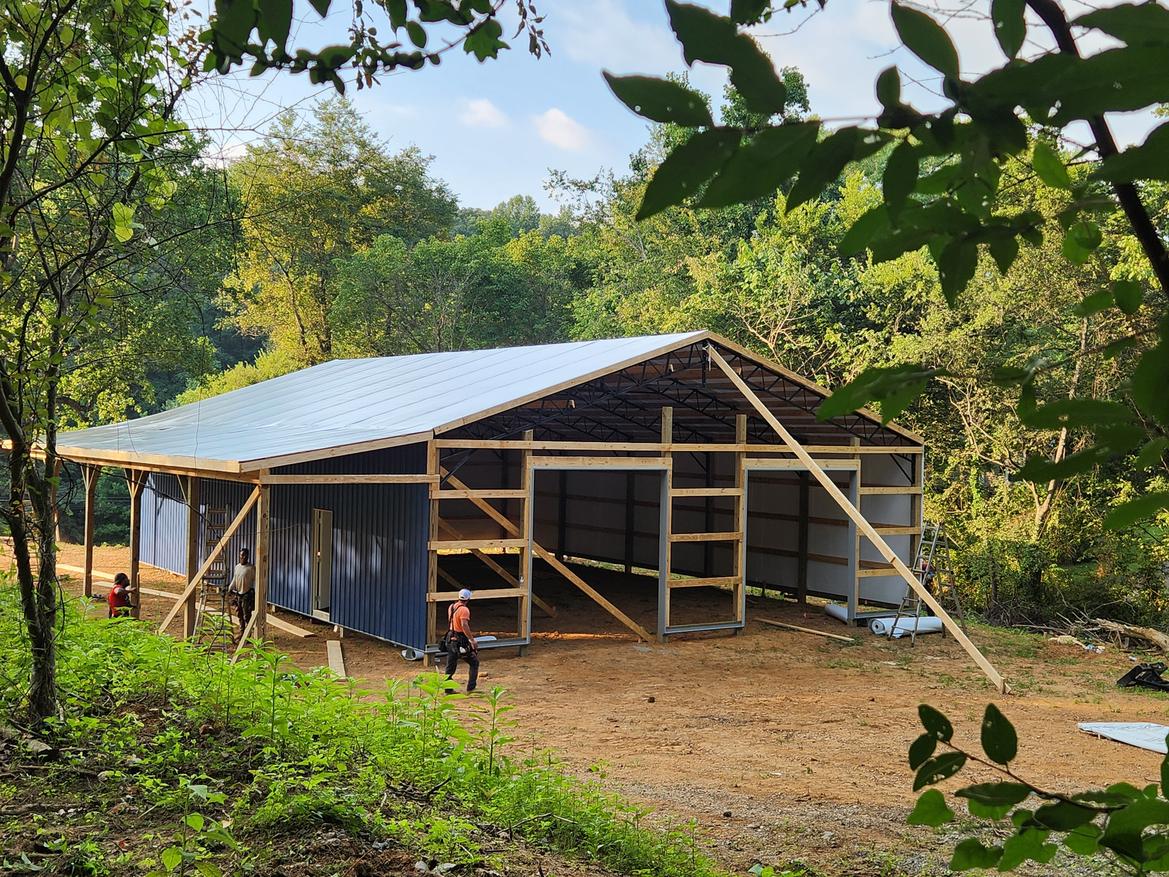
Started this project a while ago, but now I have completed my first official repair (yeah, just put on a new fanbelt) in the new shop/storage place, I figure I can go public with it.
Hi, my name is Travellering, and I am an automobile addict. I got the disease from my dad, who worked in the auto industry for 5 decades and somehow still didn't burn out on playing with cars in his off time. Smart people have a daily driver, and a project car or two if they are very capable. I am not smart. I have 22 vehicles, and many of them are not up to what some folks would consider a project car, including my daily drivers....
As you can guess, that many cars means I can't quite fit them all in the standard 2 car garage at our suburban house. Fortunately I married a lovely young woman with just as much of a car addiction as myself, and with family property just outside of town. When it became clear that our current car storage setup was becoming untenable, we started looking into steel buildings and the like.
The most reasonable, and easily broken into "installments" option turned out to be a pole barn. That choice enabled us to erect the building and have at least a covered space to put the cars that needed protection from the elements in even if we were unable to get funding for niceties like a concrete pad, electricity for doors, and the like. A true metal building required the pad be in place as the structure must be anchored to something. With the pole barn, it would actually have added to the cost to put it on an existing pad since you have to purchase the interface mount plates and through bolts that attach the 6x6 poles onto the pad.
As for most people, budget determined size. The property is "Appalachian flat" so the largest area we could afford to level out that wasn't directly in the flood plain of the creek would support about 60x50 feet of flatness.
