I ordered two valves and two guides for the offending cylinder from California and waited about a week for them to arrive, only to find out they sent the wrong valves so I waited another week for the right ones to show up. This project continues to have delays like that, but I guess it's okay since it's the double emergency backup truck and the regular truck and the emergency backup truck are doing fine.
I'm posting a lot of detail photos because I couldn't find good photos or videos on the internet. There are a lot of decent books for flatheads, but most are pretty old and have poor photos. So, maybe I can help the next guy doing this as the GRM message board comes up a lot in google searches.
Anyway, I installed the valves and guides in the block without the springs and lapped them in using valve grinding compound and a suction cup tool.
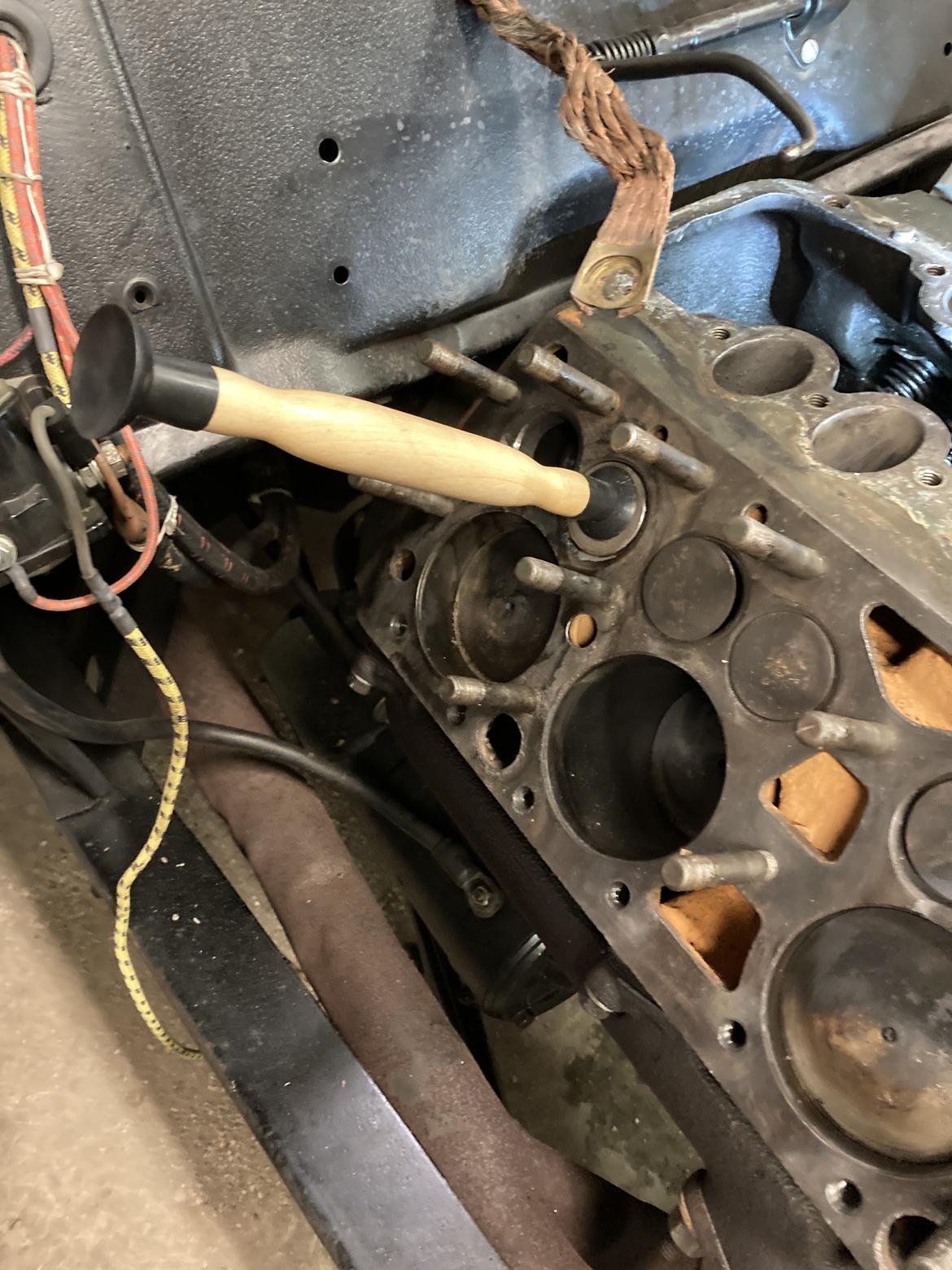
I would have liked to see a little more contact, but the seats aren't that good, so that's all I could get. Lapped valve is on the left. New, unlapped valve is on the right.
