No real progress to report. I've de-rusted and painted all the suspension bits I had taken off the car, so there isn't much more I can do on it with one working arm.
But I did start a thought exercise on my strut housing quandry. After a mail order mishap made right, I have a pair of KYB strut inserts that will go on the car. I think they will be better than the Sachs OE ones I ordered initially. And the KYB's came with a cap that threads into the top of the strut housing to hold the inserts in (the part of the housings I don't have). Since I had the caps, I could measure the threads to see where to go next.
The caps have male M50x1.5 threads on them. And I have some 2" OD steel tubing in the garage. So idea one was to cut the 2" tubing to the correct lenght, cut the corresponding amount off the stock housings and marry the two with intense heat. After that, source an appropriate tap, cut the threads in the end of the newly welded on tube and be done. But finding a tap for less than I paid for the car proved to be difficult, not to mention the effort it would take to run a tap that big in by hand.
Idea two was to find some weldable parts that already had the threads I needed cut in them, then weld those things onto the strut tube. This was easier than I thought. Google led me to the idea of "bearing lock nuts", and I was able to find some that offered the actual material they were made out of. So $40 and a couple days of waiting landed me these:
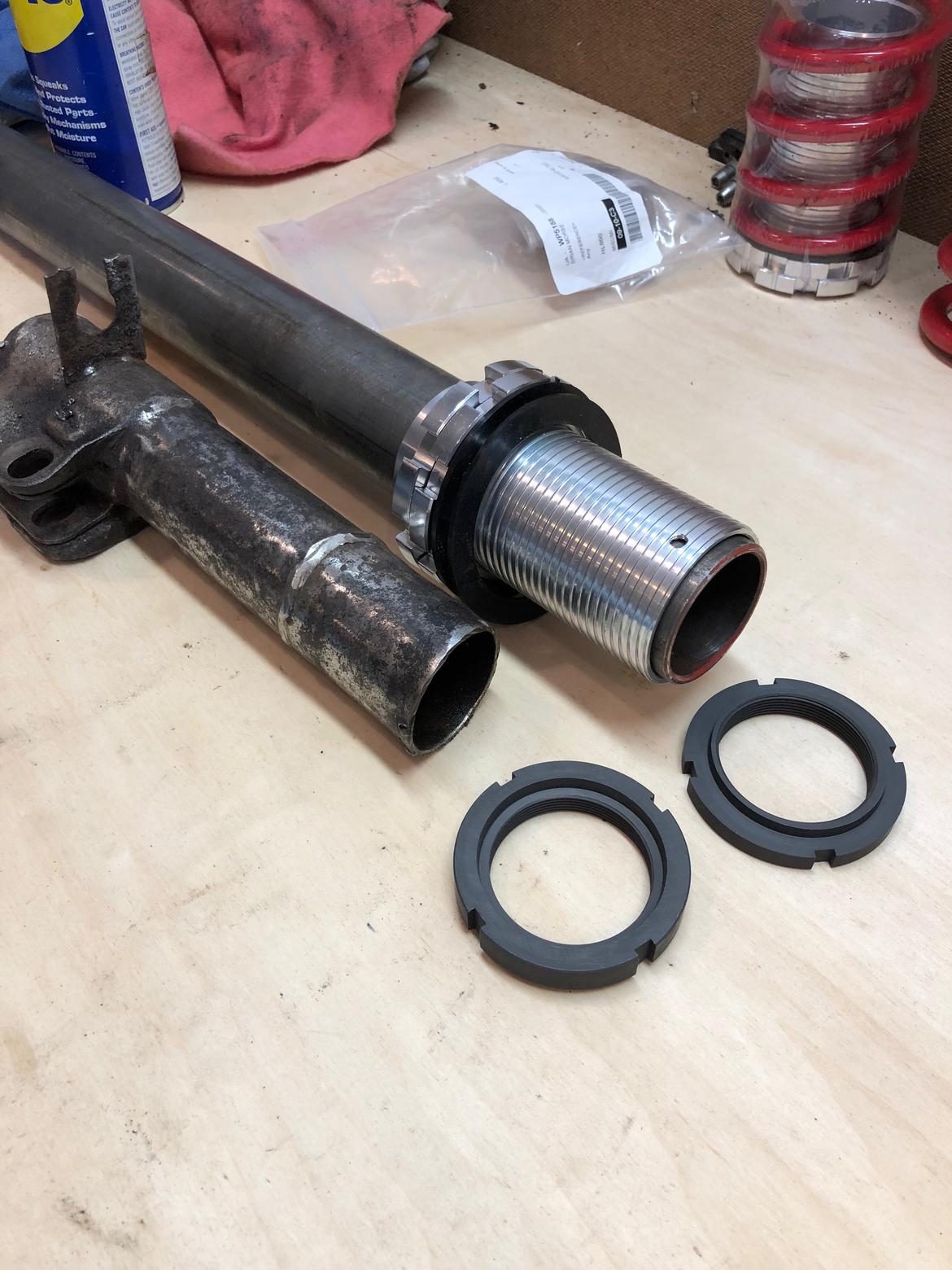
Made out of 1018 Japanese steel with the M50x1.5 threads machined in them.