The fine gentleman we found to do the levelling turned up with a Cat 953 dozer. Great for heavy earth moving and compacting the pad area, but since we had some pre-existing trees, powerlines, and a fenceline we didn't want to plow under, I was worried it was not the most finesse-able option. The guy operating it proved me wrong in short order. We told him we wanted to keep a Crepe Myrtle tree that was at one corner of the pad, and left the rest of the job in his capable hands. When we came back, not only had he protected the tree, he had picked out a tree that was growing up through the middle of it!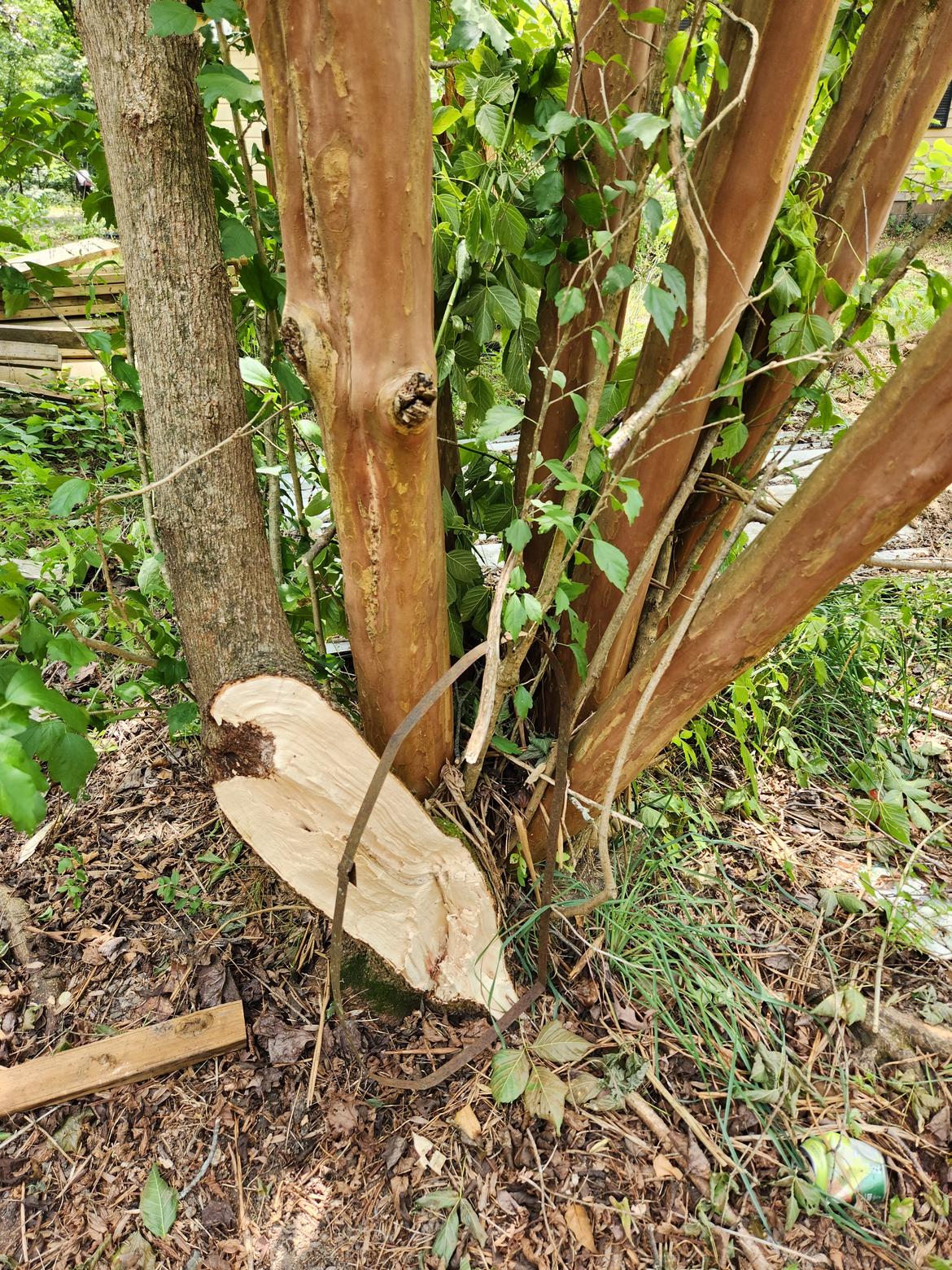
Stampie
MegaDork
12/11/23 3:15 p.m.
In reply to travellering :
I'm in and thank you for having more cars than me.
Final state of the building flat clay and mud pad a day later:
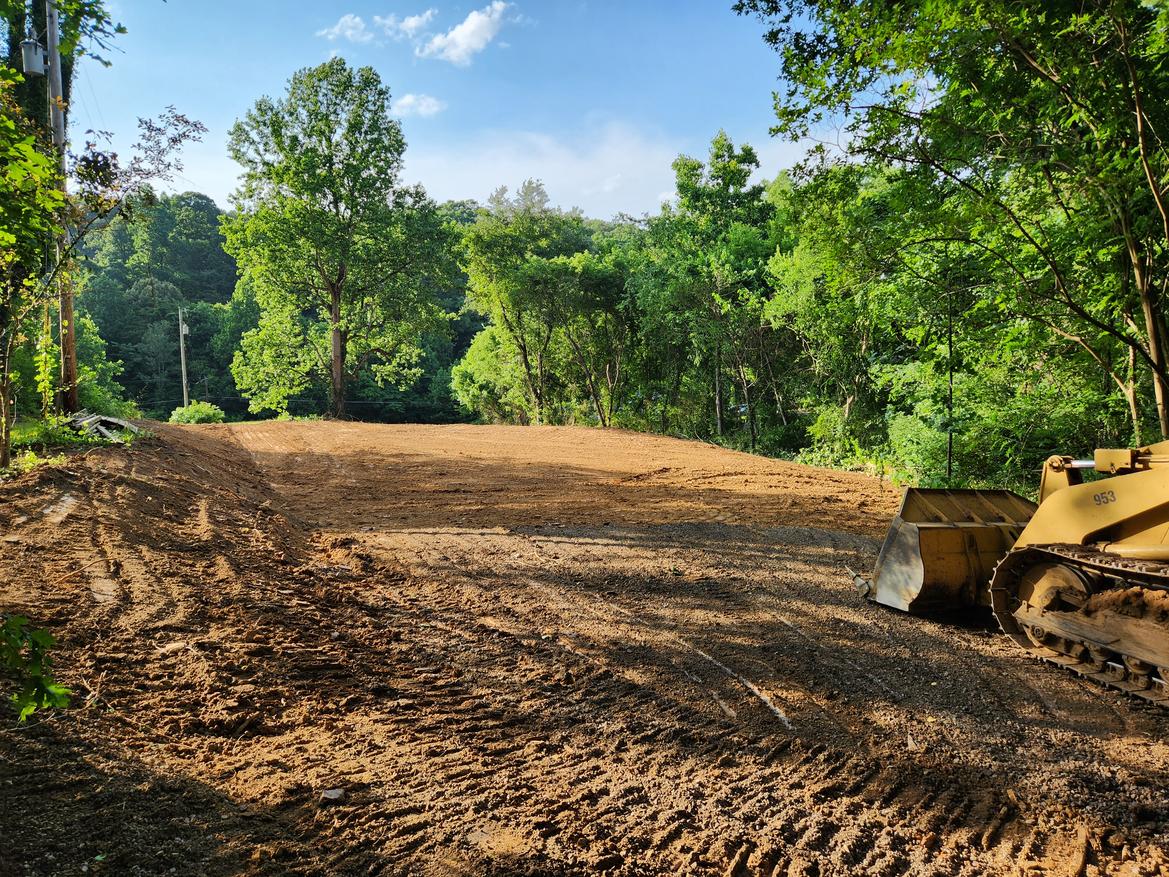
I'm not going to make this thread a 1 to 1 retelling of the whole process, as everyone would have quit reading by page 7 or 8 of the process of trying to finalize the building order. Suffice to say, the rough quote(probably just auto-generated) was really quick. The local contractor that the company puts in charge of builds in our are was super helpful, dropping by twice to answer questions we had even before we had committed to buying the building.
The actual sale took forever to get through. I would have thought that commission sales would make someone with a fish on the hook reel them in as fast as possible. Not our sales guy. Phone tag champion of the Southeast. I know it's not the company at fault, so I won't drag them through the mud, but that one guy. We actually got a same-day response from the head of the company when we called to complain after the third or fourth week of trying to give them money.
Since we had over a month of trying to get the building purchased, I didn't hold high hopes for how fast the rest of the process would go.
We were told the materials would be delivered on one date, and then the next week the construction would begin. We were led to expect a typical 3-4 day build and that was obviously contingent on good weather. Even though there was no concrete pad, each post had to be sunk 6 feet in the ground and cemented in below grade level. That had to set before trusses, purlins, and all side structure could go up.
