RedGT
HalfDork
12/19/16 8:05 a.m.
A friend of mine picked up an old Grizzly lathe about 8 months ago. He has since upgraded to a full size industrial unit. Tooling...Don't buy it new. Between craigslist and bidspotter.com he has found everything he will ever need for pennies on the dollar. At least around here a lot of old traditional machine shops are shutting down. It's depressing, but economical for people like us.
It's really a catch-22. I work with both professionally (cutting tool designer), and my very shortened opinion is as below-
-
If you're on a budget and want to keep things simple and make simple-ish things- Lathe, 100% of the time. The learning curve is easier, and the quality of the 'entry level' units are 10000x better than the similar $ for $ quality of a mill.
-
If you are willing to spend some money and turn this into a long term relationship- Buy a production quality manual mill and slap a rotary table on it. Or go further on the investment path and buy a CNC mill and learn solidworks and G-code. You'll be able to make pretty much any and everything you can bolt onto a car with that setup.
That's my easy button- A used robodrill. Cheap buy-in relative to what you're getting, unlimited parts availability, can handle anything from manual G-code programming to complete Mastercam and post-process logic, robust enough for most materials, and accurate as hell if not beaten to crap.
I have both and I use the lathe for car stuff more often than the mill but I think that once you get into it you're really going to want both.
tuna55
MegaDork
12/19/16 10:22 a.m.
I want, badly, but lack in skill and dollars.
I'll say this, I had nearly free access to both in a neighbor's garage, and he not only made me look like monkey-football, but also somehow didn't mind that I broke many of his expensive tools for the mill.
So learn! I didn't, and I'd be pissed about breaking stuff.
In reply to Huckleberry:
There are a couple ways to cut a straight keyway on a lathe without a milling attachment. Get the part chucked up and dialed in, lock up the spindle, make a form tool to keyway dimensions and manually run the carriage back and while feeding the cutter in a few thou per pass, kinda like a shaper or a slotting head. Or for outside keyways only you can make a V block to either fit into or in place of your tool post and chuck up an endmill.
Between the two: Lathe.
You may want to explore other metalworking avenues though.
I could make more and more varied stuff with a welder, angle grinder and hand drill.
Also, lots of cool stuff done with sheet metal nowadays. Check out some of the guys doing beadrolling.
Lots of components in the mcmaster catalog you might be tempted to make if you haven't seen the selection.
Reading the lathe and mill thread with the home foundry thread has all sorts of ideas bouncing in my head. I should probably just clean my garage enough so I can walk in it, first.
I'm in the combo machine camp. I started with the entry level Smithy, and that was good for a lot of things. I got tired of the lack of rigidity and power crossfeed so I sold it and got the higher end Smithy combo machine.
When I started with the first machine, I assumed I'd use the mill most, but I was very wrong. I use the lathe much more often. With the sturdier machine I have even done a lot of weight reduction machining on the front hub/rotors for the race car (Firmula Ford).
The trade off between versatility and footprint of the combo machine vs one or multiple dedicated machines has worked out well for me.
I have of course experienced the slippery slope. I now have a DRO, and that is a great addition.
pkingham wrote:
I'm in the combo machine camp. I started with the entry level Smithy, and that was good for a lot of things. I got tired of the lack of rigidity and power crossfeed so I sold it and got the higher end Smithy combo machine.
When I started with the first machine, I assumed I'd use the mill most, but I was very wrong. I use the lathe much more often. With the sturdier machine I have even done a lot of weight reduction machining on the front hub/rotors for the race car (Firmula Ford).
The trade off between versatility and footprint of the combo machine vs one or multiple dedicated machines has worked out well for me.
I have of course experienced the slippery slope. I now have a DRO, and that is a great addition.
I am in the combo camp as well. I have the midas smithy got it probably 10 years ago now and don't regret it a bit. I looked past all the "pros" on the various forums that are a get a bridgeport or nothing camp and decided that for 99% of what the hobbyist does, the combo machines are perfect. Transitioning from mill to lathe is not that bad either and made even easier in the machines they sell now. The new machines have separate motors for mill and lathe. After having this machine for so long now, I would actually prefer the Granite series mainly for the y axis power feed, but mostly for the R8 taper in the mill, as it is far easier to find attachments for this taper. (especially for used stuff from machine shops going out of business) The other downside to the midas is having to change the gearing for the different threads as well. if you think you might want to upgrade later get the granite series from the start. Initially I used the lathe more, but since I've made AR 15 lowers from 80% receivers I've used the mill more. As far as combo units go, get a grizzly or a Smithy, they are much better then the Harbor freight units and you get a lot more customer support as well.
Chris Rummel
I was given a used (rear nearly used up) harbor freight combo machine for free. The money I have in tooling is well above the cost of a better combo machine. I suggest the combo machines as they will get you started and take up less room. They do have the downside of less working space and lower rigidty, but for most things they will work well, if you take your time. Make sure you get something that has threading capabilities, as that is the part I find myself needing the most when I make one-off stuff.
I think the lathe is used about 70% of the time, as others have said.
Ian F
MegaDork
12/20/16 3:36 p.m.
You mentioned making small widgets. Micromark makes tools for model-makers. Or widgets. My ex- has a few of them she bought to make dollhouse furniture.
I also have a Taig lathe with a Z-axis that bolts onto the cross slide to turn it into a very small x-y-z mill. I also end up using the lathe about 3x as much as the mill, but I think you need both to be completely satisfied. I'm space limited in my shop, so the tiny hobbyist Taig works great, but if I had more space I'd buy an old 6" lathe with a 3' bed and a standalone mill.