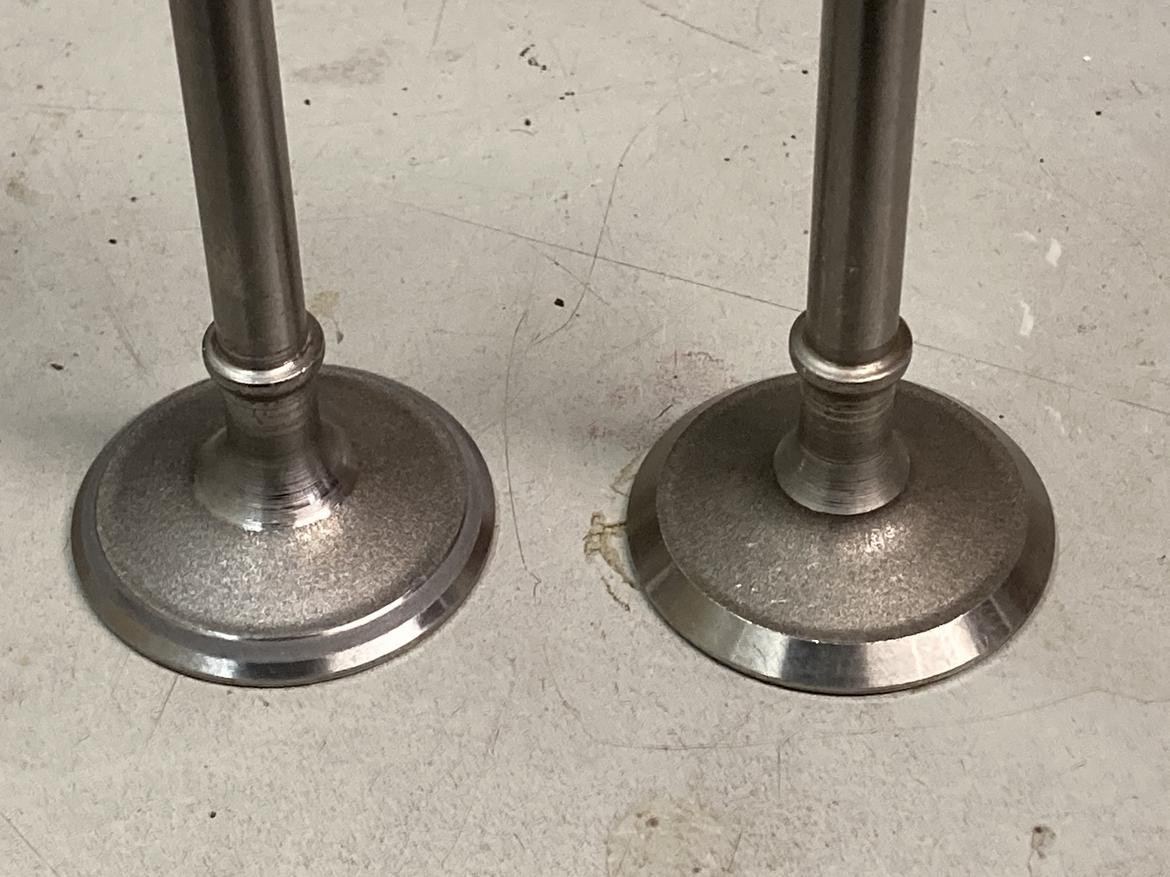
This is a pretty good comparison of the new guide half to the old one that had rusted away at the top. Amazing.