Once we had a finalized purchase, the floorplan we settled on was a 40 x 60 with a 10 foot lean-to along the one 60 foot side. Primary purpose was( and still is) to be car storage, so extra height was not justifiable, even though it is the cheapest way to add enclosed volume. The difference between 12 foot walls on our building and 18 foot walls was less than adding 10 feet on length. If we were warehousing with lots of shelving,and could make use of the vertical space, I'd have done it in a heartbeat.
Materials arrived on the specified day. Then a call came in from the contractor saying: "the weather looks good this week, and not so good next week, so we'll get started today..."
Cool stuff.
When I thought my 24 x 40 was going to be my "small" building, I decided to not spend for extra height.
Now, it's my big building, and WAY too low. Wish I'd opted for more height at the time. Ah, well.
Keep it coming 
The permits required an inspection once the posts were in, so they got the posts set and waited for the inspector. An early morning inspection "window" became early afternoon before they could crack on.
Small town inspectors are a special breed, apparently. During clearing the land, the dozer ran over the corner of a hidden septic tank. We left it open so it could be inspected and we could find out what we could be permitted to do as far as repair or replacement. The inspector quite literally couldn't find a hole in the ground when he came by. We had to lead him out there and walk across the freshly cleared dirt to the four foot diameter hole...
Better than that was the electrical inspector later. Instead of a hole in the ground, he actually couldn't find the ground... Cited our install for not having appropriate grounding. The pvc pipe with two copper wires coming out of the meter box and straight down the the ground was not visible enough.....
Anyway, back to happier subjects. The inspection finally happened, and they got cranking on putting up the rest of the building. I mean, really cranking...
