I had a big 45DCOE Weber on an MGB-GT. Went like a bat out of hell at high revs, but got terrible fuel mileage and wouldn't pass emissions no matter how I tweaked it. I've had MGs and Triumphs with S.U. carbs for years, and found that you could pretty much set and forget them. They say 99% of carb problems are electrical... go through the usual tune-up procedure and generally the "carb problem" goes away before you actually touch them. Altitude is another matter. Add 5,000 feet elevation and adjustments will need to be made. Short term, bump the idle so it won't die at every light. Long term, you'll have to lean out the mixture too. Still, they're the carbs I know best. And Zenith-Strombergs are just the same carb with all the patents bypassed as best they could. I'd prefer S.U.s, but I think I can learn to live with the Z-S carbs. Since I have four of them, I should be able to set up a pair for the TVR. Heck, maybe even get Mr. Good's triple-carb manifold and use three of them.
Sounds like you've got the SU carbs pretty well in control. Go with what you're good at, right!?
I've got a *BIG* SU that was on the turbo set-up on my carb. I can check the size if you think you might be able to use it.
I would bet it's an SU HD8. I'd need a couple of HS6s to replace the Z-S carbs.
Change of subject: I'm starting to put my steering rack together, and was thinking about its lubrication. You know, the old "grease vs. oil" controversy. It seems that MG always said to use 90EP oil in the rack, but Triumph says grease, even though they were from the same manufacturer. So, being a Triumph rack (and having grease and a grease gun) I guess I know what I'll use. But my research into that controversy led to the trunnions, where apparently every manufacturer says use oil. Even though there's a grease zirc fitting. Now, I've always just shot grease into them every time I did a lube & oil change, on MGs and Triumphs over the last few decades, and I've never seen any adverse issues as a result. But the explanation as to why you should use oil seems very rational... but I really don't want to take any of that stuff apart yet again to do it "right" if doing it wrong isn't going to cause any issues. So, Brit car guys, what are your thoughts regarding trunnions?
Len Renkenberger, founder of 6-Pack, used to say that Triumph got this wrong. He would put 90w oil in the steering rack and grease in the trunnions. I've followed his advice for 30 years and had no problems. His main reasoning is that there is no way shooting grease into the rack at the pinion will result in lubrication at the far end of the rack. I think the oil tends to soak into the tie rods better, too. The only downside I can think of is the mess if a rack gaiter tears, but those are easy to inspect.
To put oil in the rack, I use an empty grease cartridge, put some oil into it, and pack some grease around the plunger. Put a grease fitting into the pinion cap and pump away. It makes a little mess, but works.
BTW, this may be a useful link if you aren't already aware of it. Except that they want $30 for it. Len daily drove TR6s for thousands of miles, so I trust him over the factory.
http://tvrccna.org/catalog/product_info.php?products_id=68
Slow_M
Reader
9/30/20 10:24 a.m.
TVR Scott (Forum Supporter) said:
Two TR6 motors in series? That would give you an easy 300 hp.
A 300 hp N/A motor sounds like a hand grenade in the worst way.
Friend of mine did that with Jag 6s.
https://m.youtube.com/watch?v=SFl0wmwPYq8
My lord! That's what I get for joking about real-serious-things!
So how'd he do that? Some sort of coupling between cranks?