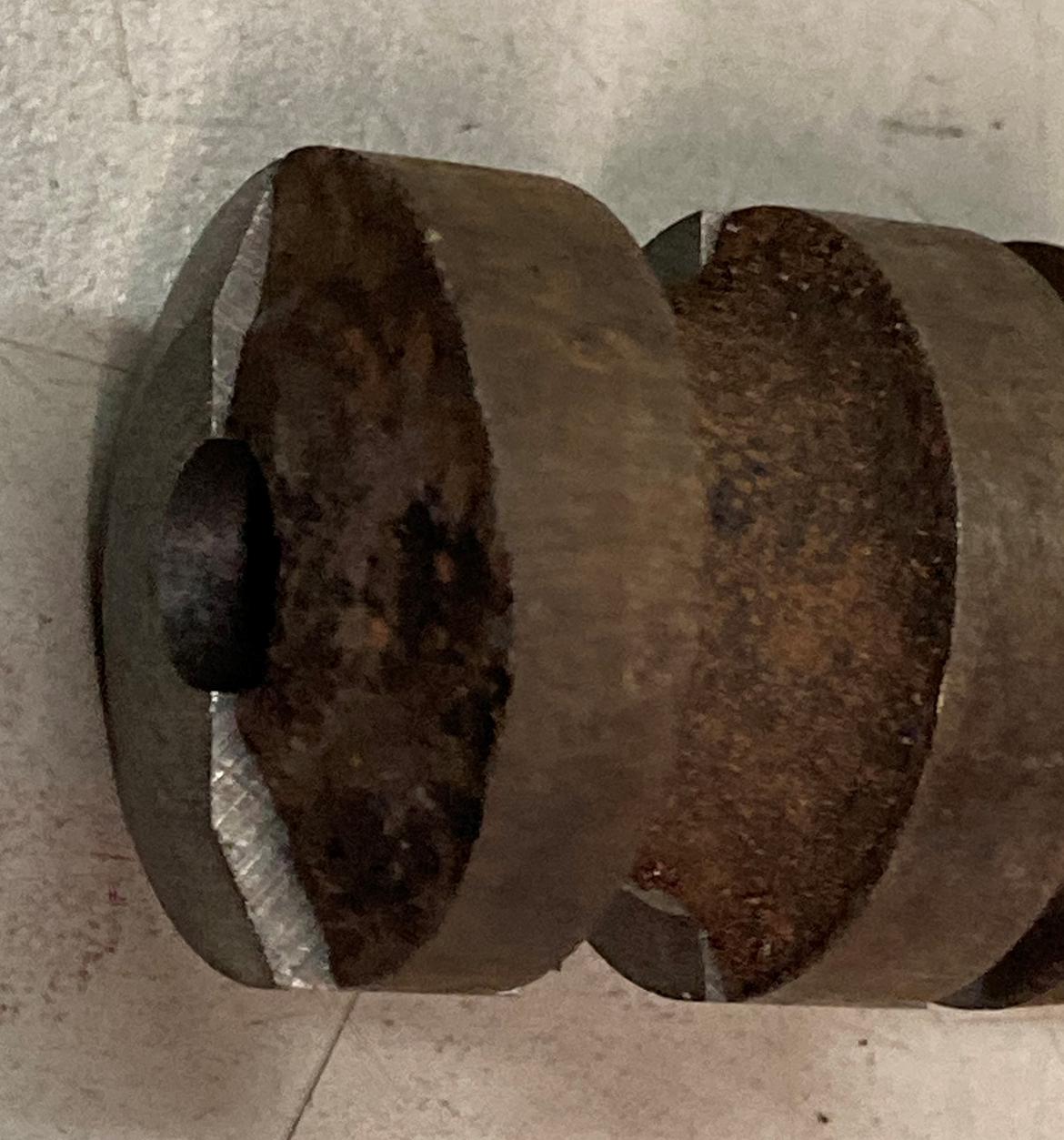
Here are all the parts laid out. The guides are split. They get put together around the valve, then the spring and keeper go on.
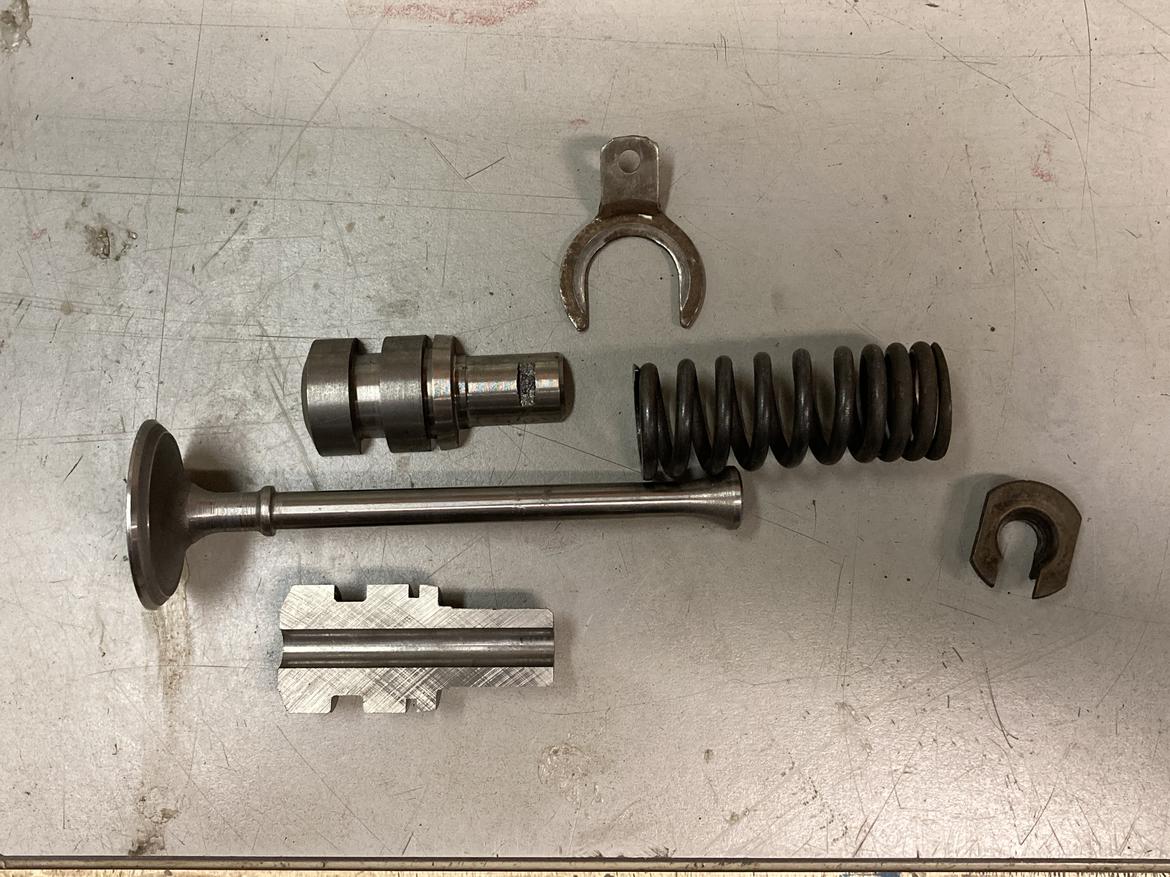