90 degree day, at 6:15 pm we checked on progress. Felt bad for the guys out in the sweltering sun, and tried our best to communicate that we were offering to get them cold drinks or milkshakes. One guy had good enough English to say "sure, milkshake ok.." As we left I took this photo of the progress:
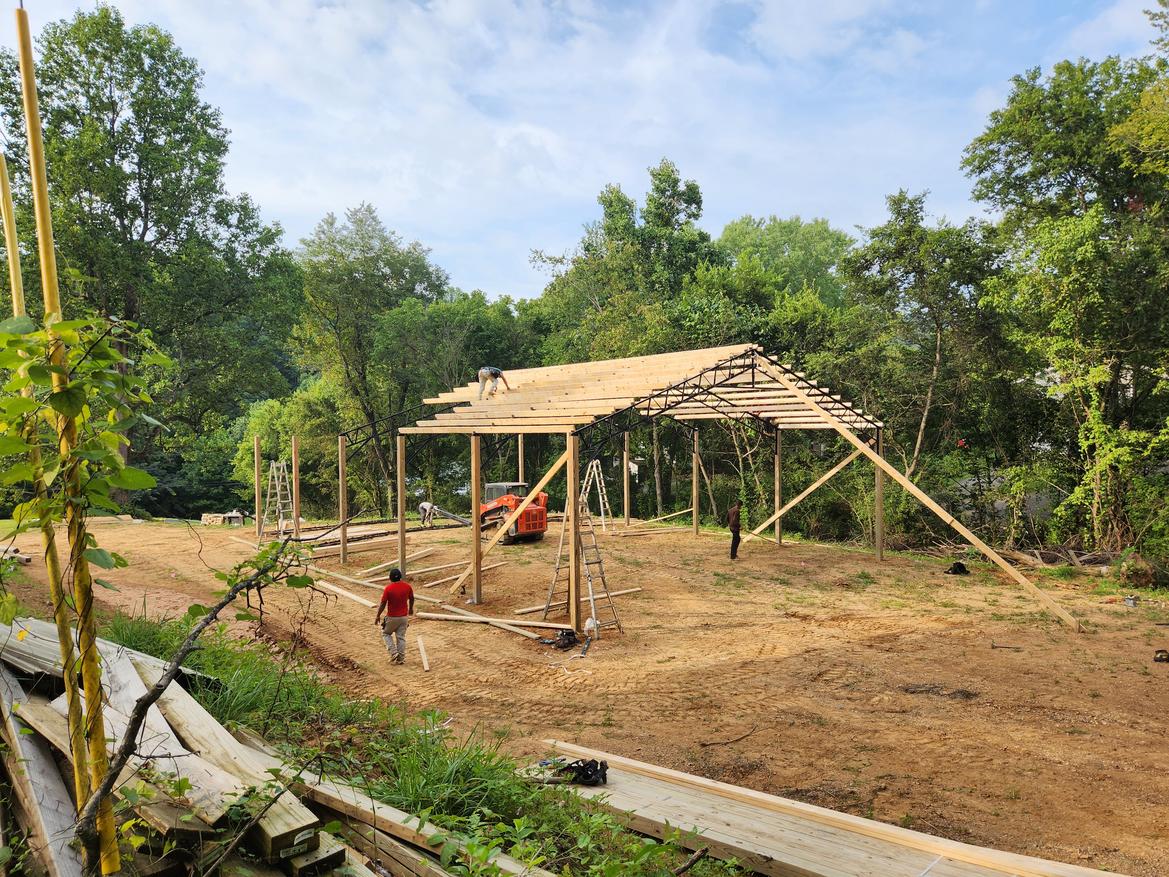
30 minutes later we got back with 9 milkshakes for the crew. 6:45 pm....
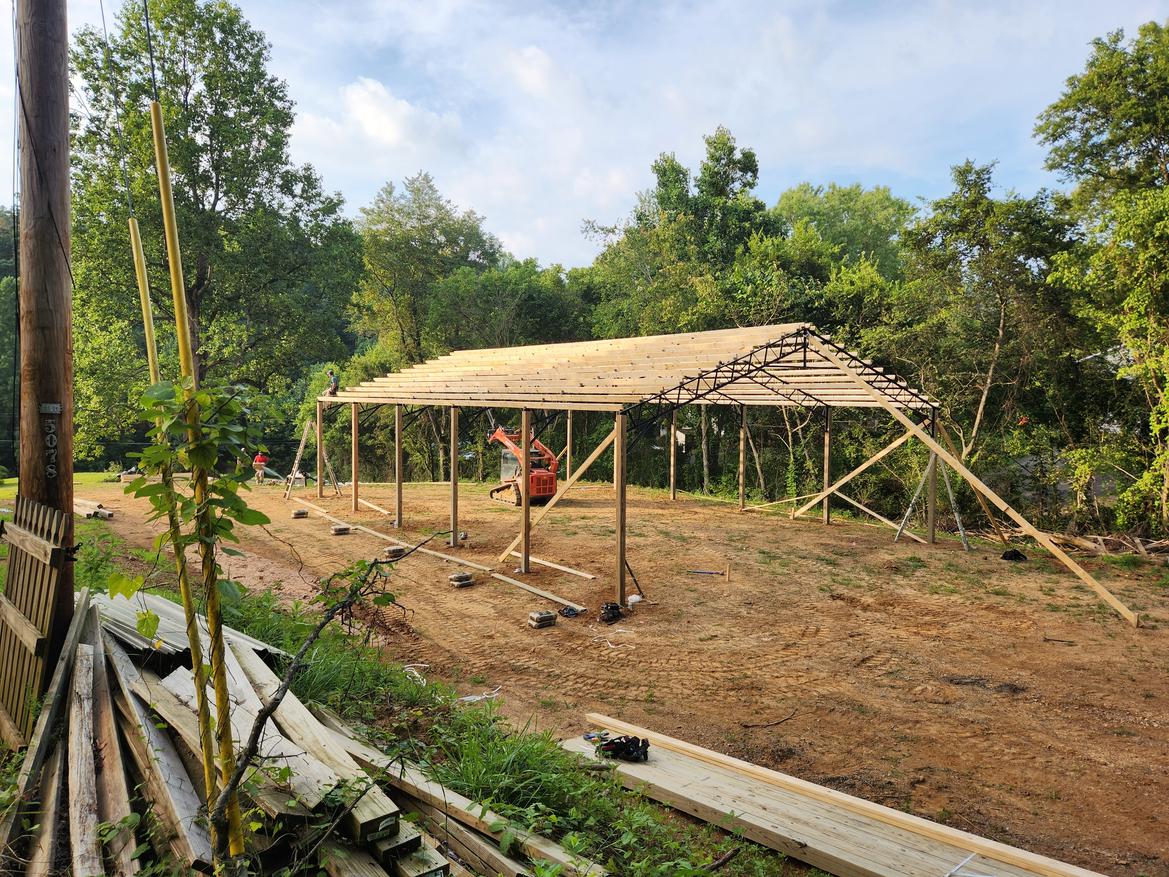
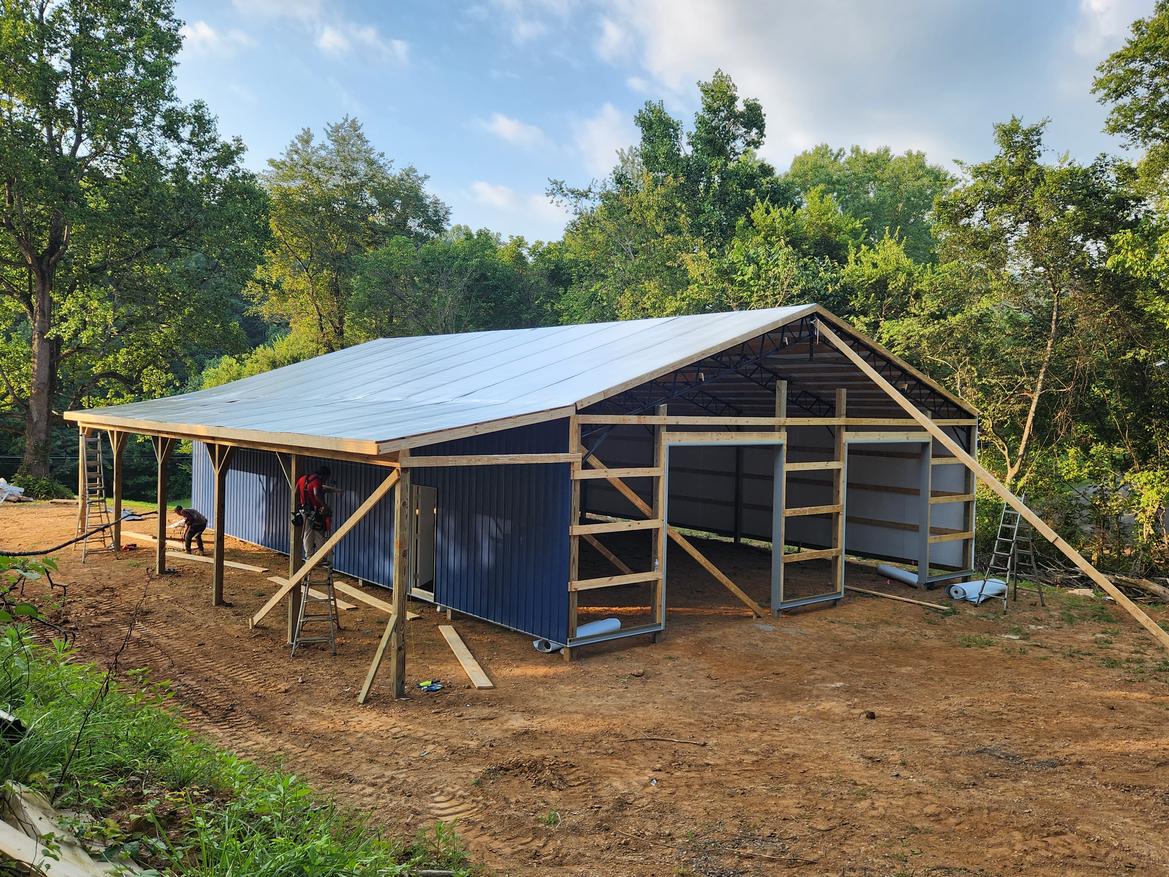
Day 2 of construction. Yeah, these guys put up a post building barn faster than I can put up a forum post...