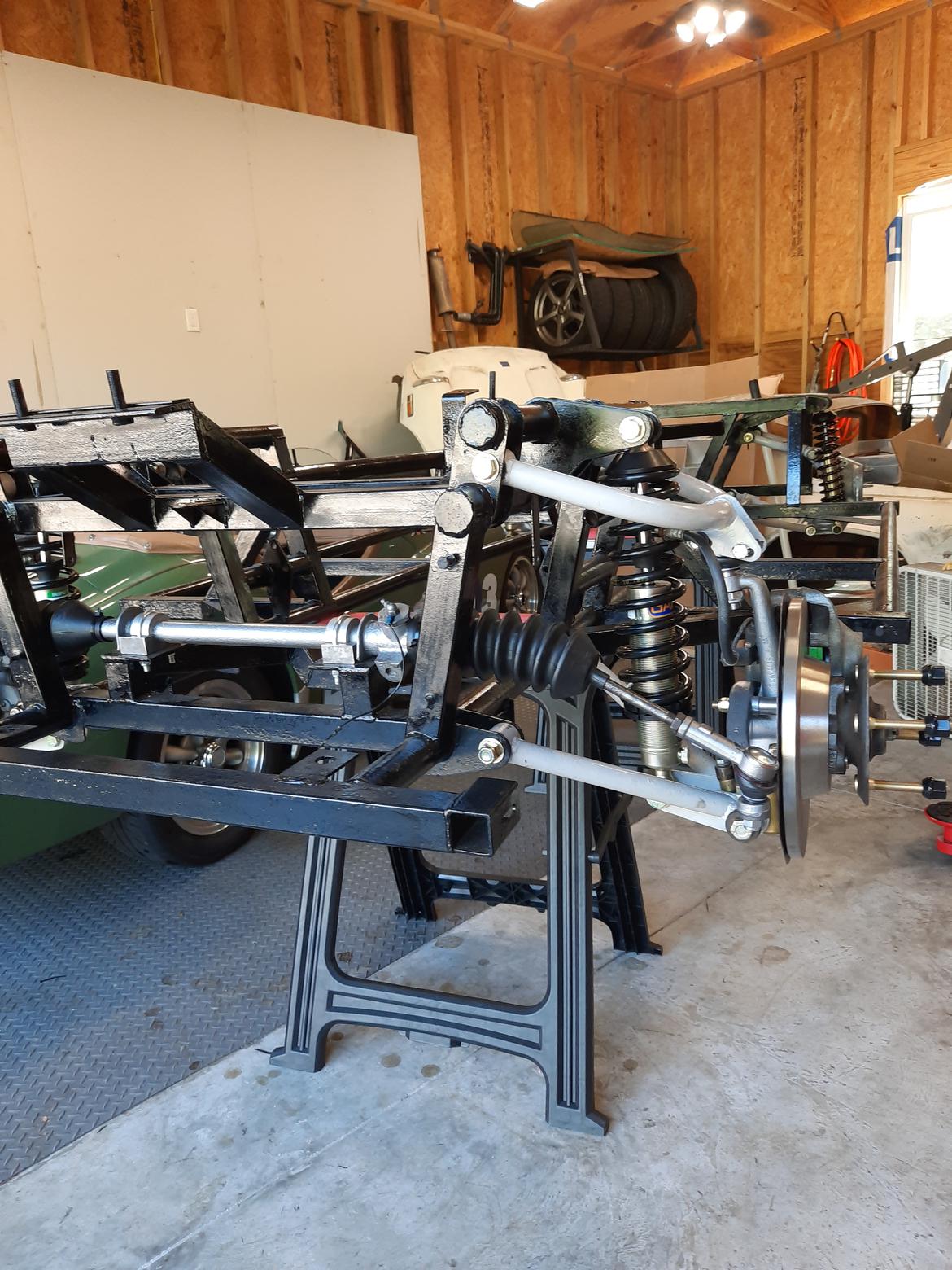
I know I haven't posted anything for a bit, but I haven't been completely idle. I got the steering rack cleaned up, lubed, and installed with new rubber gaiters and ball joints. I want to get started on modifying the differential mount for the R200, but until I have it I won't know how to approach it. I still haven't ruled out cutting a section out of the frame and welding a reinforcing section below the cut-out... that would keep the original alignment with the gearbox. Scott's approach (raising the diff by modifying the mount) would be easier, but I worry about how that would affect the u-joint angles. I don't want to have to modify the engine mounts or transmission mounts to adjust for it. Again, I know there's a solution, but I want to see just how much adjustment will need to be made. Who knows, I might be lucky... it seems every TVR is different!
Looks good!
Did you find the tie rods limited the amount of droop on your front suspension? I've been working on mine, and it was limiting travel enough that the shocks wouldn't quite line up.
On the diff install - raising the nose of the diff like I did made the pinion angle about 2-1/2 deg. Just meas....
<ninja edit!>
I was going to say to check the angle on your transmission, but it's clearly not there. So I don't know what to say about that.