And it turns into something like a cartridge that installs from the top. Once installed, the "C" clip with the tang on it holds everything in place.
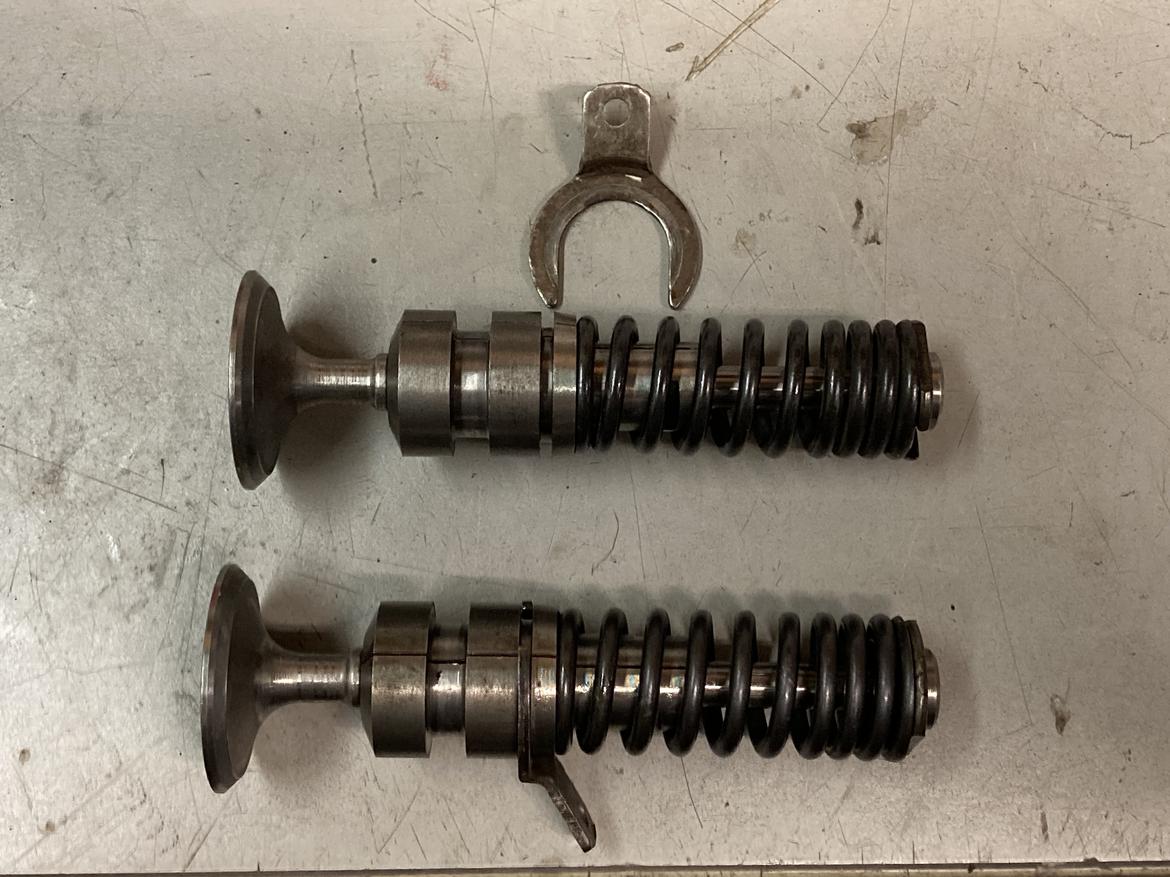
The valve "cartridge" installs from the top of the block through the valve seats/ports.