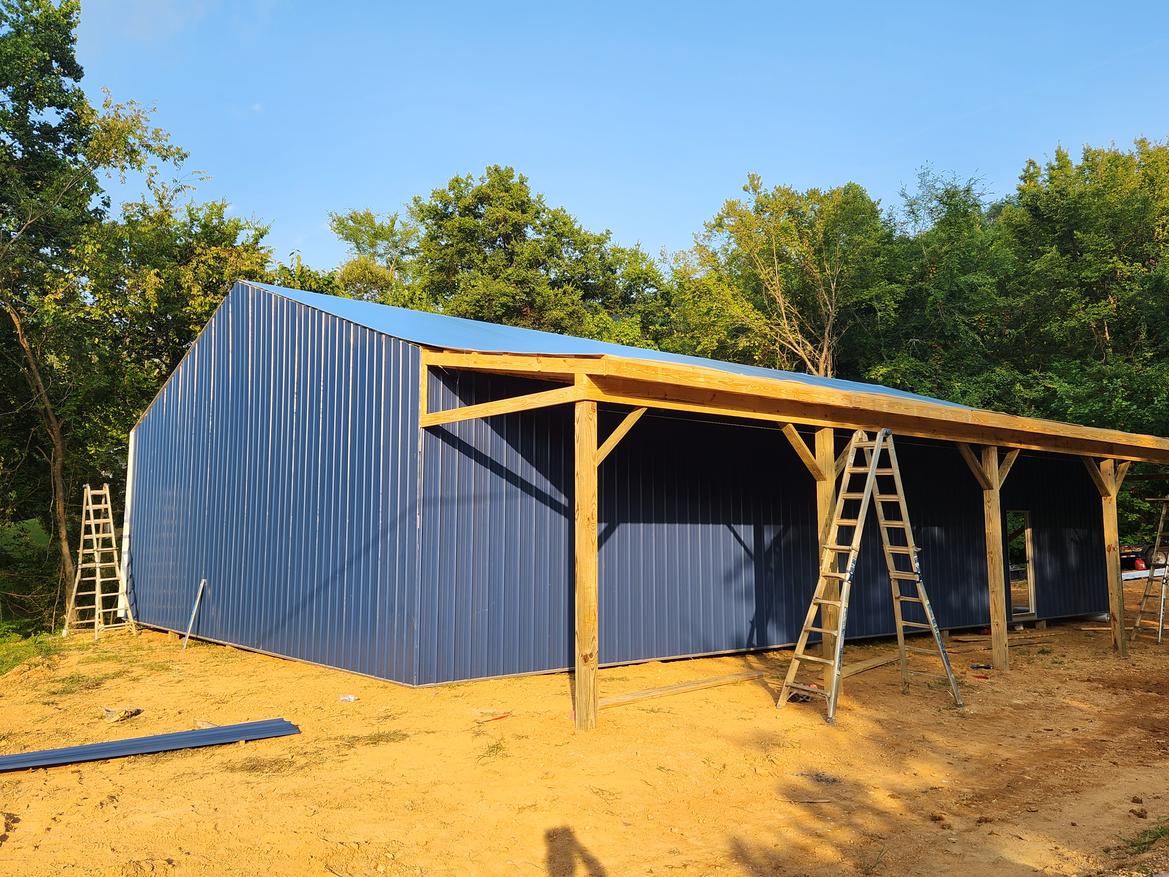
Of course, as soon as they were done I had to test-fit a vehicle in there...
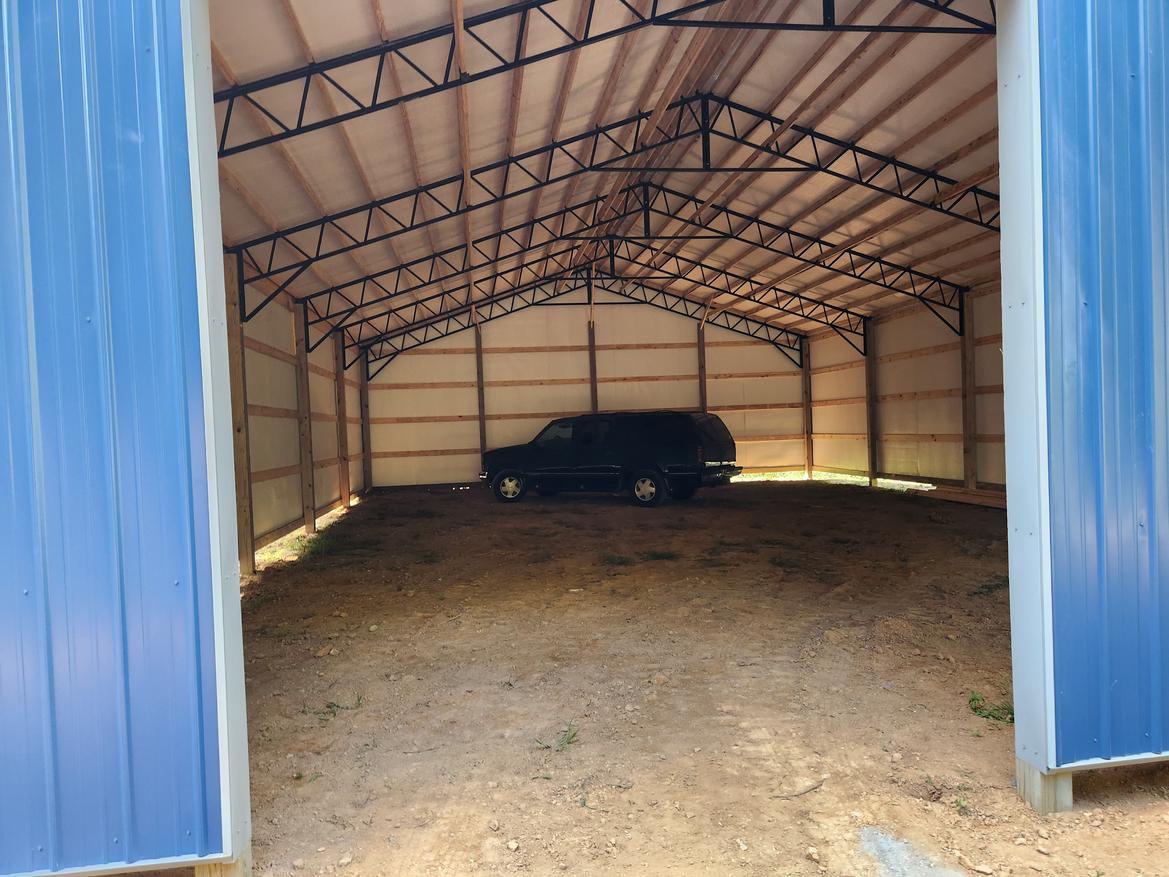
Yep, verified. 40 feet by 60 feet is at least big enough for one Suburban.