In reply to TVR Scott (Forum Supporter) :
Nope Scott, what you see there is full droop, at least as allowed by the shocks. But I had the shocks on first, before adding tie rod ends. It looks like I've got toe-out, even though I'm down to about 1/2" of thread left on the rods. I'm hoping that it's because of the suspension droop, and I'll have more room for adjustment when it's on the ground and fully weighted.
As to the diff install, I noticed that you say that you took about 3/4" off the front mounting pads... is there more room for adjustment at the rear, or did that not throw off the angle all that much? I would have thought all four mounting pads would need to be cut down. As you noted, I won't know what kind of angle tolerance I'll have until the engine/gearbox are in place.
Hooray! As of last Saturday I now have my R200 differential (thank you Patrick, and Chandler for delivering it). Now I just need to clean it up a bit, figure out how to get the seized
on axle shaft removed, and a few minor modifications (as per Goodlparts instructions). THEN I can try it and see how it hangs in my chassis. I'm still hoping I won't need to do as much as Scott did... one difference in my favor is that the TR6 driveshaft and joints are smaller than the Nissan components, so I shouldn't need 3/4" like Scott did. We'll see.
In other news, the rear hubs and brake assemblies are installed, so even without the diff installed, I can put wheels on it and it becomes (drum roll)... a rolling chassis!
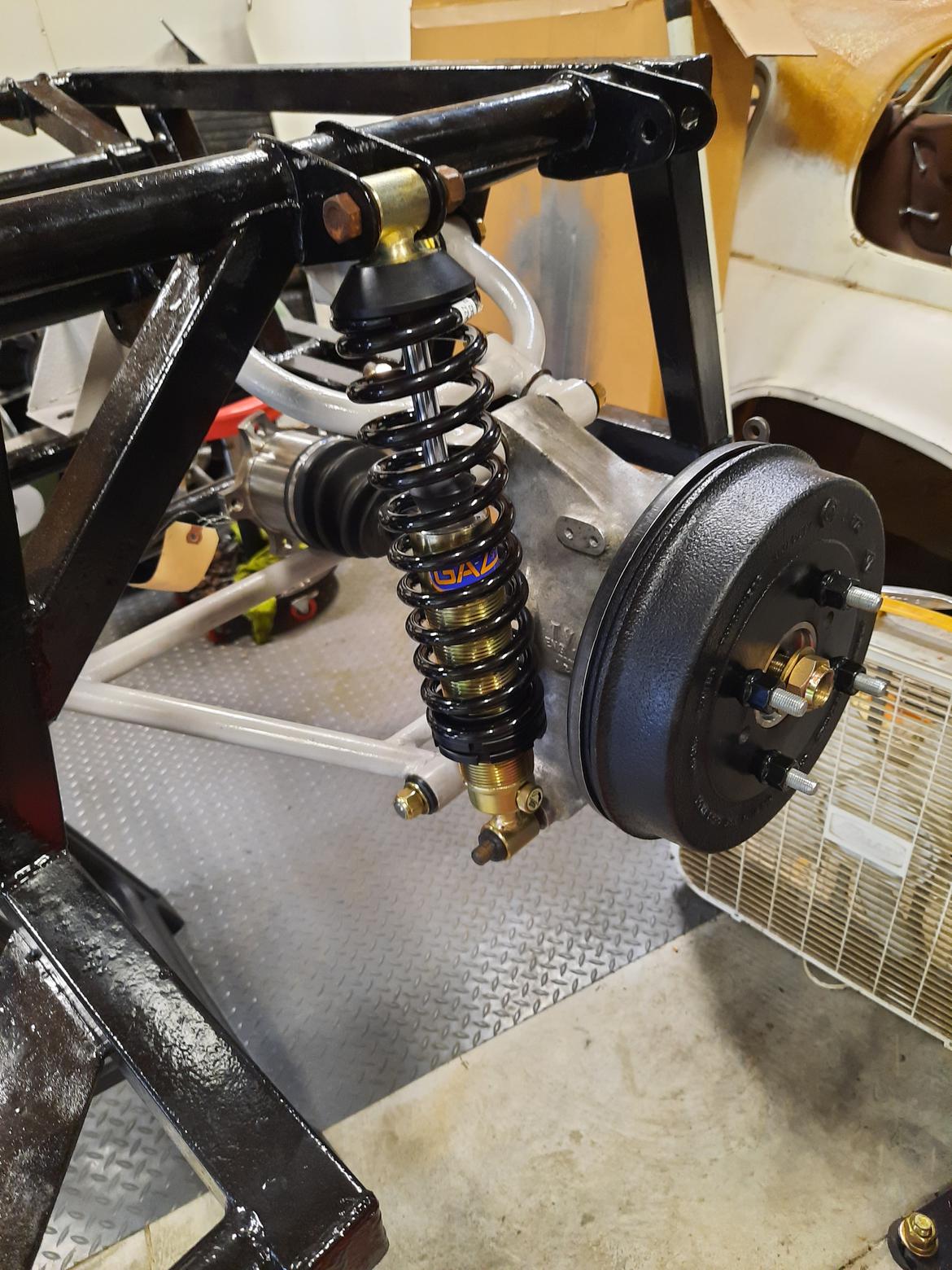
Probably just a little heat on the axle where the bolts go. The other side came off easy because the wheel was on the ground, I didn't have it in me to change the orientation of the forklift to put the drivers wheel on the ground to break the bolts free, so i just death wheeled the axle
In reply to Stu Lasswell :
When you're ready for all the info on how these actually fit, just let me know.
