After the latest flooding incident in my pole barn/workshop, I really need to get some repairs going or get a demo crew out (ideally after removing the cars).
I've been lucky in the sense that I haven't had to initiate major building projects while living in the US, but that leaves me basically with a head scratcher on how to find appropriate contractors or at least a general contractor. I'm assuming that your average residential builder probably won't touch a remodel of a pole barn and I need someone specialised?
The handyman/contractor I used before for some smaller jobs closed up his business around here so he's not an option anymore.
The way I see it, there are four distinct jobs that I need to get done:
- Fix the roof leaks for good. I've already had about 1/3rd of the metal roof replaced, but unfortunately during heavy storms the roof is still leaking, including at some of the replaced panels. At this point, if it needs reroofing, it needs reroofing and I need to get it done before the water does more damage.
Oh, and put some gutters on that roof as we discussed a few months ago to move the rainwater away from the building.
- The pole barn currently has three stalls, two have doors on them and the floor behind them is concrete, the third one is open and has a gravel floor. I'd like to have a concrete floor in there as well, with the necessary ratings to install a four poster lift (IIRC 6-8" thick and 3000-4000psi rated, but need to confirm that). Floor area is about 500 sq ft
- Once the concrete is poured, I need someone to frame the opening as it's currently 14' wide and that would be a tad expensive for a door. I'm thinking framing it in for a 10' wide roll up door, then fit said roll up.
- Put in a new side door that faces the house and close up the existing entry door opening as that's not visible from the house.
- (Very optional) frame in and fit a couple of windows if possible to get some natural light into the shop, assuming that that wouldn't be an issue with it being a barn/workshop.
So I'm guessing I need a GC who works on pole barns at the very minimum, and maybe also a concrete contractor, although I would expect that a GC would be able to arrange for that.
Am I missing something, and more importantly, how do I find these people as I don't really know anyone around here who has had people work on anything other than their houses.
SV reX
MegaDork
8/10/24 6:30 p.m.
In reply to BoxheadTim :
I don't see anything in that list that needs a pole barn specialist. It's just construction. Same as any other job.
Best way I know to find a tradesman/ contractor is to ask for referrals. First ask friends. Then ask on social networks. Then ask local supply houses for referrals (the guys that pay their bills are the guys who are also the most reliable). Also consider asking people in the inspection and code enforcement office. And design professionals like architects.
When I need a concrete contractor in an area I have no connections, I call the local concrete company and ask for a referral.
In reply to BoxheadTim :
Do you have any of these guys in your area?
You could also reach out to a local concrete company and see who they like to work with. You're gonna need concrete but the concrete company needs someone to tell them how much concrete.
I don't have any advice but have some questions. How was the roof done? Is it just metal over the rafters or was sheathing put under it? If so was ice and water shielding used? When it was repaired before what was the thought process of how to fix it?
Pole Barns. My love/hate life. I get way too involved in the job of converting pole barns into barndominiums or wonderful race shops. I will soon learn to say "NO!". 
First. Everything Sv reX said above. You need contractors/subs that pay their bills. Trust me on that. Be wary of folks that want a lot of up-front money. Most of us legit guys have enough credit and capital to be able to bill at "draws" or monthly.
Sometime you can find the best contractors from talking to managers of "real" lumber suppy businesses (not the big box orange or blue stores).
Were you the owner when the first roof was installed? That should not be happening. That is the first thing that has to be fixed correctly, or everything afterwards will be a problem.
When you wrote "flooding"... were you talking about water from leaky roof, or washing in at ground level?
Define for your contractor what you see as the finished project. Project scope creep on a step-by-step basis can get really expensive when we have to go back and re-engineer stuff after the fact.
Meanwhile.. next week i will be trying to frame an opening for a 14' foot tall roll-up door on a pole barn that was not originally designed for such door. LOL
Thanks everyone for your feedback and comments.
We're a bit south of Amish country, but not that far. Might be something to look into.
Yeah, I'm aware of the issues around prepayments. I've not done this with any contractors I've used and wasn't planning to start. Good to know I'm on the right track with that.
Re the roof - the pole barn is likely > 20 years old and a proper pole barn built using old utility poles. It has a simple galvanised steel roof on it that had started to rust through in places. We discovered that before the closing and the PO paid for a local contractor/handyman to "fix" it. The less said about that fix the better.
The roof construction is pretty simple - rafters between the poles, then purlins across and the roof sheets are screwed onto the purlins. No vapour or radiant barrier, I can see the steel sheets from the inside of the building.