So, now we have a building. Roof, walls, a bit of insulation, and door frames. All it lacks is gravel, concrete, gutters, doors, lights, plumbing, outlets, compressed air, lifts, etc., etc.................
Is this build by any chance near Knoxville?
Yup. Classic Mini world is a small one. Since there's currently 4 of them in this building, I'm sure you can sense the disturbance in the force....
Ha! I thought I recognized it! And of course, the DS is a significant clue too......
Next step was pre-plumbing prep. We knew there was a supply pipe somewhere in the pad as there had been a single wide mobile home there a few years ago. Unfortunately, I had no knowledge of where to look for the water meter, let alone where the pipe came up in the freshly leveled pad. We got the local utilities company to come out, uncover, and turn on the meter while the plumber watched for water to come up through the dirt.
Luck turned out to be on our side. The water came up within 5 feet of where we wanted to put the bathroom!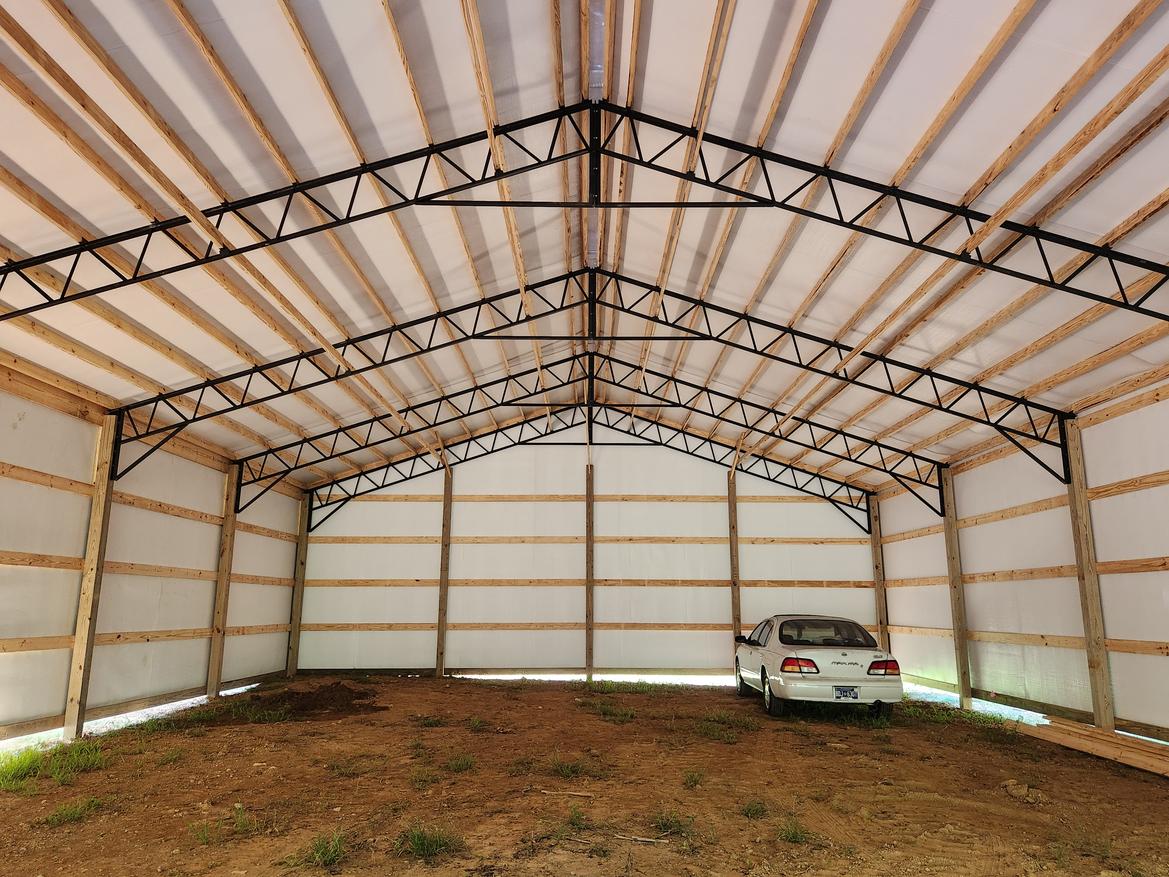
Mud patch.Also, another thing is evident in this photo. The building version of level, and the pad version of level don't really seem to agree....
The plumbers stubbed out the pipe arrangement for the bathroom (shower/utility sink/toilet/water heater, in 8'x8'), and now it's time for things to get a little rocky.
5/7 gravel to be precise. You learn new things all the way along a process like this. I had no idea what 5/7 gravel was, or that there was "crusher run" and substrate quality gravel. For under a concrete pad, especially one with none-too firmly retained edges like ours, we needed the non-crusher run, which meant that all we got was the larger, sharper edged pieces of gravel that interlock better and pack more firmly so the concrete has a more solid base to set up on.
The depth needed to bring us up to a level where the concrete could be poured level with the top of the greenboard( the only treated lumber in the pole barn), ranged from about 2 inches in the corner by the bathroom to 11 inches on the opposite corner. That put us at 5 truckloads of gravel needing to be delivered.
