I finished one part of my trans mount, the part that bolts to the trans. Unfortunately, I just have not had much time lately. I switch to day shift AND have a short vacation planned soon, so I should have time to work on it again soon.



I have been doing a ton of mental work on the car lately. Thinking about rear end, chassis, suspension... I decided to hold off on a lot of that until I can recoup a bit more cash.
Anyone know of a good chassis book? Right now, the plan is a 3-link with a Ford 8.8. I understand SOME of the theory and such, but I want to know more about it before I go all crazy with making stuff.
Also, for any experienced welders, or people that are more experienced than I am. Are my welds looking OK? I know they LOOK alright, but I'm always looking at getting better. I am having a little trouble with the bead being a little bigger than I want, but the puddle is good and deep when I am welding. I have the wire speed turned down pretty low for the amperage, so I guess the only way to thin that out is go faster. But I also want to make sure it penetrates as far as it needs to.
I'm pretty good at self diagnosing, but I am at about where my knowledge ends on this type of welding. I used to do A LOT of oxy-accetaline welding, but that is old news now.
I hope to be getting a gas tank soon. That way I can be doing real MIG instead of FCAW. Anything I should know on changing technique going from flux core to MIG?
So to recap:
-Recommend chassis/suspension book.
-Rip on my welds, but please also tell me what might be going wrong.
-Any advice on technique regarding changing from flux core to gas.
I think "Chassis Engineering" by Herb Adams, and "How to make your car handle" by Fred Puhn are pretty good books. Both are a bit long in the tooth by now but the basics and fundamentals are there. Chassis Engineering is perhaps a bit more oriented towards building a bespoke chassis while the other one deals more with modifying production cars.
Regards
Gustaf
Opinion: the best thing you can do for your welds is get on the gas. Those look very good for flux core. If you are at all worried, destroying some samples with a band saw is probably your best bet. Weld similar materials at the same settings, and see just how good the penetration is.
+1 on above books, also watch Project Binky on youtube-episode 9(ninja edit: episodes 10 and 11), I think, has good, real world bump steer and ackerman approaches.
Lookin Groovy!
Agreed, gas will help a ton and make your life easier, so much less cleanup. And cleanly cutting a couple of welds will tell you how the penetration is.
Are you seeing any discoloring from heat penetration on the back side?
HunterBenz wrote:
The front main seal went bad, real bad, so I did what anyone of us would do and decided to put a different engine in the car.
I laughed way harder at this than I should have. I was a little embarrassed after explainin to my GF why I was laughing so hard.
HunterBenz wrote:
Also, for any experienced welders, or people that are more experienced than I am. Are my welds looking OK? I know they LOOK alright, but I'm always looking at getting better. I am having a little trouble with the bead being a little bigger than I want, but the puddle is good and deep when I am welding. I have the wire speed turned down pretty low for the amperage, so I guess the only way to thin that out is go faster. But I also want to make sure it penetrates as far as it needs to.
IME you really just have to crawl with flux core. Both wire speed and hand speed.
What kind of machine are you using? I have an old Lincoln Weld Pak 100hd and a Pro Mig 140. I don't think I've ever had the wire speed over "4" on the 100hd, even when set highest settings. Welding properly prepped 1/8" stuff with that machine I usually do it on the second lowest setting With wire speed at "3". The 140 is fairly new to me, but seems to be fairly comparable with flux core wire. With gas shielding, wire speed goes waaay up.
A couple of the beads on the trans mount look a little cold (convex), hard to tell since you painted over them already. What do you have for a mask? A big mistake many will make is running the shade too dark, you should be able to see the weld puddle clearly.
Thanks for the tips. I started on 9 with that project binky thing and just started at the beginning because holeeeee shiiieeet that is awesome. I've always wanted to take an early 2000's is Mirage and "make" a legal evo 6.
I have a Lincoln 140c, I think, I usually go pretty slow and my wire speed is one smidgeon up from the bottom of travel. I do have heat discoloration on the back side when I finish.
My helmet is the HF el-cheapo auto darkening one, and yes I can see the puddle. The puddle looks fine to me.
I may just crack through a weld and see what it looks like. Not sure why I did not think if that before.
The paint is weld through primer, I hate... HATE ...the little slag balls that stick to the bare metal all around the welds with flux core. Hate them. So, after just putting up with it for too long I bought some weld through. Don't know why I did not buy it earlier.
I bought the [u]Chassis Engineering[/u] book. I also bought a highly recommended to me by other people book called [u]The Race and Rally Car Source Book[/u]. I refused to pay well into the $100.00 mark for it and found an "acceptable" copy for $17.
It will go with my other out of print automotive books that just seem to be unobtanium for a reasonable price anymore.
Honestly the primer is probably what's making your welds look cold. As I was reading your machine/setting info my first thought was "He must have a bad ground or poor prep to have those issues."
It might also be worth it to break down your leads and clean out where the wire bolts to the ground clamp etc. I had a problem with that on my older machine.
Something has to be wrong if your wire speed is that low and you're getting that big of a bead. Are you using an under rated extension cord, maybe? Or even just under rated wiring in your workspace? These things really need 10ga wiring from breaker to the machine or they suffer.
As far as the spatter, have you tried the anti spatter spray? It does work and doesn't cause any issues. If you can get your prep/settings right spatter can be fairly minimal.
In reply to Crackers:
That's the other one, those 120 volt units work great, but they will give you A LOT of E36 M3 if they aren't on a good circuit (12 gauge, 10 is probably right for a long run or extension cords) that can handle the draw without a lot of voltage drop. They really should come with and idiot light labeled "insufficient wiring" that comes on and trips the thermal breaker around 114 volts. If I ever own one it will probably get that modification. Best performance I ever saw was with one plugged straight into a 5000 watt generator, an adapter to pull 120 from a dryer/stove plug would probably do great too.
Yeah, I've added a dedicated welder outlet with 10ga wiring to the last couple houses I've lived in, and generally use a 50ft 10ga extension cord. The 100hd has even run on a 100ft 10ga extension cord with zero issues. Sidenote on overly long extension cords: Never coil your unused length if you're running heavy or sustained loads through them. A close friend of mine burned his house down that way.
A 5000 watt generator was my only option for the 100hd for a while. There doesn't seem to be any difference between the generator and the "welder plug" but I can tell if I'm using a 12ga circuit.
I'll look into the wiring thing. I know my garage, and house for that matter, are very old. As in the garage still has screw in fuses.
Edit, I decided to get off my ass and check. Both my main panel and the garage panel have 30 amperage for the garage. Wiring looks pretty heavy duty. Sometimes I use the extension cord. I'll cut that out and try again. Next time I have time on the car, I'll try direct plugging it in and welding something. Then I'll cut it in half.
I'm hesitant to think it is the primer. The welds themselves look the same primer or no. Just no spatter with primer. Actually, some of the ones with primer look better than the one I did before primer on this piece.
I'll also check the connections on the machine.
Thanks for the suggestions.
Edit: maybe it is time to allow the wife to look for that new house she wants. Criteria: 2 car garage and 220 in the garage. Then I will stop being such an shiny happy person and get a man size welder.
30 amp subpanel is alright, screw in fuses aren't a big problem in and of themselves, what matters is what comes after the fuse box in the garage, the gauge of the wire feeding the outlets and how far they are from the subpanel. A lot of that in old installations tends to be 14 gauge 15 amp circuits meant to run lights and light power tool/appliances, and then some idiot will tend to get tired of buying fuses and screw 20 amp fuses in there, or worse yet, a penny.
Well, I checked out the garage wiring today. The wiring coming in from my 30 amp breakers looks nice and beefy, then there are a couple beefy wires running out, but nothing that goes to any of the plugs is beefy. The plugs are all fed by small baby wire.
Anyone know if it will be dangerous or bad to just run a conduit from my box in the garage with a length of 10 GA to a new plug somewhere that would be convenient?
One of the circuits in the garage runs the opener. The other circuit runs plugs and lights. When the welder is running, the garage is not opening or closing. I don't see there being a draw issue, but I don't know AC for E36 M3.
I may just ask my electrician neighbor to come keep me from burning garage down. This is the box in the garage, don't ask me too much about it... I don't know.