I hope you will check the bump steer on the front before you are finished. Rack height is extremely sensitive, and frequently off. .010" makes a remarkable difference. Take the springs back off, set the ride height with a fixed link somehow and set the toe in while everything is still up on stands and body off. Then bump steer check. Much easier to do now before the body is in the way or the car is on the ground.
I saw on the TVRCCNA site there is an M for sale with a 5.0 swap. It has an R200 installed. Maybe reach out to that seller and ask what steps were taken on that build.
Well, I'll just reply to everyone in one post.
Patrick; no worries, I'm, sure I can get it apart and cleaned up... thanks again for coming through for me.
Scott; I appreciate your assistance, and I'm happy to have your experience as you travel this minefield a few steps ahead of me!
TurnerX19; I will indeed follow your advise and check for bump steer. First I need to establish the suspension setting at normal ride height. I hope that if any adjustment needs to be made, it will involve raising the rack height, as lowering it might prove difficult. I suppose the rack mount blocks could be cut down some, but not more than 1/8", maybe 1/4". Who knows, it might be perfect now, as it's undamaged and being set up as delivered (although I hear that with TVR, that doesn't guarantee anything).
In reply to Stu Lasswell :
Most of the chassis I have seen need shims to move it up. I think there was enough foresight in the drawing office to leave the tolerance in that direction. I have seen a stack of 3 shims totaling .120" as delivered on a Lotus with this upright/steering box combo. Triumph never shimmed them from the factory, and I have not seen enough TVRs to say.
In reply to Stu Lasswell :
I labored thru the LSD install so you could have it easy.
You figure out the bump steer and tell me how to do mine right!
Hey Stu, I'm going to mess with your brain a little! Because misery loves company!