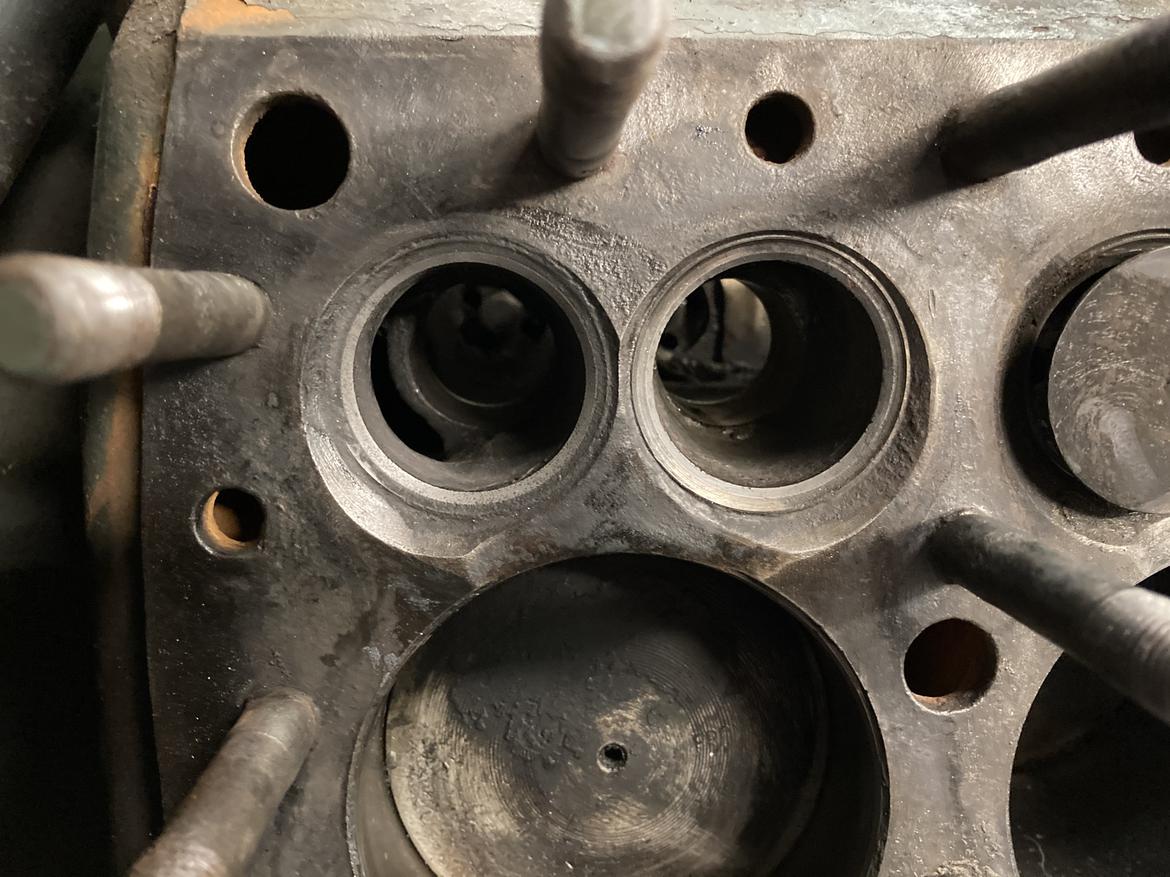
This Offenhauser tool was really helpful. It's sort of like a pickle fork and locks into some grooves in the guides. It's really long because it takes a lot of leverage to get the guides pried out. It's also useful for installing the guides--pulling them down far enough to get the "C" clip installed.

Here's the business end of the tool, pulling down the valve guide to install the "C" clip.
