www.Sollercomposites.com - good customer service, a lot of selection, good prices
And, dont get too involved in making the molding process too complicated. Some time ago, I wanted to make some intake parts from composites. The 2 things I was most interested in was a MAF adapter and Intake tube. The tube turned out kinda rough, chalk that up to inexperience. But the adapter turned out pretty good, because I broke it down into easy to swallow chunks.
I made the tube part using a tub of spackle as the pattern - it was just about the perfect size, and had a little draft to (hopefully) introduce some venturi effect that might speed up the intake charge somewhat. I made that part by itself. Then for the mounting plate, I simply laid up about 4 layers of fiberglass cloth on a flat surface, which resulted in a 8"x8" flat plate of rigid composite. I cut out the attachment plate out of that flat panel which made getting the shape right much easier.
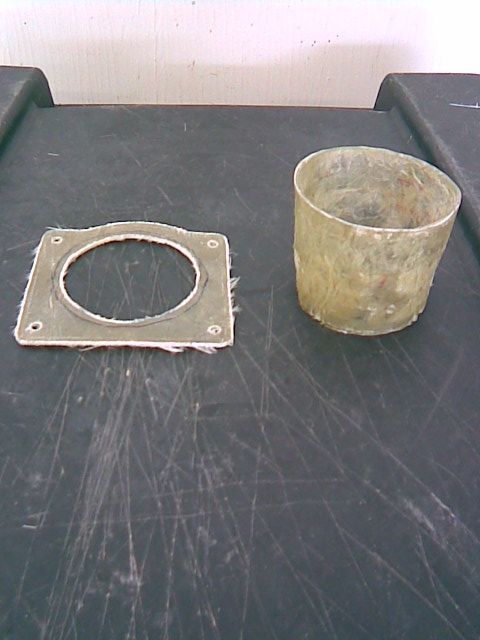
Resin will offgass somewhat as it cures, so its best to wrap it in something to compress the layers and avoid curling/delamination during the curing stage, and also to force out uneeded resin to reduce weight and increase density (strength). I did not take this step, again because of inexperience, which resulted in some unwanted defects, but a crude yet effective DIY method was published by MotoIq.com using a pattern they cast from RTV:

When the 2 pieces were done curing, I sanded them a bit to get them a little more uniform, and simply used some more resin as glue to fix the 2 pieces together. Ignore the tube in this pic, it was a hot mess. The adapter however, is still in use today, about 4 years later.
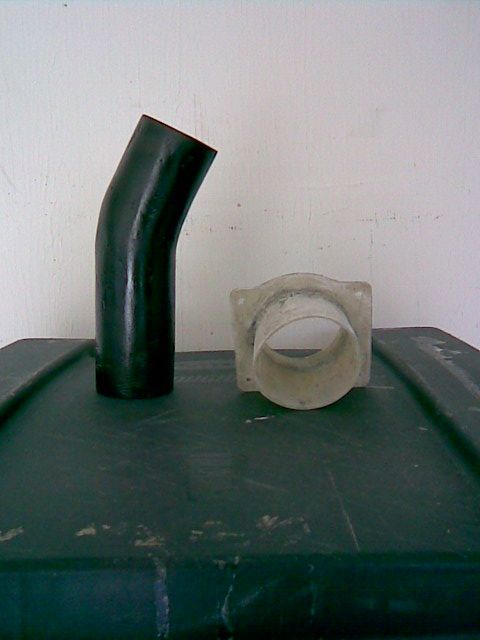
I know its not the same, since youre talking panels, and I was working on much smaller fiddly bits. But the methodology is about the same. Some panels may be tough due to shape or location. Break the panels up if need be, composites are pretty forgiving if youre creative enough. They only require a few general rules be followed.