After the initial repair that didn't work, I got a referal from one of the local-ish higher end contractors for one of the subs they use for smaller jobs. He ended up replacing about 1/3rd of the metal roof panels which fixed the rainshower inside the garage almost completely. However, from what I can tell after Debby came through, there are several new roof leaks as some of the purlins were soaking wet (at least from a visual inspection) and dripping water. Plus, there is also some water coming in at the back of the building (wall gets wet in heavy rain) that also looks like it's coming in through the roof.
I also suspect that there is some water being pushed in under the two garage doors if the wind and rain hit is just at the right angle. I've got new garage door bottom seals that I'm planning to install soon, and put in new side and top seals a couple of years ago. The insides of the doors themselves are dry, but it looks like some water is pushed in in the bottom corners of rhe garage doors.
I know that there is some issue with condensation as well, which is probably due to the exposed metal roof. That mainly manifests itself in higher humidity in side the building than outside.
Getting the roof fixed for good is definitely the highest priority and the first part I need to get addressed. Second highest priority is to get gutters fitted after the roof is watertight.
SV reX
MegaDork
8/10/24 8:38 p.m.
In reply to Purple Frog :
You and I were thinking the same thing. "Flooding" to me doesn't usually mean a bad roof- it means bad drainage.
In reply to SV reX :
What I meant by "flooding" is enough water ingress to leave standing water in the shop. On Friday morning I vacuumed up about 13-14 gallons and mopped up the rest. The area the shop is in has a drainage issue and there is occasional standing water there on the lawn, but the levels of the water are below the level of the floor.
I know some of the water is coming in through the roof, but I'm not sure where the rest is coming in from. Plus, the roof leaks definitely got worse again.
SV reX
MegaDork
8/10/24 8:42 p.m.
In reply to Stampie :
Pole barns almost always have metal roofing over purlins (or furring strips). Generally no sheathing. But your right- in WV if sheathing was used, ice and water shield would be a good idea. (Unless it's a water barrier sheathing)
I agree with you.. the repair should not have failed.
SV reX
MegaDork
8/10/24 8:51 p.m.
In reply to BoxheadTim :
Is there anything complicated about your roof? Valleys, corners, pipe penetrations, varying heights, etc?
Pole barn roofs are typically extremely simple gable roofs. It's hard to make a simple roof leak badly. That makes me suspect your grade or drainage.
Perhaps the roof can be repaired properly, save you the cost of a new roof, and then deal with a drainage issue?
In reply to SV reX :
One chimney sticking through the roof, other than that it's a big rectangular shed roof that's angled down towards the back of the building. As far as I can tell, it is not leaking at the chimney. There shouldn't be any complexity to it and I am hoping it can be repaired properly rather than removed and replaced. Some of that is of course assuming that I don't have to get all prior repaired sections removed because that's at least a third of the roof.
I did notice that the purlin at one of the new leak sites looks like it split, but the other ones in areas I've found leaks in appear to be intact.
Hurricane or tropical storm Debby? That could have been a lot of water and wind pushing it the wrong way against the seam overlaps and water can easily be forced around the seams on the roof and walls. The cure would be to install seam mastic tape during install. Silicon caulk works also and can be applied after the fact by removing all of the seam screws on a panel and caulking while somebody runs a strip of wood ahead to spread the seam. The overlap seams should be cleaned of any oil with something like alcohol, or if really oily, paint thinner and then alcohol to clean off the paint thinner residue.
metalconstructionnews.com: Caulk and Sealant Guide
Tale of the Tape
Butyl tapes are most commonly used to seal the side- and end-laps of standard single-skin panels. Butyl tape is a non-curing, 100-percent -solids compound that is a highly rubbery, tacky sealant which remains permanently flexible. Butyl tapes are packaged in rolls or strips with a removable release liner for easy handling and application. Butyl tapes are soft and pliable and are designed to compress between overlapping panels to form a positive seal. With elongation values greater than 1,000 percent, butyl tapes can last for 25-plus years and are compatible with all painted metals including but not limited to Galvalume-, Zincalume- and Kynar-coated products. With application temperatures between -5 F to 120 F and service temperatures from -40 F to 200 F, they are routinely used in all climates. Although butyl tapes exhibit excellent UV characteristics, proper application would not require them to be exposed to direct sunlight. Also, antimicrobial additives are used by some manufacturers to inhibit the growth of molds and mildew.
go-rsp.com: Strip Mastic 1/8″ x 50′ Mastic Strip
Edit: I just read where you said the roof is a single plane roof, what is the roof pitch? As far as I know, ribbed steel roofing is only rated for a 4/12 pitch or greater without strip mastic.