NOHOME
PowerDork
9/11/16 6:03 p.m.
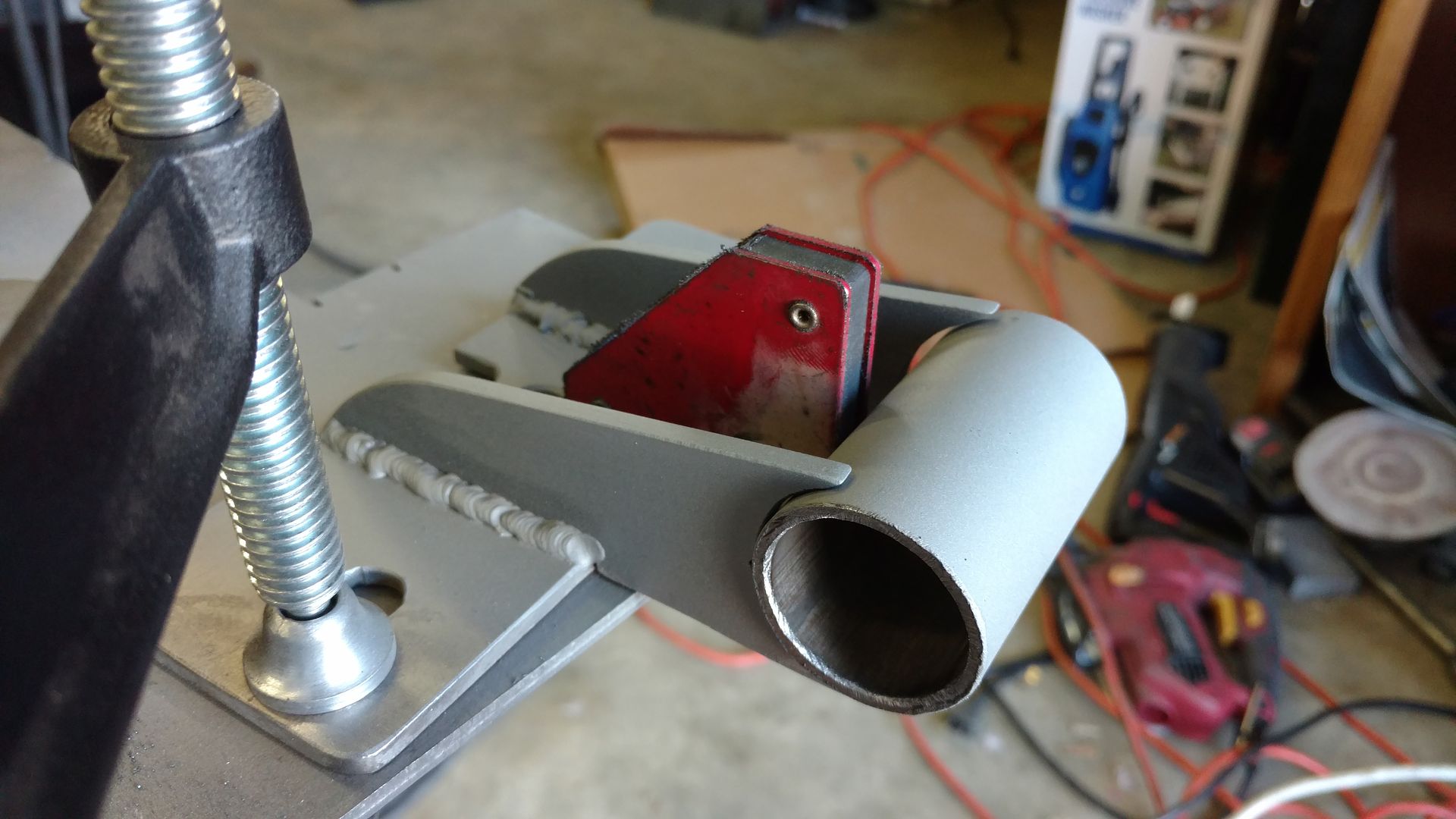
Those welds are cold and I worry about full penetration, so if you have more juice on the welder settings, increase power.
Bevel the edges of the welds. Always best to be filling a "V" fitting. If need be, do two passes filling the bottom of the V first and then the top with a side-side motion as you move along.
Always grind off the black finish on your metal; called "mill-scale" it is an impediment to good welds. Needs to be ground off at least 1" from the weld seam.
NEVER use weld through primer on structural welds. The stuff is a scam at best on on bodywork weldments, but has even less place in a structural weld. If it were mean to be there, Zinc would have been added by the wire manufacturer.
HunterBenz wrote:
Well, I checked out the garage wiring today. The wiring coming in from my 30 amp breakers looks nice and beefy, then there are a couple beefy wires running out, but nothing that goes to any of the plugs is beefy. The plugs are all fed by small baby wire.
Anyone know if it will be dangerous or bad to just run a conduit from my box in the garage with a length of 10 GA to a new plug somewhere that would be convenient?
One of the circuits in the garage runs the opener. The other circuit runs plugs and lights. When the welder is running, the garage is not opening or closing. I don't see there being a draw issue, but I don't know AC for E36 M3.
I may just ask my electrician neighbor to come keep me from burning garage down. This is the box in the garage, don't ask me too much about it... I don't know.
There are regular outlets after that but not more fuses? That's a fire waiting to happen. Beefy/baby isn't really descriptive enough, you need to know the wire gauge (it will be printed on the modern plastic insulated wire), but you don't fuse standard household 120 plugs or 14 or 12 gauge wire at 30 amps in any event.
EDIT: Also, is the breaker in the house a 240 breaker or a 120 breaker? A 240 breaker will usually take up two spaces and always have two wires attached to the breaker.
In any event screw some 15 amp fuses in there ASAP, maybe 20 if you can confirm ALL the wiring is 12 gauge.
There are definitely some issues there. I'm honestly not even sure what is really going on in that panel. Partly because I don't know much about older fused panels, but also because there's no uniformity/symmetry. Also, that fiber wrapped wire scares the bejesus out of me.