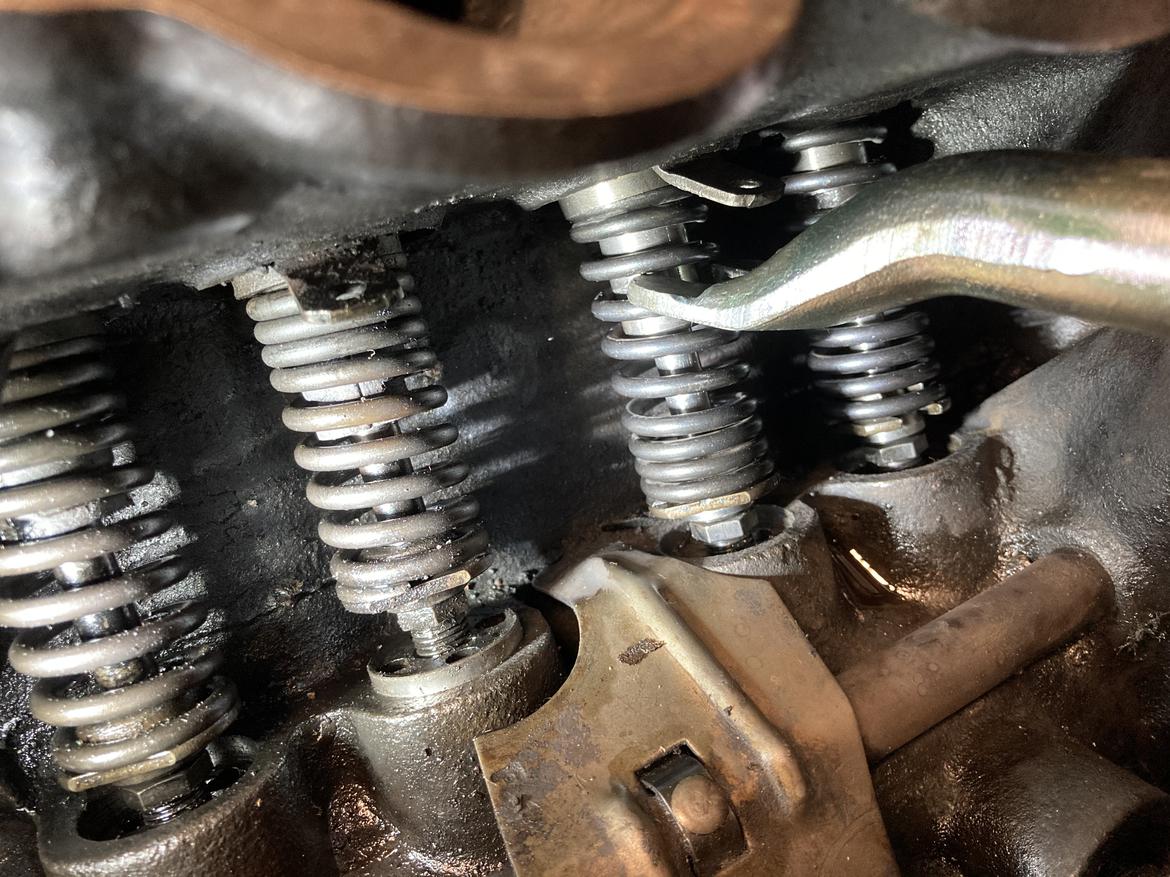
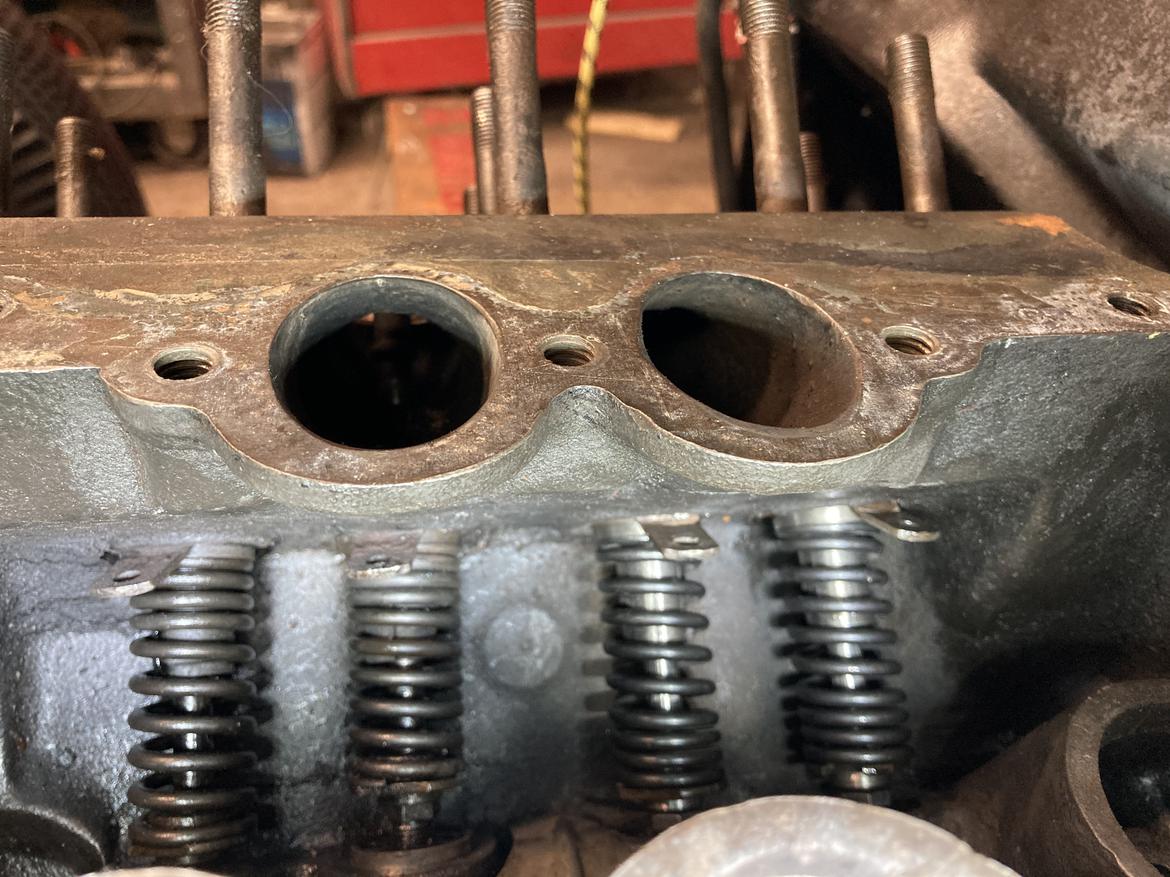
Another detail picture showing the "C" clips installed. The valve spring pushes them up into the guide bore and keeps them from falling out. One I installed the valves, I realized I