out some of the terminology. I spent 3 days researching high side and low side switches. OK now I understand one is switch to ground one is switch to hot.
grrrrrrrr!!!
moto914
New Reader
3/14/23 12:56 p.m.
Some stand alone ECU sellers offer harnesses with a plug connector on the ECU side, but you need to make the connections to your own sensor pigtails. Get a little more length and you'll be using mostly their wires. Making your own injector harness is doable but can take some time .
codrus (Forum Supporter) said:
Building a reliable wiring harness requires fairly little in the way of direct skill, but at least a moderate investment in specialized crimping tools and a lot of time, patience, and attention to detail.
My fear is translation from Jargon and terminology.
How many hours did it take you to complete it?
In reply to moto914 :
How much time did you spend on yours?
The idea of the connector wired up for me. Is almost my greatest fear. So if I DIY and all I have to do is connect the ends to the right inject, coil on plug. That sounds like I'm 90% there already. The sensors should be really straight forward.
Thanks.
It looks like a big job when you step back, but just tackle it one wire at a time and you'll make progress. You'll get a much neater result if you pay attention to wire runs and making the wire just the right length. Adding in an extra 6-12" may seem like a good idea but it means you'll have a snarl of wires jammed into your various crevices. I like to use vecro bands to bundle wires together because they're much easier to remove, resize and replace than zip ties. Pay attention to anchoring, wire harnesses don't like to vibrate over the long run.
Get a ratcheting crimping tool with the correct jaws for the connectors you're using (they're not expensive) and high quality connectors with integrated heat shrink. Don't be scared of butt connectors, but do be aware if you're dealing with a shielded sensor wire - you won't want to accidentally connect the shield to the signal.
There are special butt connectors for 2-1 connections. A good source is Del City: https://www.delcity.net/store/Terminals/. I like the heat shrink ones.
moto914
New Reader
3/14/23 1:18 p.m.
In reply to frenchyd :
The injectors took a couple hours for a 4cyl H4.
My time is worth more to me than my money. I figured research and assembly were worth 8-10 hours. Add to that the cost of wire, fuse block, fan and pump relays, and sensor and coil plugs and $500 seemed dirt cheap. I bought a harness. It was stupidly easy to install and worked. Money well spent.
https://swapspecialties.com/
In reply to Keith Tanner :
What's your favorite ratcheting crimper? I've got one for sparkplug wires but haven't looked for jaws for normal stranded wire. I would like an aviation crimper kit from DMC but I'm kind of cheap.
Thank you. I'm getting a lot more relaxed now. What about sources for loam or coverings? I saw people struggling to get a plastic mesh covering over a bundle of wires. Only to have it too thick to fit in the grommet.
Is it really bad to simply spiral wrap with electrical tape? Or long runs use heat shrink wrap? I recognize the plastic mesh looks tidy.
kb58
UltraDork
3/14/23 2:01 p.m.
The stuff to use is split mesh. The beauty of it is that you can add and remove wires anywhere along its length, which WILL happen! This is what it looks like: https://www.amazon.com/Alex-Tech-10ft-Protector-Sleeving/dp/B07FW3GTXB?ref_=ast_sto_dp&th=1&psc=1
I do not recommend any sort of spiral wrap or worse, the mesh tube type, because it makes adding or removing wires a pain.
frenchyd said:
codrus (Forum Supporter) said:
Building a reliable wiring harness requires fairly little in the way of direct skill, but at least a moderate investment in specialized crimping tools and a lot of time, patience, and attention to detail.
My fear is translation from Jargon and terminology.
How many hours did it take you to complete it?
I have not built an entire wiring harness from scratch, but a friend and I put together an ECU extension harness for my Miata. 3 connectors with about 20 wires each, 5 feet long to allow me to mount the megasquirt behind the glove box (where there was space) instead of under the steering column (where the physically smaller stock ECU went). It took like 6-8 hours of meticulous measuring, cutting, soldering (there was no crimp-on female connector available), crimping (on the other end), checking, double checking, testing, and then recording it all.