First thing would be finding the rating on the wire and putting a meter on it with the fuses out to see which end is the feed. I do know you're not supposed to have more than one wire under a screw connection though.
Do you own the house, or would your landlord be ok with you having a new sub panel put in? I just recently priced sub panels and they're only like $30-40 for smaller ones like this with no master, plus $5-10 bucks per breaker.
10/2 UF-B cable (rated for exposed outdoor/underground installation) is only about $100 for a 100' spool. Maybe just run a new line and sub panel from your main box.
In reply to Crackers:
You're looking at what amounts to an old fused air conditioner disconnect being used as a sub panel, with twice as much fuse as it should have in it for what it's being used for (which is a hackjob in itself with wires doubled up on screws and a complete and utter lack of color coding).
It is certainly a poo sandwich. I own the house and would like to get it figured out. Based on other stuff in the house, I would say this was done back in the 60's. The main house is great, but the garage was pretty much left alone.
The mess of it is kind of an add on, and some of the wires go to a switch that doesn't do anything. I may jump on the buying a new sub panel, I thought they were much more expensive than that. I mean, the house and the garage are not connected and it is just my project and tools that would burn up. 
The white wire with the stuff that looks like black athletic tape is not connected to anything. I have not had a chance to work on anything lately, and since it has not started a fire in the last 50 years, it will wait a couple days before I start up on it again.
Damn BS is going to get in the way of project work, but I may get a nice solid plug or 2 out of it if I can get it worked out. I may have to tear up a wall or 2 though. 
I appreciate the help guys.
Lowes has one for <$20.
http://www.lowes.com/pd/Eaton-12-Circuit-6-Space-125-Amp-Main-Lug-Load-Center/3015036?cm_mmc=SCE_PLA--RoughPlumbingElectrical--Switchgear-_-3015036:Eaton&CAWELAID=&kpid=3015036&CAGPSPN=pla&store_code=103&k_clickID=440916c4-ac1b-47d2-939c-b5bf219587ef
If you're gonna put in a new sub panel you might as well run a bigger line (50 amps?) out to the garage while you're at it.
Might not be a bad idea to start a separate thread on your electrical problems, I think we have a couple real actual electricians here (not me, I only know enough to not burn the house down).
Well, I found my problem and you are all wrong. Sorry to be a berkeleying prick but the problem was something you guys just don't know about I guess.