installed the springs upside down. I don't know if it makes a difference, but it was fast enough to take things apart and make them right. Karma sure is funny with this project. It went together so quickly when we built it, but it's going slowly for the maintenance.
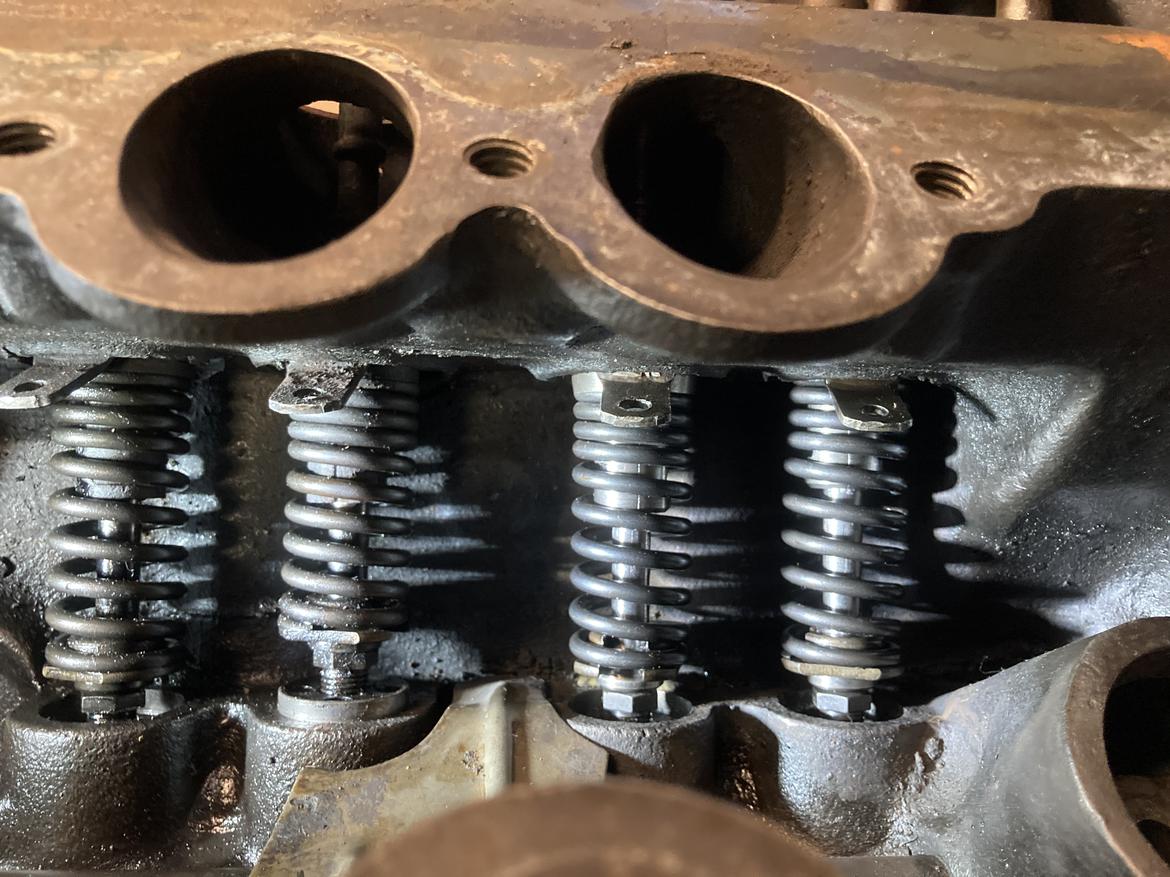
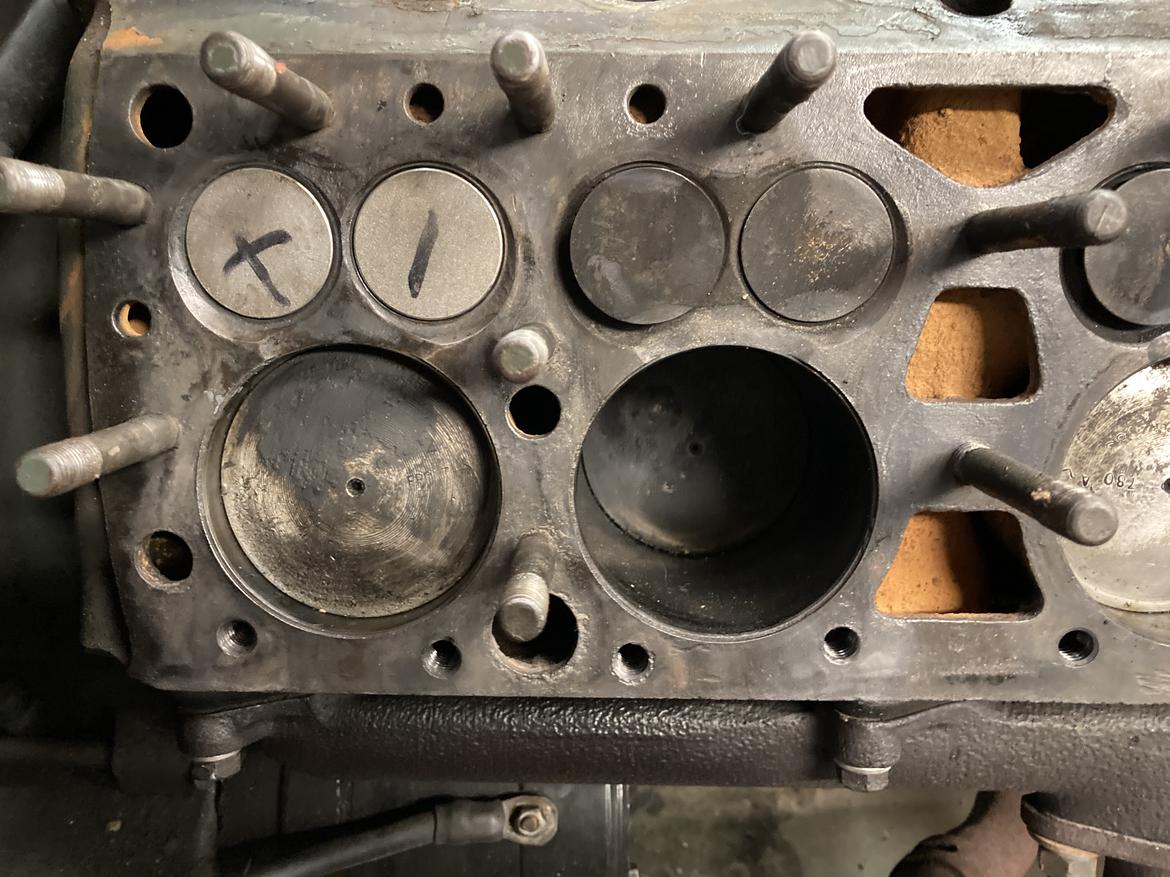
I've got it all ready for final cleanup, stud installation, and then the heads. I'm sure that I'll have my share of leaks for the first 50 miles and 5-6 retorques, but that's hot rodding.