I was having trouble getting my front coil-overs installed (purely my fault) so I went back to the factory manual that I have, and saw this picture:
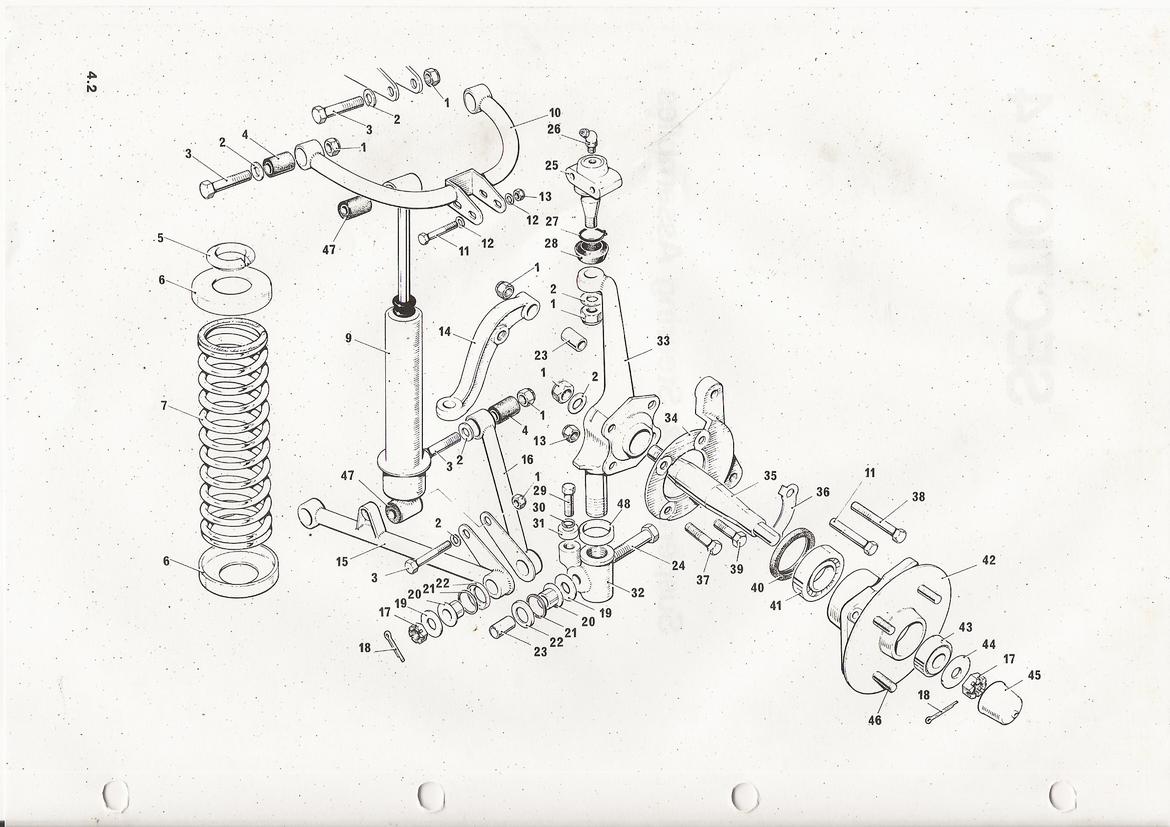
Look where the sway-bar mount is in the pic - THE FRONT SIDE!
Now more misery:
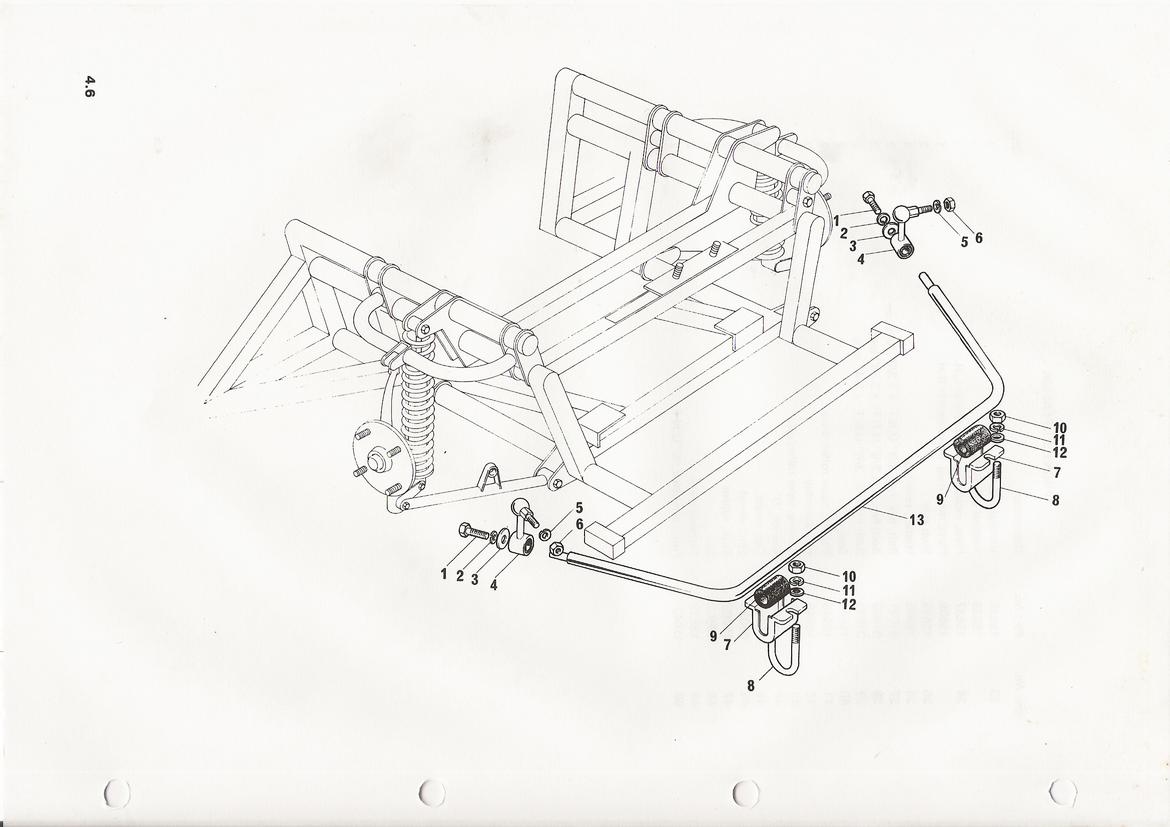
Again, front side mounts on the A-Arms, and no chassis mounting brackets. Messed up!
Clearly something changed between when the exploded view was drawn and when the cars were actually built. I've confirmed in various BaT pics that the front end goes together how you and I have both done it.
But it does confirm that the build on these cars is firmly in the "Trust but Verify" category!
In reply to TVR Scott (Forum Supporter) :
That seems fair, Scott. But you know, my TVR will be perfect "as is" while yours will need all kinds of special adjustments and modifications!
In reply to TVR Scott (Forum Supporter) :
That is funny. The other day I was looking at a photo of a partially assembled chassis on one of the many TVR Facebook groups and saw where they had put the a-arms on that way too. I just figured they would see the error of their ways when they tried to mount the sway bar. I haven't really looked at any earlier versions of TVRs... maybe that's the way the pre-Ms were set up.
In reply to TVR Scott (Forum Supporter) :
Another thing. I'm using all new grade 8 bolts, nuts and washers. Although I got the same length bolts as I'm replacing, it seems that I'm just barely getting the bolts through the nylock nuts. The washers do seem to be thicker than the ones I replaced. Now, having looked at the illustrations you provided, I see they are using a washer at the bolt head but not at the nut end, whereas I used two washers per bolt. Do you use a washer beneath the nut, or not?