With some minor fitting, two of them should be able to be welded onto the 2" tubing I have, and then that mess can be welded onto the remains of the stock housings. Maybe.
The OD of the lock nuts is too big, I knew this when I ordered them. The major diameter measures at 2.750". So I kind of figured I would turn the ODs down so the coilover sleeve would fit over the tops of them after they were welded on. But realistically that doesn't look like it would work well, as the remaining wall thickness would only be about .030".
So I'm thinking now the 2" tubing will need to be welded onto the housings, the coilover sleeve slid over the housing and then the lock nut welded on the end. The springs for the coilovers are 2.5" ID, so the lock nuts would have to be turned down at least that far so the springs can be changed out down the road. The down side is the coilover sleeves wouldn't be coming off again.
The general idea:
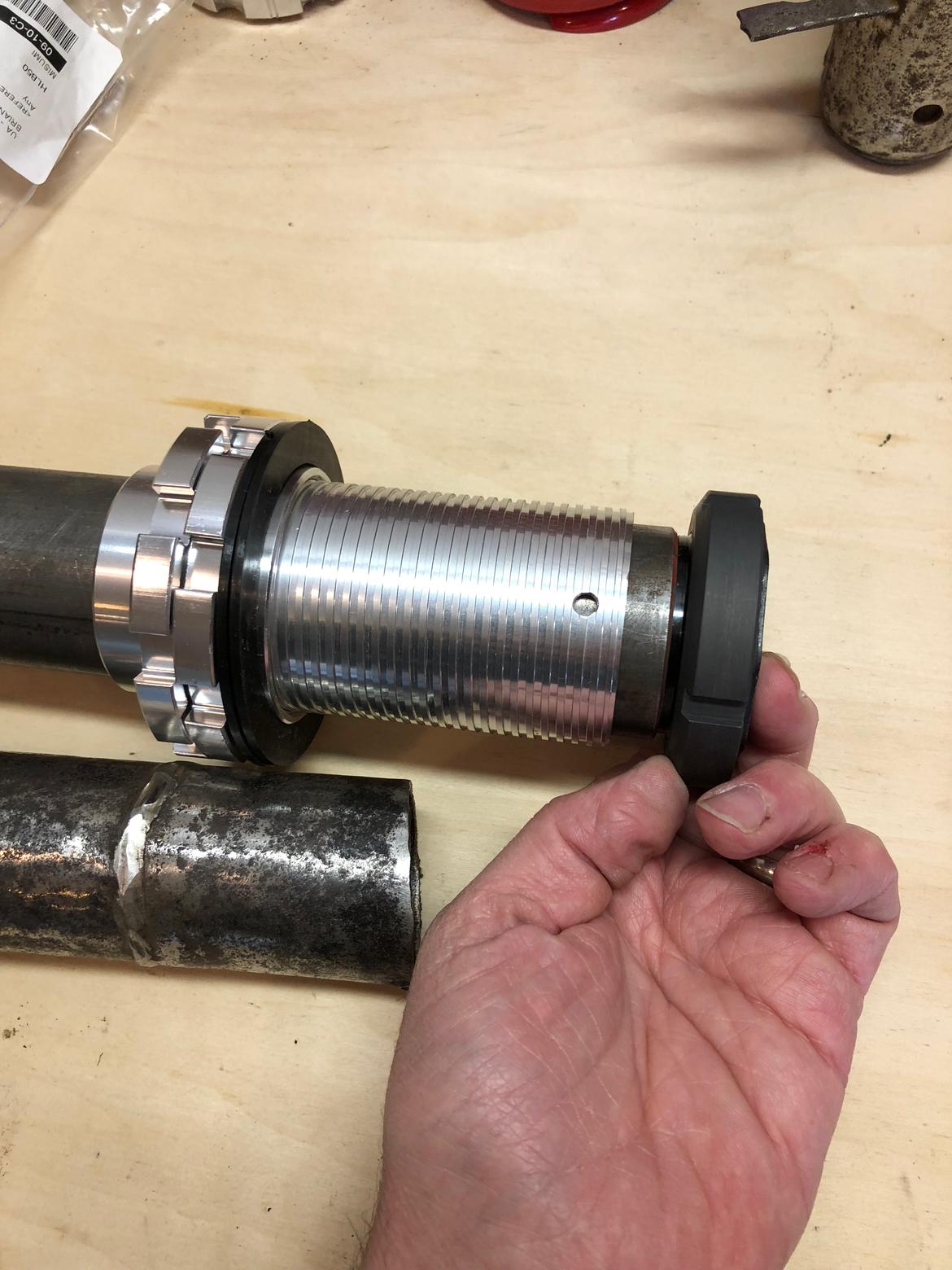
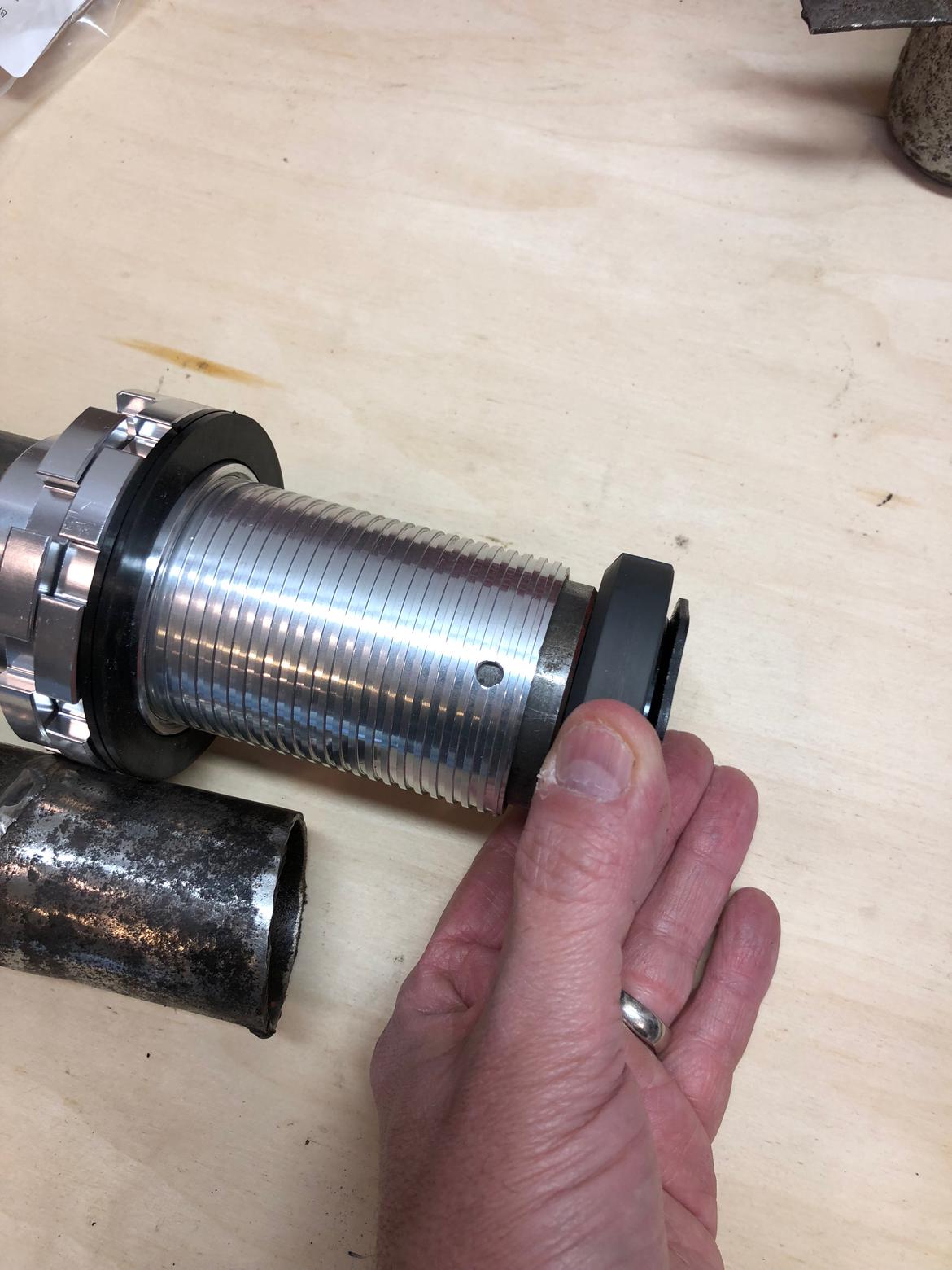
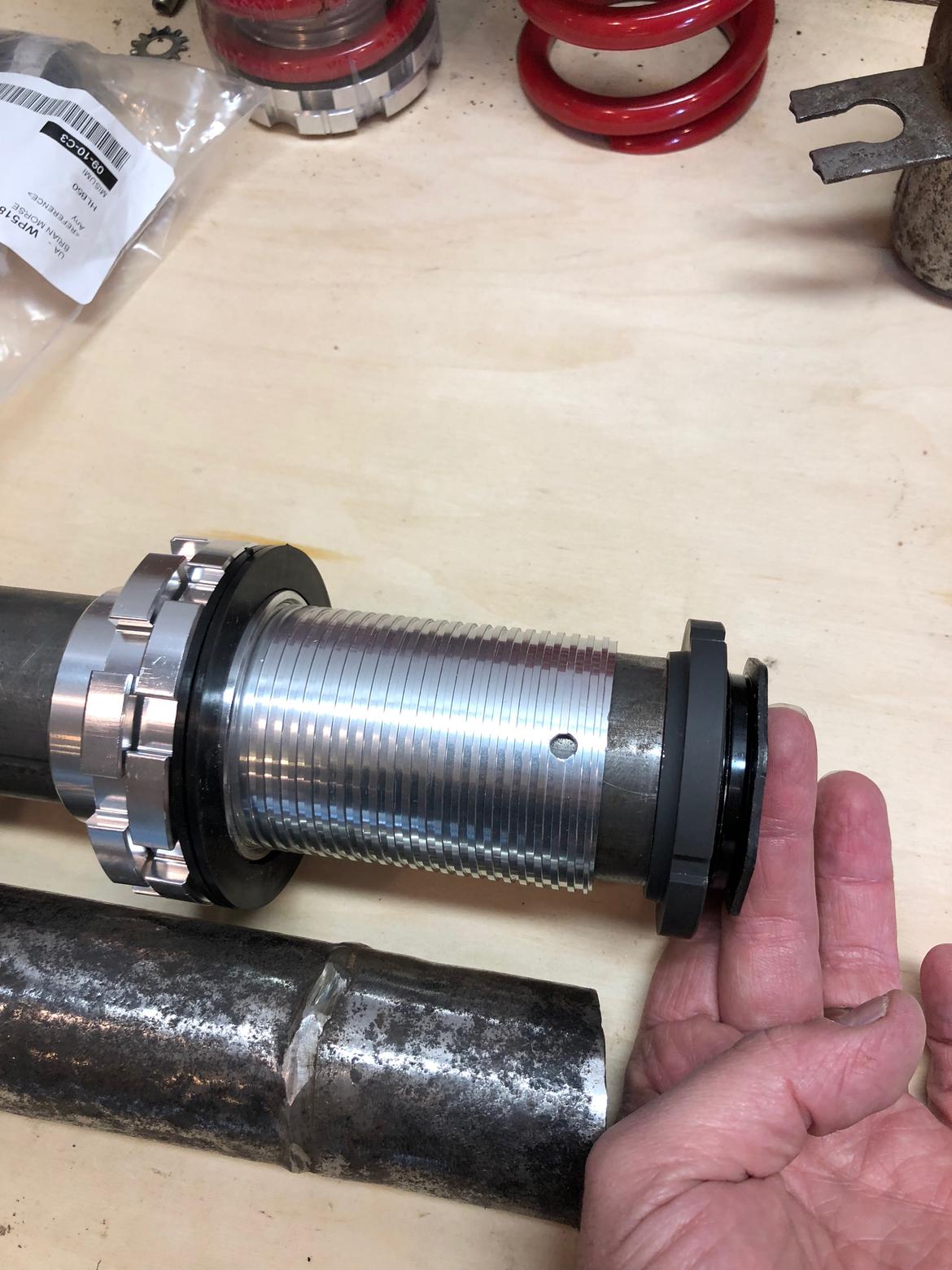
The biggest challenge for this idea so far is finding someone that has a lathe that will turn the lock nuts down for me. There aren't many shops left in Ann Arbor that do that kind of thing it seems. At least not that I've found yet.