After all of that it worked first try and is still working to this day.
If you're doing custom wiring, to retain sanity you want to meticulously document EVERYTHING. Keep an excel spreadsheet with all of the cables, wires, colors, and meanings. I also highly recommend a label printer that can print on heat shrink tubing. I have one similar to this which is super useful: https://www.amazon.com/dp/B002M1HKLC/ref=sr_1_13
A label printer loaded with heat shrink is really handy. I've been using this one, it's a good value and has been rock solid.
DYMO Label Maker LabelManager 160 Portable Label Maker, Easy-to-Use, One-Touch Smart Keys, QWERTY Keyboard, Large Display, for Home & Office Organization, Black https://a.co/d/6ALN8Qj
I've got a couple of ratcheting crimpers, one of the generic blue ones you see everywhere (might be Blue Point branded) and one of these.
Wirefy Crimping Tool Set 5 PCS - Ratcheting Wire Crimper - For Heat Shrink, Nylon, Non-Insulated Connectors, Ferrule Terminals https://a.co/d/bWL3586
I'd recommend one with removeable jaws and get a few different jaws.
Electrical tape is my last choice for bundling because it's messy. That split loom is a good choice.
moto914
New Reader
3/14/23 3:07 p.m.
In reply to kb58 :
In reply to Keith Tanner :
In reply to codrus :
Great info. Bookmarked
In reply to Keith Tanner :
Thank you again. Great help!!
I've done two. One was a custom harness with all new wire that was coated with a fabric cover to look old. The tedium of tracing circuits when they all looked relatively the same was torture. Still, it turned out museum quality, but I never told the owner as he drove away that I noticed I must have mixed up the brake with the running light on the right side. Took me weeks, about a pound of butane, and about a mile of shrink tube.
The second one I did was in a 55 Chevy using an EZ Wiring pre-made harness. I crimped a bunch of stuff together, wrapped it with vinyl tape, and called it good. Lazy work, but I wasn't doing another multi-week custom thing.
The next one I do I want a big, single-point disconnect like this on the engine
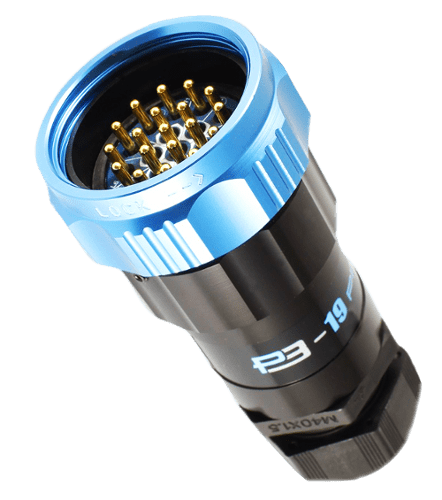
I can run up to 20A per pin, weatherproof, and (because it's used for theatrical lighting) stoopidly reliable. I'll run the alternator to the starter, so this way if I have to pull an engine I can just disconnect the hot and ground from the battery, unscrew this, and all of my electrical is done.
Curtis73 (Forum Supporter) said:
I can run up to 20A per pin, weatherproof, and (because it's used for theatrical lighting) stoopidly reliable. I'll run the alternator to the starter, so this way if I have to pull an engine I can just disconnect the hot and ground from the battery, unscrew this, and all of my electrical is done.
If it's an EFI engine then you'll want to be careful about running high-current switched (especially PWM or other square wave) power wires next to analog sensor signals.
Nylon split braid loom and the tesa fabric tape are the best bet for a diy job. I usually use closed barrel splices and my own shrink over, as I use offset size ones to do power, ground, 5v and sensor ground splits easily. The diagram in the micro manualis a good start to a base and you just add your particulars to it.
Motorsport grade harnesses are about $75 per input or output to ball park what you'd pay a pro.