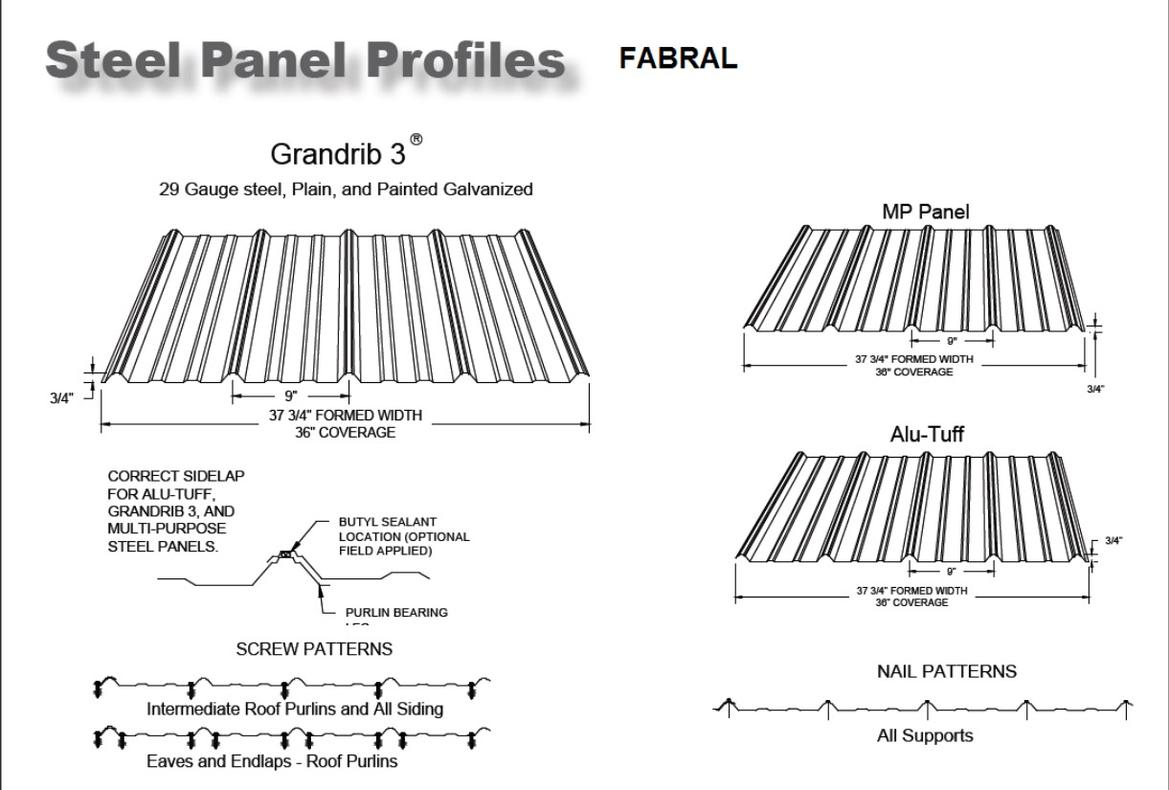
SV reX
MegaDork
8/10/24 10:45 p.m.
VH raises a good point. Metal roofs on purlins aren't always 100%. Expansion/ contraction, screws working loose, lack of seam tape, etc. Pole barns often aren't expected to be 100%... 97% will sometimes suffice.
How is it screwed? I've seen a lot of metal roofs (especially in the North) where the screws are installed in the ridges (ribs) of the metal. That's incorrect. They should be in the low (flat) parts of the metal. They should technically also be screwed next to each rib, not halfway between the ribs (although 99% of roofs are not installed this way).
Its possible your roof needs to be re-screwed with new larger screws. This is common.
13-14 gallons of water is a lot. There should be a visible failure point if the "flood" problem is the roof.
WV... mountains... I'm still thinking grade/ drainage.
SV reX
MegaDork
8/10/24 10:53 p.m.
The reality of strip mastic tape is that it makes installation really hard. You can't make minor adjustments in the panels before screwing them down. So it's usually ignored.
I actually asked my metal roof supplier about this this week. He said they rarely actually sell the mastic tape. Only on architecturally supervised jobs.