Put 5 more HP on the welder and all is good. 
Nah, I figured some wiring stuff out and not much changed. I cut some of my welds in half and looking at penetration on the backside, I think my biggest issue is I am trying to weld flux arc like it is gas and I am going way, like way way, too slow. Slow enough to warp a piece of 3/16 in plate. I was only .5 or so of the machine's units off on suggested wire speed.
I'm working on speeding my welding pace up a bit and it is looking more like I think it should, though still not quite. The welds are still a bit more convex than they should be.
Running new power lines to the garage is not in the cards right now. They are under my driveway.
I got some work done this past couple days. Finished the trans mount. It was a long process because it was get under car, measure, go play with kids, get back under car measure, re-measure, then get out from under car, cut piece too big, take it back under car, measure, measure piece, put piece where it goes, mark... Well, you get the idea. I basically got under the car about 1.5 million times.
First I made this crossbar thing.

Did a million measurements, got it partly wrong, fixed it. Tacked somethings together and had this.

I welded in another plate to keep it straight and hopefully keep it from getting bashed up too bad if something hits it.

Bolted in, it sits like this.

Makes the engine sit fairly nicely.

Next up is going to be mounting the pedals and steering under the dash. Then finish the steering rack to wheels. I know what I am doing for the rack to wheels... But the under dash stuff, I need to do some thinkin'.
Hope everyone is having a good weekend.