Update: I was talking to my brother in law over the holidays, he makes stuff out of wood when he's not running a nuclear reactor, and mentioned that he had an old bench top metal lathe. He picked it up at a garage sale just because and did I want it?
Yes, yes I do.
Picked it up today. It's an old Craftsman, 1/3 hp motor, three jaw and four jaw chuck, a billion other things in two drawers. I'm excited to get it home and see what I have and make stuff. More to follow.
Good God im jealous. Looks to be a late 50s model.
Looks like it has all the change gears and little wear, make sure you lube it up before running it to keep it that way. As a rule of thumb you've got too much oil on a machine tool when it starts dripping and throwing it off, some lube points should be hit before every use. I'd guess late 40s or maybe early 50s, it's not an Atlas (a good thing to many people), you can probably figure it out and find info on it at vintagemachinery.org.
Nice find.
Not to derail this thread, but does anyone have experience with mini lathes? I'm looking at this one pretty much for the price alone.
"Theoretical clamping length 18cm, clamping width 7cm" not huge, but big enough to play with
79rex
New Reader
12/29/16 9:26 p.m.
You can always turn parts on a mill with a boring bar in a good boring head. Turn the bar so the insert faces oppsite of boring an ID, then run the spindle in reverse. if it were me id get a mill.
qued
New Reader
12/29/16 9:46 p.m.
Craftsman 109 it looks like. I have the atlas 618 of similiar vintage.
RevRico wrote:
Nice find.
Not to derail this thread, but does anyone have experience with mini lathes? I'm looking at this one pretty much for the price alone.
"Theoretical clamping length 18cm, clamping width 7cm" not huge, but big enough to play with
That's more or less a tiny wood lathe, not for metal work.
Wow, that worked out well! That lathe looks awesome. A properly aged machine tool is a thing to truly enjoy.
Here is some light reading for you:
How fast should it turn? Not lathe specific but the same rules apply.
What your tool should look like.
Edit: I'm sure you know this, but it's a good habit to get into- the only time the key is in the chuck is when your hand is on it. 
codrus
SuperDork
12/29/16 10:44 p.m.
I dunno how often you go to Austin, but if it's practical you might take a look at TechShop. With a monthly membership you get access to a ton of machine tools at their various locations (many in California, a few around the rest of the country) and they also offer classes in how to use them. It's a pretty good way to play with this kind of stuff without requiring a huge investment up front.
(Not just machine tools, either. They have a bunch of other cool toys, CNC laser and plasma cutters, woodworking tools, etc)
BrokenYugo wrote:
RevRico wrote:
Nice find.
Not to derail this thread, but does anyone have experience with mini lathes? I'm looking at this one pretty much for the price alone.
"Theoretical clamping length 18cm, clamping width 7cm" not huge, but big enough to play with
That's more or less a tiny wood lathe, not for metal work.
I was kind of afraid of that. What's the difference between a metal and wood lathe? Speed, torque, something else?
I'm still thinking about this, as it could be useful for making wooden patterns for metal casting, but I was hoping it would be good for cleaning up casted objects too.
In reply to RevRico:
A metal cutting lathe has a rigid means of holding a cutting tool, precision means of moving it and in the majority of cases the tool can be synchronized to the spindle for thread cutting. A wood lathe just spins the work and offers a place to rest a hand held chisel.
This is a typical mini metal lathe. The three handwheels are used to move the bit around, from the bottom up, parallel to the work, perpendicular, and at an adjustable angle. The lever on the lower right corner of the carriage is for connecting the carriage to the screw (which is geared to the spindle) for power feeding (only cheap lathes use the screw for this, better ones use a keyway cut in the screw or another shaft entirely to reduce wear on the screw and "half nuts") and thread cutting.
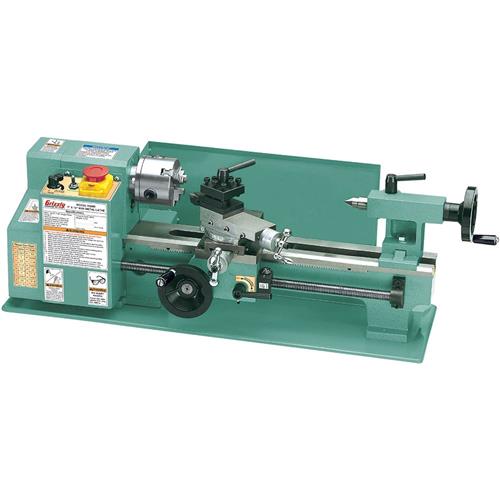
This old MIT video series is pretty commonly shown to engineering students and such as a crash course for the machine shop.
https://www.youtube.com/embed/Za0t2Rfjewg
I have a "Quick & Dirty" series of super short videos that show all the basic procedures of the lathe that I use in my metalwork class.
Starts here at Facing, and works through tapering, drilling, internal threading, knurling, etc. I haven't done external threading yet, because most kids can't do it.
SkinnyG's Lathe Vid Play List
Don't put your fingers anywhere you wouldn't put your hootus.
In reply to SkinnyG:
I'll be watching those videos. And the MIT ones. So far all I've done is move the lathe from my BIL's porch to the truck, drive it back to my in-laws, and take a picture for you guys as I moved it to the back of the bed before stacking the detritus of two weeks worth of Christmas vacation all around it for the drive home. I'll probably start a Mazdeuce machines stuff thread in the build section to log what I'm doing and ask for more help.