(This is rural GA/ AL)
In reply to SV reX :
I agree, and why we only used silicon caulking on the seams. We also used stitch screws along the seam rib to physically compress the panel seams together (which I liked a lot because if you ever slipped on an oily wet roof, the screw heads where you last chance of not going over the edge.) We would use two needle nose vise grip pliers at the bottom and top of the panel seam rib to keep everything aligned and straight.
Edit: I only have worked on Pre-Engineered steel building. However, I have designed a dozen or so engineered wood pole structures, several with one or two story living quarters inside or on the engineered fix of a 400'x100'x18' farm equipment shop that was tipping over.
SV reX
MegaDork
8/10/24 11:24 p.m.
In reply to VolvoHeretic :
Correction...
If you ever slip on an oily wet roof, your SAFETY HARNESS will keep you from going over the edge!!
I found three areas of the roof where water was still dripping from what looked like soaking wet purlins several hours after the severe storms had passed. While the storm woke me up, I didn't think of checking the shop building, otherwise I'd know for certain where the water came in and how much.
I'll have to get up on the roof to check how the new panels are screwed in; I know the old ones are screwed down next to the ribs, not on the ribs.
I'd have to check the roof pitch, but assuming 4/12 means a 4" drop over a distance of 12", my guesstimate is that it's very close or less than that. I'm also 99% confident that the original panels were installed without strip mastic tape and I don't think the replacement panels were either.
It certainly felt like a lot of water, even for a shop that's roughly 28'x29'. And that's not taking into account the water I couldn't get at with my wet/dry vac and used my big fan to dry it out.
Im not ruling out drainage being part of the issue, but I didn't see much in the way of obvious signs of water ingress at the bottom of the walls.
In reply to SV reX :
Lol, I don't think that safety harnesses where invented back in the 70's, at least not in ND. 
In reply to BoxheadTim :
If the wind was blowing at the O.H. Doors, the square footage of each door times the amount of rainfall in feet would try to blow under the doors no matter how good of a seal you have under the doors, it could easily equal 14 gallons. So, if just one inch of rain fell: 1" = 0.083' x 14' x 10' = 11.66 cubic feet of water per a 14'x10' door. 1 cubic foot of water equals 7.5 gallons x 11.66 cu ft = 87.5 gallons per door trying to get in. This is assuming that the outside concrete beyond the doors is flat and not tapered to the outside edge. 
I would replace the panels with full length standing seam panels attached to the roof framing with clips. No laps.
..if I had to have laps I'd use butyl sealant. If it had to be a corrugated panel I would not do what SVRex said and I would 100% drill through the high points and not the valleys. Because water runs in the valleys.
SV reX
MegaDork
8/11/24 1:09 p.m.
In reply to OHSCrifle :
If you do that, the warranty is void.
The problem is that there is nothing solid behind the ribs. You are not screwing against solid backing, and the neoprene washer can't compress properly. The finished attachment is hanging on the screws with 1" of air space under it- no good.
The ribs can be screwed additionally with stitch screws, but those are metal to metal only. They don't screw ti the substrate at all.
SV reX
MegaDork
8/11/24 1:12 p.m.
In reply to OHSCrifle :
I just priced standing seam vs ribbed roofing with exposed screws for my own house. The materials were 3X the cost, and so was the labor. That put the price significantly out of reach.
I did, however, use custom full length panels with no lap joints. (Though I really see no issue with a properly done lap joint)
In reply to SV reX :
That labor delta makes no sense.
Curiously.. in Australia the corrugated panel has to be screwed on the ribs to comply with their building code. Maybe because they're on the other side of the planet gravity is different.
SV reX
MegaDork
8/11/24 2:18 p.m.
...I actually noticed while I was at the manufacturing plant ordering my roof that the roof on THEIR building was screwed in the ribs. I got back out of the truck and went inside and asked....
The rep told me "Well, some guys screw in the ribs, and some guys screw in the flats. But if you screw in the ribs, the warranty will be void".
I thought that was humorous!
I then double checked the manufacturer's specs- they said NEXT TO the ribs.
In reply to SV reX :
To me it is like nailing shingles in a valley. No thankya.
Edit: I agree that's funny about the manufacturer's own building. I also strongly disagree with metal roofing manufacturers who say oil canning is inevitable. If you give it room to grow and shrink based on the known coefficient of thermal expansion (including noting the air temp when you install it) you can have great success. If you DGAS.. you won't.