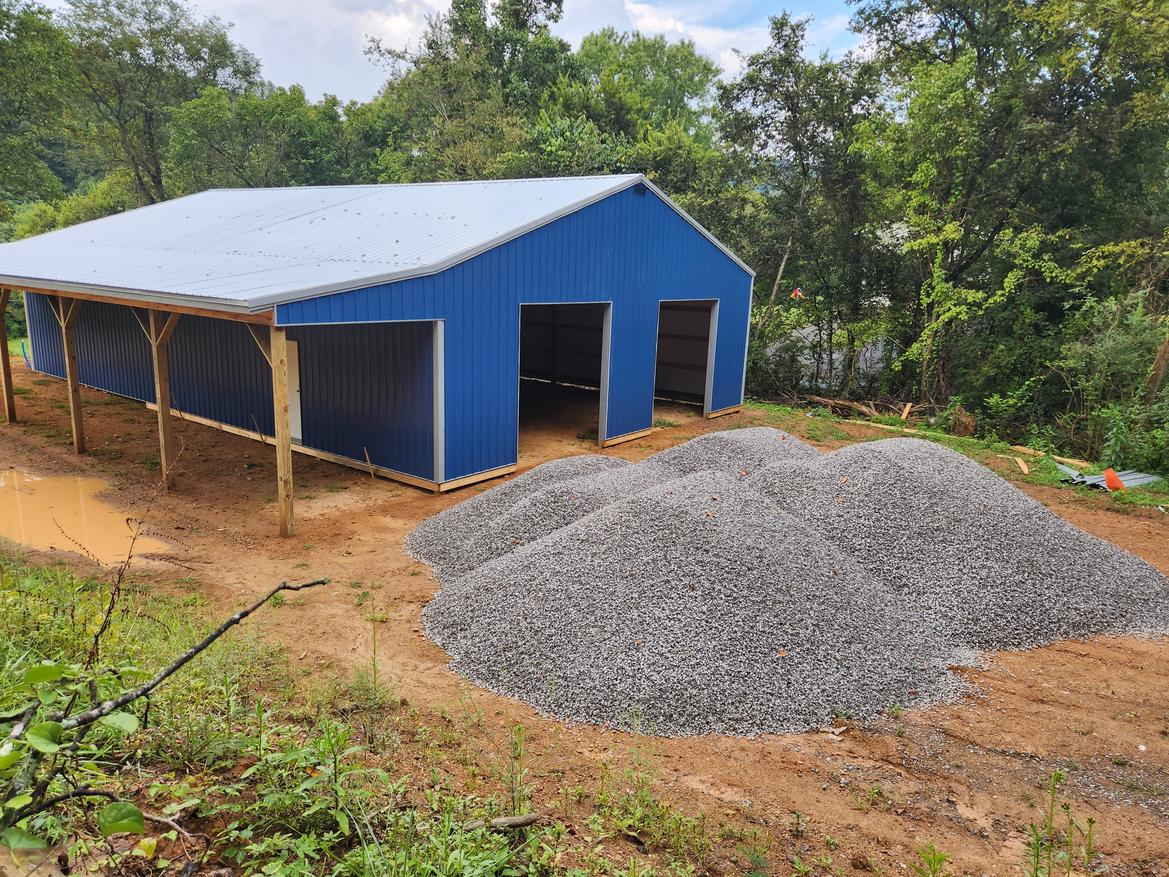
I looked at that pile, and at my rusted out wheelbarrow and lightweight shovel and said "I'm gonna need a bigger shovel..."
Thankfully, the guys putting in the concrete were more than willing to come out a week earlier than pour day and get it spread out and leveled out. My only special request was that we made a depression in the gravel to allow for a thicker channel where I would like to put a 2 post lift in down the line. The rest of it is 4-inch thick pad with fiber reinforcement.
Just finished mine (50 x 36, 12 ' lean-to, 25 x 25' leg), final for structure construction should occur tomorrow (well, later today.) Structure is county, electrical is state, too late for any electrical installation this year, need to wait for spring when the snow melts.
We chose T1-11 siding because we like the look better than tin walls. It's insulated, and we chose to go higher because, while we don't thiink we'll get one, we wanted to be able to park a motorhome inside
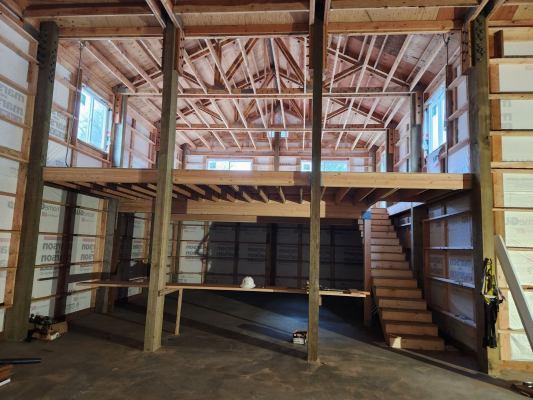
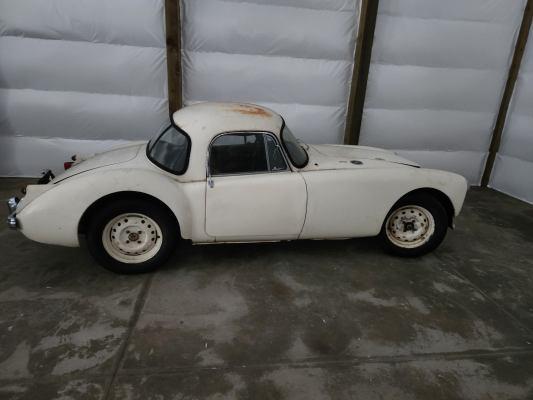
In reply to twentyover :
Nice looking little loft area! Home away from home in the future, or MIL apartment?