edit. Maybe it's the polyurethane bushings... I forgot you shaved yours down a bit.
Stu Lasswell said:
In reply to TVR Scott (Forum Supporter) :
Another thing. I'm using all new grade 8 bolts, nuts and washers. Although I got the same length bolts as I'm replacing, it seems that I'm just barely getting the bolts through the nylock nuts. The washers do seem to be thicker than the ones I replaced. Now, having looked at the illustrations you provided, I see they are using a washer at the bolt head but not at the nut end, whereas I used two washers per bolt. Do you use a washer beneath the nut, or not?
I'm a hardware nerd. I obsess about things most people don't. I've bought all AN aircraft bolts for my suspension pivots. You specify the grip-length on them so that no thread is loaded in sheer. Only the shank. These have short thread length, so you don't have much extra. It's pedantic. And expensive. But I can't help myself. Take that as a preamble.
Definitely use a washer on both the head side and the nut side. You probably have generic USS washers which are all huge and thick. You can buy thinner washers - look for AN960 aircraft washers. They come in 0.063" and 0.032" thickness, and they're pretty small on the OD. An in-between that I often call out for my machine designs is the SAE size.
I would suggest you order up some Grade 8 Hex Thin Locknuts. You can get them from McMaster if you don't have a good local hardware supplier.
Then you can use washers on both sides and get a couple threads of bolt protrusion. I used those exact nuts on a couple of the rear lower control arms.
As a brief aside, I never bother with split-lock washers. They're a waste of time and don't work. Nylocks or Belleville washers are the way to go. Fancy wedge-lock washers work well too. Safety wire, if you're fancy and don't have much going on...